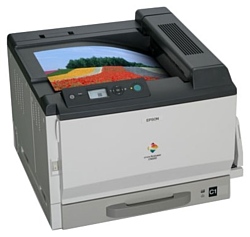
Epson AcuLaser C9200TN
Рейтинг
Снят с производства
Тип устройства
Принтер
Технология печати
лазерная
Макс. формат
A3
Число страниц в месяц
150000
Скорость печати
A4
26
Цветность печати
цветная
Общие характеристики |
|
---|---|
Технология печати |
лазерная |
Тип |
лазерный/светодиодный |
Макс. формат |
A3 |
Область применения |
большой офис |
Число страниц в месяц |
150 000 |
Факс |
|
Копир |
|
Телефон |
|
Печать фотографий |
|
Сканер |
|
Тип устройства |
Принтер |
Размещение |
настольный |
Цветность печати |
цветная |
Принтер |
|
Двусторонняя печать |
|
Пигментные чернила |
|
Печать без полей |
|
Количество цветов |
4 |
Макс, разрешение для ч/б печати |
|
По Y | 600 |
По X | 600 |
По X | 2 400 |
Скорость ч/б печати |
|
A4 | 26 |
A3 | 13 |
Макс, разрешение для цветной печати |
|
По Y | 2 400 |
Время выхода первого отпечатка |
|
Ч/б | 11,4 |
Цветн, | 8,1 |
Сканер |
|
Стандарт TWAIN |
|
Отправка изображения по e-mail |
|
Стандарт WIA |
|
Расходные материалы |
|
Ресурс ч/б картриджа/тонера |
21 000 |
Ресурс цветного картриджа/тонера |
14 000 |
Количество картриджей |
4 |
Печать на: |
|
Рулоне |
|
Фотобумаге |
|
CD/DVD |
|
Матовой бумаге |
![]() |
Этикетках |
![]() |
Конвертах |
![]() |
Пленках |
![]() |
Глянцевой бумаге |
![]() |
Карточках |
![]() |
Плотность бумаги |
|
Максимальная | 256 |
Минимальная | 60 |
Факс |
|
Цветной |
|
Телефон |
|
Проводная трубка |
|
АОН |
|
Caller ID |
|
Автоответчик |
|
Стандарт DECT |
|
Беспроводная трубка |
|
Спикерфон |
|
Языки управления |
|
PPDS |
|
PCL 5e |
|
PostScript 2 |
|
PCL 5c |
![]() |
PostScript |
![]() |
PostScript 3 |
![]() |
PCL 6 |
![]() |
![]() |
|
Лотки |
|
Емкость лотка ручной подачи |
100 |
Подача бумаги |
|
Максимальная | 1 850 |
Стандартная | 850 |
Вывод бумаги |
|
Максимальный | 500 |
Стандартный | 500 |
Финишер |
|
Степлер |
|
Сортер |
|
Электронная сортировка |
|
Брошюровщик |
|
Интерфейсы |
|
Версия USB |
2,0 |
RS-232 |
|
Bluetooth |
|
FireWire (IEEE 1394) |
|
Wi-Fi |
|
Устройство для чтения карт памяти |
|
Инфракрасный порт |
|
USB |
![]() |
LPT |
![]() |
Ethernet (RJ-45) |
![]() |
Память/Процессор |
|
Частота процессора |
600 |
Макс, объем памяти |
768 |
Объем памяти |
256 |
Дополнительная информация |
|
Экран |
|
Поддержка ОС |
|
Linux |
|
Windows |
![]() |
Mac OS |
![]() |
Уровень шума |
|
При работе | 53 |
В режиме ожидания | 40 |
Габариты |
|
Вес |
64,3 |
Глубина |
608 |
Высота |
645 |
Ширина |
823 |
Модули
MECH-202
MECH-081
MECH-251
MECH-101
MECH-232
MECH-133
MECH-031
MECH-071
MECH-221
MECH-162
MECH-051
MECH-011
ELEC-012A
MECH-021
MECH-181
MECH-041
CASE-011
MECH-121
MECH-091
MECH-211
MECH-061
MECH-141
MECH-151
MECH-171
MECH-111
MECH-192
MECH-241
Детали MECH-041
Деталь: | GEAR 18T |
Парткод: | 1429268 |
Деталь: | GEAR 18T |
Парткод: | 1429269 |
Деталь: | GEAR 37T |
Парткод: | 1429270 |
Деталь: | GEAR 81/17T |
Парткод: | 1429271 |
Деталь: | SCREW |
Парткод: | 1497961 |
Деталь: | HOLDER |
Парткод: | 1429272 |
Деталь: | BUSHING |
Парткод: | 1213118 |
Деталь: | GEAR 16T |
Парткод: | 1429279 |
Деталь: | GEAR 22T |
Парткод: | 1429280 |
Деталь: | GEAR 20T |
Парткод: | 1429283 |
Деталь: | CLUTCH |
Парткод: | 1424236 |
Деталь: | GEAR 41T |
Парткод: | 1429284 |
Деталь: | PULSE MOTOR |
Парткод: | 2107251 |
Деталь: | FUSER DRIVE ASSY |
Парткод: | 2125210 |
Деталь: | PLATE SPRING |
Парткод: | 1428814 |
Деталь: | SCREW |
Парткод: | 1498097 |
Деталь: | PRESSURE SPRING |
Парткод: | 1428821 |
Деталь: | GEAR 30T |
Парткод: | 1428826 |
Деталь: | SKEW ADJUSTMENT ASSY |
Парткод: | 1428832 |
Деталь: | P/H ASSY |
Парткод: | 2143693 |
Деталь: | WASHER |
Парткод: | 1046909 |
Деталь: | ROLLER |
Парткод: | 1424240 |
Деталь: | STOP RING |
Парткод: | 1083195 |
Деталь: | ROLLER ASSY |
Парткод: | 1424239 |
Деталь: | BUSHING |
Парткод: | 1046883 |
Деталь: | PIN |
Парткод: | 1429464 |
Деталь: | PAWL |
Парткод: | 1046886 |
Деталь: | ROLLER ASSY |
Парткод: | 1429466 |
Деталь: | IU CONTACT PLATE ASSY |
Парткод: | 1429110 |
Деталь: | REAR COVER |
Парткод: | 1429111 |
Деталь: | SCREW |
Парткод: | 1497961 |
Деталь: | HOLDER |
Парткод: | 1429112 |
Деталь: | COVER |
Парткод: | 1429113 |
Деталь: | REAR COVER |
Парткод: | 1429114 |
Деталь: | HV TRANSFORMER |
Парткод: | 2107241 |
Деталь: | CONTACT ASSY |
Парткод: | 1429117 |
Деталь: | CONTACT B ASSY |
Парткод: | 1429118 |
Деталь: | FUN MOTOR |
Парткод: | 1429400 |
Деталь: | HARNESS |
Парткод: | 2142904 |
Деталь: | LEFT COVER |
Парткод: | 1498258 |
Деталь: | FAN MOTOR |
Парткод: | 2108366 |
Деталь: | POWER CABLE |
Парткод: | 2080469 |
Деталь: | WASHER |
Парткод: | 1574055 |
Деталь: | SCREW |
Парткод: | 1429153 |
Деталь: | WIRE HARNESS ASSY |
Парткод: | 2108336 |
Деталь: | SCREW |
Парткод: | 1497961 |
Деталь: | SEAL |
Парткод: | 1429136 |
Деталь: | WIRE HARNESS ASSY |
Парткод: | 2108332 |
Деталь: | TRANSFER KIT |
Парткод: | 1495376 |
Деталь: | SWITCH ASSY |
Парткод: | 2108337 |
Деталь: | GUIDE ASSY |
Парткод: | 1543785 |
Деталь: | SHOULDER SCREW |
Парткод: | 1053408 |
Деталь: | HARNESS ASSY |
Парткод: | 2117414 |
Деталь: | PHOTO INTERRUPTER |
Парткод: | 2108435 |
Деталь: | ACTUATOR |
Парткод: | 1045733 |
Деталь: | SOLID STATE SWITCH |
Парткод: | 2108267 |
Деталь: | ACTUATOR |
Парткод: | 1428761 |
Деталь: | TENSION SPRING |
Парткод: | 1428762 |
Деталь: | HOLDER |
Парткод: | 1046860 |
Деталь: | PWB-I |
Парткод: | 2108268 |
Деталь: | LEVER |
Парткод: | 1046861 |
Деталь: | PHOTO INTERRUPTER |
Парткод: | 2108436 |
Деталь: | LEVER |
Парткод: | 1428766 |
Деталь: | SEAL |
Парткод: | 1428768 |
Деталь: | COVER |
Парткод: | 1497963 |
Деталь: | SIZE DETECTING PWB ASSY |
Парткод: | 2108269 |
Деталь: | LEFT COVER LOWER ASSY |
Парткод: | 1497964 |
Деталь: | GUIDE (MPC) |
Парткод: | 1466458 |
Деталь: | BRACKET |
Парткод: | 1454270 |
Деталь: | STEP SCREW |
Парткод: | 1454272 |
Деталь: | PWB ASSY |
Парткод: | 2122908 |
Деталь: | CONNECTOR ASSY |
Парткод: | 1428810 |
Деталь: | WIRE HARNESS ASSY |
Парткод: | 2123382 |
Деталь: | PU LIFT REAR ASSY |
Парткод: | 1428812 |
Деталь: | PU LIFT FRONT ASSY |
Парткод: | 1428813 |
Деталь: | POLYESTER FILM |
Парткод: | 1451731 |
Деталь: | GUIDE |
Парткод: | 1429297 |
Деталь: | TORSION SPRING |
Парткод: | 1429298 |
Деталь: | COLLAR |
Парткод: | 1429299 |
Деталь: | EARTH GROUND |
Парткод: | 1429300 |
Деталь: | BUSHING |
Парткод: | 1429302 |
Деталь: | ROLLER |
Парткод: | 1429303 |
Деталь: | ROLL |
Парткод: | 1429304 |
Деталь: | SHAFT |
Парткод: | 1429306 |
Деталь: | BRACKET |
Парткод: | 1429308 |
Деталь: | DUCT |
Парткод: | 1429311 |
Деталь: | GEAR 16T |
Парткод: | 1429312 |
Деталь: | PAPER EXIT DRIVE ASSY |
Парткод: | 1429313 |
Деталь: | CLUTCH |
Парткод: | 1429233 |
Деталь: | CLUTCH |
Парткод: | 1429234 |
Деталь: | TRANSFER DRIVE ASSY |
Парткод: | 2107249 |
Деталь: | GUIDE |
Парткод: | 1498092 |
Деталь: | ROLLER ASSY |
Парткод: | 1424239 |
Деталь: | PAPER GUIDE ASSY |
Парткод: | 1498093 |
Деталь: | ROLLER ASSY |
Парткод: | 1428798 |
Деталь: | EARTH PLATE |
Парткод: | 1466461 |
Деталь: | LEVER |
Парткод: | 1468423 |
Деталь: | PROTECTION |
Парткод: | 1428740 |
Деталь: | SWITCH |
Парткод: | 2035317 |
Деталь: | COVER |
Парткод: | 1428743 |
Деталь: | CAP |
Парткод: | 1497962 |
Деталь: | WIRE HARNESS |
Парткод: | 2108258 |
Деталь: | RUBBER FOOT |
Парткод: | 1046693 |
Деталь: | SEAL |
Парткод: | 1428748 |
Деталь: | SCREW |
Парткод: | 1498097 |
Деталь: | SCREW |
Парткод: | 1497961 |
Деталь: | POWER SUPPLY |
Парткод: | 2122912 |
Деталь: | FUN MOTOR |
Парткод: | 1429400 |
Деталь: | WIRE HARNESS ASSY |
Парткод: | 2117415 |
Деталь: | HARNESS |
Парткод: | 2120007 |
Деталь: | WIRE HARNESS ASSY |
Парткод: | 2108370 |
Деталь: | HARNESS ASSY |
Парткод: | 2123391 |
Деталь: | PWB ASSY |
Парткод: | 2122913 |
Деталь: | HARNESS ASSY |
Парткод: | 2123392 |
Деталь: | WIRE HARNESS ASSY |
Парткод: | 2108375 |
Деталь: | MAIN BODY CONTROL HARNESS |
Парткод: | 2123393 |
Деталь: | PWB-R |
Парткод: | 2107254 |
Деталь: | COVER,TYPE-B |
Парткод: | 1110073 |
Деталь: | FERRITE CORE |
Парткод: | 2123394 |
Деталь: | BOARD ASSY,MAIN |
Парткод: | 2122290 |
Деталь: | BOARD ASSY.,MEMORY |
Парткод: | 2129210 |
Деталь: | GUIDE RAIL |
Парткод: | 1012848 |
Деталь: | MICRO-SWITCH |
Парткод: | 2108261 |
Деталь: | SCREW |
Парткод: | 1497961 |
Деталь: | FRONT COVER SW ASSY |
Парткод: | 2115353 |
Деталь: | WIRE HARNESS ASSY |
Парткод: | 2108260 |
Деталь: | SWITCH |
Парткод: | 2036353 |
Деталь: | SHOULDER SCREW |
Парткод: | 1458118 |
Деталь: | TORSION SPRING |
Парткод: | 1428752 |
Деталь: | COVER |
Парткод: | 1428754 |
Деталь: | INNER COVER ASSY |
Парткод: | 1467171 |
Деталь: | TRAY |
Парткод: | 1498076 |
Деталь: | COVER |
Парткод: | 1498079 |
Деталь: | HARNESS ASSY |
Парткод: | 2108270 |
Деталь: | ACTUATOR |
Парткод: | 1428775 |
Деталь: | PHOTO INTERRUPTER |
Парткод: | 2108404 |
Деталь: | TRAY |
Парткод: | 1498080 |
Деталь: | LABEL CAUTION |
Парткод: | 1428778 |
Деталь: | COVER |
Парткод: | 1498081 |
Деталь: | HOLD PLATE |
Парткод: | 1428780 |
Деталь: | GUIDE |
Парткод: | 1428783 |
Деталь: | COVER |
Парткод: | 1498082 |
Деталь: | SCREW |
Парткод: | 1497961 |
Деталь: | GEAR 13/18T |
Парткод: | 1428786 |
Деталь: | LIFTING PLATE |
Парткод: | 1498083 |
Деталь: | FRICTION SHEET |
Парткод: | 1242317 |
Деталь: | BRAKE |
Парткод: | 1428788 |
Деталь: | HOLDER |
Парткод: | 1498084 |
Деталь: | PAPER GUIDE R ASSY |
Парткод: | 1498087 |
Деталь: | PAPER GUIDE F ASSY |
Парткод: | 1498089 |
Деталь: | CUSHION |
Парткод: | 1428794 |
Деталь: | Manual Feed Tray Unit |
Парткод: | 2122907 |
Деталь: | TOP COVER |
Парткод: | 1497950 |
Деталь: | COVER |
Парткод: | 1497951 |
Деталь: | TOP COVER |
Парткод: | 1497952 |
Деталь: | RIGHT COVER |
Парткод: | 1497953 |
Деталь: | CLEANING PAD |
Парткод: | 1463958 |
Деталь: | BAND |
Парткод: | 1428669 |
Деталь: | MAGNET |
Парткод: | 1442709 |
Деталь: | CLEANING MATERIAL |
Парткод: | 1451729 |
Деталь: | CONTROL PANEL |
Парткод: | 2120010 |
Деталь: | LEFT COVER |
Парткод: | 1497956 |
Деталь: | LEFT COVER |
Парткод: | 1497957 |
Деталь: | SHOULDER SCREW |
Парткод: | 1428678 |
Деталь: | REAR COVER |
Парткод: | 1428680 |
Деталь: | RIGHT COVER |
Парткод: | 1497958 |
Деталь: | COVER ASSY |
Парткод: | 1497960 |
Деталь: | LABEL,PAPER SIZE |
Парткод: | 1489684 |
Деталь: | LABEL,UNIT NAME |
Парткод: | 1489669 |
Деталь: | CAP |
Парткод: | 1497962 |
Деталь: | WIRE HARNESS ASSY |
Парткод: | 2108332 |
Деталь: | BRASHLESS MOTOR |
Парткод: | 2107242 |
Деталь: | BRASHLESS MOTOR |
Парткод: | 2107243 |
Деталь: | HOPPER DRIVE ASSY |
Парткод: | 2110971 |
Деталь: | DEVELOP DRIVE ASSY |
Парткод: | 2110972 |
Деталь: | FAN MOTOR |
Парткод: | 2108333 |
Деталь: | SCREW |
Парткод: | 1429153 |
Деталь: | RAIL |
Парткод: | 1428852 |
Деталь: | PAWL |
Парткод: | 1428854 |
Деталь: | LABEL K |
Парткод: | 1428855 |
Деталь: | LABEL C |
Парткод: | 1428856 |
Деталь: | LABEL M |
Парткод: | 1428857 |
Деталь: | LABEL Y |
Парткод: | 1428858 |
Деталь: | WIRE HARNESS ASSY |
Парткод: | 2108440 |
Деталь: | RAIL |
Парткод: | 1498105 |
Деталь: | RAIL |
Парткод: | 1498107 |
Деталь: | RAIL |
Парткод: | 1498109 |
Деталь: | STIRRING MEMBER |
Парткод: | 1428864 |
Деталь: | SEAL |
Парткод: | 1429106 |
Деталь: | GUIDE ASSY |
Парткод: | 1429108 |
Деталь: | STIRRING MEMBER |
Парткод: | 1439353 |
Деталь: | SEAL(T/C SEAL) |
Парткод: | 1467173 |
Деталь: | Neutralizing Brush |
Парткод: | 1429286 |
Деталь: | SCREW |
Парткод: | 1429153 |
Деталь: | FAN MOTOR |
Парткод: | 2108356 |
Деталь: | GUIDE |
Парткод: | 1429289 |
Деталь: | EARTH GROUND |
Парткод: | 1429290 |
Деталь: | WIRE HARNESS ASSY |
Парткод: | 2108336 |
Деталь: | COVER |
Парткод: | 1498128 |
Деталь: | PAPER EXIT COVER ASSY |
Парткод: | 1498135 |
Деталь: | CLUTCH ASSY |
Парткод: | 1424233 |
Деталь: | BUSHING |
Парткод: | 1046739 |
Деталь: | GEAR 30T |
Парткод: | 1428800 |
Деталь: | GEAR 30T |
Парткод: | 1428801 |
Деталь: | BUSHING |
Парткод: | 1217624 |
Деталь: | CAM |
Парткод: | 1428802 |
Деталь: | ROLLER |
Парткод: | 1213567 |
Деталь: | STOP RING |
Парткод: | 1058361 |
Деталь: | GEAR 25T |
Парткод: | 1428804 |
Деталь: | CLUTCH |
Парткод: | 1424234 |
Деталь: | SOLENOID |
Парткод: | 1450639 |
Деталь: | PHOTO INTERRUPTER |
Парткод: | 2108404 |
Деталь: | BUSHING |
Парткод: | 1428808 |
Деталь: | SHIELD PLATE |
Парткод: | 1428809 |
Деталь: | ROLLER |
Парткод: | 1429177 |
Деталь: | SOLID STATE SWITCH |
Парткод: | 2108340 |
Деталь: | ROLLER |
Парткод: | 1429184 |
Деталь: | SHOULDER SCREW |
Парткод: | 1448554 |
Деталь: | BUSHING |
Парткод: | 1429190 |
Деталь: | GEAR 20T |
Парткод: | 1429191 |
Деталь: | GEAR 14T |
Парткод: | 1429192 |
Деталь: | RESISTOR |
Парткод: | 2108341 |
Деталь: | ACTUATOR |
Парткод: | 1429206 |
Деталь: | PRISM |
Парткод: | 1429207 |
Деталь: | PHOTO SENSING ELEMENT |
Парткод: | 2123384 |
Деталь: | PHOTO INTERRUPUTER |
Парткод: | 2077353 |
Деталь: | WIRE HARNESS ASSY |
Парткод: | 2108346 |
Деталь: | HUMIDITY CONVERTION EL. |
Парткод: | 2108347 |
Деталь: | TORSION SPRING |
Парткод: | 1045731 |
Деталь: | CLUTCH |
Парткод: | 1424236 |
Деталь: | SEAL |
Парткод: | 1429212 |
Деталь: | COVER |
Парткод: | 1429213 |
Деталь: | SEAL |
Парткод: | 1467174 |
Деталь: | HANDLE ASSY |
Парткод: | 1429216 |
Деталь: | VERT.TRANSFER UNIT |
Парткод: | 2117289 |
Деталь: | COVER |
Парткод: | 1498119 |
Деталь: | CAM |
Парткод: | 1429219 |
Деталь: | HOLDER |
Парткод: | 1429221 |
Деталь: | SCREW |
Парткод: | 1429153 |
Деталь: | LEVER |
Парткод: | 1429222 |
Деталь: | PRESSURE SPRING |
Парткод: | 1429225 |
Деталь: | SHOULDER SCREW |
Парткод: | 1429230 |
Деталь: | STOPPER |
Парткод: | 1429231 |
Деталь: | LABEL,PAPER CAUTION,MP, B |
Парткод: | 1489674 |
Деталь: | LABEL,COVER A |
Парткод: | 1489673 |
Деталь: | DOOR ASSY |
Парткод: | 1495378 |
Деталь: | ROLLER ASSY |
Парткод: | 1440112 |
Деталь: | GEAR 18T |
Парткод: | 1429236 |
Деталь: | GEAR 18T |
Парткод: | 1429238 |
Деталь: | GEAR 18/30T |
Парткод: | 1429239 |
Деталь: | BUSHING |
Парткод: | 1429240 |
Деталь: | SCREW |
Парткод: | 1429244 |
Деталь: | GEAR 16T |
Парткод: | 1429247 |
Деталь: | BUSHING |
Парткод: | 1429248 |
Деталь: | PHOTO INTERRUPTER |
Парткод: | 2108404 |
Деталь: | GEAR 32/30T |
Парткод: | 1429251 |
Деталь: | GEAR 32T |
Парткод: | 1429252 |
Деталь: | PIPE ASSY |
Парткод: | 1429255 |
Деталь: | RAIL |
Парткод: | 1429126 |
Деталь: | LABEL K |
Парткод: | 1429127 |
Деталь: | LABEL C |
Парткод: | 1429128 |
Деталь: | LABEL M |
Парткод: | 1429129 |
Деталь: | LABEL Y |
Парткод: | 1429130 |
Деталь: | REINFORCE PLATE |
Парткод: | 1429131 |
Деталь: | SEAL |
Парткод: | 1429137 |
Деталь: | REINFORCE PLATE |
Парткод: | 1429140 |
Деталь: | ERASER YMC ASSY |
Парткод: | 1429142 |
Деталь: | ERASER K ASSY |
Парткод: | 1429143 |
Деталь: | PIPE YMC ASSY |
Парткод: | 1429145 |
Деталь: | SEAL(E) |
Парткод: | 1457128 |
Деталь: | SEAL(IU RAIL UNDER) |
Парткод: | 1457129 |
Деталь: | SEAL(IU RAIL BACK) |
Парткод: | 1457130 |
Деталь: | POLYESTER FILM |
Парткод: | 1457131 |
Деталь: | POLYESTER FILM |
Парткод: | 1457132 |
Деталь: | FUSING UNIT 230V |
Парткод: | 2122911 |
Деталь: | WIRE HARNESS ASSY |
Парткод: | 2108348 |
Деталь: | ACTUATOR |
Парткод: | 1486332 |
Деталь: | LIFTING PLATE |
Парткод: | 1498275 |
Деталь: | FRICTION SHEET |
Парткод: | 1242317 |
Деталь: | REGULATING PLATE |
Парткод: | 1498276 |
Деталь: | LABEL,MPC SCALE, CD |
Парткод: | 1423969 |
Деталь: | PRESSURE SPRING |
Парткод: | 1452499 |
Деталь: | LEVER |
Парткод: | 1498277 |
Деталь: | GUIDE |
Парткод: | 1429433 |
Деталь: | GUIDE |
Парткод: | 1242312 |
Деталь: | LOCK LEVER |
Парткод: | 1046907 |
Деталь: | PRESSURE SPRING |
Парткод: | 1046906 |
Деталь: | COVER |
Парткод: | 1498279 |
Деталь: | LABEL,C1 |
Парткод: | 1489676 |
Деталь: | HANDLE |
Парткод: | 1498280 |
Деталь: | COVER |
Парткод: | 1498281 |
Деталь: | SCREW |
Парткод: | 1429153 |
Деталь: | LEVER |
Парткод: | 1429443 |
Деталь: | SPACER |
Парткод: | 1498282 |
Деталь: | RACK |
Парткод: | 1429446 |
Деталь: | GEAR 20T |
Парткод: | 1046897 |
Деталь: | SPACER |
Парткод: | 1498283 |
Деталь: | SPACER |
Парткод: | 1429449 |
Деталь: | REGULATING PLATE |
Парткод: | 1498284 |
Деталь: | LABEL |
Парткод: | 1498285 |
Деталь: | MULTIPURPOSE CASSETTE |
Парткод: | 1495385 |
Деталь: | REGULATING PLATE R ASSY |
Парткод: | 1498286 |
Коды ошибок
C0000 ... C0799
C0800
C0998
C0999
C1000 ... C1002
C1010
C1020
C1021
C1100
C1101
C1120
C1121
C1122
C1123
C1200
C1210
C1300
C1400
C1500
C1550
C1600
C1700
C1800
C1999
C2000
E100
E101
E102
E103
E110
E111
E112
E113
E200
E210
E220
E300
E301
E302
E303
E304
E305
E310
E400
E401
E402
E403
E404
E405
E406
E407
E500
E501
E510
E511
E520
E521
E550
E551
E552
E553
E554
E555
E556
E600
E601
E602
E603
E610
E611
E612
E620
E621
E630
E631
E640
E641
E701
E702
E703
E704
E900
E901
E998
Описание
Error code: | C0000 ... C0799 |
Description: | CPU error |
Causes: | Controller Board. Noise, etc. |
Error code: | C0800 |
Description: | Image processing error |
Causes: | The print sequence jam (J010x) was detected 2 times continuously. |
Remedy: | 1 Checking the image data The image data is faulty. When this issue occurs only when handling the certain image data, check if the image data is faulty. 2 Checking the situation The printing operation of the certain file is faulty. Acquire the jobs log if the phenomenon can be reproduced by specifying the job when the error was detected.` 3 Checking the connection The connector is not properly connected. Or, the wire is faulty. Reinsert all the connectors on the main PWB. If the wire is pinched by other parts or it is damaged, repair or replace the wire. Detaching and reattaching the main PWB 4 Replacing the main PWB The main PWB is faulty. Replace the main PWB. Detaching and reattaching the main PWB |
Error code: | C0998 |
Description: | Shift transfer |
Causes: | Controller Board. Video I/F Cable. Mechanical Control Board |
Remedy: | 1 I/O check for Shifter Return Position Sensor operation: the voltage across PJ7A-7A on Control Board and GND is DC5V (sensor unblocked) and DC0V (sensor blocked). YES Change Control Board. NO Change sensor or Cabinet Transport Board. Change flat cable. 2 I/O check for Shifter Home Position Sensor operation: the voltage across PJ7A-8A on Control Board and GND is DC5V (sensor unblocked) and DC0V (sensor blocked). YES Change Control Board. NO Change sensor or Cabinet Transport Board. Change flat cable. |
Error code: | C0999 |
Description: | Shift return |
Causes: | Code DIMM |
Remedy: | 1 Lift 2 ascends after the LCC Lift-Up Motor has been energized. NO: Correct drive coupling (oneway gear engagement, coupling engagement, spring operation, and belt tension). 2 I/O check for Lift-Up Sensor 2 operation: the voltage across CN4A-9 on LCC Control Board and GND is DC 0 V when the sensor is unblocked and DC 5 V when the sensor is blocked (during lifting motion detection). YES: Change LCC Control Board. NO: Check sensor for installation. Check sensor connector for connection. Change sensor. |
Error code: | C1000 ... C1002 |
Description: | Standard RAM error (When the standard size is not determined, etc.) |
Causes: | Std. RAM DIMM |
Error code: | C1010 |
Description: | Lift motor 1 error |
Causes: | Either of the following was detected 5 times continuously. 1. Lift sensor 2 does not turn on when passing 12s after cassette 1 is installed. 2. The lock-up signal is not released for 1s after lift motor 1 turns on. |
Remedy: | 1 Checking the cassette base The cassette base does not operate properly. Repair or replace the cassette base if it cannot move vertically. 2 Checking the drive gear The drive gear to lift up the cassette base does not rotate properly. Check if the drive gears to lift up the cassette base rotate smoothly or have no excessive load. And apply the grease to the frictional parts and repair the related parts so that they can rotate smoothly. 3 Checking the wire The connector is not properly connected. Or, the wire is faulty. Clean the terminal of the following wire connectors and reconnect the connectors. If there is no continuity, replace the wire. • Lift motor 1 - Feed PWB Wiring diagram 4 Checking lift motor 1 Lift motor 1 is faulty. Check the operation of lift motor 1, and replace it if necessary. Detaching and reattaching the lift motor 5 Checking the wire The connector is not properly connected. Or, the wire is faulty. Clean the terminal of the following wire connectors and reconnect the connectors. If there is no continuity, replace the wire. • Lift sensor 1 - Feed PWB Wiring diagram 6 Checking the sensor Lift sensor 1 is not properly attached or faulty. Reattach lift sensor 1. If not repaired, replace the sensor. 7 Replacing the feed PWB The feed PWB is faulty. Replace the feed PWB. 8 Firmware upgrade The firmware is not the latest version. Upgrade the engine firmware to the latest version Firmware Update 9 Replacing the engine PWB The engine PWB is faulty. Replace the engine PWB. Detaching and reattaching the engine PWB |
Error code: | C1020 |
Description: | Lift motor 2 error |
Causes: | Either of the following was detected 5 times continuously. 1. Lift sensor 2 does not turn on when passing 12s after cassette 2 is installed. 2. The lock-up signal is not released for 1s after lift motor 2 turns on. |
Remedy: | 1 Checking the cassette base The cassette base does not operate properly. Repair or replace the cassette base if it cannot move vertically. 2 Checking the drive gear The drive gear to lift up the cassette base does not rotate properly. Check if the drive gears to lift up the cassette base rotate smoothly or have no excessive load. And apply the grease to the frictional parts and repair the related parts so that they can rotate smoothly. 3 Checking the wire The connector is not properly connected. Or, the wire is faulty. Clean the terminal of the following wire connectors and reconnect the connectors. If there is no continuity, replace the wire. •Lift motor 2 - Feed PWB Wiring diagram 4 Checking lift motor 2 Lift motor 2 is faulty. Check the operation of lift motor 2, and replace it if necessary. Detaching and reattaching the lift motor 5 Checking the connection The connector is not properly connected. Or, the wire is faulty. Clean the terminal of the following wire connectors and reconnect the connectors. If there is no continuity, replace the wire. • Lift sensor 2 - Feed PWB Wiring diagram 6 Checking the sensor Lift sensor 2 is not properly attached or faulty. Reattach lift sensor 2. If not repaired, replace the sensor. 7 Replacing the feed PWB The feed PWB is faulty. Replace the feed PWB. 8 Firmware upgrade The firmware is not the latest version. Upgrade the engine firmware to the latest version Firmware Update 9 Replacing the engine PWB The engine PWB is faulty. Replace the engine PWB. Detaching and reattaching the engine PWB |
Error code: | C1021 |
Description: | RAM error (slot 1) |
Causes: | Controller Board. Opt. RAM DIMM |
Error code: | C1100 |
Description: | PF lift motor 1 error |
Causes: | [The right cassette section of the large capacity feeder for the main unit] The lift error continued 5 times because one of the phenomena below. 1. PF lift sensor 1 does not turn on when passing 23s while PF lift motor 1 turns on for the first time after inserting the cassette. 2. PF lift sensor 1 does not turn on when passing 2s while PF lift motor 1 turns on for the second time or later after inserting the cassette. 3. The excess lift current protection monitor signal turning on for 1s or more is detected while the PF lift motor 1 is operating. |
Remedy: | 1 Checking the cassette base The cassette base does not operate properly. Repair or replace the cassette base if it cannot move vertically. 2 Checking the drive gear The drive gear to lift up the cassette base does not rotate properly. Check if the drive gears to lift up the cassette base rotate smoothly or have no excessive load. And apply the grease to the frictional parts and repair the related parts so that they can rotate smoothly. 3 Checking the connection The connector is not properly connected. Or, the wire is faulty. Clean the terminal of the following wire connectors and reconnect the connectors. If there is no continuity, replace the wire. • PF lift motor 1 - PF main PWB Wiring diagram 4 Checking PF lift motor 1 PF lift motor 1 is faulty. Replace PF lift motor 1. 5 Checking the connection The connector is not properly connected. Or, the wire is faulty. Clean the terminal of the following wire connectors and reconnect the connectors. If there is no continuity, replace the wire. • PF lift sensor 1 - PF main PWB Wiring diagram 6 Checking the sensor PF lift sensor 1 is not properly attached or faulty. Reattach PF lift sensor 1. If not repaired, replace the sensor. 7 Replacing the PF main PWB The PF main PWB is faulty. Replace the PF main PWB. Detaching and reattaching the PF main PWB |
Error code: | C1101 |
Description: | Shift roller motor drive failure |
Causes: | Code DIMM |
Error code: | C1120 |
Description: | PF left lift position problem (optional 3000-sheet paper feeder) Level switch 1 does not turn on within 30 s of PF lift motor 2 turning on. |
Causes: | Poor contact in the connector terminals. Defective level switch 1. Defective PF lift motor 2. The PF left lift does not rise properly. |
Remedy: | Poor contact in the connector terminals. Check the connection of connector YC27 on the engine PWB and the connector on the PF main PWB, and the continuity across the connector terminals. Repair or replace if necessary. Defective level switch 1. Check if YC5-4 on the PF main PWB goes low when level switch 1 is turned off. If not, replace PF lift switch 1. Defective PF lift motor 1. Check for continuity across the coil. If none, replace PF lift motor 1. The PF left lift does not rise properly. Check the gears and belts, and remedy if necessary. |
Error code: | C1121 |
Description: | ROM Checksum Error (bit 8 -15) (Program) |
Causes: | Code DIMM |
Remedy: | 1 PROG ROM is defective. Replace ROM-DIMM mounted in CN8/ROM-DIMM socket, and confirm correct operation. Replace ROM DIMM. 2 C232 MAIN board is defective Replace the board. |
Error code: | C1122 |
Description: | ROM Checksum Error (bit16 - 23) (Program) |
Causes: | Code DIMM |
Remedy: | 1 PROG ROM is defective. Replace ROM-DIMM mounted in CN8/ROM-DIMM socket, and confirm correct operation. Replace ROM DIMM. 2 C232 MAIN board is defective Replace the board. |
Error code: | C1123 |
Description: | ROM Checksum Error (bit24-31) (Program) |
Causes: | Code DIMM |
Remedy: | 1 PROG ROM is defective. Replace ROM-DIMM mounted in CN8/ROM-DIMM socket, and confirm correct operation. Replace ROM DIMM. 2 C232 MAIN board is defective Replace the board. |
Error code: | C1200 |
Description: | Duplex side registration motor error • The duplex side registration home position sensor does not detect the home position of the side registration guide. |
Causes: | Defective duplex side registration home position sensor. Defective duplex side registration motor. Defective duplex PWB. |
Remedy: | Defective duplex side registration home position sensor. Check the connection of connector YC29 on the engine PWB and the connector YC1 on the duplex PWB. Repair or replace if necessary. Defective duplex side registration motor. Replace the duplex side registration motor. Defective duplex PWB. Replace the duplex PWB. |
Error code: | C1210 |
Description: | Side registration home position sensor detection error • The side registration home position sensor does not detect home position of side registration guides. • Detection occurs twice continuously after the duplex unit is removed and then inserted. |
Causes: | Defective side registration home position sensor. Defective side registration motor. Defective engine controller PCB. |
Remedy: | Replace the side registration home position sensor. Replace the side registration motor. Replace the engine controller PCB and check for correct operation. |
Error code: | C1300 |
Description: | Cutter motor error • The cutter has not returned to its home position after a certain amount of time (900 ms) when the main switch is turned on or when the detachable unit, eject cover or lower right cover is opened/closed. |
Causes: | The cutter motor connector terminals are loosely connected or are making poor contact. The cutter motor does not operate correctly. The left or right cutter home position switch is defective. The engine main PCB is defective. |
Remedy: | Reinsert the connector. Also check for continuity across the terminal wire and if none, remedy or replace the cutter unit. Replace the cutter unit. Replace the cutter unit. Replace the engine main PCB and check for correct operation. |
Error code: | C1400 |
Description: | Rotary guide motor error Rotary guide sensor does not turn on. |
Causes: | Poor contact in the connector terminals. Broken gear s or couplings of rotary guide motor. Defective rotary guide motor. Defective rotary guide sensor. Poor contact in the connector terminals. Defective PWB. |
Remedy: | Poor contact in the connector terminals. Check the connection of connector of the rotary guide motor and the connector YC2 on the main front PWB, and the continuity across the connector terminals. Repair or replace if necessary. Broken gears or couplings of rotary guide motor. Replace rotary guide motor. Defective rotary guide motor. Check for continuity across the coil. If none, replace rotary guide motor. Defective rotary guide sensor. Check if YC2-8 on the main front PWB goes low when rotary guide sensor is turned off. If not, replace rotary guide sensor. Poor contact in the connector terminals. Check the connection of connector of the rotary guide sensor and the connector YC2 on the main front PWB, and the continuity across the connector terminals. Repair or replace if necessary. Defective PWB. Main front PWB or engine PWB and check for correct operation. |
Error code: | C1500 |
Description: | CCNV hardware error |
Causes: | Controller Board |
Error code: | C1550 |
Description: | Compression SRAM initialization hardware error |
Causes: | Controller Board |
Error code: | C1600 |
Description: | Video related hardware error (including PWM IC calibration error) |
Causes: | Controller Board |
Error code: | C1700 |
Description: | Built-in network hardware error |
Error code: | C1800 |
Description: | Large capacity feeder communication error Condition: When turning the main power off and on while disconnecting the connector of the cable from the side multi feeder, this service call error does not reappear. (It is caused by the large capacity feeder.) |
Causes: | The communication error was detected 10 times continuously. |
Remedy: | 1 Firmware upgrade The firmware is not the latest version. Upgrade the engine firmware and the large capacity feeder firmware to the latest version. Firmware Update 2 Checking the connection The connector is not properly connected. Or, the wire is faulty. Clean the terminal of the following wire connectors and reconnect the connectors. If there is no continuity, replace the wire. • PF main PWB (Large capacity feeder) - PF main PWB (Side multi feeder) • PF main PWB (Side multi feeder) - Engine PWB Wiring diagram 3 Replacing the PF main PWB The PF main PWB is faulty. Replace the PF main PWB. (Large capacity feeder) Detaching and reattaching the PF main PWB (Large capacity feeder) 4 Replacing the PF main PWB The PF main PWB is faulty. Replace the PF main PWB. (Side multi feeder) Detaching and reattaching the PF main PWB (Side multi feeder) 5 Replacing the engine PWB The engine PWB is faulty. Replace the engine PWB. Detaching and reattaching the engine PWB |
Error code: | C1999 |
Description: | Other Hardware Error |
Causes: | Controller Board |
Error code: | C2000 |
Description: | Drive motor problem Stable OFF is detected for 1 s continuously after drive motor stability. The drive motor is not stabilized in 6 s since the motor is activated. |
Causes: | Poor contact in the connector terminals. Defective drive transmission system. Defective drive motor. Defective engine PWB. |
Remedy: | Poor contact in the connector terminals. Check the connection of connector YC11 on the engine PWB and the connector on the drive motor, and the continuity across the connector terminals. Repair or replace if necessary. Defective drive transmission system. Check if the rollers and gears rotate smoothly. If not, grease the bushings and gears. Check for broken gears and replace if any. Defective drive motor. Replace the drive motor. Defective engine PWB. Replace the engine PWB and check for correct operation. |
Error code: | E100 |
Display: | E100 error Vacuum pump |
Description: | Abnormal condition in vacuum pump. |
Causes: | • PH Unit • PH Interface Board (PWB-D) • Mechanical Control Board (PWB-M) |
Remedy: | (1) MAIN board assembly may be damaged. * Replace MAIN board assembly. |
Error code: | E101 |
Display: | E101 error Sub tank sensor |
Description: | Exposure lamp too long |
Causes: | • PH Unit • PH Interface Board (PWB-D) • Mechanical Control Board (PWB-M) |
Remedy: | (1) Sub tank sensor assembly may be damaged. * Replace sub tank assembly. (2) MAIN board assembly may be damaged. * Replace MAIN board assembly. |
Error code: | E102 |
Description: | Polygon Motor/Y failure to turn - The Polygon motor fails to turn stably even after the lapse of a given period of time after activating the Polygon motor. - Motor Lock signal detects H for a given period time consecutively during the Polygon motor is rotating. |
Causes: | • PH Unit • PH Interface Board (PWB-D) • Mechanical Control Board (PWB-M) |
Remedy: | 1 Check the connector for proper connection and correct as necessary. - - 2 Change PH Unit - - 3 Change PWB-D - - 4 Change PWB-M |
Error code: | E103 |
Description: | Frequency problem |
Causes: | • PH Unit • PH Interface Board (PWB-D) • Mechanical Control Board (PWB-M) |
Remedy: | 1 Check the connector for proper connection and correct as necessary. - - 2 Change PH Unit - - 3 Change PWB-D - - 4 Change PWB-M |
Error code: | E110 |
Description: | Transport jam during duplex printing (paper not reaching registration sensor): Paper which passed the reverse transport section does not reach the registration sensor during duplex printing. |
Causes: | Registration sensor ADU motor2 ADU board PFC board LGC board ADU roller |
Remedy: | (First page of printing) Open the jam access cover. Is there paper in front of the registration sensor? → YES → Remove the paper. NO Is the registration sensor working? (Perform the input check in the test mode: 03-[FAX]ON/[4]/[E]) ↓ → NO → 1. Check if the connector of the registration sensor is disconnected. 2. Check if the connector CN341 on the LGC board is disconnected. 3. Check if the connector pins are disconnected and the harnesses are open circuited. 4. Check if the conductor pattern on the LGC board is short circuited or open circuited. 5. Replace the registration sensor. 6. Replace the LGC board. YES Is the transport motor (M17) rotating? (Perform the output check in the test mode: 03-133,183) ↓ → NO → Replace the transport motor. 1. Check if the connector of the transport motor is disconnected. 2. Check if the connector CN327 on the LGC board is disconnected. 3. Check if the connector on the transport motor driving PC board is disconnected. 4. Check if the connector pins are disconnected and the harnesses are open circuited. 5. Check if the conductor pattern on the LGC board is short circuited or open circuited. 6. Check if the conductor pattern on the transport motor driving PC board is short circuited or open circuited. 7. Replace the LGC board. 8. Replace the transport motor driving PC board. YES Check if the spring of the follower roller of the intermediate transport roller is working properly. YES Check the transport roller. Clean or replace it. (Second page or later of printing) Leading edge of paper not reaching the fuser exit sensor. ↓ → YES → If the paper is damaged, remove the paper and check the followings. 1. Check if the paper is skewed, and correct it if it is skewed. 2. Check the paper amount. 3. Check if the paper is not the one with printing on its back side. 4. Check if the width of the side guides of the drawer is too narrow. 5. Check the motor-related adjustment value. NO Is the intermediate transport sensor working? (Perform the input check in the test mode: 03-[FAX]OFF/[1]/[A]) ll → NO → 1. Are paper dusts accumulated on the intermediate transport sensor? 2. Check if the harness is not damaged. 3. Check if the connector is disconnected. YES Is the transport motor rotating? (Perform the output check in the test mode: 03-133,183) NO → Replace the transport motor. 1. Check if the connector of the transport motor is disconnected. 2. Check if the connector on the LGC board is disconnected. 3. Check if the connector pins are disconnected and the harnesses are open circuited. 4. Check if the conductor pattern on the LGC board is short circuited or open circuited. 5. Replace the LGC board. YES Check if the spring of the follower roller of the intermediate transport roller is working properly. Replace the registration roller(rubber) if not solved. |
Error code: | E111 |
Description: | Laser malfunction (Magenta) - SOS signal is not detected within the lapse of a given period of time after staring the laser output. - SOS signal is not detected within a given period of time during printing or IDC sensor adjustment |
Causes: | • PH Unit • PH Interface Board (PWB-D) • Mechanical Control Board (PWB-M) |
Remedy: | 1 Check the connector for proper connection and correct as necessary. - - 2 Change PH Unit - - 3 Change PWB-D - - 4 Change PWB-M |
Error code: | E112 |
Description: | Laser malfunction (Yellow) - SOS signal is not detected within the lapse of a given period of time after staring the laser output. - SOS signal is not detected within a given period of time during printing or IDC sensor adjustment |
Causes: | • PH Unit • PH Interface Board (PWB-D) • Mechanical Control Board (PWB-M) |
Remedy: | 1 Check the connector for proper connection and correct as necessary. - - 2 Change PH Unit - - 3 Change PWB-D - - 4 Change PWB-M |
Error code: | E113 |
Display: | E113 error NVRAM |
Description: | Parameters cannot be written. |
Causes: | • PH Unit • PH Interface Board (PWB-D) • Mechanical Control Board (PWB-M) |
Remedy: | (1) MAIN board assembly may be damaged. * Replace MAIN board assembly. |
Error code: | E200 |
Description: | 1st drawer transport jam (paper not reaching registration sensor): Paper which has passed the 1st drawer transport sensor does not reach the registration sensor during the feeding at the 1st drawer. |
Causes: | Registration sensor Transport motor-1 PFC board LGC board Rollers |
Remedy: | (First page of printing) Open the jam access cover. Is there paper in front of the registration sensor? → YES → Replace the paper. NO Is the registration sensor(S18) working? (Perform the input check in the test mode: 03-[FAX]ON/[4]/[E]) ↓ → NO → 1. Check if the connector of the registration sensor is disconnected. 2. Check if the connector CN305 on the LGC board is disconnected. 3. Check if the connector pins are disconnected and the harnesses are open circuited. 4. Check if the conductor pattern on the LGC board is short circuited or open circuited. 5. Replace the registration sensor. 6. Replace the LGC board. YES 1. Check the transport roller. Replace it if it is worn out. (Second page or later of printing) Open the jam access cover. Is there any paper on the transport path? ↓ → YES → If the paper is damaged, remove the paper and check the followings 1. Check if the paper is skewed, and correct it if it is skewed. 2. Check the paper amount. 3. Check if the paper is not the one with printing on its back side. 4. Check if the width of the side guides of the drawer is too narrow. 5. Check the motor-related adjustment value. NO Is the intermediate transport sensor (S17) working? (Perform the input check in the test mode: 03-[FAX]OFF/[1]/[A]) ↓ → NO → 1. Are paper dusts accumulated on the intermediate transport sensor? 2. Check if the harness is not damaged. 3. Check if the connector is disconnected. YES Is the transport motor (M17) rotating? (Perform the output check in the test mode: 03-133,183) ↓ → NO → Check if the bearing of the transportation roller is locked. Replace the transport motor. 1. Check if the connector of the transport motor is disconnected. 2. Check if the connector CN327 on the LGC board is disconnected. 3. Check if the connector on the transport motor driving PC board is disconnected. 4. Check if the connector pins are disconnected and the harnesses are open circuited. 5. Check if the conductor pattern on the LGC board is short circuited or open circuited. 6. Replace the LGC board. 7. Replace the transport motor driving PC board. YES Check if the spring of the follower roller of the intermediate transport roller is working properly. Check if the registration roller (rubber) is rotating smoothly. |
Error code: | E210 |
Description: | 2nd drawer transport jam (paper not reaching registration sensor): Paper which has passed the 1st drawer transport sensor does not reach the registration sensor during the feeding at the 2nd drawer. |
Causes: | Registration sensor Transport motor-1 PFC board LGC board Rollers |
Remedy: | (First page of printing) Open the jam access cover. Is there paper in front of the registration sensor? → YES → Replace the paper. NO Is the registration sensor(S18) working? (Perform the input check in the test mode: 03-[FAX]ON/[4]/[E]) ↓ → NO → 1. Check if the connector of the registration sensor is disconnected. 2. Check if the connector CN305 on the LGC board is disconnected. 3. Check if the connector pins are disconnected and the harnesses are open circuited. 4. Check if the conductor pattern on the LGC board is short circuited or open circuited. 5. Replace the registration sensor. 6. Replace the LGC board. YES 1. Check the transport roller. Replace it if it is worn out. (Second page or later of printing) Open the jam access cover. Is there any paper on the transport path? ↓ → YES → If the paper is damaged, remove the paper and check the followings 1. Check if the paper is skewed, and correct it if it is skewed. 2. Check the paper amount. 3. Check if the paper is not the one with printing on its back side. 4. Check if the width of the side guides of the drawer is too narrow. 5. Check the motor-related adjustment value. NO Is the intermediate transport sensor (S17) working? (Perform the input check in the test mode: 03-[FAX]OFF/[1]/[A]) ↓ → NO → 1. Are paper dusts accumulated on the intermediate transport sensor? 2. Check if the harness is not damaged. 3. Check if the connector is disconnected. YES Is the transport motor (M17) rotating? (Perform the output check in the test mode: 03-133,183) ↓ → NO → Check if the bearing of the transportation roller is locked. Replace the transport motor. 1. Check if the connector of the transport motor is disconnected. 2. Check if the connector CN327 on the LGC board is disconnected. 3. Check if the connector on the transport motor driving PC board is disconnected. 4. Check if the connector pins are disconnected and the harnesses are open circuited. 5. Check if the conductor pattern on the LGC board is short circuited or open circuited. 6. Replace the LGC board. 7. Replace the transport motor driving PC board. YES Check if the spring of the follower roller of the intermediate transport roller is working properly. Check if the registration roller (rubber) is rotating smoothly. |
Error code: | E220 |
Description: | 2nd drawer transport jam (paper not reaching 1st drawer transport sensor): Paper which has passed the 2nd drawer transport sensor does not reach the 1st drawer transport sensor during the feeding at the 2nd drawer. |
Causes: | 1st drawer transport sensor Transport motor-2 Transport motor-1 PFC board Rollers |
Remedy: | (First page of printing) Open the jam access cover. Is there paper in front of the 1st drawer transport sensor? → YES → Remove the paper. NO Is the 1st drawer transport sensor (S33) working? (Perform the input check in the test mode: 03-[FAX]OFF/[1]/[C]) ↓ → NO → 1. Check if the connector of the 1st drawer transport sensor is disconnected. 2. Check if the connector CN329 on the LGC board is disconnected. 3. Check if the connector pins are disconnected and the harnesses are open circuited. 4. Check if the conductor pattern on the LGC board is short circuited or open circuited. 5. Replace the 1st drawer transport sensor. 6. Replace the LGC board. YES Are the transport clutches (CLT5,7,9,11) working? (Perform the output check in the test mode: 03-210/225/229/230/231) ↓ → NO → 1. Check if the connectors of the transport clutches are disconnected. 2. Check if the connector CN328,329,350 on the LGC board is disconnected. 3. Check if the connector pins are disconnected and the harnesses are open circuited. 4. Check if the conductor pattern on the LGC board is short circuited or open circuited. 5. Replace the transport clutches. 6. Replace the LGC board. YES 1. Check the condition of the feed roller, separation roller and pickup roller of each paper source, and clean or replace them. 2. Check the transport roller. Clean or replace it. (Second page or later of printing) Open the jam access cover. Is there any paper on the transport path? ↓ → YES → If the paper is damaged, remove the paper and check the followings: 1. Check if the paper is skewed, and correct it if it is skewed. 2. Check the paper amount. 3. Check if the paper is not the one with printing on its back side. 4. Check if the width of the side guides of the drawer is too narrow. 5. Check the motor-related adjustment value. NO Check if the spring of the follower roller of the intermediate transport roller is working properly. |
Error code: | E300 |
Description: | 3rd drawer transport jam (paper not reaching registration sensor): Paper which has passed the 1st drawer transport sensor does not reach the registration sensor during the feeding at the 3rd drawer. |
Causes: | Registration sensor Transport motor-1 PFC board LGC board Rollers |
Remedy: | (First page of printing) Open the jam access cover. Is there paper in front of the registration sensor? → YES → Replace the paper. NO Is the registration sensor(S18) working? (Perform the input check in the test mode: 03-[FAX]ON/[4]/[E]) ↓ → NO → 1. Check if the connector of the registration sensor is disconnected. 2. Check if the connector CN305 on the LGC board is disconnected. 3. Check if the connector pins are disconnected and the harnesses are open circuited. 4. Check if the conductor pattern on the LGC board is short circuited or open circuited. 5. Replace the registration sensor. 6. Replace the LGC board. YES 1. Check the transport roller. Replace it if it is worn out. (Second page or later of printing) Open the jam access cover. Is there any paper on the transport path? ↓ → YES → If the paper is damaged, remove the paper and check the followings 1. Check if the paper is skewed, and correct it if it is skewed. 2. Check the paper amount. 3. Check if the paper is not the one with printing on its back side. 4. Check if the width of the side guides of the drawer is too narrow. 5. Check the motor-related adjustment value. NO Is the intermediate transport sensor (S17) working? (Perform the input check in the test mode: 03-[FAX]OFF/[1]/[A]) ↓ → NO → 1. Are paper dusts accumulated on the intermediate transport sensor? 2. Check if the harness is not damaged. 3. Check if the connector is disconnected. YES Is the transport motor (M17) rotating? (Perform the output check in the test mode: 03-133,183) ↓ → NO → Check if the bearing of the transportation roller is locked. Replace the transport motor. 1. Check if the connector of the transport motor is disconnected. 2. Check if the connector CN327 on the LGC board is disconnected. 3. Check if the connector on the transport motor driving PC board is disconnected. 4. Check if the connector pins are disconnected and the harnesses are open circuited. 5. Check if the conductor pattern on the LGC board is short circuited or open circuited. 6. Replace the LGC board. 7. Replace the transport motor driving PC board. YES Check if the spring of the follower roller of the intermediate transport roller is working properly. Check if the registration roller (rubber) is rotating smoothly. |
Error code: | E301 |
Description: | 3rd drawer transport jam (paper not reaching intermediate transport sensor): Paper which has passed the 1st drawer transport sensor does not reach the intermediate transport sensor during the feeding at the 3rd drawer. |
Causes: | • Fusing Unit • DC Power Supply (PU1) • Mechanical Control Board (PWB-M) |
Remedy: | (First page of printing) Is the intermediate transport sensor working? (Perform the input check in the test mode: 03-[FAX]OFF/[1]/[A]) ↓ → NO → Open the jam access cover. Remove the paper and check the followings. 1. Check if the connector of the intermediate transport sensor is disconnected. 2. Check if the connector CN327 on the LGC board is disconnected. 3. Check if the connector pins are disconnected and the harnesses are open circuited. 4. Check if the conductor pattern on the LGC board is short circuited or open circuited. 5. Replace the LGC board. YES Is the transport motor rotating? (Perform the output check in the test mode: 03-133,183) ↓ → NO → Check if the bearing of the transportation roller is locked. Replace the transport motor. 1. Check if the connector of the transport motor is disconnected. 2. Check if the connector CN327 on the LGC board is disconnected. 3. Check if the connector on the transport motor driving PC board is disconnected. 4. Check if the connector pins are disconnected and the harnesses are open circuited. 5. Check if the conductor pattern on the LGC board is short circuited or open circuited. 6. Check if the conductor pattern on the transport motor driving PC board is short circuited or open circuited. 7. Replace the LGC board. 8. Replace the transport motor driving PC board. YES Is the 1st drawer transport clutch working? (Perform the output check in the test mode: 03-210/225/229/230/231) ↓ → NO → 1. Check if the connector of the 1st drawer transport clutch is disconnected. 2. Check if the connector CN305 on the LGC board is disconnected. 3. Check if the connector pins are disconnected and the harnesses are open circuited. 4. Check if the conductor pattern on the LGC board is short circuited or open circuited. 5. Replace the 1st drawer transport clutch. 6. Replace the LGC board. Check if the spring of the follower roller of the intermediate transport roller is working properly. (Second page or later of printing) Leading edge of paper not reaching the fuser exit sensor. ↓ → YES → If the paper is damaged, remove the paper and check the followings. 1. Check if the paper is skewed, and correct it if it is skewed. 2. Check the paper amount. 3. Check if the paper is not the one with printing on its back side. 4. Check if the width of the side guides of the drawer is too narrow. 5. Check the motor-related adjustment value. NO Is the intermediate transport sensor working? (Perform the input check in the test mode: 03-[FAX]OFF/[1]/[A]) ll → NO → 1. Are paper dusts accumulated on the intermediate transport sensor? 2. Check if the harness is not damaged. 3. Check if the connector is disconnected. YES Is the transport motor rotating? (Perform the output check in the test mode: 03-133,183) ↓ → NO → Check if the bearing of the transportation roller is locked. Replace the transport motor. 1. Check if the connector of the transport motor is disconnected. 2. Check if the connector CN327 on the LGC board is disconnected. 3. Check if the connector on the transport motor driving PC board is disconnected. 4. Check if the connector pins are disconnected and the harnesses are open circuited. 5. Check if the conductor pattern on the LGC board is short circuited or open circuited. 6. Check if the conductor pattern on the transport motor driving PC board is short circuited or open circuited. 7. Replace the LGC board. 8. Replace the transport motor driving PC board. YES Check if the spring of the follower roller of the intermediate transport roller is working properly. |
Error code: | E302 |
Description: | Charge roller problem or HVT problem |
Causes: | • Fusing Unit • DC Power Supply (PU1) • Mechanical Control Board (PWB-M) |
Remedy: | 1 Check the Fusing Unit for correct installation (whether it is secured in position). - - 2 Check the Fusing Unit, PWB-M and PU1 for proper connection and correct or change as necessary. - - 3 Change Fusing Unit - - 4 Change PWB-M - - 5 Change PU1 |
Error code: | E303 |
Description: | Toner sensor |
Causes: | • Fusing Unit • DC Power Supply (PU1) • Mechanical Control Board (PWB-M) |
Remedy: | 1 Check the Fusing Unit for correct installation (whether it is secured in position). - - 2 Check the Fusing Unit, PWB-M and PU1 for proper connection and correct or change as necessary. - - 3 Change Fusing Unit - - 4 Change PWB-M - - 5 Change PU1 |
Error code: | E304 |
Description: | Heating Roller warm-up failure - The Heating Roller Thermistor/1 (TH1) and the Heating Roller Thermistor/2 (TH3) fails to raise a given degree of temperature even after the lapse of a given period of time after the Heating Roller Heater lamp/1 (H1) is turned ON. - The detected temperature of the Heating Roller Thermistor/1 (TH1) is lower for a given level of degree than one of the Fusing Pressure Roller Thermistor/1 (TH2) after the Front Cover is opened or closed, the Main Power Switch is turned ON, or TROUBLE RESET is implemented. - The counter value of zero cross signal input is not updated for a given period of time. |
Causes: | • Fusing Unit • DC Power Supply (PU1) • Mechanical Control Board (PWB-M) |
Remedy: | 1 Check the Fusing Unit for correct installation (whether it is secured in position). - - 2 Check the Fusing Unit, PWB-M and PU1 for proper connection and correct or change as necessary. - - 3 Change Fusing Unit - - 4 Change PWB-M - - 5 Change PU1 |
Error code: | E305 |
Description: | Fusing Pressure Roller warm-up failure - The Fusing Pressure Roller Thermistor/1 (TH2) fails to raise a given degree of temperature even after the lapse of a given period of time after the Fusing Pressure Heater Lamp (H3) is turned ON. - The detected temperature of the Fusing Pressure Roller Thermistor/1 (TH2) is lower for a given level of degree than one of the Heating Roller Thermistor/1 (TH1) after the Front Cover is opened or closed, the Main Power Switch is turned ON, or TROUBLE RESET is implemented. |
Causes: | • Fusing Unit • DC Power Supply (PU1) • Mechanical Control Board (PWB-M) |
Remedy: | 1 Check the Fusing Unit for correct installation (whether it is secured in position). - - 2 Check the Fusing Unit, PWB-M and PU1 for proper connection and correct or change as necessary. - - 3 Change Fusing Unit - - 4 Change PWB-M - - 5 Change PU1 |
Error code: | E310 |
Description: | 3rd drawer transport jam (paper not reaching 1st drawer transport sensor): Paper which has passed the 2nd transport sensor does not reach the 1st drawer transport sensor during the feeding at the 3rd drawer. |
Causes: | 1st drawer transport sensor Transport motor-2 Transport motor-1 PFC board Rollers |
Remedy: | (First page of printing) Open the jam access cover. Is there paper in front of the 1st drawer transport sensor? → YES → Remove the paper. NO Is the 1st drawer transport sensor (S33) working? (Perform the input check in the test mode: 03-[FAX]OFF/[1]/[C]) ↓ → NO → 1. Check if the connector of the 1st drawer transport sensor is disconnected. 2. Check if the connector CN329 on the LGC board is disconnected. 3. Check if the connector pins are disconnected and the harnesses are open circuited. 4. Check if the conductor pattern on the LGC board is short circuited or open circuited. 5. Replace the 1st drawer transport sensor. 6. Replace the LGC board. YES Are the transport clutches (CLT5,7,9,11) working? (Perform the output check in the test mode: 03-210/225/229/230/231) ↓ → NO → 1. Check if the connectors of the transport clutches are disconnected. 2. Check if the connector CN328,329,350 on the LGC board is disconnected. 3. Check if the connector pins are disconnected and the harnesses are open circuited. 4. Check if the conductor pattern on the LGC board is short circuited or open circuited. 5. Replace the transport clutches. 6. Replace the LGC board. YES 1. Check the condition of the feed roller, separation roller and pickup roller of each paper source, and clean or replace them. 2. Check the transport roller. Clean or replace it. (Second page or later of printing) Open the jam access cover. Is there any paper on the transport path? ↓ → YES → If the paper is damaged, remove the paper and check the followings: 1. Check if the paper is skewed, and correct it if it is skewed. 2. Check the paper amount. 3. Check if the paper is not the one with printing on its back side. 4. Check if the width of the side guides of the drawer is too narrow. 5. Check the motor-related adjustment value. NO Check if the spring of the follower roller of the intermediate transport roller is working properly. |
Error code: | E400 |
Display: | Print Unable E4 Turn the power off and then back on again. |
Description: | Duplexing unit open jam |
Causes: | Fuse LGC board Switching regulator Interlock switch |
Remedy: | 1. Close the duplexing unit if it is opened. Remove if there is any paper before closing it. 2. Is the voltage of 24V being supplied from the power supply unit? (Perform the input check: 03- [COPY] ON/[6]/[A]) 3. Check if the connector CN309 on the LGC board is disconnected from the connector CN403 on the switching regulator or the harnesses are open circuited. Correct if any. 4. Check if the fuse (F201, F202, F203, and F204) on the switching regulator has blown. 5. Replace the PFC board. 6. Replace the switching regulator. 7. Is the interlock switch working properly? (Perform the input check: 03-[SCAN] ON/[4]/[G]) 8. Check if the connector CN312 on the LGC board is disconnected from the interlock switch or the harnesses are open circuited. Correct if any. |
Error code: | E401 |
Description: | Low temperature. Lamp, thermofuse, thermistor etc. |
Causes: | • Photoconductor Unit/C • Photoconductor Unit/M • Photoconductor Unit/Y • Mechanical Control Board (PWB-M) • Controller Board (PWB-P) |
Remedy: | 1 Clean the TCR Sensor window on the underside of the Photoconductor Unit if dirty. - - 2 Reinstall Photoconductor Unit. - - 3 Change Photoconductor Unit. - - 4 Change PWB-M - - 5 Change PWB-P |
Error code: | E402 |
Description: | Abnormally low toner density detected Magenta TCR Sensor - Mixture ratio of the toner and carrier in the developing machine is lower than the specified value. |
Causes: | • Photoconductor Unit/C • Photoconductor Unit/M • Photoconductor Unit/Y • Toner Supply Motor Y/M (M6) • Toner Supply Motor C/K (M7) • Mechanical Control Board (PWB-M) • Controller Board (PWB-P) |
Remedy: | 1 Perform image troubleshooting procedure if image density is low. - - 2 Clean the TCR Sensor window on the underside of the Photoconductor Unit if dirty. - - 3 M6, M7 operation check PWB-M CNDM2-10 to 13(M6) PWB-M CNDM3-10 to 13(M7) C-22 C-23 4 Reinstall Photoconductor Unit. - - 5 Change Photoconductor Unit. - - 6 Change PWB-M - - 7 Change PWB-P |
Error code: | E403 |
Description: | Abnormally high toner density detected Magenta TCR Sensor - Mixture ratio of the toner and carrier in the developing machine is higher than the specified value. |
Causes: | • Photoconductor Unit/C • Photoconductor Unit/M • Photoconductor Unit/Y • Mechanical Control Board (PWB-M) • Controller Board (PWB-P) |
Remedy: | 1 Clean the TCR Sensor window on the underside of the Photoconductor Unit if dirty. - - 2 Reinstall Photoconductor Unit. - - 3 Change Photoconductor Unit. - - 4 Change PWB-M - - 5 Change PWB-P |
Error code: | E404 |
Description: | Abnormally low toner density detected Yellow TCR Sensor - Mixture ratio of the toner and carrier in the developing machine is lower than the specified value. |
Causes: | • Photoconductor Unit/C • Photoconductor Unit/M • Photoconductor Unit/Y • Toner Supply Motor Y/M (M6) • Toner Supply Motor C/K (M7) • Mechanical Control Board (PWB-M) • Controller Board (PWB-P) |
Remedy: | 1 Perform image troubleshooting procedure if image density is low. - - 2 Clean the TCR Sensor window on the underside of the Photoconductor Unit if dirty. - - 3 M6, M7 operation check PWB-M CNDM2-10 to 13(M6) PWB-M CNDM3-10 to 13(M7) C-22 C-23 4 Reinstall Photoconductor Unit. - - 5 Change Photoconductor Unit. - - 6 Change PWB-M - - 7 Change PWB-P |
Error code: | E405 |
Description: | Transfer belt or charge roller drive |
Causes: | • Photoconductor Unit/C • Photoconductor Unit/M • Photoconductor Unit/Y • Mechanical Control Board (PWB-M) • Controller Board (PWB-P) |
Remedy: | 1 Clean the TCR Sensor window on the underside of the Photoconductor Unit if dirty. - - 2 Reinstall Photoconductor Unit. - - 3 Change Photoconductor Unit. - - 4 Change PWB-M - - 5 Change PWB-P |
Error code: | E406 |
Description: | Abnormally low toner density detected Black TCR Sensor - Mixture ratio of the toner and carrier in the developing machine is lower than the specified value. |
Causes: | • Photoconductor Unit /K • Toner Supply Motor C/K (M7) • Mechanical Control Board (PWB-M) • Controller Board (PWB-P) |
Remedy: | 1 Perform image troubleshooting procedure if image density is low. - - 2 Clean the TCR Sensor window on the underside of the Photoconductor Unit if dirty. - - 3 M7 operation check PWB-M CNDM3-10 to 13 C-23 4 Reinstall Photoconductor Unit - - 5 Change Photoconductor Unit /K - - 6 Change PWB-M - - 7 Change PWB-P |
Error code: | E407 |
Description: | Abnormally high toner density detected Black TCR Sensor - Mixture ratio of the toner and carrier in the developing machine is higher than the specified value. |
Causes: | • Photoconductor Unit /K • Mechanical Control Board (PWB-M) • Controller Board (PWB-P) |
Remedy: | 1 Clean the TCR Sensor window on the underside of the Photoconductor Unit if dirty. - - 2 Reinstall Photoconductor Unit - - 3 Change Photoconductor Unit /K - - 4 Change PWB-M - - 5 Change PWB-P |
Error code: | E500 |
Display: | Print Unable E5 Turn the power off and then back on again. |
Description: | MAIN MOTOR failure MOTOR ASSY is not turning, or not turning normally. |
Causes: | • Main Motor (M1) • Mechanical Control Board (PWB-M) • DC Power Supply (PU1) |
Remedy: | 1. Connectors on LVPS and MCU Board Assy are correctly connected? 2. Check the connections between MAIN MOTOR <=> LVPS <=> MCU Board Assy. Disconnection/slant connection of a connector Disconnection/damage of a harness. 3. MAIN MOTOR is not turning normally due to an abnormal load on it. Check GEAR ASSY HOUSING`s Drive Transmission Path. 4. Replace MAIN MOTOR. 5. Replace LVPS. 6. Replace MCU Board Assy. |
Error code: | E501 |
Description: | Upper lift motor |
Causes: | • Main Motor (M1) • Mechanical Control Board (PWB-M) • DC Power Supply (PU1) |
Remedy: | 1 M1 operation check PWB-M CNDM1-5 (REM) PWB-M CNDM1-8 (LOCK) K to L-2 2 Change PWB-M - - 3 Change PU1 |
Error code: | E510 |
Description: | Transport jam during duplex printing (paper not reaching reverse sensor-2): Paper which has passed the reverse sensor-1 does not reach the reverse sensor-2 during duplex printing. |
Causes: | Duplexing unit path entrance sensor Reverse motor ADU motor-2 PFC board ADU board DRV board Rollers |
Remedy: | Open the exit cover. Is there any paper in front of the reverse sensor-2? → YES → Remove the paper. NO Is the reverse sensor-1 working? (Perform the input check in the test mode: 03-[FAX]OFF/[1]/[G]) ↓ → NO → 1. Check if the connector of the reverse sensor-1 is disconnected. 2. Check if the connector CN335 on the LGC board is disconnected. 3. Check if the connector pins are disconnected and the harnesses are open circuited. 4. Check if the conductor patterns on LGC board are short circuited or open circuited. 5. Replace the reverse sensor-1. 6. Replace the LGC board. YES Is the horizontal transport section driving clutch working? (Perform the output check in the test mode: 03-222) ↓ → NO → 1. Check if the connector of the horizontal transport section driving clutch is disconnected. 2. Check if the connector CN334 on the LGC board is disconnected. 3. Check if the connector pins are disconnected and the harnesses are open circuited. 4. Check if the conductor pattern on the LGC board is short circuited or open circuited. 5. Replace the horizontal transport section driving clutch. 6. Replace the LGC board. YES Is the Mylar at the reverse section normal? → NO → Replace the Mylar. YES Check the condition of the roller at the horizontal transport section and clean or replace it. |
Error code: | E511 |
Description: | Transport jam during duplex printing (paper not reaching horizontal transport sensor-1): Paper which has passed the reverse sensor-2 does not reach the horizontal transport sensor-1 during duplex printing. |
Causes: | Duplexing unit path entrance sensor Reverse motor ADU motor-1 PFC board ADU board Rollers |
Remedy: | Is there any paper at the reverse section when the exit cover is opened? → YES → Remove the paper. NO Is the Horizontal transport sensor-1 working? (Perform the input check in the test mode: 03-[FAX]OFF/[9]/[F]) ↓ → NO → 1. Check if the connector of the Horizontal transport sensor-1 is not disconnected. 2. Check if the connector CN334 on the LGC board is not disconnected. 3. Check if the connector pins are not disconnected and the harness is not open circuited. 4. Check if the conductor pattern on the LGC board is not short circuited or open circuited. 5. Replace the Horizontal transport sensor-1. 6. Replace the LGC board. YES Is the transport roller 1/2 at the horizontal transport section rotating? (Perform the output check in the test mode: 03-110/220) ↓ → NO → 1. Check if the connectors of the and horizontal transport section driving clutch-1 and horizontal transport section driving clutch-2 are not disconnected. 2. Check if the connectors of the and horizontal transport section driving clutch-1 and and horizontal transport section driving clutch-2 are not misconnected (drive clutch: black-black, transport clutch 1: bluepurple). 3. Check if the connector CN334 on the LGC board is not disconnected. 4. Check if the connector pins are not disconnected and the harness is not open circuited. 5. Check if the conductor pattern on the LGC board is not short- or open circuited. 6. Replace the transport drive clutch and transport clutch 1. 7. Replace the LGC board. 8. Check if the front side timing belt is put on properly. 9. Check the installation state of the horizontal transport section driving clutch-1. YES Check the condition of the rollers at the horizontal transport section and clean or replace them. |
Error code: | E520 |
Description: | Stop jam in the ADU: The paper does not reach the ADU exit sensor after it has passed the ADU entrance sensor. |
Causes: | ADU exit sensor LGC board ADU exit sensor MOT board MOT2 board Rollers in the ADU |
Remedy: | 1 Open the ADU. Is there any paper in front of the ADU exit sensor? Yes Remove the paper. No 2 2 Is the ADU exit sensor working? (Perform the input check in the test mode: 03- [FAX]OFF/[1]/[E]) Yes 3 No • Check if the connector of the ADU exit sensor is disconnected. • Check if the connector CN311 on the LGC board is disconnected. • Check if the connector pins are disconnected and the harnesses are open circuited. • Check if the conductor patterns on the LGC board are short circuited or open circuited. • Replace the ADU exit sensor. • Replace the LGC board. 3 Is the ADU motor working? (Perform the output check in the test mode: 03-119) Yes 4 No • Check if the connector of the ADU motor is disconnected. • Check if the connector CN402 and CN404 on the MOT/MOT2 board is disconnected. • Check if the connector CN303 on the LGC board is disconnected. • Check if the connector pins are disconnected and the harnesses are open circuited. • Check if the conductor pattern on the LGC board is short circuited or open circuited. • Replace the ADU exit sensor. • Replace the MOT/MOT2 board. • Replace the LGC board. 4 ADU • Check the rollers in the ADU. Replace them if they are worn out. |
Error code: | E521 |
Description: | BTR 2 Error - The input of 2nd BTR Retract Sensor does not change when 2nd BTR is initialized. |
Causes: | • HARNESS ASSY MAIN • MOT ASSY MICRO • SENSOR 2BTR RETRACT • HARNESS ASSY ADC • PWBA MCU • LV/HVPS |
Remedy: | 1 Check of 2ND BTR ASSY attachment Is 2ND BTR ASSY attached correctly? Go to Step [2]. Re-attach, and go to step [2]. 2 Does the error recur when restarting the printer? Go to Step [3]. End of procedure 3 Continuity check of HARNESS ASSY MAIN Disconnect the P/J403 from PWBA MCU. Do all of the wiring below have normal continuity? J403-1 . J600-3 J403-2 . J600-2 J403-3 . J600-1 Go to Step [4]. Repair broken or shorted part. 4 24 VDC power supply check to MOT ASSY MICRO (2nd BTR Retract Motor) The voltage of P403-3 . P403-2 on PWBA MCU is 24 VDC? Go to Step [5]. Go to Step [10]. 5 Check after replacement of MOT ASSY MICRO Replace MOT ASSY MICRO. Does the error recur when restarting the printer? Go to Step [6]. End of procedure 6 5 VDC power supply check to SENSOR 2BTR RETRACT. The voltage of P418-4 . P418-5 on PWBA MCU is 5 VDC? Go to Step [7]. Go to Step [10]. 7 Continuity check of HARNESS ASSY ADC Disconnect the P/J418 from PWBA MCU. Do all of the wiring below have normal continuity? J418-4 . J112-3 J418-5 . J112-2 J418-6 . J112-1 Go to Step [8]. Replace HARNESS ASSY ADC. 8 Check after replacement of SENSOR 2BTR RETRACT Replace SENSOR 2BTR RETRACT. Does the error recur when restarting the printer? Go to Step [9]. End of procedure 9 Check after replacement of PWBA MCU Replace PWBA MCU. Does the error recur when restarting the printer? Go to Step [11]. End of procedure 10 Power supply check to PWBA MCU Are each of the power voltages being supplied to the following terminals on PWBA MCU from LV/HVPS? P410-1 . P410-2: 3. 3VDC P410-3 . P410-4: 5VDC P410-5/6 .P410-7/8: 24VDC Replace PWBA MCU. Go to Step [11]. 11 Continuity check of HARNESS ASSY MAIN Are each of the power voltages being supplied to the following terminals on PWBA MCU from LV/HVPS? J410-1 . J502-1 J410-2 . J502-2 J410-3 . J502-3 J410-4 . J502-4 J410-5 . J502-5 J410-6 . J502-6 J410-7 . J502-7 J410-8 . J502-8 Replace LV/ HVPS. Repair broken or shorted part. |
Error code: | E550 |
Description: | Paper remaining jam at paper transport path: Paper is remaining on the paper transport path when the printing has finished. (Jam caused by a multiple paper feeding) |
Causes: | Feed or transport roller possibly causing multiple feeding Sensor in the jamming area Refer to the table below PFC board |
Remedy: | Open the cover of the unit/area whose picture is blinking on the control panel. Is there any paper on the transport path? → YES → Remove the paper. NO Is the sensor in the jamming area working? (Perform the input check in the test mode: refer to the following table) ↓ → NO→ 1. Check if the connector of the sensor is disconnected. 2. Check if any of the connectors on the LGC board is disconnected. 3. Check if the connector pins are disconnected and the harnesses are open circuited. 4. Check if the conductor pattern on the LGC board is short circuited or open circuited. 5. Replace the sensor. 6. Replace the LGC board. YES 1. Check if any multiple paper is fed from the drawer. 2. Replace the LGC board. Registration area Registration sensor 03-[FAX]ON/[4]/[E] Exit/Reverse area Exit sensor 03-[FAX]OFF/[7]/[B] Reverse sensor-1 03-[FAX]OFF/[7]/[E] Reverse sensor-2 03-[FAX]OFF/[7]/[D] Fuser transport sensor 03-[FAX]OFF/[7]/[C] Reverse transport area Horizontal transport sensor-1 03-[FAX]OFF/[9]/[F] Horizontal transport sensor-2 03-[FAX]OFF/[9]/[G] Horizontal transport sensor-3 03-[FAX]OFF/[9]/[H] Paper feeding area 1st drawer feed sensor 03-[FAX]OFF/[1]/[D] 2nd drawer feed sensor 03-[FAX]OFF/[2]/[D] 3rd drawer / tandem LCF feed sensor 03-[FAX]OFF/[3]/[D] 4th drawer feed sensor 03-[FAX]OFF/[4]/[D] 1st drawer transport sensor 03-[FAX]OFF/[1]/[C] 2nd drawer transport sensor 03-[FAX]OFF/[2]/[C] 3rd drawer / tandem LCF transport sensor 03-[FAX]OFF/[3]/[C] 4th drawer transport sensor 03-[FAX]OFF/[4]/[C] Intermediate transport sensor 03-[FAX]OFF/[1]/[A] |
Error code: | E551 |
Description: | Paper remaining jam on the transport path (when a service call occurs) |
Causes: | Feed or transport roller possibly causing multiple feeding Sensor in the jamming area Refer to the table below. LGC board |
Remedy: | 1 Jamming transport path Open the cover of the unit/area whose picture is flashing on the control panel and remove any paper on the transport path. 2 Sensor in the jamming area • Sensor check (Refer to the table below) • Harness check • Connector check 3 LGC board • Harness check • Connector check • Board check Notes: If the jam is occurring in the ADU, LCF or PFP, check the board in each unit. Registration area Jam access cover Registration sensor 03-[ALL]OFF/[9]/[A] Paper clinging detection sensor 03-[ALL]OFF/[9]/[E] Registration pass sensor 03-[ALL]OFF/[9]/[F] Feed sensor 03-[ALL]OFF/[9]/[B] Exit area Fuser cover Exit sensor 03-[ALL]OFF/[9]/[C] ADU ADU ADU entrance sensor 03-[ALL]OFF/[9]/[G] ADU exit sensor 03-[ALL]OFF/[9]/[H] Bypass feed unit Side cover 2nd drawer feed sensor 03-[FAX]ON/[4]/[D] LCF LCF side cover LCF feed sensor 03-[COPY]ON/[9]/[F] PFP PFP side cover PFP upper drawer feed sensor 03-[FAX]ON/[0]/[C] PFP lower drawer feed sensor 03-[FAX]ON/[0]/[D] Bridge unit Bridge unit Bridge unit transport sensor-1 (Entrance sensor) 03-[ALL]OFF/[0]/[A] Bridge unit transport sensor-2 (Exit sensor) 03-[ALL]OFF/[0]/[B] Finisher Finisher door Sensors in the finisher |
Error code: | E552 |
Description: | Paper remaining jam on the transport path (when the cover is closed) |
Causes: | Feed or transport roller possibly causing multiple feeding Sensor in the jamming area Refer to the table below. LGC board |
Remedy: | 1 Jamming transport path Open the cover of the unit/area whose picture is flashing on the control panel and remove any paper on the transport path. 2 Sensor in the jamming area • Sensor check (Refer to the table below) • Harness check • Connector check 3 LGC board • Harness check • Connector check • Board check Notes: If the jam is occurring in the ADU, LCF or PFP, check the board in each unit. Registration area Jam access cover Registration sensor 03-[ALL]OFF/[9]/[A] Paper clinging detection sensor 03-[ALL]OFF/[9]/[E] Registration pass sensor 03-[ALL]OFF/[9]/[F] Feed sensor 03-[ALL]OFF/[9]/[B] Exit area Fuser cover Exit sensor 03-[ALL]OFF/[9]/[C] ADU ADU ADU entrance sensor 03-[ALL]OFF/[9]/[G] ADU exit sensor 03-[ALL]OFF/[9]/[H] Bypass feed unit Side cover 2nd drawer feed sensor 03-[FAX]ON/[4]/[D] LCF LCF side cover LCF feed sensor 03-[COPY]ON/[9]/[F] PFP PFP side cover PFP upper drawer feed sensor 03-[FAX]ON/[0]/[C] PFP lower drawer feed sensor 03-[FAX]ON/[0]/[D] Bridge unit Bridge unit Bridge unit transport sensor-1 (Entrance sensor) 03-[ALL]OFF/[0]/[A] Bridge unit transport sensor-2 (Exit sensor) 03-[ALL]OFF/[0]/[B] Finisher Finisher door Sensors in the finisher |
Error code: | E553 |
Description: | Fusing Cooling Fan Motor/2`s failure to turn - The Fan Lock signal remains HIGH for a predetermined continuous period of time while the Motor remains stationary |
Causes: | • Mechanical Control Board (PWB-M) • Right Door |
Remedy: | 1 Check the connector of motor for proper connection and correct as necessary. - - 2 Check the fan for possible overload and correct as necessary. - - 3 M13 operation check PWB-M CNDM1-14 (ON) PWB-M CNDM1-17 (LOCK) K to L-1 4 Change PWB-M |
Error code: | E554 |
Description: | Ozone Ventilation Fan Motor`s failure to turn - The Fan Lock signal remains HIGH for a predetermined continuous period of time while the Motor remains stationary |
Causes: | • Ozone Ventilation Fan Motor (M14) • Mechanical Control Board (PWB-M) |
Remedy: | 1 Check the connector of motor for proper connection and correct as necessary. - - 2 Check the fan for possible overload and correct as necessary. - - 3 M14 operation check PWB-M CNDM1-14 (ON) PWB-M CNDM1-17 (LOCK) K to L-1 4 Change PWB-M |
Error code: | E555 |
Description: | Power Supply Cooling Fan Motor/1`s failure to turn - The Fan Lock signal remains HIGH for a predetermined continuous period of time while the Motor remains stationary. |
Causes: | • Power Supply Cooling Fan Motor/1 (M8) • Mechanical Control Board (PWB-M) |
Remedy: | 1 Check the connector of motor for proper connection and correct as necessary. - - 2 Check the fan for possible overload and correct as necessary. - - 3 M8 operation check PWB-M CNLV3-2 (ON) PWB-M CNLV3-3 (LOCK) C-27 4 Change PWB-M |
Error code: | E556 |
Description: | Cooling Fan Motor 2`s failure to turn - The Fan Lock signal remains HIGH for a predetermined continuous period of time while the Motor remains stationary. |
Causes: | • Cooling Fan Motor/2 (M22) • Mechanical Control Board (PWB-M) |
Remedy: | 1 Check the connector of motor for proper connection and correct as necessary. - - 2 Check the fan for possible overload and correct as necessary. - - 3 M22 operation check - - 4 Change PWB-M |
Error code: | E600 |
Display: | Print Unable E6 Turn the power off and then back on again. |
Description: | Cyan TCR Sensor adjustment failure - TCR Sensor automatic adjustment does not function properly, failing to adjust to an appropriate value. |
Causes: | • Photoconductor Unit /C • Photoconductor Unit /M • Photoconductor Unit /Y • Toner Supply Motor Y/M (M6) • Toner Supply Motor C/K (M7) • Mechanical Control Board (PWB-M) • Controller Board (PWB-P) |
Remedy: | 1 Clean the TCR Sensor window on the underside of the Photoconductor Unit if dirty - - 2 M6, M7 operation check PWB-M CNDM2-10 to 13 (M6) PWB-M CNDM3-10 to 13 (M7) C-22 C-23 3 Reinstall Photoconductor Unit - - 4 Change Photoconductor Unit - - 5 Change PWB-M - - 6 Change PWB-P |
Error code: | E601 |
Description: | Magenta TCR Sensor adjustment failure - TCR Sensor automatic adjustment does not function properly, failing to adjust to an appropriate value. |
Causes: | • Photoconductor Unit /C • Photoconductor Unit /M • Photoconductor Unit /Y • Toner Supply Motor Y/M (M6) • Toner Supply Motor C/K (M7) • Mechanical Control Board (PWB-M) • Controller Board (PWB-P) |
Remedy: | 1 Clean the TCR Sensor window on the underside of the Photoconductor Unit if dirty - - 2 M6, M7 operation check PWB-M CNDM2-10 to 13 (M6) PWB-M CNDM3-10 to 13 (M7) C-22 C-23 3 Reinstall Photoconductor Unit - - 4 Change Photoconductor Unit - - 5 Change PWB-M - - 6 Change PWB-P |
Error code: | E602 |
Description: | Yellow TCR Sensor adjustment failure - TCR Sensor automatic adjustment does not function properly, failing to adjust to an appropriate value. |
Causes: | • Photoconductor Unit /C • Photoconductor Unit /M • Photoconductor Unit /Y • Toner Supply Motor Y/M (M6) • Toner Supply Motor C/K (M7) • Mechanical Control Board (PWB-M) • Controller Board (PWB-P) |
Remedy: | 1 Clean the TCR Sensor window on the underside of the Photoconductor Unit if dirty - - 2 M6, M7 operation check PWB-M CNDM2-10 to 13 (M6) PWB-M CNDM3-10 to 13 (M7) C-22 C-23 3 Reinstall Photoconductor Unit - - 4 Change Photoconductor Unit - - 5 Change PWB-M - - 6 Change PWB-P |
Error code: | E603 |
Description: | Black TCR Sensor adjustment failure - TCR Sensor automatic adjustment does not function properly, failing to adjust to an appropriate value. |
Causes: | • Photoconductor Unit /K • Toner Supply Motor C/K (M7) • Mechanical Control Board (PWB-M) • Controller Board (PWB-P) |
Remedy: | 1 Clean or correct each contact of the Photoconductor Unit if faulty. - - 2 M7 operation check PWB-M CNDM3-10 to 13 C-23 3 Reinstall Photoconductor Unit /K - - 4 Change Photoconductor Unit /K - - 5 Change PWB-M - - 6 Change PWB-P |
Error code: | E610 |
Description: | 1st Image Transfer ATVC (color) failure - An abnormal average value is detected while performing the first image transfer ATVC of color. |
Causes: | • Transfer Belt Unit • Transfer Roller • High Voltage Unit |
Remedy: | 1 Check if the Transfer Roller and Transfer Belt are dirty and correct as necessary. - - 2 Change High Voltage Unit - - 3 Change Transfer Belt Unit |
Error code: | E611 |
Description: | 1st Image Transfer ATVC (K) failure - An abnormal average value is detected while performing the first image transfer ATVC of black. |
Causes: | • Transfer Belt Unit • High Voltage Unit |
Remedy: | 1 Check if the Transfer Roller and Transfer Belt are dirty and correct as necessary. - - 2 Change High Voltage Unit - - 3 Change Transfer Belt Unit |
Error code: | E612 |
Description: | 2nd Image Transfer ATVC failure - An abnormal average value is detected while performing the second image transfer ATVC. |
Causes: | • Transfer Belt Unit • 2nd Transfer Roller • High Voltage Unit |
Remedy: | 1 Check if the Transfer Roller and Transfer Belt are dirty and correct as necessary. - - 2 Check that the 2nd Transfer Roller is properly installed and correct as necessary. - - 3 Change 2nd Transfer Roller. - - 4 Change High Voltage Unit. |
Error code: | E620 |
Description: | Communication problem between main board and ARDF |
Causes: | • Transport Drive Assy • Mechanical Control Board (PWB-M) • Harness |
Remedy: | 1 Check if the Detect Light Shield Plate has damages and is properly installed, and correct as necessary. - - 2 Check the Transport Drive Assy connector for proper connection and correct as necessary. - - 3 Check the PWB-M connector for proper connection and correct as necessary. - - 4 Change the cable that connects Transport Drive Assy and PWB-M. - - 5 Change Transport Drive Assy - - 6 Change PWB-M |
Error code: | E621 |
Description: | Communication problem between main board and sorter |
Causes: | • Transport Drive Assy • Mechanical Control Board (PWB-M) • Harness |
Remedy: | 1 Check if the Detect Light Shield Plate has damages and is properly installed, and correct as necessary. - - 2 Check the Transport Drive Assy connector for proper connection and correct as necessary. - - 3 Check the PWB-M connector for proper connection and correct as necessary. - - 4 Change the cable that connects Transport Drive Assy and PWB-M. - - 5 Change Transport Drive Assy - - 6 Change PWB-M |
Error code: | E630 |
Description: | IDC Sensor (front) failure - All outputs of Sensor photo-receiver section from the detection point (unprinted surface on the Image Transfer Belt) are 0.5 V or less, or 4.3 V or more at output checking during IDC Sensor adjustment. - All outputs of Sensor photo-receiver section from the detection point (unprinted surface on the Image Transfer Belt) are 1.9 V or less, or 4.4 V or more at density setting during IDC Sensor adjustment. - The output of Sensor photo-receiver section from the detection point (toner pattern on the Image Transfer Belt) is 1.0 V or less after the adjustment. |
Causes: | IDC Sensor |
Remedy: | 1 Check that the IDC Sensor is properly installed and correct as necessary. - - 2 Check if the IDC sensor is dirty and correct as necessary. - - 3 Check the IDC Sensor connector for proper connection and correct as necessary. - - 4 Check the PWB-M connector for proper connection and correct as necessary. - - 5 Change the cable that connects IDC Sensor and PWB-M. - - 6 Change the IDC Sensor. |
Error code: | E631 |
Description: | IDC Sensor (back) failure - All outputs of Sensor photo-receiver section from the detection point (unprinted surface on the Image Transfer Belt) are 0.5 V or less, or 4.3 V or more at output checking during IDC Sensor adjustment. - All outputs of Sensor photo-receiver section from the detection point (unprinted surface on the Image Transfer Belt) are 1.9 V or less, or 4.4 V or more at density setting during IDC Sensor adjustment. - The output of Sensor photo-receiver section from the detection point (toner pattern on the Image Transfer Belt) is 1.0 V or less after the adjustment. |
Causes: | IDC Sensor |
Remedy: | 1 Check that the IDC Sensor is properly installed and correct as necessary. - - 2 Check if the IDC sensor is dirty and correct as necessary. - - 3 Check the IDC Sensor connector for proper connection and correct as necessary. - - 4 Check the PWB-M connector for proper connection and correct as necessary. - - 5 Change the cable that connects IDC Sensor and PWB-M. - - 6 Change the IDC Sensor. |
Error code: | E640 |
Description: | Color Shift Test Pattern failure - The number of points detected in the main scan direction is more or less than the specified value during main scan direction registration correction. - The number of points detected in the sub scan direction is more or less than the specified value during sub scan direction registration correction. |
Causes: | • Transfer Belt Unit • IDC Sensor • Photoconductor Unit • PH Unit |
Remedy: | 1 Check if Transfer Belt has damages and correct as necessary. - - 2 Check that the IDC Sensor is properly installed and correct as necessary. - - 3 Check if the IDC sensor is dirty and correct as necessary. - - 4 Check the IDC Sensor connector for proper connection and correct as necessary. - - 5 Check the PWB-M connector for proper connection and correct as necessary. - - 6 Change the cable that connects IDC Sensor and PWB-M. 7 Change IDC Sensor. 8 Change Photoconductor Unit. 9 Change PH Unit. |
Error code: | E641 |
Description: | Color Shift Adjust failure - The color shift amount is greater than the specified range during main scan direction registration correction. - The color shift amount is greater than the specified range during sub scan direction registration correction. - The skew correction amount is greater than the specified value. |
Causes: | • PH Unit (displacement) • Transfer Belt Unit |
Remedy: | 1 Execute the correction of skew. - - 2 Check if Transfer Belt has damages and correct as necessary. |
Error code: | E701 |
Display: | Print Unable E7 Turn the power off and then back on again. |
Description: | MP tray Rise Descent Error - The Bypass Lift-Up Sensor is not blocked even when the Vertical Transport Motor has turned for a given number of pulses after the sequence to move the Paper Lifting Plate from the standby position to the feed position was started. - The Bypass Lift-Up Sensor is not unblocked even when the Vertical Transport Motor has turned for a given number of pulses after the sequence to move the Paper Lifting Plate from the feed position to the standby position was started. |
Causes: | • MP tray Lift-up Sensor (PC14) • Vertical Transport Motor (M2-PC) • Control Board (PWB-Z-PC) |
Remedy: | 1 Check the M2-PC connector for proper connection and correct as necessary. - - 2 Check the connector of M2-PC for proper drive coupling and correct as necessary. - - 3 PC14 I/O check, Sensor check PWB-M CNTRY1-10 (ON) C-10 4 M2-PC operation check PWB-Z PJ5Z PC-5~8 Q-22 5 Change PWB-Z-PC. |
Error code: | E702 |
Display: | Print Unable E7 Turn the power off and then back on again. |
Description: | Standard cassette Elevator failure - The Lift-Up Sensor is not blocked even after the lapse of a given period of time after the lifting motion has been started. |
Causes: | • Lift-up Sensor (PC7-PC) • Lift-up Sensor (PC7-PC) • Control Board (PWB-Z-PC) |
Remedy: | 1 Check the M3-PC connector for proper connection and correct as necessary. - - 2 Check the connector of M3-PC for proper drive coupling and correct as necessary. - - 3 PC7-PC I/O check, Sensor check PWB-Z PJ6Z PC-3 (ON) PWB-Z PJ4Z PC-4 to 5 V-21 to 22 4 M3-PC operation check Q-24 5 Change PWB-Z-PC. |
Error code: | E703 |
Description: | Optional Cassette1 Elevator failure - The Lift-Up Sensor is not blocked even after the lapse of a given period of time after the lifting motion has been started. |
Causes: | • Lift-up Sensor (PC7-PC) • Lift-up Sensor (PC7-PC) • Control Board (PWB-Z-PC) |
Remedy: | 1 Check the M3-PC connector for proper connection and correct as necessary. - - 2 Check the connector of M3-PC for proper drive coupling and correct as necessary. - - 3 PC7-PC I/O check, Sensor check PWB-Z PJ6Z PC-3 (ON) PWB-Z PJ4Z PC-4 to 5 V-21 to 22 4 M3-PC operation check Q-24 5 Change PWB-Z-PC. |
Error code: | E704 |
Description: | Optional Cassette2 Elevator failure - The Lift-Up Sensor is not blocked even after the lapse of a given period of time after the lifting motion has been started. |
Causes: | • Lift-up Sensor (PC7-PC) • Lift-up Sensor (PC7-PC) • Control Board (PWB-Z-PC) |
Remedy: | 1 Check the M3-PC connector for proper connection and correct as necessary. - - 2 Check the connector of M3-PC for proper drive coupling and correct as necessary. - - 3 PC7-PC I/O check, Sensor check PWB-Z PJ6Z PC-3 (ON) PWB-Z PJ4Z PC-4 to 5 V-21 to 22 4 M3-PC operation check Q-24 5 Change PWB-Z-PC. |
Error code: | E900 |
Display: | Print Unable E9 Turn the power off and then back on again. |
Description: | Copy counter |
Causes: | Mechanical Control Board (PWB-M) |
Remedy: | 1. Any other electric appliances; generators, radiotransmitter, etc., within three meters from the printer? In such a case, noises from them may cause an error in reading/writing; therefore, change the location of them or turn them off. 2. MCU Board Assy itself has abnormality. Replace MCU Board Assy. |
Error code: | E901 |
Description: | Copy counter |
Causes: | • RTC Board (PWB-R) • Mechanical Control Board (PWB-M) |
Remedy: | 1 Check the connector for proper connection and correct as necessary. - - 2 Change PWB-R - - 3 Change PWB-M |
Error code: | E998 |
Description: | Engine communication error Communication between Main Board Assy and MCU Board Assy has abnormality. |
Causes: | The firmware of the engine controller is faulty. The Main Board Assy. is faulty. |
Remedy: | 1. Any other electric appliances; generators, radiotransmitter, etc., within three meters from the printer? In such a case, noises from them may cause an error in reading/writing; therefore, change the location of them or turn them off. 2. Connection between Main Board Assy and MCU Board Assy correct? 3. Replace Main Board Assy. 4. Replace MCU Board Assy. |
Парткод
Название
EPSON 0474 Тонер-картридж желтый
EPSON 0475 Тонер-картридж пурпурный
EPSON 0476 Тонер-картридж голубой
EPSON 0477 Тонер-картридж черный
EPSON 0478 Коллектор отработанного тонера
EPSON 1175 Блок фотобарабана желтый
EPSON 1176 Блок фотобарабана пурпурный
EPSON 1177 Блок фотобарабана голубой
EPSON 1178 Блок фотобарабана черный