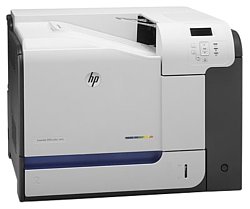
HP LaserJet Enterprise M551n
Рейтинг
Снят с производства
Тип устройства
Принтер
Технология печати
лазерная
Макс. формат
A4
Число страниц в месяц
75000
Скорость печати
A4
32
Цветность печати
цветная
Общие характеристики |
|
---|---|
Область применения |
средний офис |
Число страниц в месяц |
75 000 |
Тип |
лазерный/светодиодный |
Технология печати |
лазерная |
Размещение |
настольный |
Печать фотографий |
|
Тип устройства |
Принтер |
Макс. формат |
A4 |
Телефон |
|
Сканер |
|
Копир |
|
Факс |
|
Цветность печати |
цветная |
Принтер |
|
Количество цветов |
4 |
Печать без полей |
|
Система непрерывной подачи чернил |
|
Двусторонняя печать |
|
Пигментные чернила |
|
Прямая печать |
|
Макс, разрешение для ч/б печати |
|
По X | 1 200 |
По Y | 1 200 |
Скорость ч/б печати |
|
A4 | 32 |
Время выхода первого отпечатка |
|
Ч/б | 11 |
Сканер |
|
Отправка изображения по e-mail |
|
Слайд-адаптер |
|
Стандарт WIA |
|
Стандарт TWAIN |
|
Скорость сканирования |
|
Цветн, | 11 |
Расходные материалы |
|
Количество картриджей |
4 |
Ресурс цветного картриджа/тонера |
6 000 |
Ресурс ч/б картриджа/тонера |
5 500 |
Печать на: |
|
Карточках |
![]() |
Матовой бумаге |
![]() |
Конвертах |
![]() |
Глянцевой бумаге |
![]() |
Этикетках |
![]() |
Пленках |
![]() |
Рулоне |
|
CD/DVD |
|
Фотобумаге |
|
Плотность бумаги |
|
Минимальная | 60 |
Максимальная | 220 |
Факс |
|
PC Fax |
|
Цветной |
|
Телефон |
|
Стандарт DECT |
|
Проводная трубка |
|
Беспроводная трубка |
|
АОН |
|
Caller ID |
|
Автоответчик |
|
Спикерфон |
|
Шрифты и языки управления |
|
Языки управления |
|
PostScript |
![]() |
PostScript 3 |
![]() |
PCL 5c |
![]() |
PCL 6 |
![]() |
![]() |
|
PCL 5e |
|
PPDS |
|
PostScript 2 |
|
Количество установленных шрифтов |
|
PostScript | 92 |
PCL | 105 |
Лотки |
|
Емкость лотка ручной подачи |
100 |
Подача бумаги |
|
Стандартная | 600 |
Максимальная | 1 100 |
Вывод бумаги |
|
Стандартный | 250 |
Финишер |
|
Степлер |
|
Электронная сортировка |
|
Брошюровщик |
|
Сортер |
|
Сортировка со сдвигом |
|
Интерфейсы |
|
Версия USB |
2,0 |
Инфракрасный порт |
|
Устройство для чтения карт памяти |
|
RS-232 |
|
AirPrint |
|
LPT |
|
Bluetooth |
|
Wi-Fi 802.11n |
|
Wi-Fi |
|
FireWire (IEEE 1394) |
|
USB |
![]() |
Веб-интерфейс |
![]() |
Ethernet (RJ-45) |
![]() |
Память/Процессор |
|
Объем памяти |
1 024 |
Частота процессора |
800 |
Макс, объем памяти |
1 024 |
Дополнительная информация |
|
Экран |
|
Работа от аккумулятора |
|
Поддержка ОС |
|
Windows |
![]() |
Mac OS |
![]() |
Linux |
|
DOS |
|
Потребляемая мощность |
|
При работе | 605 |
В режиме ожидания | 51 |
Уровень шума |
|
В режиме ожидания | 30 |
При работе | 52 |
Габариты |
|
Глубина |
491 |
Вес |
34 |
Ширина |
514 |
Высота |
385 |
Модули
Internal assemblies 1
Paper feeder PCA
CASSETTE
Paper feeder covers
PCAs
1 x 500-sheet paper feeder
Paper pickup assembly
Right-door assembly
External covers, panels, and doors
Internal assemblies 5
Paper feeder main body
Internal assemblies 4
Internal assemblies 3
Paper feeder cassette
Internal assemblies 2
Детали Right-door assembly
Деталь: | LEFT CABLE ASSEMBLY |
Парткод: | RM1-5742-000CN |
Деталь: | Holder, CST positioning |
Парткод: | RC3-1231-000CN |
Цена: | 290 ₽ |
Деталь: | Cover, front inner lower unit (CMK) |
Парткод: | RL1-1914-020CN |
Деталь: | COVER, FRONT INNER, UPPER |
Парткод: | RC3-1070-000CN |
Цена: | 1 200 ₽ |
Деталь: | Cover, front inner lower (Y) |
Парткод: | RL1-1915-000CN |
Деталь: | ROLLER, RAIL |
Парткод: | RC2-4831-000CN |
Цена: | 250 ₽ |
Деталь: | WASTE TONER DETECT ASSEMBLY |
Парткод: | RM1-5696-000CN |
Цена: | 900 ₽ |
Деталь: | Waste toner duct assembly |
Парткод: | RM1-8138-000CN |
Деталь: | SPRING, TENSION |
Парткод: | RU7-2192-000CN |
Цена: | 270 ₽ |
Деталь: | Spring, ground |
Парткод: | RU6-2237-000CN |
Цена: | 360 ₽ |
Деталь: | Lever, cartridge pressure front |
Парткод: | RC2-3983-030CN |
Цена: | 500 ₽ |
Деталь: | LOCK, DOOR |
Парткод: | RC2-5937-000CN |
Цена: | 600 ₽ |
Деталь: | LEVER, BOX PRESENCE DETECT |
Парткод: | RC2-5951-000CN |
Цена: | 320 ₽ |
Деталь: | PCA, paper feeder driver |
Парткод: | RM1-5839-000CN |
Деталь: | CASSETTE |
Парткод: | RM1-8125-000CN |
Деталь: | COVER, LEFT |
Парткод: | RC2-5428-000CN |
Деталь: | COVER, REAR |
Парткод: | RC2-5429-000CN |
Деталь: | COVER, RIGHT |
Парткод: | RC2-5427-000CN |
Деталь: | COVER, FRONT UPPER |
Парткод: | RC2-5425-000CN |
Деталь: | Cover, front right |
Парткод: | RC2-5426-000CN |
Деталь: | STOPPER, DOOR |
Парткод: | RC2-5417-000CN |
Деталь: | COVER, LEFT FRONT |
Парткод: | RC2-5430-000CN |
Деталь: | Link, door right |
Парткод: | RC2-5435-000CN |
Деталь: | RIGHT DOOR ASSEMBLY |
Парткод: | RM1-6192-000CN |

Деталь: | Lower HVPS-D PCA |
Парткод: | RM1-8087-000CN |
Цена: | 2 300 ₽ |
Деталь: | Upper HVPS-T PCA (simplex) |
Парткод: | RM1-8089-000CN |

Деталь: | Upper HVPS-T PCA (duplex) |
Парткод: | RM1-8088-000CN |
Цена: | 2 300 ₽ |
Деталь: | DC controller PCA |
Парткод: | RM1-8104-000CN |
Деталь: | Low-voltage power supply 110V |
Парткод: | RM1-8091-000CN |
Деталь: | Low-voltage power supply 220V |
Парткод: | RM1-8093-000CN |
Деталь: | Inner connecting PCA (ICB) |
Парткод: | RM1-8143-000CN |
Деталь: | Formatter assembly kit (exchange) |
Парткод: | CF081-69001 |
Деталь: | Formatter assembly kit (China) |
Парткод: | CF081-67912 |
Деталь: | 1 x 500-sheet feeder replacement kit |
Парткод: | CF084-67901 |
Деталь: | Paper pickup assembly (simplex) |
Парткод: | RM1-8168-000CN |
Деталь: | Paper pickup assembly (duplex) |
Парткод: | RM1-8124-000CN |

Деталь: | PHOTOINTERRUPTER |
Парткод: | WG8-5935-000CN |
Цена: | 900 ₽ |
Деталь: | Right-door assembly (simplex) |
Парткод: | RM1-8167-000CN |
Деталь: | Right-door assembly (duplex) |
Парткод: | RM1-8123-000CN |
Деталь: | DUPLEXING PAPER FEED ASSEMBLY |
Парткод: | RM1-4959-000CN |
Цена: | 2 500 ₽ |
Деталь: | COVER, REAR UPPER |
Парткод: | RC2-5058-000CN |
Деталь: | PLATE, BLANKING |
Парткод: | RC2-5938-000CN |
Деталь: | COVER, LEFT LOWER |
Парткод: | RC3-1112-000CN |
Деталь: | COVER, LEFT FRONT |
Парткод: | RC3-1113-000CN |
Деталь: | COVER, REAR LOWER |
Парткод: | RC3-1114-000CN |
Деталь: | COVER, REAR |
Парткод: | RC3-1115-000CN |
Деталь: | COVER, RIGHT REAR |
Парткод: | RC3-1116-000CN |
Деталь: | COVER, RIGHT LOWER |
Парткод: | RC3-1117-000CN |
Деталь: | COVER, UPPER |
Парткод: | RC3-1118-000CN |
Деталь: | TRAY, PAPER DELIVERY |
Парткод: | RL1-1941-030CN |
Деталь: | Operation (control) panel assembly |
Парткод: | RM1-8096-000CN |
Деталь: | Cover, USB (simplex) |
Парткод: | RC3-1093-000CN |
Деталь: | Cover, USB (duplex) |
Парткод: | RM1-8173-000CN |
Деталь: | Cover, left assembly |
Парткод: | RM1-8159-000CN |
Деталь: | Cover, right-front assembly |
Парткод: | RM1-8165-000CN |
Деталь: | Duplexing unit cable assembly |
Парткод: | RM1-5730-000CN |
Деталь: | Auto close assembly |
Парткод: | RM1-8137-000CN |
Деталь: | LIFTER DRIVE ASSEMBLY |
Парткод: | RM1-8136-000CN |

Деталь: | Main motor unit (M3, M4, M5) |
Парткод: | RM1-8105-000CN |
Цена: | 7 500 ₽ |
Деталь: | CONNECTOR, DRAWER |
Парткод: | VS1-7258-007CN |

Деталь: | PHOTO INTERRUPTER, TLP1243 |
Парткод: | WG8-5935-000CN |
Цена: | 900 ₽ |
Деталь: | Cassette paper pick up drive assembly (M13) |
Парткод: | RM1-8135-000CN |
Цена: | 1 300 ₽ |
Деталь: | Rear Pre-exposure PCA assembly |
Парткод: | RM1-5705-000CN |
Деталь: | Fusing (fixing) drive assembly (simplex) |
Парткод: | RM1-8169-000CN |
Деталь: | Fusing (fixing) drive assembly (duplex) |
Парткод: | RM1-8134-000CN |
Деталь: | DUPLEXING DRIVE ASSEMBLY |
Парткод: | RM1-4973-000CN |
Деталь: | Stepping motor, DC (developing disengagement M10) |
Парткод: | RK2-2415-000CN |
Цена: | 3 500 ₽ |
Деталь: | Pickup motor assembly (M13) |
Парткод: | RM1-5773-000CN |
Цена: | 5 100 ₽ |

Деталь: | Fusing (fixing) motor assembly (M2) |
Парткод: | RM1-4983-000CN |
Цена: | 7 600 ₽ |
Деталь: | Lifter base assembly |
Парткод: | RM1-5913-000CN |
Деталь: | PAPER FEED ASSEMBLY |
Парткод: | RM1-6194-030CN |

Деталь: | Paper pickup assembly |
Парткод: | RM1-5919-000CN |
Цена: | 5 800 ₽ |
Деталь: | PAPER FEED ROLLER ASSEMBLY |
Парткод: | CF081-67913 |
Деталь: | Roller, paper pickup |
Парткод: | CF081-67913 |
Деталь: | Drawer connector holder |
Парткод: | VS1-7257-007CN |
Деталь: | HOLDER, DRAWER CONNECTOR |
Парткод: | RC2-5416-000CN |
Деталь: | Screw, tapping, pan head M4X10 |
Парткод: | XB4-7401-007CN |
Деталь: | Fusing connecting cable assembly |
Парткод: | RM1-5714-000CN |

Деталь: | Fan (FM1) |
Парткод: | RK2-2416-000CN |
Цена: | 1 000 ₽ |
Деталь: | Cable, flat 2 laser |
Парткод: | RK2-3943-000CN |
Деталь: | Switch arm |
Парткод: | RC2-5943-000CN |
Деталь: | MP sensor cable assembly (simplex) |
Парткод: | RM1-5750-000CN |
Деталь: | MP sensor cable assembly (duplex) |
Парткод: | RM1-5737-000CN |
Деталь: | Cable, flat 1 scanner |
Парткод: | RK2-3941-000CN |
Деталь: | Wire, (mech) sensor protect |
Парткод: | RC2-4828-000CN |
Деталь: | Sensor cable guide assembly |
Парткод: | RM1-8178-000CN |
Деталь: | Cover, right lower inner |
Парткод: | RC2-5019-000CN |
Деталь: | LINK, INTERLOCK |
Парткод: | RC2-5120-000CN |
Деталь: | MOUNT, INTERLOCK SWITCH |
Парткод: | RC2-5123-000CN |
Деталь: | ARM, INTERLOCK LINK SWITCH |
Парткод: | RC2-5121-000CN |
Деталь: | LINK, INTERLOCK |
Парткод: | RC2-5119-000CN |
Деталь: | LINK, INTERLOCK |
Парткод: | RC2-5118-000CN |
Деталь: | SHAFT |
Парткод: | RC2-5913-000CN |
Деталь: | LINK, INTERLOCK |
Парткод: | RC2-5122-000CN |
Деталь: | MICROSWITCH |
Парткод: | WC4-5171-000CN |
Деталь: | DOOR SWITCH ASSEMBLY |
Парткод: | RM1-5732-000CN |
Деталь: | Switch, PCA assembly |
Парткод: | RM1-8097-000CN |
Деталь: | Density detect assembly |
Парткод: | RM1-8163-000CN |
Деталь: | Pick up lower guide assembly |
Парткод: | RM1-8132-000CN |
Деталь: | Paper delivery assembly (simplex) |
Парткод: | RM1-5003-050CN |

Деталь: | Paper delivery assembly (duplex) |
Парткод: | RM1-4970-060CN |
Цена: | 2 100 ₽ |
Деталь: | Registration assembly (simplex) |
Парткод: | RM1-5009-000CN |
Деталь: | Registration assembly (duplex) |
Парткод: | RM1-4969-000CN |
Деталь: | Rear lock arm assembly |
Парткод: | RM1-5533-000CN |
Деталь: | Cassette assembly (Tray 3) |
Парткод: | RM1-6198-000CN |
Деталь: | Fan cable assembly |
Парткод: | RM1-5746-000CN |
Цена: | 700 ₽ |
Деталь: | SPRING, TENSION |
Парткод: | RU6-2436-000CN |
Деталь: | COVER |
Парткод: | RC2-5912-000CN |
Деталь: | COVER |
Парткод: | RC2-5962-000CN |
Деталь: | SPRING, COMPRESSION |
Парткод: | RU6-2316-000CN |
Деталь: | LEVER, SHUTTER |
Парткод: | RC2-4415-000CN |
Деталь: | Temperature sensor assembly |
Парткод: | RK2-3267-000CN |
Цена: | 2 200 ₽ |
Деталь: | Toner sensor holder assembly |
Парткод: | RM1-5700-000CN |

Деталь: | Fan (FM2, FM3) |
Парткод: | RK2-2418-000CN |
Цена: | 2 700 ₽ |
Деталь: | CONNECTING CABLE ASSEMBLY |
Парткод: | RM1-5749-000CN |
Деталь: | Sensor cable assembly |
Парткод: | RM1-5740-000CN |
Деталь: | Sensor cable assembly |
Парткод: | RM1-5741-000CN |
Деталь: | Motor/sensor cable assembly |
Парткод: | RM1-5752-000CN |
Коды ошибок
10.00.00
10.00.10
10.00.15
10.00.25
10.00.34
10.00.35
10.00.40
10.00.41
10.00.60
10.00.70
10.01.00
10.01.10
10.01.15
10.01.25
10.01.34
10.01.35
10.01.40
10.01.41
10.01.60
10.01.70
10.02.00
10.02.10
10.02.15
10.02.25
10.02.34
10.02.35
10.02.40
10.02.41
10.02.60
10.02.70
10.03.00
10.03.10
10.03.15
10.03.25
10.03.34
10.03.35
10.03.40
10.03.41
10.03.60
10.03.70
10.10.15
10.22.50
10.22.51
10.22.52
10.22.60
10.22.70
10.23.15
10.23.35
10.23.50
10.23.51
10.23.52
10.23.60
10.23.70
10.31.15
10.31.60
10.31.70
11.00.01
11.00.02
13.00.00
13.A3.D3
13.A3.D4
13.A3.FF
13.AA.EE
13.B2.9C
13.B2.9Z
13.B2.A1
13.B2.A2
13.B2.A3
13.B2.AZ
13.B2.D1
13.B2.D2
13.B2.D3
13.B2.DD
13.B2.DZ
13.B2.FF
13.B4.FF
13.B9.CZ
13.B9.DD
13.B9.DZ
13.B9.FF
13.BA.EE
13.BB.EE
13.D3.DZ
13.E1.DZ
13.FF.FF
20.00.00
21.00.00
32.08.A1
32.08.A2
32.08.A3
32.1C.01
32.1C.02
32.1C.03
32.1C.04
32.1C.05
32.1C.06
32.1C.07
32.1C.08
32.1C.09
32.1C.0A
32.1C.0B
32.1C.0C
32.1C.0D
32.1C.0E
32.1C.11
32.1C.12
32.1C.13
32.1C.14
32.1C.17
32.1C.1B
32.1C.1C
32.1C.21
32.1C.22
32.1C.24
32.1C.28
32.1C.29
32.1C.2B
32.1C.2E
32.1C.2F
32.21.00
33.01.01
33.01.02
33.01.03
33.02.01
33.02.02
33.02.03
33.XX.YY
41.02.00
41.03.YZ
41.05.YZ
41.07.YZ
42.XX.YY
47.00.XX
47.01.XX
47.02.XX
47.03.XX
47.04.XX
47.05.00
47.06.XX
47.FC.00
47.FC.01
47.FC.02
47.FC.03
47.FC.10
47.FC.11
47.FC.12
47.FC.13
47.FC.20
47.FC.21
47.FC.22
47.FC.23
47.FC.30
47.FC.31
47.FC.32
47.FC.33
47.FC.40
47.FC.41
47.FC.42
47.FC.430
49.XX.YY
50.10X.YZ
50.11X.YZ
50.12X.YZ
50.13X.YZ
50.14X.YZ
50.2X.YZ
50.3X.YZ
50.4X.YZ
50.6X.YZ
50.8X.YZ
51.00.20
51.00.21
51.00.22
51.00.23
52.00.04
52.00.05
54.00.03
54.00.06
54.00.14
54.00.19
54.01.05
54.06.21
54.0X.0B
54.0X.0C
54.0X.0D
54.0X.0E
55.00.01
55.00.02
55.00.07
55.01.06
55.02.06
56.00.YY
57.00.03
57.00.04
57.00.05
58.00.04
59.00.04
59.00.05
59.05.06
59.05.07
59.05.08
59.05.09
59.05.10
59.05.11
59.05.12
59.05.13
59.05.B0
60.00.11
61.00.01
62.00.00
70.00.00
81.01.00
81.02.00
81.03.00
81.04.00
81.06.00
81.07.00
81.08.00
81.09.00
98.00.01
98.00.02
98.00.03
98.00.04
99.00.01
99.00.02
99.00.03
99.00.04
99.00.05
99.00.06
99.00.07
99.00.08
99.00.09
99.00.10
99.00.11
99.00.12
99.00.13
99.00.14
99.00.20
99.00.21
99.00.22
99.00.23
99.00.24
99.00.25
99.00.26
99.00.27
99.09.60
99.09.61
99.09.62
99.09.63
99.09.64
99.09.65
99.09.66
99.09.67
99.XX.YY
Описание
Error code: | 10.00.00 |
Display: | 10.00.00 e-Label Memory Error |
Description: | The printer is unable to read the cartridge data. This message indicates that the printer cannot read or write to the e-label of the toner cartridge. This error can cause the supplies status feature to be disabled. |
Remedy: | 1. Remove, and then reinstall the indicated print cartridge. 2. If the error reappears, turn the power off, and then on. 3. Check the cartridge memory tag. If it is damaged, replace the cartridge. 4. If the error persists, replace the indicated print cartridge. |
Error code: | 10.00.10 |
Display: | 10.00.10 e-Label Missing Memory Error |
Description: | The printer is unable to detect the e-label. This message indicates that the printer has determined that the e-label is missing. This error can cause the supplies status feature to be disabled. |
Remedy: | 1. Remove and the reinstall the indicated print cartridge. 2. If the message displays again, turn the printer off then on. 3. Check the cartridge memory tag. If it is damaged, replace the cartridge. 4. If the error persists, replace the indicated print cartridge. |
Error code: | 10.00.15 |
Display: | 10.00.15 Install <supply> |
Description: | The indicated supply has been removed or installed incorrectly. |
Remedy: | Replace or install the indicated supply. See the parts chapter in the service manual for the correct supply or kit part number. |
Error code: | 10.00.25 |
Display: | Wrong cartridge in <color> slot |
Description: | The indicated slot for a print cartridge contains a cartridge that is not the correct color. From left to right, the print cartridges should be installed in the following order: Black |
Remedy: | Remove the print cartridge from that slot, and install a cartridge that is the correct color. |
Error code: | 10.00.34 |
Display: | 10.XX.34 Used Supply In Use |
Description: | The toner cartridge is used. Black toner cartridge |
Remedy: | Removing a cartridge from one product and then installing it in a different product (for testing functionality) will cause this event code. |
Error code: | 10.00.35 |
Display: | 10.YY.35 Incompatible <supply> |
Description: | The indicated supply is not compatible with this product. Black toner cartridge |
Remedy: | The fuser might be hot. Be careful when removing the fuser. Install a supply that is designed for this product. |
Error code: | 10.00.40 |
Display: | 10.XX.40 Genuine HP Supplies Installed |
Description: | A genuine HP toner cartridge has been installed. Black toner cartridge |
Remedy: | No action necessary. |
Error code: | 10.00.41 |
Display: | 10.XX.41 Unsupported Supply in Use |
Description: | The installed toner cartridge is for a different product. Black toner cartridge |
Remedy: | Remove the toner cartridge, and then install the correct cartridge for this product. |
Error code: | 10.00.60 |
Display: | <Supply> low OR Supplies low |
Description: | The product indicates when a supply level, or more than one supply, is low. Actual print cartridge life might vary. You do not need to replace the print cartridge at this time unless print quality is no longer acceptable. When multiple supplies are low, more than one event code is recorded. Black print cartridge |
Remedy: | If print quality is no longer acceptable, replace the supply. HP recommends that the customer have a replacement supply available to install when print quality is no longer acceptable. |
Error code: | 10.00.70 |
Display: | 10.XX.70 Printing past very low |
Description: | The product indicates when a supply level is very low. The actual remaining toner cartridge life might vary. Black toner cartridge |
Remedy: | If print quality is no longer acceptable, replace the toner cartridge. |
Error code: | 10.01.00 |
Display: | 10.0X.Y0 Supply memory error |
Description: | The product cannot read or write to at least one print cartridge memory tag or a memory tag is missing from a print cartridge. Memory error Cyan print cartridge |
Remedy: | 1. Remove, and then reinstall the indicated print cartridge. 2. If the error reappears, turn the power off, and then on. 3. Check the cartridge e-label. If it is damaged, replace the cartridge. 4. If the error persists, replace the indicated print cartridge. |
Error code: | 10.01.10 |
Display: | 10.0X.Y0 Supply memory error |
Description: | The product cannot read or write to at least one print cartridge memory tag or a memory tag is missing from a print cartridge. E-label missing Cyan print cartridge |
Remedy: | 1. Remove, and then reinstall the indicated print cartridge. 2. If the error reappears, turn the power off, and then on. 3. Check the cartridge e-label. If it is damaged, replace the cartridge. 4. If the error persists, replace the indicated print cartridge. |
Error code: | 10.01.15 |
Display: | 10.YY.15 Install <supply> |
Description: | The indicated supply has been removed or installed incorrectly. Cyan print cartridge |
Remedy: | Replace or install the indicated supply. |
Error code: | 10.01.25 |
Display: | Wrong cartridge in <color> slot |
Description: | The indicated slot for a print cartridge contains a cartridge that is not the correct color. From left to right, the print cartridges should be installed in the following order: Cyan |
Remedy: | Remove the print cartridge from that slot, and install a cartridge that is the correct color. |
Error code: | 10.01.34 |
Display: | 10.XX.34 Used supply in use |
Description: | The indicated cartridge is used. Cyan print cartridge |
Remedy: | NOTE: Removing a cartridge from one product and then installing it in a different product (for testing functionality) will cause this event code. |
Error code: | 10.01.35 |
Display: | 10.YY.35 Incompatible <supply> |
Description: | The indicated supply is not compatible with this product. Cyan print cartridge |
Remedy: | CAUTION: The fuser might be hot. Be careful when removing the fuser. Install a supply that is designed for this product. |
Error code: | 10.01.40 |
Display: | 10.XX.40 Genuine HP supplies installed |
Description: | More than one genuine HP print cartridge has been installed. Cyan print cartridge |
Remedy: | No action necessary. |
Error code: | 10.01.41 |
Display: | 10.XX.41 Unsupported supply in use |
Description: | The indicated print cartridge is for a different product. Cyan print cartridge |
Remedy: | Remove the indicated print cartridge, and then install the correct cartridge for this product. |
Error code: | 10.01.60 |
Display: | <Supply> low OR Supplies low |
Description: | The product indicates when a supply level, or more than one supply, is low. Actual print cartridge life might vary. You do not need to replace the print cartridge at this time unless print quality is no longer acceptable. When multiple supplies are low, more than one event code is recorded. Cyan print cartridge |
Remedy: | If print quality is no longer acceptable, replace the supply. HP recommends that the customer have a replacement supply available to install when print quality is no longer acceptable. |
Error code: | 10.01.70 |
Display: | Replace Supplies |
Description: | This alert appears only if the product is configured to stop when a supplies reach the very low threshold. Two or more supplies have reached the estimated end of life. The product indicates when a supply level is at its estimated end of life. The actual life remaining might be different than estimated. The supply does not need to be replaced now unless the print quality is no longer acceptable. HP recommends that the customer have a replacement supply available to install when print quality is no longer acceptable. NOTE: When an HP supply has reached its approximated end of life, the HP Premium Protection Warranty on that supply ends. Recorded event codes depend on which supplies are at the end of life. Cyan print cartridge |
Remedy: | Press the OK button to find out which supplies need to be replaced. Or, configure the product to continue printing by using the Manage Supplies menu. |
Error code: | 10.02.00 |
Display: | 10.0X.Y0 Supply memory error |
Description: | The product cannot read or write to at least one print cartridge memory tag or a memory tag is missing from a print cartridge. Memory error Magenta print cartridge |
Remedy: | 1. Remove, and then reinstall the indicated print cartridge. 2. If the error reappears, turn the power off, and then on. 3. Check the cartridge e-label. If it is damaged, replace the cartridge. 4. If the error persists, replace the indicated print cartridge. |
Error code: | 10.02.10 |
Display: | 10.0X.Y0 Supply memory error |
Description: | The product cannot read or write to at least one print cartridge memory tag or a memory tag is missing from a print cartridge. E-label missing Magenta print cartridge |
Remedy: | 1. Remove, and then reinstall the indicated print cartridge. 2. If the error reappears, turn the power off, and then on. 3. Check the cartridge e-label. If it is damaged, replace the cartridge. 4. If the error persists, replace the indicated print cartridge. |
Error code: | 10.02.15 |
Display: | Install <supply> |
Description: | A supply item is either not installed or installed incorrectly. Magenta cartridge |
Remedy: | Install the supply item or make sure that the installed supply item is fully seated. |
Error code: | 10.02.25 |
Display: | Wrong cartridge in <color> slot |
Description: | The indicated slot for a print cartridge contains a cartridge that is not the correct color. From left to right, the print cartridges should be installed in the following order: Magenta |
Remedy: | Remove the print cartridge from that slot, and install a cartridge that is the correct color. |
Error code: | 10.02.34 |
Display: | 10.XX.34 Used supply in use |
Description: | The indicated cartridge is used. Magenta print cartridge |
Remedy: | NOTE: Removing a cartridge from one product and then installing it in a different product (for testing functionality) will cause this event code. |
Error code: | 10.02.35 |
Display: | 10.YY.35 Incompatible <supply> |
Description: | The indicated supply is not compatible with this product. Magenta print cartridge |
Remedy: | CAUTION: The fuser might be hot. Be careful when removing the fuser. Install a supply that is designed for this product. |
Error code: | 10.02.40 |
Display: | 10.XX.40 Genuine HP supplies installed |
Description: | More than one genuine HP print cartridge has been installed. Magenta print cartridge |
Remedy: | No action necessary. |
Error code: | 10.02.41 |
Display: | 10.XX.41 Unsupported supply in use |
Description: | The indicated print cartridge is for a different product. Magenta print cartridge |
Remedy: | Remove the indicated print cartridge, and then install the correct cartridge for this product. |
Error code: | 10.02.60 |
Display: | <Supply> low OR Supplies low |
Description: | The product indicates when a supply level, or more than one supply, is low. Actual print cartridge life might vary. You do not need to replace the print cartridge at this time unless print quality is no longer acceptable. When multiple supplies are low, more than one event code is recorded. Magenta print cartridge |
Remedy: | If print quality is no longer acceptable, replace the supply. HP recommends that the customer have a replacement supply available to install when print quality is no longer acceptable. |
Error code: | 10.02.70 |
Display: | Replace Supplies |
Description: | This alert appears only if the product is configured to stop when a supplies reach the very low threshold. Two or more supplies have reached the estimated end of life. The product indicates when a supply level is at its estimated end of life. The actual life remaining might be different than estimated. The supply does not need to be replaced now unless the print quality is no longer acceptable. HP recommends that the customer have a replacement supply available to install when print quality is no longer acceptable. NOTE: When an HP supply has reached its approximated end of life, the HP Premium Protection Warranty on that supply ends. Recorded event codes depend on which supplies are at the end of life. Magenta print cartridge |
Remedy: | Press the OK button to find out which supplies need to be replaced. Or, configure the product to continue printing by using the Manage Supplies menu. |
Error code: | 10.03.00 |
Display: | 10.0X.Y0 Supply memory error |
Description: | The product cannot read or write to at least one print cartridge memory tag or a memory tag is missing from a print cartridge. Memory error Yellow print cartridge |
Remedy: | 1. Remove, and then reinstall the indicated print cartridge. 2. If the error reappears, turn the power off, and then on. 3. Check the cartridge e-label. If it is damaged, replace the cartridge. 4. If the error persists, replace the indicated print cartridge. |
Error code: | 10.03.10 |
Display: | 10.0X.Y0 Supply memory error |
Description: | The product cannot read or write to at least one print cartridge memory tag or a memory tag is missing from a print cartridge. E-label missing Yellow print cartridge |
Remedy: | 1. Remove, and then reinstall the indicated print cartridge. 2. If the error reappears, turn the power off, and then on. 3. Check the cartridge e-label. If it is damaged, replace the cartridge. 4. If the error persists, replace the indicated print cartridge. |
Error code: | 10.03.15 |
Display: | Install <supply> |
Description: | A supply item is either not installed or installed incorrectly. Yellow cartridge |
Remedy: | Install the supply item or make sure that the installed supply item is fully seated. |
Error code: | 10.03.25 |
Display: | Wrong cartridge in <color> slot |
Description: | The indicated slot for a print cartridge contains a cartridge that is not the correct color. From left to right, the print cartridges should be installed in the following order: Yellow |
Remedy: | Remove the print cartridge from that slot, and install a cartridge that is the correct color. |
Error code: | 10.03.34 |
Display: | 10.XX.34 Used supply in use |
Description: | The indicated cartridge is used. Yellow print cartridge |
Remedy: | NOTE: Removing a cartridge from one product and then installing it in a different product (for testing functionality) will cause this event code. |
Error code: | 10.03.35 |
Display: | 10.YY.35 Incompatible <supply> |
Description: | The indicated supply is not compatible with this product. Yellow print cartridge |
Remedy: | CAUTION: The fuser might be hot. Be careful when removing the fuser. Install a supply that is designed for this product. |
Error code: | 10.03.40 |
Display: | 10.XX.40 Genuine HP supplies installed |
Description: | More than one genuine HP print cartridge has been installed. Yellow print cartridge |
Remedy: | No action necessary. |
Error code: | 10.03.41 |
Display: | 10.XX.41 Unsupported supply in use |
Description: | The indicated print cartridge is for a different product. Yellow print cartridge |
Remedy: | Remove the indicated print cartridge, and then install the correct cartridge for this product. |
Error code: | 10.03.60 |
Display: | <Supply> low OR Supplies low |
Description: | The product indicates when a supply level, or more than one supply, is low. Actual print cartridge life might vary. You do not need to replace the print cartridge at this time unless print quality is no longer acceptable. When multiple supplies are low, more than one event code is recorded. Yellow print cartridge |
Remedy: | If print quality is no longer acceptable, replace the supply. HP recommends that the customer have a replacement supply available to install when print quality is no longer acceptable. |
Error code: | 10.03.70 |
Display: | Replace Supplies |
Description: | This alert appears only if the product is configured to stop when a supplies reach the very low threshold. Two or more supplies have reached the estimated end of life. The product indicates when a supply level is at its estimated end of life. The actual life remaining might be different than estimated. The supply does not need to be replaced now unless the print quality is no longer acceptable. HP recommends that the customer have a replacement supply available to install when print quality is no longer acceptable. NOTE: When an HP supply has reached its approximated end of life, the HP Premium Protection Warranty on that supply ends. Recorded event codes depend on which supplies are at the end of life. Yellow print cartridge |
Remedy: | Press the OK button to find out which supplies need to be replaced. Or, configure the product to continue printing by using the Manage Supplies menu. |
Error code: | 10.10.15 |
Display: | Install <supply> |
Description: | A supply item is either not installed or installed incorrectly. Cyan cartridge |
Remedy: | Install the supply item or make sure that the installed supply item is fully seated. |
Error code: | 10.22.50 |
Display: | 10.22.50 |
Description: | The transfer kit life was reset above the order threshold. A new ITB was installed. |
Remedy: | No action necessary. |
Error code: | 10.22.51 |
Display: | 10.22.51 |
Description: | The transfer kit life was reset above the replace threshold. A new ITB was installed. |
Remedy: | No action necessary. |
Error code: | 10.22.52 |
Display: | 10.22.52 |
Description: | The transfer kit life was reset above the reset threshold. A new ITB was installed. |
Remedy: | No action necessary. |
Error code: | 10.22.60 |
Display: | <Supply> low OR Supplies low |
Description: | The product indicates when a supply level, or more than one supply, is low. Actual print cartridge life might vary. You do not need to replace the print cartridge at this time unless print quality is no longer acceptable. When multiple supplies are low, more than one event code is recorded. Transfer kit |
Remedy: | If print quality is no longer acceptable, replace the supply. HP recommends that the customer have a replacement supply available to install when print quality is no longer acceptable. |
Error code: | 10.22.70 |
Display: | Replace Supplies |
Description: | This alert appears only if the product is configured to stop when a supplies reach the very low threshold. Two or more supplies have reached the estimated end of life. The product indicates when a supply level is at its estimated end of life. The actual life remaining might be different than estimated. The supply does not need to be replaced now unless the print quality is no longer acceptable. HP recommends that the customer have a replacement supply available to install when print quality is no longer acceptable. NOTE: When an HP supply has reached its approximated end of life, the HP Premium Protection Warranty on that supply ends. Recorded event codes depend on which supplies are at the end of life. Transfer kit |
Remedy: | Press the OK button to find out which supplies need to be replaced. Or, configure the product to continue printing by using the Manage Supplies menu. |
Error code: | 10.23.15 |
Display: | 10.YY.15 Install <supply> |
Description: | The indicated supply has been removed or installed incorrectly. Fuser kit |
Remedy: | Replace or install the indicated supply. |
Error code: | 10.23.35 |
Display: | 10.YY.35 Incompatible <supply> |
Description: | The indicated supply is not compatible with this product. Fuser kit |
Remedy: | The fuser might be hot. Be careful when removing the fuser. Install a supply that is designed for this product. |
Error code: | 10.23.50 |
Display: | 10.23.50 |
Description: | The fuser kit life was reset above the order threshold. |
Remedy: | No action necessary. |
Error code: | 10.23.51 |
Display: | 10.23.51 |
Description: | The fuser kit life was reset above the replace threshold. |
Remedy: | No action necessary. |
Error code: | 10.23.52 |
Display: | 10.23.52 |
Description: | The fuser kit life was reset above the reset threshold. |
Remedy: | No action necessary. |
Error code: | 10.23.60 |
Display: | 10.23.60 |
Description: | The printer indicates when fuser kit is very low. The actual remaining fuse kit life might vary. You do not need to replace the fuser kit at this time unless print quality is no longer acceptable. |
Remedy: | If print quality is no longer acceptable, replace the fuser kit. See the parts chapter in the service manual for the fuser kit part number. TIP: Advise the customer that HP recommends that they have replacement supplies available to install when the print quality is no longer acceptable. |
Error code: | 10.23.70 |
Display: | 10.23.70 printing past very low |
Description: | The printer indicates when the fuser kit is very low. The actual remaining fuse kit life might vary. |
Remedy: | If print quality is no longer acceptable, the customer must order and pay for a replacement fuser assembly (fuser kit). TIP: Advise the customer that HP recommends that they have replacement supplies available to install when the print quality is no longer acceptable. |
Error code: | 10.31.15 |
Display: | Install <supply> Close rear door |
Description: | The toner collection unit has been removed or has been installed incorrectly. Toner collection unit |
Remedy: | Replace or reinstall the toner collection unit correctly to continue printing. |
Error code: | 10.31.60 |
Display: | <Supply> almost full |
Description: | Toner Collection bottle is almost full. Toner collection unit |
Remedy: | Replace the toner collection unit |
Error code: | 10.31.70 |
Display: | Replace Supplies |
Description: | This alert appears only if the product is configured to stop when a supplies reach the very low threshold. Two or more supplies have reached the estimated end of life. The product indicates when a supply level is at its estimated end of life. The actual life remaining might be different than estimated. The supply does not need to be replaced now unless the print quality is no longer acceptable. HP recommends that the customer have a replacement supply available to install when print quality is no longer acceptable. NOTE: When an HP supply has reached its approximated end of life, the HP Premium Protection Warranty on that supply ends. Recorded event codes depend on which supplies are at the end of life. Toner collection unit |
Remedy: | Press the OK button to find out which supplies need to be replaced. Or, configure the product to continue printing by using the Manage Supplies menu. |
Error code: | 11.00.01 |
Display: | 11.00.01 Internal clock error |
Description: | This message indicates a problem with the formatter`s real time clock. The product real time clock has experienced an error. 01=dead clock 02=dead real time clock |
Remedy: | 1. Whenever the product is turned off and then turned on again, set the time and date on the control panel. 2. If the error persists, you might need to replace the formatter. |
Error code: | 11.00.02 |
Display: | 11.00.01 Internal clock error |
Description: | This message indicates a problem with the formatter`s real time clock. The product real time clock has experienced an error. 01=dead clock 02=dead real time clock |
Remedy: | 1. Whenever the product is turned off and then turned on again, set the time and date on the control panel. 2. If the error persists, you might need to replace the formatter. |
Error code: | 13.00.00 |
Display: | 13.00.00 |
Description: | Generic jam event code. |
Remedy: | Check the printer for a jam. See the clear jams section in the service manual. |
Error code: | 13.A3.D3 |
Display: | 13.A3.D3 |
Description: | Jam In Tray 3 This jam occurs when the media does not reach the Tray 3A feed sensor (PS1404) in the designated amount of time after the start of media pick-up from Tray 3. This is a no-pick jam from Tray 3. |
Remedy: | 1. Open Tray 3, remove any jammed paper, and then close the tray. 2. Open and close the upper right door to allow the product to attempt to clear the jam. 3. Make sure that the Tray 3 pickup, feed, and separation roller are installed correctly and show no damage or wear. 4. Clean or replace the pickup/feed rollers as needed. 5. Check the connectors at the sensor, feed motor, and the DC controller PCA. 6. Check connector (J221) on the DC controller PCA and interconnect J21. 7. Open the following menus: • Administration • Troubleshooting • Diagnostic Tests 8. Test PS1404 using the Tray/Bin Manual sensor test to verify that the sensors are functioning correctly. 9. Run the Tray 3 pickup/feed motor drive test to verify that the feed motor is functioning correctly. If it is not, replace the pickup assembly. 10. If the error persists, replace the paper pickup assembly. |
Error code: | 13.A3.D4 |
Display: | 13.WX.YZ Jam in middle right door |
Description: | Late to path jam from Tray 3 This jam occurs when the paper does not reach the Tray 3 feed sensor (SR1) in designated amount of time. |
Remedy: | Clear the jam. |
Error code: | 13.A3.FF |
Display: | 13.A3.FF |
Description: | Residual Media Jam in Tray 3. This jam occurs when residual media is detected at the Tray 3 feed sensor (PS432). |
Remedy: | 1. Open Tray 3, remove any jammed paper, and then close the tray. 2. Open and close the upper right door to allow the printer to attempt to clear the jam. 3. Remove the paper from the tray and check that the paper tray size guides are properly set and that the tray is not over filled with paper. 4. Make sure that the Tray 3 pickup, feed, and separation roller are installed correctly and show no damage or wear. 5. Clean or replace the pickup/feed rollers as needed. Use a damp, lint-free cloth to gently clean the rollers. 6. Check the connectors at the sensor, feed motor, and the DC controller PCA. 7. Open the following menus: • Administration • Troubleshooting • Diagnostic Tests 8. Test PS432 using the Tray/Bin Manual sensor test to verify that the sensors are functioning correctly. 9. Run the Tray 3 pickup/feed motor drive test to verify that the feed motor is functioning correctly (listen for the motor to activate). If it is not, replace the optional paper feeder. 10. If either of the previous steps fail, elevate the issue to HP for possible printer replacement. NOTE: On-site technicians should check ALL connections on the Paper feed controller PCA before elevating the issue. |
Error code: | 13.AA.EE |
Display: | 13.AA.EE |
Description: | HCI Door Open Jam This jam occurs when the HCI right door (SW3301) is opened during printing. |
Remedy: | 1. Close the Lower Right door to allow the product to attempt to clear the jam. 2. Open the following menus: • Administration • Troubleshooting • Diagnostic Tests 3. Test SW3301 using the Manual Sensor Switch test to verify that the switch is functioning correctly. 4. If the error persists, replace the Merge Assembly. |
Error code: | 13.B2.9C |
Display: | 13.B2.9C |
Description: | Page at duplex switchback jam. |
Remedy: | Check the product for a jam. |
Error code: | 13.B2.9Z |
Display: | 13.WX.YZ Jam below control panel |
Description: | Page at duplex switchback jam. Z = the source tray number |
Remedy: | Check the product for a jam. |
Error code: | 13.B2.A1 |
Display: | 13.B2.Az |
Description: | This jam occurs when the media is present longer than "the expected media length plus 50mm" or more is detected at the Registration sensor (PS4) when printing from the Tray 1. |
Remedy: | 1. Open the front door and clear the jam in the indicated area. 2. Close the door to allow the product to attempt to clear the jam. 3. Make sure that the transfer roller is seated correctly and not worn or deformed. Replace the roller if necessary. 4. Check the registration assembly for proper operation. Replace the registration assembly as needed. 5. If media is stopped under the toner cartridge, but has moved most of the way through registration, try another toner cartridge. If necessary, replace the toner cartridge. 6. Open the following menus: • Administration • Troubleshooting • Diagnostic Tests 7. Test the TOP sensor (PS4) using the Tray/Bin manual sensor test to verify that the sensor is functioning correctly. If it is not, replace the registration sensor assembly. |
Error code: | 13.B2.A2 |
Display: | 13.B2.Az |
Description: | This jam occurs when the media is present longer than" the expected media length plus 50mm" or more is detected at the Registration sensor (PS4) when printing from the Tray 2. |
Remedy: | 1. Open the front door and clear the jam in the indicated area. 2. Close the door to allow the product to attempt to clear the jam. 3. Make sure that the transfer roller is seated correctly and not worn or deformed. Replace the roller if necessary. 4. Check the registration assembly for proper operation. Replace the registration assembly as needed. 5. If media is stopped under the toner cartridge, but has moved most of the way through registration, try another toner cartridge. If necessary, replace the toner cartridge. 6. Open the following menus: • Administration • Troubleshooting • Diagnostic Tests 7. Test the TOP sensor (PS4) using the Tray/Bin manual sensor test to verify that the sensor is functioning correctly. If it is not, replace the registration sensor assembly. |
Error code: | 13.B2.A3 |
Display: | 13.B2.Az |
Description: | This jam occurs when the media is present longer than "the expected media length plus 50mm" or more is detected at the Registration sensor (PS4) when printing from the Tray 3. |
Remedy: | 1. Open the front door and clear the jam in the indicated area. 2. Close the door to allow the product to attempt to clear the jam. 3. Make sure that the transfer roller is seated correctly and not worn or deformed. Replace the roller if necessary. 4. Check the registration assembly for proper operation. Replace the registration assembly as needed. 5. If media is stopped under the toner cartridge, but has moved most of the way through registration, try another toner cartridge. If necessary, replace the toner cartridge. 6. Open the following menus: • Administration • Troubleshooting • Diagnostic Tests 7. Test the TOP sensor (PS4) using the Tray/Bin manual sensor test to verify that the sensor is functioning correctly. If it is not, replace the registration sensor assembly. |
Error code: | 13.B2.AZ |
Display: | 13.WX.YZ Jam in right door |
Description: | Stopped at registration jam. This jam occurs when the media is longer than the longest Universal size, (470 mm; 18.50 in), by 40 mm (1.57 in) or more, and printing from Tray 1. However, this jam occurs when the media that is longer than the designated length by 40 mm (1.57 in) and more is detected, if the media that is longer than the longest Universal is designated. This jam occurs when the media longer than LEDGER-P by 40 mm (1.57 in) or more is detected at printing from Tray 2. Z = the source tray number |
Remedy: | Clear the jam. |
Error code: | 13.B2.D1 |
Display: | 13.B2.Dz |
Description: | Media delay jam at registration sensor PS4. This jam occurs when the media does not reach the Registration sensor (PS4) in the designated amount of time after the Tray 1 feed sensor (PS2502) sensed the leading edge when printing from Tray 1. |
Remedy: | 1. Open the front and right doors and clear the jam in the indicated area. Inspect the paper path and make sure that no paper is blocking the paper path. 2. Check the registration assembly for proper orientation. Replace the registration assembly as needed. 3. Open the following menus: • Administration • Troubleshooting • Diagnostic Tests 4. Test the TOP sensor (PS4) using the Tray/Bin manual sensor test to verify that the sensor is functioning correctly. If it is not, replace the registration sensor assembly. 5. Touch Component Test. 6. Run the Tray 2 intermediate feed motor (M3) drive test to verify that the feed motor is functioning correctly. If it is not, replace the pickup assembly. 7. If the error only occurs when duplexing, check the duplexer for blockage or damage and replace as needed. |
Error code: | 13.B2.D2 |
Display: | 13.B2.Dz |
Description: | Media delay jam at registration sensor PS4. This jam occurs when the media does not reach the Registration sensor (PS4) in the designated amount of time after the Tray 2C feed sensor (PS8) sensed the leading edge when printing from Tray 2. |
Remedy: | 1. Open the front and right doors and clear the jam in the indicated area. Inspect the paper path and make sure that no paper is blocking the paper path. 2. Check the registration assembly for proper orientation. Replace the registration assembly as needed. 3. Open the following menus: • Administration • Troubleshooting • Diagnostic Tests 4. Test the TOP sensor (PS4) using the Tray/Bin manual sensor test to verify that the sensor is functioning correctly. If it is not, replace the registration sensor assembly. 5. Touch Component Test. 6. Run the Tray 2 intermediate feed motor (M3) drive test to verify that the feed motor is functioning correctly. If it is not, replace the pickup assembly. 7. If the error only occurs when duplexing, check the duplexer for blockage or damage and replace as needed. |
Error code: | 13.B2.D3 |
Display: | 13.B2.Dz |
Description: | Media delay jam at registration sensor PS4. This jam occurs when the media does not reach the Registration sensor (PS4) in the designated amount of time after the Tray 2C feed sensor (PS8) sensed the leading edge when printing from Tray 3. |
Remedy: | 1. Open the front and right doors and clear the jam in the indicated area. Inspect the paper path and make sure that no paper is blocking the paper path. 2. Check the registration assembly for proper orientation. Replace the registration assembly as needed. 3. Open the following menus: • Administration • Troubleshooting • Diagnostic Tests 4. Test the TOP sensor (PS4) using the Tray/Bin manual sensor test to verify that the sensor is functioning correctly. If it is not, replace the registration sensor assembly. 5. Touch Component Test. 6. Run the Tray 2 intermediate feed motor (M3) drive test to verify that the feed motor is functioning correctly. If it is not, replace the pickup assembly. 7. If the error only occurs when duplexing, check the duplexer for blockage or damage and replace as needed. |
Error code: | 13.B2.DD |
Display: | 13.B2.Dz |
Description: | Media delay jam at registration sensor PS4. This jam occurs when the media does not reach the Registration sensor (PS4) in the designated amount of time after leaving the Duplex Wait Point when duplexing. |
Remedy: | 1. Open the front and right doors and clear the jam in the indicated area. Inspect the paper path and make sure that no paper is blocking the paper path. 2. Check the registration assembly for proper orientation. Replace the registration assembly as needed. 3. Open the following menus: • Administration • Troubleshooting • Diagnostic Tests 4. Test the TOP sensor (PS4) using the Tray/Bin manual sensor test to verify that the sensor is functioning correctly. If it is not, replace the registration sensor assembly. 5. Touch Component Test. 6. Run the Tray 2 intermediate feed motor (M3) drive test to verify that the feed motor is functioning correctly. If it is not, replace the pickup assembly. 7. If the error only occurs when duplexing, check the duplexer for blockage or damage and replace as needed. |
Error code: | 13.B2.DZ |
Display: | 13.WX.YZ Jam in right door |
Description: | Late to registration jam, from tray <Z> This jam occurs when the paper does not reach the registration (TOP; SR8) sensor in the designated amount of time after the Tray 3 feed sensor sensed the leading edge at printing from Tray 3. Z = source tray |
Remedy: | Clear the jam. |
Error code: | 13.B2.FF |
Display: | 13.B2.FF Jam in top cover |
Description: | Media residual jam in top cover at image area. Paper present at SR2 at power on or after clearing jam. |
Remedy: | 1. Open top cover and check for media jammed in feed area. 2. Check under toner cartridge at transfer area, make sure everything is properly seated. 3. Test the top of page sensor (SR2). 4. If the sensor fails test, elevate the issue to HP for possible printer replacement. NOTE: On-site technicians should check the following connections on the DC controller PCA to ensure they are properly seated and connected before elevating the issue. (J151, J110, J144) |
Error code: | 13.B4.FF |
Display: | 13.B4.FF |
Description: | Residual Media jam Loop sensor (PS9) This jam occurs when residual media is detected at the Loop sensor (PS9) at power on. |
Remedy: | 1. Open the front door and clear the jam in the indicated area. 2. Close the door to allow the product to attempt to clear the jam. 3. If the issue persists as another specific Paper Jam, troubleshoot the specified Jam location. 4. Open the following menus: • Administration • Troubleshooting • Diagnostic Tests 5. Test the Loop sensor (PS9) using the Tray/Bin manual sensor test to verify that the sensor is functioning correctly. If it is not, replace the assembly containing Loop Sensor PS9. |
Error code: | 13.B9.CZ |
Display: | 13.WX.YZ Fuser wrap jam |
Description: | Fuser wrap jam This jam occurs when the paper disappears from the fuser output sensor before a designated amount of time after the paper reached the fuser output sensor (It is determined that the paper is being wrapped around the fuser roller). Z = fuser mode 1 = Normal auto sense 2 = Normal non-auto sense 3 = Light 1 to 3 4 = Heavy 1 5 = Heavy 2 6 = Heavy 3 7 = Glossy 1 8 = Glossy 2 9 = Glossy 3 A = Glossy film |
Remedy: | Clear the jam. |
Error code: | 13.B9.DD |
Display: | 13.WX.YZ Jam in right door |
Description: | Late to fuser jam, from duplexer This jam occurs when the paper does not reach the fuser output sensor in designated amount of time. |
Remedy: | Clear the jam. |
Error code: | 13.B9.DZ |
Display: | 13.WX.YZ Fuser area jam |
Description: | Stopped at fuser jam This jam occurs when the paper stays at the fuser output sensor for a designated amount of time after it has reached the fuser output sensor: Z = the source tray number This jam occurs when the paper does not reach the fuser output sensor in the designated amount of time. |
Remedy: | Clear the jam. See the clear jams section in the service manual. For a 13.B9.DZ jam: Make sure media is within specifications, check for obstructions in the fuser, check that the T2 roller is installed properly. |
Error code: | 13.B9.FF |
Display: | 13.B9.FF |
Description: | Residual Media jam Fuser Output Sensor. Paper present at SR13 after specified time limit or on power up. |
Remedy: | 1. Open the top and rear cover and clear the jam in the indicated area. 2. Close the covers to allow the printer to attempt to clear the jam. 3. Verify the media meets HP specification for the printer. 4. Remove the fuser and inspect the fuser sleeve, pressure roller, and delivery roller for blockage and/or damage. Replace the fuser as needed. CAUTION: The fuser might be HOT. 5. Open the following menus: • Administration • Troubleshooting • Diagnostic Tests 6. Test the Fuser Delivery sensor (SR13) using the manual sensor test to verify the sensor is functioning correctly. If it is not, replace the fuser. 7. Run the Fuser motor drive test to verify that the Fuser Drive and Gears are functioning correctly. If they are not, elevate the issue to HP for possible printer replacement. |
Error code: | 13.BA.EE |
Display: | 13.BA.EE |
Description: | This jam occurs when the engine front door (SW8) is opened during printing. |
Remedy: | 1. Close the front door. 2. Check the projection tabs of the front door that engage the door sensor (SW8). If damaged, replace the appropriate part. 3. Use the Manual sensor test to activate the door switch. Replace the switch if it is not functioning correctly. 4. Check connector J302 on the DC controller PCA and connector J3 on SW8. |
Error code: | 13.BB.EE |
Display: | 13.BB.EE |
Description: | This jam occurs when the engine right door (SW7) is opened during printing. |
Remedy: | 1. Close the right door. 2. Check the projection tabs of the right door that engage the door sensor (SW7). If damaged, replace the appropriate part. 3. Use the Manual sensor test to activate the door switch. Replace the switch if it is not functioning correctly. 4. Check connector J302 on the DC controller PCA and connector J3 on SW7. |
Error code: | 13.D3.DZ |
Display: | 13.D3.DZ |
Description: | Late to duplex re-feed jam Z = fuser mode |
Remedy: | Check the product for a jam. |
Error code: | 13.E1.DZ |
Display: | 13.WX.YZ Fuser area jam |
Description: | Stopped at fuser jam This jam occurs when the paper stays at the fuser output sensor for a designated amount of time after it has reached the fuser output sensor: Z = fuser mode This jam occurs when the paper stays at the fuser output sensor for a designated amount of time after it has reached the fuser output sensor. |
Remedy: | Clear the jam. See the clear jams section in the service manual. For a 13.B9.DZ jam: Make sure media is within specifications, check for obstructions in the fuser, check that the T2 roller is installed properly. |
Error code: | 13.FF.FF |
Display: | 13.FF.FF |
Description: | A power on residual paper jam has occurred. This error has no specific sensor designated. It could be any sensor in the media feed path. |
Remedy: | 1. Check the printer for a jam.2. Look for media present or obstructions in paper path. View event log to determine if other Jam errors are occurring and troubleshoot those errors.3. Use the Manual sensors test or Tray/Bin manual sensors test to isolate a faulty door switch or sensor.4. Replace parts as determined by Sensor tests or obstructions. If sensor can not be replaced, elevate the issue for possible printer replacement. |
Error code: | 20.00.00 |
Display: | 20.00.00 Insufficient memory <device> |
Description: | Insufficient memory: <Device> Event log error message 20.00.00. The product does not have enough memory to print the page. The product received more data than can fit in the available memory. You might have tried to transfer too many macros, soft fonts, or complex graphics. |
Remedy: | Touch the OK button to print the transferred data. Some data might be lost. Reduce the page complexity or add product memory. |
Error code: | 21.00.00 |
Display: | 21.00.00 Page Too Complex Event log error message 21.00.00. |
Description: | Page Too Complex Event log error message 21.00.00. The product displays this message to indicate that the page decompression process was too slow for the product. |
Remedy: | Touch the OK button to continue. There may be some data loss on the page that was being formatted when the error occurred. |
Error code: | 32.08.A1 |
Display: | 32.08.XX |
Description: | Initialized after abnormal shutdown |
Remedy: | No action necessary |
Error code: | 32.08.A2 |
Display: | 32.08.XX |
Description: | Clean shutdown |
Remedy: | No action necessary |
Error code: | 32.08.A3 |
Display: | 32.08.XX |
Description: | Normal initialization |
Remedy: | No action necessary |
Error code: | 32.1C.01 |
Display: | 32.1C.01 |
Description: | NVRAM backup/restore service backup started |
Error code: | 32.1C.02 |
Display: | 32.1C.02 |
Description: | NVRAM backup/restore service restore started |
Error code: | 32.1C.03 |
Display: | 32.1C.03 |
Description: | NVRAM backup/restore administrator backup started |
Error code: | 32.1C.04 |
Display: | 32.1C.04 |
Description: | NVRAM backup/restore administrator restore started |
Error code: | 32.1C.05 |
Display: | 32.1C.05 |
Description: | The restore job ticket was submitted with invalid credentials. There was an error during the creation, read, or write of the restore file. |
Remedy: | Verify the credentials that were submitted. Check the domain, user name, and password. |
Error code: | 32.1C.06 |
Display: | 32.1C.06 |
Description: | The backup job ticket was submitted with invalid credentials. |
Remedy: | Verify the credentials that were submitted. Check the domain, user name, and password. |
Error code: | 32.1C.07 |
Display: | 32.1C.07 |
Description: | Backup restore permissions error. |
Remedy: | Retry the job. |
Error code: | 32.1C.08 |
Display: | 32.1C.08 |
Description: | Not enough disk space to perform backup/restore or network share issue. There was an error during the creation, read, or write of the backup file. |
Remedy: | • Retry the job. • Remove stored jobs and retry. • Use a larger capacity storage device. • Check the network share. Remove any stored jobs, and then retry. If the error persists, try using a larger capacity storage device and check the network share settings. |
Error code: | 32.1C.09 |
Display: | 32.1C.09 |
Description: | Tried to restore a backup file that was not valid for this printer. The data in the backup file specified in the restore job ticket is no longer valid due to a corruption of the data or no loner present. |
Remedy: | Use a valid backup file. |
Error code: | 32.1C.0A |
Display: | 32.1C.0A |
Description: | Backup file is invalid The data in the backup file specified in the restore job ticket is no longer valid due to a corruption of the data or no loner present. |
Remedy: | Use a valid backup file. Reboot, and then observe the state of the printer. If the error persists, perform a partition clean from the Preboot menu. |
Error code: | 32.1C.0B |
Display: | 32.1C.0B |
Description: | Backup is from newer version of FW than what is currently on the product |
Error code: | 32.1C.0C |
Display: | 32.1C.0C |
Description: | Backup cancelled from the HP Embedded Web Server |
Error code: | 32.1C.0D |
Display: | 32.1C.0D |
Description: | Backup/restore failed, auto-reboot failed, or the printer might be busy. |
Remedy: | Reboot, and then retry the backup/restore. |
Error code: | 32.1C.0E |
Display: | 32.1C.0E |
Description: | Backup/restore timeout while communicating with the formatter |
Error code: | 32.1C.11 |
Display: | 32.1C.11 |
Description: | Backup/restore time-out while communicating with the engine. The backup was aborted because the printer is busy. |
Remedy: | Wait until the printer is idle, and then try again. |
Error code: | 32.1C.12 |
Display: | 32.1C.12 |
Description: | Backup/restore timeout while communicating with the disk |
Error code: | 32.1C.13 |
Display: | 32.1C.13 |
Description: | Scheduled backup failure |
Error code: | 32.1C.14 |
Display: | 32.1C.14 |
Description: | NVRAM restore timeout while communicating with the formatter |
Error code: | 32.1C.17 |
Display: | 32.1C.17 |
Description: | NVRAM restore timeout while communicating with the engine |
Error code: | 32.1C.1B |
Display: | 32.1C.1B |
Description: | Backup of print subsystem failed |
Error code: | 32.1C.1C |
Display: | 32.1C.1C |
Description: | Backup of networking subsystem failed |
Error code: | 32.1C.21 |
Display: | 32.1C.21 |
Description: | Restore of print subsystem failed |
Error code: | 32.1C.22 |
Display: | 32.1C.22 |
Description: | Restore of networking subsystem failed |
Error code: | 32.1C.24 |
Display: | 32.1C.24 |
Description: | NVRAM backup/restore successful |
Error code: | 32.1C.28 |
Display: | 32.1C.28 |
Description: | Reset of print subsystem failed |
Error code: | 32.1C.29 |
Display: | 32.1C.29 |
Description: | Reset of networking subsystem failed |
Error code: | 32.1C.2B |
Display: | 32.1C.2B |
Description: | Reset formatter timeout |
Error code: | 32.1C.2E |
Display: | 32.1C.2E |
Description: | The restore was aborted because the printer is busy. |
Remedy: | Wait until the printer is idle, and then try again. Turn the printer off then on, and then retry. |
Error code: | 32.1C.2F |
Display: | 32.1C.2F |
Description: | Reset failure. |
Remedy: | Turn the printer off then on, and then retry. |
Error code: | 32.21.00 |
Display: | 32.21.00 |
Description: | Corrupt firmware in external accessory |
Remedy: | Turn the product off, then on, and retry. If the error persists, clear the firmware image from the active partition by using the Partial Clean item in the Preboot menu |
Error code: | 33.01.01 |
Display: | 33.01.01 |
Description: | Recover occurred |
Error code: | 33.01.02 |
Display: | 33.01.02 |
Description: | Initial save occurred |
Error code: | 33.01.03 |
Display: | 33.01.03 |
Description: | Save/recover status OK |
Error code: | 33.02.01 |
Display: | 33.02.01 Used board/disk installed |
Description: | Used board/disk installed Used board disk installed. An encrypted board or disk with existing data previously locked to a different product has replaced the original. If you continue, data is permanently lost. |
Remedy: | 1. Reinstall the used board or disk back into its original printer. 2. To save the data on the board or disk, turn the product off. Replace the board or disk with another board or disk. 3. To delete the data on the board or disk and continue, touch the OK button. |
Error code: | 33.02.02 |
Display: | 33.02.02 |
Description: | Save/recover disabled (one or both disabled) |
Error code: | 33.02.03 |
Display: | 33.02.03 |
Description: | Save/recover disabled (product functions normally) |
Error code: | 33.XX.YY |
Display: | 33.XX.YY Used board/disk |
Description: | An encryped board or disk with existing data previously locked to a different product has replaced the original. If you continue, data is permanently lost. |
Remedy: | To save the data on the board or disk, turn the product off. Replace the board or disk with another board or disk. To delete the data on the board or disk and continue, press the OK button. |
Error code: | 41.02.00 |
Display: | 41.02.00 Error |
Description: | A beam detected misprint error occurred. |
Remedy: | 1. To clear the error message, touch OK.2. If the error persists, turn the printer off, and then on again.3. Verify that the toner cartridge is in good condition and the shutter works properly. Swap toner cartridge to test as needed.4. If the error returns, check the wire harness from the laser/scanners to the DC controller.5. If the error persists, replace the laser scanner assembly and the Laser Scanner Cable. |
Error code: | 41.03.YZ |
Display: | 41.03.YZ Unexpected size in tray <X> |
Description: | Unexpected size in tray <X> The product detected a different paper size than expected. Y = Type, Z = Tray• Y = 0 Size mismatch. Detected media is longer or shorter than expected.• Y = A Size mismatch. Detected media too long.• Y = B Size mismatch. Detected media too short.• Y = C Size mismatch. Inter-page gap error.• Z = D Source is the duplexer.• Z = 1 Source is Tray 1.• Z = 2 Source is Tray 2.• Z = 3 Source is Tray 3. |
Remedy: | 1. Touch OK to use another tray.2. Make sure that the tray is loaded with the correct paper size and that the sliding paper guides are correctly adjusted.3. Use the Tray/Bin manual sensor test to verify that the cassette media switch is correctly functioning.4. If the issue persists, replace the Mech kit. |
Error code: | 41.05.YZ |
Display: | 41.05.YZ Unexpected type in tray <X> |
Description: | The printer can detect the type of paper in the paper path, and it adjusts the print mode accordingly. Tray X is loaded with a media type (transparencies, envelopes, etc.) that is different than what they tray is configured to use. Y = Expected type, Z = Detected type • Y = 0: Photo Media (1, 2, or 3) • Y = 1: Auto Sense (Normal) • Y = 2: Normal (typed not from Auto Sense) • Y = 3: Light media 1, 2, or 3 mode • Y = 4: Heavy media 1 • Y = 5: Heavy media 2 • Y = 6: Heavy media 3 • Y = 7: Glossy media 1 • Y = 8: Glossy media 2 • Y = 9: Glossy media 3 • Y = A: Glossy film • Y = B: OHT • Y = C: Label • Y = D: Envelope 1, 2, or 3 mode • Y = E: Rough • Y = F: Other mode • Z = 0: Photo Media (1, 2, or 3) • Z = 1: Auto Sense (Normal) • Z = 2: Normal (typed not from Auto Sense) • Z = 3: Light media 1, 2, or 3 mode • Z = 4: Heavy media 1 • Z = 5: Heavy media 2 • Z = 6: Heavy media 3 • Z = 7: Glossy media 1 • Z = 8: Glossy media 2 • Z = 9: Glossy media 3 • Z = A: Glossy film • Z = B: OHT • Z = C: Label • Z = D: Envelope 1, 2, or 3 mode • Z = E: Rough • Z = F: Other mode |
Remedy: | 1. Load the tray with the size and type of paper indicated, or use another tray if available.2. If this message displays and the tray is loaded with the correct paper type, check the print driver settings to make sure they match the tray type settings.3. Check all application and printer settings to make sure that the Type setting is correct.4. Clean the Media sensor.5. If the error persists, elevate issue for printer replacement. |
Error code: | 41.07.YZ |
Display: | 41.07.YZ Error To continue, press OK |
Description: | A media transportation error has occurred. Y = 0 Photo media 1, Photo media 2, Photo media 3, Designated media 2, Designated media 3, or N/ A, typed or AutoSense Y = 1 AutoSense (Normal): special case distinguished from typed Normal Y = 2 Normal: typed (not AutoSense) Y = 3 Light media 1, 2, or 3: typed or AutoSense Y = 4 Heavy media 1: typed or AutoSense Y = 5 Heavy media 2: typed or AutoSense Y = 6 Heavy media 3: typed or AutoSense Y = 7 Glossy media 1: typed or AutoSense Y = 8 Glossy media 2: typed or AutoSense Y = 9 Glossy media 3: typed or AutoSense Y = A Glossy film: typed or AutoSense Y = B OHT: typed or AutoSense Y = C Label Y = D Envelope 1, Envelope 2, or Envelope 3 Y = E Rough (designated media 1): typed or AutoSense Z = 1 Tray 1 Z = 2 Tray 2 Z = 3 Tray 3 |
Remedy: | Turn the product off, and then on. If the error persists, replace the DC controller PCA. |
Error code: | 42.XX.YY |
Display: | 42.XX.YY Error Event Log message |
Description: | Error Event Log message Internal system failure. |
Remedy: | 1. Turn the product off, then on, and then retry.2. If the error persists, clear the firmware image from the active partition by using the Partial Clean item in the Preboot menu. |
Error code: | 47.00.XX |
Display: | 47.00.XX |
Description: | Back channel internal error. |
Remedy: | 1. Turn the product off, and then on again.2. Resend the print job.3. If the error persists, clear the active partition by using the Partial Clean item in the Preboot menu. |
Error code: | 47.01.XX |
Display: | 47.01.XX |
Description: | Image transformer internal error. |
Remedy: | 1. Turn the product off, and then on again.2. Resend the print job.3. If the error persists, clear the active partition by using the Partial Clean item in the Preboot menu. |
Error code: | 47.02.XX |
Display: | 47.02.XX |
Description: | Job parser internal error. |
Remedy: | 1. Turn the product off, and then on again.2. Resend the print job.3. If the error persists, clear the active partition by using the Partial Clean item in the Preboot menu. |
Error code: | 47.03.XX |
Display: | 47.03.XX |
Description: | Print job internal error. |
Remedy: | 1. Turn the product off, and then on again.2. Resend the print job.3. If the error persists, clear the active partition by using the Partial Clean item in the Preboot menu. |
Error code: | 47.04.XX |
Display: | 47.04.XX |
Description: | Print spooler 9100 internal error. |
Remedy: | 1. Turn the product off, and then on again.2. Resend the print job.3. If the error persists, clear the active partition by using the Partial Clean item in the Preboot menu. |
Error code: | 47.05.00 |
Display: | 47.05.00 |
Description: | Print spooler framework internal error. |
Remedy: | 1. Turn the product off, and then on again.2. Resend the print job.3. If the error persists, clear the active partition by using the Partial Clean item in the Preboot menu. |
Error code: | 47.06.XX |
Display: | 47.06.XX |
Description: | Print application internal error. |
Remedy: | 1. Turn the product off, and then on again.2. Resend the print job.3. If the error persists, clear the active partition by using the Partial Clean item in the Preboot menu. |
Error code: | 47.FC.00 |
Display: | 47.WX.YZ Printer calibration error To continue, press OK |
Description: | The device is unable to access or implement one of the image patterns files. Y = calibration type, Z = event Color plane registration (CPR) Image not found at system initialization |
Remedy: | Turn the product off, and then on. If the error persists, reload the firmware. |
Error code: | 47.FC.01 |
Display: | 47.WX.YZ Printer calibration error To continue, press OK |
Description: | The device is unable to access or implement one of the image patterns files. Y = calibration type, Z = event CPR Store Image failure |
Remedy: | Turn the product off, and then on. If the error persists, reload the firmware. |
Error code: | 47.FC.02 |
Display: | 47.WX.YZ Printer calibration error To continue, press OK |
Description: | The device is unable to access or implement one of the image patterns files. Y = calibration type, Z = event CPR Image not found |
Remedy: | Turn the product off, and then on. If the error persists, reload the firmware. |
Error code: | 47.FC.03 |
Display: | 47.WX.YZ Printer calibration error To continue, press OK |
Description: | The device is unable to access or implement one of the image patterns files. Y = calibration type, Z = event CPR Print engine execution failure |
Remedy: | Turn the product off, and then on. If the error persists, reload the firmware. |
Error code: | 47.FC.10 |
Display: | 47.WX.YZ Printer calibration error To continue, press OK |
Description: | The device is unable to access or implement one of the image patterns files. Y = calibration type, Z = event Consecutive Dmax Dhalf Image not found at system initialization |
Remedy: | Turn the product off, and then on. If the error persists, reload the firmware. |
Error code: | 47.FC.11 |
Display: | 47.WX.YZ Printer calibration error To continue, press OK |
Description: | The device is unable to access or implement one of the image patterns files. Y = calibration type, Z = event Consecutive Dmax Dhalf Store image failure |
Remedy: | Turn the product off, and then on. If the error persists, reload the firmware. |
Error code: | 47.FC.12 |
Display: | 47.WX.YZ Printer calibration error To continue, press OK |
Description: | The device is unable to access or implement one of the image patterns files. Y = calibration type, Z = event Consecutive Dmax Dhalf Image not found |
Remedy: | Turn the product off, and then on. If the error persists, reload the firmware. |
Error code: | 47.FC.13 |
Display: | 47.WX.YZ Printer calibration error To continue, press OK |
Description: | The device is unable to access or implement one of the image patterns files. Y = calibration type, Z = event Consecutive Dmax Dhalf Print engine execution failure |
Remedy: | Turn the product off, and then on. If the error persists, reload the firmware. |
Error code: | 47.FC.20 |
Display: | 47.WX.YZ Printer calibration error To continue, press OK |
Description: | The device is unable to access or implement one of the image patterns files. Y = calibration type, Z = event Error Diffusion Image not found at system initialization |
Remedy: | Turn the product off, and then on. If the error persists, reload the firmware. |
Error code: | 47.FC.21 |
Display: | 47.WX.YZ Printer calibration error To continue, press OK |
Description: | The device is unable to access or implement one of the image patterns files. Y = calibration type, Z = event Error Diffusion Store image failure |
Remedy: | Turn the product off, and then on. If the error persists, reload the firmware. |
Error code: | 47.FC.22 |
Display: | 47.WX.YZ Printer calibration error To continue, press OK |
Description: | The device is unable to access or implement one of the image patterns files. Y = calibration type, Z = event Error Diffusion Image not found |
Remedy: | Turn the product off, and then on. If the error persists, reload the firmware. |
Error code: | 47.FC.23 |
Display: | 47.WX.YZ Printer calibration error To continue, press OK |
Description: | The device is unable to access or implement one of the image patterns files. Y = calibration type, Z = event Error Diffusion Print engine execution failure |
Remedy: | Turn the product off, and then on. If the error persists, reload the firmware. |
Error code: | 47.FC.30 |
Display: | 47.WX.YZ Printer calibration error To continue, press OK |
Description: | The device is unable to access or implement one of the image patterns files. Y = calibration type, Z = event Drum Speed Adjustment Image not found at system initialization |
Remedy: | Turn the product off, and then on. If the error persists, reload the firmware. |
Error code: | 47.FC.31 |
Display: | 47.WX.YZ Printer calibration error To continue, press OK |
Description: | The device is unable to access or implement one of the image patterns files. Y = calibration type, Z = event Drum Speed Adjustment Store image failure |
Remedy: | Turn the product off, and then on. If the error persists, reload the firmware. |
Error code: | 47.FC.32 |
Display: | 47.WX.YZ Printer calibration error To continue, press OK |
Description: | The device is unable to access or implement one of the image patterns files. Y = calibration type, Z = event Drum Speed Adjustment Image not found |
Remedy: | Turn the product off, and then on. If the error persists, reload the firmware. |
Error code: | 47.FC.33 |
Display: | 47.WX.YZ Printer calibration error To continue, press OK |
Description: | The device is unable to access or implement one of the image patterns files. Y = calibration type, Z = event Drum Speed Adjustment Print engine execution failure |
Remedy: | Turn the product off, and then on. If the error persists, reload the firmware. |
Error code: | 47.FC.40 |
Display: | 47.WX.YZ Printer calibration error To continue, press OK |
Description: | The device is unable to access or implement one of the image patterns files. Y = calibration type, Z = event Pulse Width Modulation Image not found at system initializatione |
Remedy: | Turn the product off, and then on. If the error persists, reload the firmware. |
Error code: | 47.FC.41 |
Display: | 47.WX.YZ Printer calibration error To continue, press OK |
Description: | The device is unable to access or implement one of the image patterns files. Y = calibration type, Z = event Pulse Width Modulation Store image failure |
Remedy: | Turn the product off, and then on. If the error persists, reload the firmware. |
Error code: | 47.FC.42 |
Display: | 47.WX.YZ Printer calibration error To continue, press OK |
Description: | The device is unable to access or implement one of the image patterns files. Y = calibration type, Z = event Pulse Width Modulation Image not found |
Remedy: | Turn the product off, and then on. If the error persists, reload the firmware. |
Error code: | 47.FC.430 |
Display: | 47.WX.YZ Printer calibration error To continue, press OK |
Description: | The device is unable to access or implement one of the image patterns files. Y = calibration type, Z = event Pulse Width Modulation Print engine execution failure |
Remedy: | Turn the product off, and then on. If the error persists, reload the firmware. |
Error code: | 49.XX.YY |
Display: | 49 Error, Turn off then on |
Description: | Error To continue turn off then on A firmware error occurred. Corrupted print jobs, software application issues, non-product specific print drivers, poor quality USB or network cables, bad network connections or incorrect configurations, invalid firmware operations, or unsupported accessories can cause this error. |
Remedy: | 1. Turn the product off, and then on. 2. If the error persists, check the following: • The error might be caused by a network connectivity problem, such as a bad interface cable, a bad USB port, or an invalid network configuration setting. • The error might be caused by the print job, due to an invalid print driver, a problem with the software application, or a problem with the file being printed. • Upgrading the product firmware might help resolve the error. See the product user guide for more information. When a 49 error occurs, the user sees a 49.XXXX message on the control panel (where XXXX is replaced by a combination of letters and numbers). A 49 error might happen at any time for multiple reasons. Although some types of 49 errors can be caused by hardware failures, it is more common for 49 errors to be caused by printing a specific document or performing some task on the product. 49 errors most often occur when a product is asked to perform an action that the product firmware is not capable of and might not have been designed to comply with, such as: • Printing files with unsupported programming commands • A unique combination of user environment and user interactions with the product • Interfacing with a third-party solution that was not designed to work with the product • Specific timing, network traffic, or concurrent processing of jobs Each of these interactions could cause the product firmware to initiate an action that the product cannot accomplish. In situations like this, the product might present the error if it has no other option. When these errors occur, the only way to recover is to turn the product`s power off and back on. NOTE: LaserJet formatter PCAs are rarely the root cause of 49 service errors. Please do not replace the formatter or flash unless troubleshooting has identified the formatter as the root cause. If the error persists, continue troubleshooting with the flowcharts for either Intermittent or Persistent 49 error troubleshooting (whichever is appropriate) in document c03122817, gHP LaserJet FutureSmart Devices - 49 Error Troubleshooting (Persistent and Intermittent). |
Error code: | 50.10X.YZ |
Display: | 50.WX.YZ Fuser error To continue, turn off then on |
Description: | The fuser has experienced an error. W = fuser error code, X = fuser mode, Y = previous printer sleep state, Z = next printer sleep state Low fuser temperature 2 |
Remedy: | 1. Remove and then reseat the fuser. Make sure there is no residual paper in the fuser. Make sure the device is not located in front of a vent or window where cool air may interfere with the ability of the fuser to heat up. 2. Check the product power source. Make sure the power source meets product requirements. Make sure this is the only device using the circuit. 3. Replace the fuser. 4. Check the connector (J50) between the fuser and the product. If it is damaged, replace the fuser. 5. If this product has been previously serviced, check the connector (J50) on the DC controller PCA. |
Error code: | 50.11X.YZ |
Display: | 50.WX.YZ Fuser error To continue, turn off then on |
Description: | The fuser has experienced an error. W = fuser error code, X = fuser mode, Y = previous printer sleep state, Z = next printer sleep state High fuser temperature 2 |
Remedy: | 1. Remove and then reseat the fuser. Make sure there is no residual paper in the fuser. Make sure the device is not located in front of a vent or window where cool air may interfere with the ability of the fuser to heat up. 2. Check the product power source. Make sure the power source meets product requirements. Make sure this is the only device using the circuit. 3. Replace the fuser. 4. Check the connector (J50) between the fuser and the product. If it is damaged, replace the fuser. 5. If this product has been previously serviced, check the connector (J50) on the DC controller PCA. |
Error code: | 50.12X.YZ |
Display: | 50.WX.YZ Fuser error To continue, turn off then on |
Description: | The fuser has experienced an error. W = fuser error code, X = fuser mode, Y = previous printer sleep state, Z = next printer sleep state Fuser pressure-release mechanism failure |
Remedy: | 1. Remove and then reseat the fuser. Make sure there is no residual paper in the fuser. 2. Check the fuser pressure-release sensor flag. If it is damaged, replace the fuser. 3. Use the sensor test in the Manual sensor test to verify that the fuser pressure-release sensor (PS7) is properly functioning. If it is not, replace the fuser. 4. Use the fuser pressure-release drive test in the component test to verify that the fuser motor (M2) is properly functioning. If it is not, replace the fuser motor (M2). 5. If the error persists, replace the fuser. 6. If this product has been previously serviced, check the connector (J117; J123) on the DC controller PCA. |
Error code: | 50.13X.YZ |
Display: | 50.WX.YZ Fuser error To continue, turn off then on |
Description: | The fuser has experienced an error. W = fuser error code, X = fuser mode, Y = previous printer sleep state, Z = next printer sleep state Low fuser temperature 3 |
Remedy: | 1. Remove and then reseat the fuser. Remove any residual paper in the product. 2. Check the paper type setting using the product menus and in the printer driver. Making sure that they match and are correct for the type of media being used. 3. If this product has been previously serviced, check the connector (J50) on the DC controller PCA. 4. If the error persists, replace the fuser. |
Error code: | 50.14X.YZ |
Display: | 50.WX.YZ Fuser error To continue, turn off then on |
Description: | The fuser has experienced an error. W = fuser error code, X = fuser mode, Y = previous printer sleep state, Z = next printer sleep state High fuser temperature 3 |
Remedy: | 1. Remove and then reseat the fuser. Remove any residual paper in the product. 2. Check the paper type setting using the product menus and in the printer driver. Making sure that they match and are correct for the type of media being used. 3. If this product has been previously serviced, check the connector (J50) on the DC controller PCA. 4. If the error persists, replace the fuser. |
Error code: | 50.2X.YZ |
Display: | 50.2X.YZ Fuser Error |
Description: | Fuser warm up failure. X = fuser mode, Y = previous printer sleep state, Z = next printer sleep state |
Remedy: | 1. Turn printer power off and then back on again. 2. If the error returns, unplug the device from any power-strips or uninterrupted power supplies and plug directly in to a wall socket. 3. If error returns, power off the unit and wait till fuser has cooled. 4. Remove the fuser and check fuser for damage or obstructions. Reinstall or replace fuser as needed. 5. Check the connector (J132 and J152) between the fuser and the DC controller PCA. 6. If the error persists, replace the fuser and then replace the fuser power supply assmebly if needed or if the fuser has already been replaced. 7. If issue persists, elevate the issue for possible printer replacement. |
Error code: | 50.3X.YZ |
Display: | 50.3X.YZ Fuser Error |
Description: | High Fuser temperature. X = fuser mode, Y = previous printer sleep state, Z = next printer sleep state |
Remedy: | 1. Reinstall the fuser. Check the connector (J128) between the fuser and the printer. If it is damaged, replace the fuser. 2. Check the connector (J132 and J152) on the DC controller PCA. 3. Replace the fuser. 4. If the error persists, replace the fuser power supply assembly. 5. If issue persists, elevate the issue for possible printer replacement. |
Error code: | 50.4X.YZ |
Display: | 50.4X.YZ Fuser Error |
Description: | Drive circuit fault. X = fuser mode, Y = previous printer sleep state, Z = next printer sleep state |
Remedy: | 1. Check the power source. Make sure the power source meets printer requirements. NOTE: If the power source does not meet the power frequency requirement of 40 to 70Hz, the fuser temperature control does not work properly and causes this error. 2. Reconnect connectors (J132 and J152) on the DC controller PCA. 3. If the error persists, replace the fuser power supply assembly. 4. If issue persists, elevate the issue for possible printer replacement. |
Error code: | 50.6X.YZ |
Display: | 50.6X.YZ Fuser Error |
Description: | Fuser error. Fuser open error. X = fuser mode, Y = previous printer sleep state, Z = next printer sleep state |
Remedy: | 1. Ensure the media type and fuser mode are correctly set for the paper being used. 2. turn the printer off. remove the fuser. Check the connector (J128) between the fuser and the printer. If it is damaged, replace the fuser. 3. Reinstall the fuser and turn the printer back on. 4. Reconnect connectors (J132 and J152) on the DC controller PCA. 5. Replace the fuser. 6. If the error persists, replace the power supply unit. |
Error code: | 50.8X.YZ |
Display: | 50.WX.YZ Fuser error To continue turn off then on |
Description: | Low fuser temperature 2 The fuser has experienced an error. W = fuser error code, X = fuser mode, Y = previous printer sleep state, and Z = next printer sleep state. Fuser modes and sleep states are listed after all 50.WX.YZ troubleshooting. Fuser Modes • 0 = Photo Media 1, 2, 3 • 1 = Normal.Auto Sense • 2 = Normal • 3 = Light 1 • 4 = Heavy 1 • 5 = Heavy 2 • 6 = Heavy 3 • 7 = Glossy 1 • 8 = Glossy 2 • 9 = Glossy 3 • A = Glossy Film • B = Transparency • C = Label • D = Envelope 1 • E = Rough Sleep States • 0 = Printing • 1 = Standby level 1 (no temperature control) • 2 = Standby level 2 (high temperature control) • 3 = Standby level 3 (middle temperature control) • 4 = Standby level 2 (low temperature control) • 5 = Middle sleep • 6 = Deep sleep • F = Power off |
Remedy: | 1. Remove and reinstall the fuser. Make sure that it is seated correctly. 2. Make sure that there is no residual paper in the fuser. 3. Check the product power source. Make sure that the power source meets product requirements. Make sure that the product is the only device using the circuit. 4. Check the connector (J514) between the fuser and the printer. If it is damaged, replace the fuser connector assembly or fuser. 5. If the product has been serviced previously, check the connectors (J219 and J206) on the DC controller PCA and the connectors (J90 and J91) on the power line between the low voltage power supply assembly and the fuser. 6. If the issue persists, replace the fuser. 7. If the issue persists, replace the low voltage power supply assembly. |
Error code: | 51.00.20 |
Display: | 51.00.20 Laser Scanner Error - Laser malfunction Sens |
Description: | A printer laser scanner error occurred. |
Remedy: | 1. Reconnect the connector (J1) on the laser driver PCA and connector J209 on the DC controller PCA. 2. Reconnect the connector (J151) on the laser scanner assembly and connector J234 on the DC controller PCA. 3. Reconnect the intermediate connector (J23) of the laser scanner. 4. If the error persists, replace the laser/scanner. 5. If the error persists, replace the upper cable guide assembly. 6. If the error persists, replace the DC controller. |
Error code: | 51.00.21 |
Display: | 51.00.YY Error |
Description: | Laser/scanner error YY = 20 or 21 Cyan/black laser/scanner error (C/K) YY = 22 or 23 Yellow/magenta laser/scanner error (Y/M)tate |
Remedy: | 1. Check the connector (J501) on the laser/scanner driver PCA and the connector (J111) on the DC controller PCA. 2. If the error persists, replace the C/K laser/scanner. |
Error code: | 51.00.22 |
Display: | 51.00.YY Error |
Description: | Laser/scanner error YY = 20 or 21 Cyan/black laser/scanner error (C/K) YY = 22 or 23 Yellow/magenta laser/scanner error (Y/M)tate |
Remedy: | 1. Check the connector (J501) on the laser/scanner driver PCA and the connector (J110) on the DC controller PCA. 2. If the error persists, replace the Y/M laser/scanner. |
Error code: | 51.00.23 |
Display: | 51.00.YY Error |
Description: | Laser/scanner error YY = 20 or 21 Cyan/black laser/scanner error (C/K) YY = 22 or 23 Yellow/magenta laser/scanner error (Y/M)tate |
Remedy: | 1. Check the connector (J501) on the laser/scanner driver PCA and the connector (J110) on the DC controller PCA. 2. If the error persists, replace the Y/M laser/scanner. |
Error code: | 52.00.04 |
Display: | 52.00.XX To continue, turn off then on |
Description: | Laser/scanner motor startup error XX = 04 or 05 laser/scanner motor startup error XX = 05 Laser/scanner rotation error/M |
Remedy: | 1. Check the connector (J501) on the laser/scanner driver PCA and the connector (J106) on the DC controller PCA. 2. If the error persists, replace the approriate laser/scanner. |
Error code: | 52.00.05 |
Display: | 52.00.XX To continue, turn off then on |
Description: | Laser/scanner motor startup error XX = 04 or 05 laser/scanner motor startup error XX = 05 Laser/scanner rotation error/M |
Remedy: | 1. Check the connector (J50-Y/K or J503-C/M) on the laser/scanner driver PCA and the connectors (J106; J110-C/K or J111-C/M) on the DC controller PCA. 2. If the error persists, replace the appropriate laser/scanner. |
Error code: | 54.00.03 |
Display: | 54.00.03 (EVENT LOG ONLY) |
Description: | Environmental sensor abnormality warning |
Remedy: | 1. Turn the product off, and then on. 2. If the environment sensor has been removed or replaced, check the connector from tray 1 to the environment sensor and the connector (J223) on the DC controller PCA. 3. If the error persists, replace the environment sensor assembly. 4. If the error persists, replace the right door assembly. |
Error code: | 54.00.06 |
Display: | 54.XX.YY Error |
Description: | A sensor error has occurred Registration density sensor failure |
Remedy: | 1. Open and close the right door (or turn on and then off the power switch) to perform the color plane registration. 2. If the error persists, replace the registration density sensor assembly. |
Error code: | 54.00.14 |
Display: | 54.XX.YY Error |
Description: | A sensor error has occurred Registration density sensor failure |
Remedy: | 1. Open and close the right door (or turn on and then off the power switch) to perform the color plane registration. 2. If the error persists, replace the registration density sensor assembly. |
Error code: | 54.00.19 |
Display: | 54.XX.YY Error |
Description: | A sensor error has occurred Registration density sensor failure |
Remedy: | 1. Open and close the right door (or turn on and then off the power switch) to perform the color plane registration. 2. If the error persists, replace the registration density sensor assembly. |
Error code: | 54.01.05 |
Display: | 54.XX.YY Error |
Description: | A sensor error has occurred Media sensor is out of calibration range |
Remedy: | 1. Turn the product off, and then clean the media sensor with a lint-free cloth. Turn the product on. 2. If the error persists, replace the paper pickup assembly. |
Error code: | 54.06.21 |
Display: | 54.06.21 error |
Description: | A sensor error has occurred. Primary laser/scanner beam detect abnormality. |
Remedy: | 1. Turn the printer off, and then on. 2. If the printer has had parts removed or replace, check the connector (J161 and J162) on the DC controller PCA. 3. If the error persists, replace the laser/scanner assembly. |
Error code: | 54.0X.0B |
Display: | 54.XX.YY Error |
Description: | A sensor error has occurred Density sensor out of range error or Dhalf calibration failure X = 0 black, X = 1 cyan, X = 2 magenta, X = 3 yellow |
Remedy: | 1. Check the supplies status page to make sure the toner cartridges are not past their useful life. 2. Check the ITB for damage. 3. Make sure the CPR sensor is not contaminated with toner or paper dust. Clean the sensor with compressed air and soft brush. 4. If error persists, replace the registration sensor assembly. |
Error code: | 54.0X.0C |
Display: | 54.XX.YY Error |
Description: | A sensor error has occurred Density sensor out of range error or Dhalf calibration failure X = 0 black, X = 1 cyan, X = 2 magenta, X = 3 yellow |
Remedy: | 1. Check the supplies status page to make sure the toner cartridges are not past their useful life. 2. Check the ITB for damage. 3. Make sure the CPR sensor is not contaminated with toner or paper dust. Clean the sensor with compressed air and soft brush. 4. If error persists, replace the registration sensor assembly. |
Error code: | 54.0X.0D |
Display: | 54.XX.YY Error |
Description: | A sensor error has occurred Optical memory element abnormal or CPR sensor out of range X = 0 black, X = 1 cyan, X = 2 magenta, X = 3 yellow |
Remedy: | 1. Check the supplies status page to make sure the toner cartridges are not past their useful life. 2. Check the ITB for damage. 3. Make sure the CPR sensor is not contaminated with toner or paper dust. Clean the sensor with compressed air and soft brush. 4. If error persists, replace the registration sensor assembly. |
Error code: | 54.0X.0E |
Display: | 54.XX.YY Error |
Description: | A sensor error has occurred Optical memory element abnormal or CPR sensor out of range X = 0 black, X = 1 cyan, X = 2 magenta, X = 3 yellow |
Remedy: | 1. Check the supplies status page to make sure the toner cartridges are not past their useful life. 2. Check the ITB for damage. 3. Make sure the CPR sensor is not contaminated with toner or paper dust. Clean the sensor with compressed air and soft brush. 4. If error persists, replace the registration sensor assembly. |
Error code: | 55.00.01 |
Display: | 55.00.01, 55.00.03 or 55.00.04 DC Controller Error |
Description: | The communication link between the formatter and DC controller was lost. • 55.00.01.DC controller memory error. • 55.00.03-DC controller no engine response • 55.00.04-DC controller communications time out. |
Remedy: | Turn the product off and then on. Verify that the all connectors on the DC controller are seated correctly. If the error persists, replace the DC controller. |
Error code: | 55.00.02 |
Display: | 55.00.YY DC controller error To continue, turn off then on |
Description: | DC controller PCA error DC controller no engine response |
Remedy: | Turn the product off, and then on. If the error persists, replace the DC controller PCA. |
Error code: | 55.00.07 |
Display: | 55.00.YY DC controller error To continue, turn off then on |
Description: | DC controller PCA error DC controller communications timeout |
Remedy: | Turn the product off, and then on. If the error persists, replace the DC controller PCA. |
Error code: | 55.01.06 |
Display: | 55.01.06 |
Description: | NVRAM memory data error warning DC controller PCA error occurred. The engine is not communicating with the formatter. The communication link between the formatter and the DC controller was lost. This can occur due to a timing error or intermittent connection loss between the formatter and the DC controller. |
Remedy: | 1. Turn the product off, and then on. 2. Check the life remaining on the maintenance kit. 3. Reseat the formatter, DIMMs, and EIO cards. 4. If the error persists, replace the DC controller PCA. 5. If the error persists, replace the formatter. |
Error code: | 55.02.06 |
Display: | 55.02.06 |
Description: | NVRAM memory access error warning DC controller PCA error occurred. The engine is not communicating with the formatter. The communication link between the formatter and the DC controller was lost. This can occur due to a timing error or intermittent connection loss between the formatter and the DC controller. |
Remedy: | 1. Turn the product off, and then on. 2. Check the life remaining on the maintenance kit. 3. Reseat the formatter, DIMMs, and EIO cards. 4. If the error persists, replace the DC controller PCA. 5. If the error persists, replace the formatter. |
Error code: | 56.00.YY |
Display: | 56.00.YY Error |
Description: | Optional paper trays communication error occurred. |
Remedy: | 1. Turn the product off, and then on. 2. If the error persists, reseat the optional paper trays (HCO and HCI).. 3. Check the input connectors for damage. If a connector is damaged, replace the connector. |
Error code: | 57.00.03 |
Display: | 57.00.03 Error To continue turn off then on |
Description: | Rear delivery fan (FM-3B) malfunction (M830 only) |
Remedy: | 1. Turn the product off, and then on. 2. Listen for fan noise at the left side, upper back of the product. 3. If no noise is heard, make sure that the connectors (J1453B and J1451B) on the intermediate PCA and connector (J205) on the DC controller are connected correctly and undamaged. 4. If the error persists, replace the delivery fan assembly.. |
Error code: | 57.00.04 |
Display: | 57.00.04 Error To continue turn off then on |
Description: | Front delivery fan (FM-4B) malfunction (M830 only) |
Remedy: | 1. Turn the product off, and then on. 2. Listen for fan noise at the left side, upper front of the product. 3. If no noise is heard, make sure that the connectors (J1455B and J1451B) on the intermediate PCA, relay connector (J1451), and connector (J205) on the DC controller board are connected correctly and undamaged. 4. If the error persists, replace the delivery fan assembly. |
Error code: | 57.00.05 |
Display: | 57.00.05 Error To continue turn off then on |
Description: | Cartridge fan (FM-5) malfunction |
Remedy: | 1. Turn the product off, and then on. 2. Listen for fan noise at the right side, upper back of the product just above Tray 1. 3. If no noise is heard, make sure that the connector (J225) on the DC controller PCA is connected correctly and undamaged. 4. If the error persists, replace the cartridge fan assembly (FM5) |
Error code: | 58.00.04 |
Display: | 58.00.04 Error |
Description: | The printer experienced a low voltage power supply unit malfunction. |
Remedy: | 1. Turn the printer off and then back on. NOTE: This error might be caused by source power related issues. Determine if the area where the printer is located has experienced brown outs or is subject to power quality issues. 2. Ensure printer is plug into dedicated power outlet. 3. If error persists, replace the power supply unit. |
Error code: | 59.00.04 |
Display: | 59.00.YY Error To continue, turn off then on |
Description: | Printing error |
Remedy: | Fuser motor (M2) start up error or fuser motor (M2) rotational error---preasure roller, delivery roller, fuser pressurization, primary transfer roller disengaement 1. Use the fuser motor (M2) drive test in the component test to verify that the fuser motor is properly functioning. If it is not, replace the fuser motor assembly. 2. If the product has been serviced, check the connector (J15) on the fuser motor and the connector (J17) on the DC controller PCA. |
Error code: | 59.00.05 |
Display: | 59.00.YY Error To continue, turn off then on |
Description: | Printing error |
Remedy: | Fuser motor (M2) start up error or fuser motor (M2) rotational error---preasure roller, delivery roller, fuser pressurization, primary transfer roller disengaement 1. Use the fuser motor (M2) drive test in the component test to verify that the fuser motor is properly functioning. If it is not, replace the fuser motor assembly. 2. If the product has been serviced, check the connector (J15) on the fuser motor and the connector (J17) on the DC controller PCA. |
Error code: | 59.05.06 |
Display: | 59.05.XX |
Description: | A drum startup or drum rotational error has occurred. XX = 06 Black drum startup error (M3); XX = 07 Black drum rotational error (M3) XX = 08 Yellow drum startup error (M1); XX = 09 Yellow drum rotational error (M1) XX = 10 Magenta drum startup error (M1); XX = 11 Magenta drum rotational error (M1) XX = 12 Cyan drum startup error; XX = 13 Cyan drum rotational error (M1) XX = B0 Residual toner feed motor error (M12) |
Remedy: | 1. Turn the product off, and then on. 2. Check the connector (J121) on the DC controller PCA. 3. Use the motor drive test in the componet test to verify that the motor is properly functioning. If it is not, replace the drum motor (M3). |
Error code: | 59.05.07 |
Display: | 59.05.XX |
Description: | A drum startup or drum rotational error has occurred. XX = 06 Black drum startup error (M3); XX = 07 Black drum rotational error (M3) XX = 08 Yellow drum startup error (M1); XX = 09 Yellow drum rotational error (M1) XX = 10 Magenta drum startup error (M1); XX = 11 Magenta drum rotational error (M1) XX = 12 Cyan drum startup error; XX = 13 Cyan drum rotational error (M1) XX = B0 Residual toner feed motor error (M12) |
Remedy: | 1. Turn the product off, and then on. 2. Check the connector (J121) on the DC controller PCA. 3. Use the motor drive test in the componet test to verify that the motor is properly functioning. If it is not, replace the drum motor (M3). |
Error code: | 59.05.08 |
Display: | 59.05.XX |
Description: | A drum startup or drum rotational error has occurred. XX = 06 Black drum startup error (M3); XX = 07 Black drum rotational error (M3) XX = 08 Yellow drum startup error (M1); XX = 09 Yellow drum rotational error (M1) XX = 10 Magenta drum startup error (M1); XX = 11 Magenta drum rotational error (M1) XX = 12 Cyan drum startup error; XX = 13 Cyan drum rotational error (M1) XX = B0 Residual toner feed motor error (M12) |
Remedy: | 1. Turn the product off, and then on. 2. Check the connector (J120) on the DC controller PCA. 3. Use the motor drive test in the componet test to verify that the motor is properly functioning. If it is not, replace the drum motor (M1). |
Error code: | 59.05.09 |
Display: | 59.05.XX |
Description: | A drum startup or drum rotational error has occurred. XX = 06 Black drum startup error (M3); XX = 07 Black drum rotational error (M3) XX = 08 Yellow drum startup error (M1); XX = 09 Yellow drum rotational error (M1) XX = 10 Magenta drum startup error (M1); XX = 11 Magenta drum rotational error (M1) XX = 12 Cyan drum startup error; XX = 13 Cyan drum rotational error (M1) XX = B0 Residual toner feed motor error (M12) |
Remedy: | 1. Turn the product off, and then on. 2. Check the connector (J120) on the DC controller PCA. 3. Use the motor drive test in the componet test to verify that the motor is properly functioning. If it is not, replace the drum motor (M1). |
Error code: | 59.05.10 |
Display: | 59.05.XX |
Description: | A drum startup or drum rotational error has occurred. XX = 06 Black drum startup error (M3); XX = 07 Black drum rotational error (M3) XX = 08 Yellow drum startup error (M1); XX = 09 Yellow drum rotational error (M1) XX = 10 Magenta drum startup error (M1); XX = 11 Magenta drum rotational error (M1) XX = 12 Cyan drum startup error; XX = 13 Cyan drum rotational error (M1) XX = B0 Residual toner feed motor error (M12) |
Remedy: | 1. Turn the product off, and then on. 2. Check the connector (J120) on the DC controller PCA. 3. Use the motor drive test in the componet test to verify that the motor is properly functioning. If it is not, replace the drum motor (M1). |
Error code: | 59.05.11 |
Display: | 59.05.XX |
Description: | A drum startup or drum rotational error has occurred. XX = 06 Black drum startup error (M3); XX = 07 Black drum rotational error (M3) XX = 08 Yellow drum startup error (M1); XX = 09 Yellow drum rotational error (M1) XX = 10 Magenta drum startup error (M1); XX = 11 Magenta drum rotational error (M1) XX = 12 Cyan drum startup error; XX = 13 Cyan drum rotational error (M1) XX = B0 Residual toner feed motor error (M12) |
Remedy: | 1. Turn the product off, and then on. 2. Check the connector (J120) on the DC controller PCA. 3. Use the motor drive test in the componet test to verify that the motor is properly functioning. If it is not, replace the drum motor (M1). |
Error code: | 59.05.12 |
Display: | 59.05.XX |
Description: | A drum startup or drum rotational error has occurred. XX = 06 Black drum startup error (M3); XX = 07 Black drum rotational error (M3) XX = 08 Yellow drum startup error (M1); XX = 09 Yellow drum rotational error (M1) XX = 10 Magenta drum startup error (M1); XX = 11 Magenta drum rotational error (M1) XX = 12 Cyan drum startup error; XX = 13 Cyan drum rotational error (M1) XX = B0 Residual toner feed motor error (M12) |
Remedy: | 1. Turn the product off, and then on. 2. Check the connector (J120) on the DC controller PCA. 3. Use the motor drive test in the componet test to verify that the motor is properly functioning. If it is not, replace the developing disengagement motor (M10). 4. Use the Manual sensor test to verify that the ITB alienation sensor (SR17) is properly functioning. If it is not, replace the ITB alienation sensor (SR17). |
Error code: | 59.05.13 |
Display: | 59.05.XX |
Description: | A drum startup or drum rotational error has occurred. XX = 06 Black drum startup error (M3); XX = 07 Black drum rotational error (M3) XX = 08 Yellow drum startup error (M1); XX = 09 Yellow drum rotational error (M1) XX = 10 Magenta drum startup error (M1); XX = 11 Magenta drum rotational error (M1) XX = 12 Cyan drum startup error; XX = 13 Cyan drum rotational error (M1) XX = B0 Residual toner feed motor error (M12) |
Remedy: | 1. Turn the product off, and then on. 2. Check the connector (J120) on the DC controller PCA. 3. Use the motor drive test in the componet test to verify that the motor is properly functioning. If it is not, replace the developing disengagement motor (M10). 4. Use the Manual sensor test to verify that the ITB alienation sensor (SR17) is properly functioning. If it is not, replace the ITB alienation sensor (SR17). |
Error code: | 59.05.B0 |
Display: | 59.05.XX |
Description: | A drum startup or drum rotational error has occurred. XX = 06 Black drum startup error (M3); XX = 07 Black drum rotational error (M3) XX = 08 Yellow drum startup error (M1); XX = 09 Yellow drum rotational error (M1) XX = 10 Magenta drum startup error (M1); XX = 11 Magenta drum rotational error (M1) XX = 12 Cyan drum startup error; XX = 13 Cyan drum rotational error (M1) XX = B0 Residual toner feed motor error (M12) |
Remedy: | 1. Turn the product off, and then on. 2. Check the connector (J89) on the residual feed motor (M12), intermediate connectors (J75 and J77), and the connector (J137) on the DC controller. 3. Use the motor drive test in the componet test to verify that the motor is properly functioning. If it is not, replace the developing disengagement motor (M12). 4. Use the Manual sensor test to verify that the ITB alienation sensor (SR17) is properly functioning. If it is not, replace the ITB alienation sensor (SR17). |
Error code: | 60.00.11 |
Display: | 60.00.0Y Tray <Y> lifting error |
Description: | Tray lift motors error Lifter motor failure (M7) |
Remedy: | 1. Turn the product off, and then on. 2. Check the connector (J141) on the DC controller PCA. 3. Check the connector (J78) on the lifter motor (M7). 4. Use the Cassette lifter sensor sensor (SR9) test in the Tray/Bin manual sensor test to verify that the sensor is properly functioning. If it is not, replace the lifter drive assembly. 5. If the error persists, replace the lifter drive assembly. |
Error code: | 61.00.01 |
Display: | 61.00.01 |
Description: | Print Engine Error 61.00.02 Print Engine Error 61.00.03 Print Engine Error The print engine has encountered an error. The payload data will be included which will be with the error code, and string. Service_Station_Cap_Home_Long (6100000D) Paper_Load_Tray1_Pick_Motor (6100002D) Paper_Load_Pick_Tire_Index_Sensor (6100002E) Service_Station_Cap_Home_Short (6100000E) SS_Restricted_Movement_Error (61000011) Lift_Restricted_Movement_Error (61000012) Carriage_Restricted_Movement_Error (61000013) Service_Move_To_Tranny_State (610000C8) DPU_Printbar_Crash_Into_Service_Station (610000D3) DPU_Service_Station_Under_Print_Bar (610000D4) Printbar_Clutch_Slippage (61000035) Service_Station_Pen_Too_Cold (6100000B) Service_Station_Home_Failure (6100000C) Service_Carriage_Home_Invalid (610000C9) Pen_Start_Up_Spits_Already_Done (6100004E) |
Remedy: | 1. Turn the power off on the product by pressing the power button and holding it for more than 3 seconds.2. Unplug power cord from back of product and wait 30 seconds.3. Plug power cord back into product. 4. Turn the power on to the product using power button. 5. If the error condition is cleared then the issue is resolved, if not continue to step 6. 6. Repeat steps 1 & 2. 7. Remove the formatter, check formatter thoroughly for any loose connections and reseat them, then reinstall the formatter. 8. Repeat steps 3 & 4. 9. If the error condition is cleared then the issue is resolved, if issue is not resolved replace the Mech Kit. NOTE: It is critical to either print the event log after power cycle clears issue, or access the event log through EWS and capture the 8 character fail code value corresponding to the 61.00.0X and log it into the case. Look for the last 61.00.0x error that occurred which also has the 8 character value under the text . This value is critical in HP understanding the failure and debugging potential field issues. |
Error code: | 62.00.00 |
Display: | 62.00.00 To continue turn off the on. |
Description: | Internal system failure. |
Remedy: | Turn the printer off, and then on. If the error persists, reload the firmware. If the error still persists, perform a firmware upgrade. If the firmware upgrade does not resolve the problem, replace the hard disk. |
Error code: | 70.00.00 |
Display: | 70.00.00 Error To continue turn off then on |
Description: | DC controller failure. |
Remedy: | 1. Turn the printer off, and then on.2. If the error persists, replace the DC controller. |
Error code: | 81.01.00 |
Display: | 81.0X.YY Embedded JetDirect error |
Description: | Embedded HP JetDirect print server critical error EIO Networking Event |
Remedy: | Turn the product off, and then on. If the error persists, replace the formatter. |
Error code: | 81.02.00 |
Display: | 81.0X.YY Embedded JetDirect error |
Description: | Embedded HP JetDirect print server critical error Wireless Networking Event: <UVWXYZ> |
Remedy: | Turn the product off, and then on. If the error persists, replace the formatter. |
Error code: | 81.03.00 |
Display: | 81.0X.YY Embedded JetDirect error |
Description: | Embedded HP JetDirect print server critical error Access Point Wireless Networking Event: <UVWXYZ> |
Remedy: | Turn the product off, and then on. If the error persists, replace the formatter. |
Error code: | 81.04.00 |
Display: | 81.0X.YY Embedded JetDirect error |
Description: | Embedded HP JetDirect print server critical error JetDirect Inside Networking Event: <UVWXYZ> |
Remedy: | Turn the product off, and then on. If the error persists, replace the formatter. |
Error code: | 81.06.00 |
Display: | 81.0X.YY Embedded JetDirect error |
Description: | Embedded HP JetDirect print server critical error Internal EIO Networking Event: <UVWXYZ> |
Remedy: | Turn the product off, and then on. If the error persists, replace the formatter. |
Error code: | 81.07.00 |
Display: | 81.0X.YY Embedded JetDirect error |
Description: | Embedded HP JetDirect print server critical error Internal Wireless Networking Event: <UVWXYZ> |
Remedy: | Turn the product off, and then on. If the error persists, replace the formatter. |
Error code: | 81.08.00 |
Display: | 81.0X.YY Embedded JetDirect error |
Description: | Embedded HP JetDirect print server critical error Internal Access Point Wireless Networking Event: <UVWXYZ> |
Remedy: | Turn the product off, and then on. If the error persists, replace the formatter. |
Error code: | 81.09.00 |
Display: | 81.0X.YY Embedded JetDirect error |
Description: | Embedded HP JetDirect print server critical error Internal JetDirect Inside Networking Event: <UVWXYZ> |
Remedy: | Turn the product off, and then on. If the error persists, replace the formatter. |
Error code: | 98.00.01 |
Display: | 98.00.01 Corrupt data in firmware volume |
Description: | Data corrupt has occurred in the firmware volume. |
Remedy: | 1. Turn the product off, and then on. 2. Use the Clean Disk item in the Preboot menu. 3. Reload the firmware. 98.00.02 Corrupt data in the solutions volume |
Error code: | 98.00.02 |
Display: | 98.00.02 Corrupt data in the solutions volume |
Description: | Corrupt data in the solutions volume Data corruption has occurred in the solutions volume. |
Remedy: | 1. Turn the product off, and then on.2. Use the Clean Disk item in the Preboot menu.3. Reload the firmware. |
Error code: | 98.00.03 |
Display: | 98.00.03 Corrupt data in the configuration volume |
Description: | Corrupt data in the configuration volume Data corrupt has occurred in the configuration volume. |
Remedy: | 1. Turn the product off, and then on.2. Download the firmware again, and then attempt the upgrade again.3. Use the Clean Disk item in the Preboot menu.4. Reload the firmware. |
Error code: | 98.00.04 |
Display: | 98.00.04 Corrupt data in the job data volume |
Description: | Corrupt data in the job data volume Data corrupt has occurred in the job data volume. |
Remedy: | 1. Turn the product off, and then on.2. Rerun the file erase function. |
Error code: | 99.00.01 |
Display: | 99.00.01 Upgrade not performed file is corrupt |
Description: | Upgrade not performed file is corrupt A remote firmware upgrade (RFU) was not performed. This is a CRC error in the firmware image (bad image). |
Remedy: | Download the RFU file, and then attempt the upgrade again. |
Error code: | 99.00.02 |
Display: | 99.00.02 Upgrade not performed time-out during receive |
Description: | Upgrade not performed timeout during receive A remote firmware upgrade (RFU) was not performed. The issue is an I/O timeout when reading the header number and size. It indicates a problem with the network environment, not the product. |
Remedy: | The most common cause is an issue with the network environment. Make sure that there is a good network connection to the product, and then attempt the firmware upgrade again, or upgrade using the USB walk-up port. |
Error code: | 99.00.03 |
Display: | 99.00.03 Upgrade not performed error writing to disk |
Description: | Upgrade not performed error writing to disk A remote firmware upgrade (RFU) was not performed. This is a disk error. It might indicate a problem or a hard disk failure. It might be necessary to check the connection to the hard disk or replace the hard disk. |
Remedy: | 1. Download the RFU file, and then attempt the upgrade again.2. If the error persists, run the Clean Disk process from the Preboot menu. You will need to download the firmware from the Preboot menu.3. If the error persists, replace the hard disk. |
Error code: | 99.00.04 |
Display: | 99.00.04 Upgrade not performed time-out during receive |
Description: | Upgrade not performed timeout during receive A remote firmware upgrade (RFU) was not performed. The issue is an I/O timeout when reading the header. |
Remedy: | The most common cause is an issue with the network environment. Make sure that there is a good network connection to the product, and then attempt the firmware upgrade again, or upgrade using the USB walk-up port. |
Error code: | 99.00.05 |
Display: | 99.00.05 Upgrade not performed time-out during receive |
Description: | Upgrade not performed timeout during receive A remote firmware upgrade (RFU) was not performed. The issue is an I/O timeout when reading image data. |
Remedy: | The most common cause is an issue with the network environment. Make sure that there is a good network connection to the product, and then attempt the firmware upgrade again, or upgrade using the USB walk-up port. |
Error code: | 99.00.06 |
Display: | 99.00.06 Upgrade not performed error reading upgrade |
Description: | Upgrade not performed error reading upgrade A remote firmware upgrade (RFU) was not performed. The issue is an unexpected read error when reading the header number and size. |
Remedy: | 1. Download the RFU file, and then attempt the upgrade again.2. If the error persists, replace the hard disk. |
Error code: | 99.00.07 |
Display: | 99.00.07 Upgrade not performed error reading upgrade |
Description: | Upgrade not performed error reading upgrade A remote firmware upgrade (RFU) was not performed. The issue is an unexpected read error when reading the rest of the header. |
Remedy: | 1. Download the RFU file, and then attempt the upgrade again.2. If the error persists, replace the hard disk. |
Error code: | 99.00.08 |
Display: | 99.00.08 Upgrade not performed error reading upgrade |
Description: | Upgrade not performed error reading upgrade A remote firmware upgrade (RFU) was not performed. The issue is an unexpected read error when reading image data. |
Remedy: | 1. Download the RFU file, and then attempt the upgrade again.2. If the error persists, replace the hard disk. |
Error code: | 99.00.09 |
Display: | 99.00.09 Upgrade canceled by user |
Description: | Upgrade canceled by user A remote firmware upgrade (RFU) was not performed. The RFU was canceled by the user. |
Remedy: | Resend the RFU. |
Error code: | 99.00.10 |
Display: | 99.00.10 Upgrade canceled by user |
Description: | Upgrade canceled by user A remote firmware upgrade (RFU) was not performed. The RFU was canceled by the user when reading the header number and size. |
Remedy: | Resend the RFU. |
Error code: | 99.00.11 |
Display: | 99.00.11 Upgrade canceled by user |
Description: | Upgrade canceled by user A remote firmware upgrade (RFU) was not performed. The RFU was canceled by the user when reading the rest of the header. |
Remedy: | Resend the RFU. |
Error code: | 99.00.12 |
Display: | 99.00.12 Upgrade not performed the file is invalid |
Description: | Upgrade not performed the file is invalid A remote firmware upgrade (RFU) was not performed. The header number is 1, but the header size does not match version 1 size. |
Remedy: | Download the RFU file again. Make sure that you download the file for the correct product model, and then resend the RFU. |
Error code: | 99.00.13 |
Display: | 99.00.13 Upgrade not performed the file is invalid |
Description: | Upgrade not performed the file is invalid A remote firmware upgrade (RFU) was not performed. The header number is 2, but the header size does not match version 2 size. |
Remedy: | Download the RFU file again. Make sure that you download the file for the correct product model, and then resend the RFU. |
Error code: | 99.00.14 |
Display: | 99.00.14 Upgrade not performed the file is invalid |
Description: | Upgrade not performed the file is invalid A remote firmware upgrade (RFU) was not performed. The file is invalid. |
Remedy: | Download the RFU file again. Make sure that you download the file for the correct product model, and then resend the RFU. |
Error code: | 99.00.20 |
Display: | 99.00.2X |
Description: | The bundle is not for this product |
Remedy: | Download the correct firmware file from HP website, and then resend the firmware upgrade. |
Error code: | 99.00.21 |
Display: | 99.00.2X |
Description: | The bundle is not signed with the correct signature, or the signature is invalid |
Remedy: | Download the correct firmware file from HP website, and then resend the firmware upgrade. |
Error code: | 99.00.22 |
Display: | 99.00.2X |
Description: | The bundle header version is not supported by this firmware |
Remedy: | Download the correct firmware file from HP website, and then resend the firmware upgrade. |
Error code: | 99.00.23 |
Display: | 99.00.2X |
Description: | The package header version is not supported by this firmware |
Remedy: | Download the correct firmware file from HP website, and then resend the firmware upgrade. |
Error code: | 99.00.24 |
Display: | 99.00.2X |
Description: | The format of the bundle is invalid |
Remedy: | Download the correct firmware file from HP website, and then resend the firmware upgrade. |
Error code: | 99.00.25 |
Display: | 99.00.2X |
Description: | The format of the package is invalid |
Remedy: | Download the correct firmware file from HP website, and then resend the firmware upgrade. |
Error code: | 99.00.26 |
Display: | 99.00.2X |
Description: | A CRC32 check did not pass |
Remedy: | Download the correct firmware file from HP website, and then resend the firmware upgrade. |
Error code: | 99.00.27 |
Display: | 99.00.2X |
Description: | An I/O error occurred while downloading the bundle |
Remedy: | Turn the product off, and then on again. Resend the firware upgrade. If the error persists, try the sending the upgrade by another method (USB or Embedded Web Server). |
Error code: | 99.09.60 |
Display: | 99.09.60 Unsupported disk |
Description: | Unsupported disk This is a Preboot menu error. The hard disk currently installed is not recognized or supported by the product. |
Remedy: | Install the correct hard disk for this product. |
Error code: | 99.09.61 |
Display: | 99.09.61 Unsupported disk |
Description: | Unsupported disk This is a Preboot menu error. The installed disk is installed in a product configured for an encrypted hard disk. |
Remedy: | Access the Preboot menu, and then select Lock Disk to lock the disk. |
Error code: | 99.09.62 |
Display: | 99.09.62 Unknown disk |
Description: | Unknown disk This error indicates that there is an encryption mismatch between the HDD and the formatter. This typically happens because an HDD was swapped into a device from another device. |
Remedy: | Install a new disk or use the Preboot menu unlock the disk. If a disk is to be reused in a different product, execute the Clean Disk procedure from the Preboot, and then reload the firmware and lock the disk. |
Error code: | 99.09.63 |
Display: | 99.09.63 Incorrect disk |
Description: | Incorrect disk This error indicates that the expected encrypted HDD is not present. This is expected behavior when installing a new HDD in a device where the previous HDD was encrypted. |
Remedy: | Follow the procedure to load firmware on a new hard disk, and then lock the disk to this product. |
Error code: | 99.09.64 |
Display: | 99.09.64 Disk Nonfunctiona |
Description: | Disk malfunction A fatal hard disk failure has occurred. |
Remedy: | Replace the hard disk. |
Error code: | 99.09.65 |
Display: | 99.09.65 Disk data error |
Description: | Disk data error Disk data corruption has occurred. |
Remedy: | Use the Clean Disk procedure from the Preboot menu, and then resend the RFU. |
Error code: | 99.09.66 |
Display: | 99.09.66 No boot device. |
Description: | No disk installed A disk drive is not installed in the product. |
Remedy: | 1. Install a compatible hard disk drive.2. If a compatible hard disk is installed, reseat the hard disk to make sure that it is connected correctly.3. If the error persists, replace the hard disk drive. |
Error code: | 99.09.67 |
Display: | 99.09.67 Disk is not bootable please download firmware |
Description: | Disk is not bootable please download firmware This is an error indicating that there is no firmware installed on the disk. This is usually the result of installing a new disk or performing a Clean Disk operation from the Preboot menu. |
Remedy: | 1. Press any button to continue to the main Preboot menu.2. Press the Help button to see the help text for the error.3. Select the Administration menu. NOTE: If there is a password assigned to the administrator, a prompt to enter the product displays. Enter the password to proceed. 4. Select the Download item, and then download the latest firmware. The user can now download a new firmware bundle to the product. |
Error code: | 99.XX.YY |
Display: | 99.XX.YY |
Description: | A message of this form indicates a firmware installation error. |
Remedy: | Reload the firmware. |
Название
HP Емкость отработанного тонера
HP 507A Тонер-картридж черный (5500 стр.)
HP 507X Тонер-картридж черный (11000 стр.)
HP 507Y Тонер-картридж черный (11400 стр.) - контрактный
HP 507A Тонер-картридж голубой (6000 стр.)
HP 507Y Тонер-картридж голубой (7800 стр.) - контрактный
HP 507A Тонер-картридж желтый (6000 стр.)
HP 507Y Тонер-картридж желтый (7800 стр.) - контрактный
HP 507A Тонер-картридж пурпурный (6000 стр.)
HP 507Y Тонер-картридж пурпурный (7800 стр.) - контрактный
HP Печь в сборе 220V