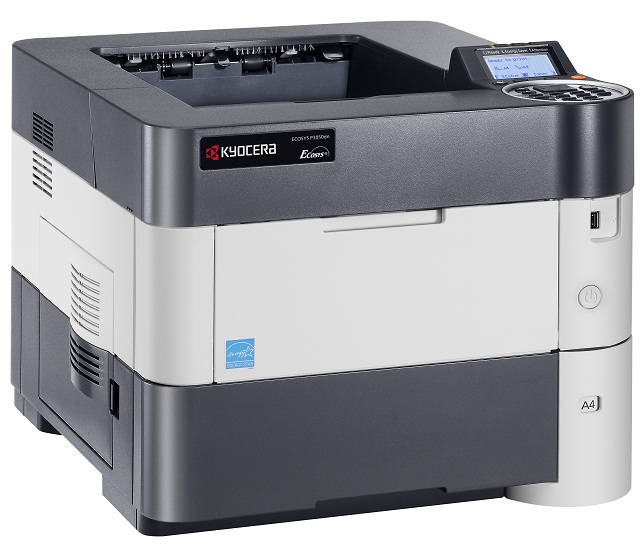
Kyocera ECOSYS P3050dn
Рейтинг
Актуальный
Тип устройства
Принтер
Технология печати
лазерная
Макс. формат
A4
Число страниц в месяц
200000
Скорость печати
A4
50
Цветность печати
черно-белая
Общие характеристики |
|
---|---|
Размещение |
настольный |
Макс. формат |
A4 |
Тип устройства |
Принтер |
Факс |
|
Печать фотографий |
|
Сканер |
|
Телефон |
|
Копир |
|
Область применения |
большой офис |
Число страниц в месяц |
200 000 |
Технология печати |
лазерная |
Тип |
лазерный/светодиодный |
Цветность печати |
|
Принтер |
|
Время разогрева |
20 |
Макс, ширина отпечатка |
297 |
Двусторонняя печать |
![]() |
Прямая печать |
![]() |
Печать без полей |
|
Система непрерывной подачи чернил |
|
Пигментные чернила |
|
Макс, длина отпечатка |
356 |
Макс, разрешение для ч/б печати |
|
По Y | 1 200 |
По X | 1 200 |
Скорость ч/б печати |
|
A4 | 50 |
Время выхода первого отпечатка |
|
Ч/б | 6,2 |
Сканер |
|
Стандарт TWAIN |
|
Стандарт WIA |
|
Отправка изображения по e-mail |
|
Слайд-адаптер |
|
Расходные материалы |
|
Количество картриджей |
1 |
Ресурс фотобарабана |
500 000 |
Ресурс ч/б картриджа/тонера |
12 500 |
Печать на: |
|
Глянцевой бумаге |
![]() |
Матовой бумаге |
![]() |
Карточках |
![]() |
Конвертах |
![]() |
Пленках |
![]() |
Этикетках |
![]() |
CD/DVD |
|
Фотобумаге |
|
Рулоне |
|
Плотность бумаги |
|
Максимальная | 220 |
Минимальная | 60 |
Факс |
|
Цветной |
|
Телефон |
|
Проводная трубка |
|
Беспроводная трубка |
|
Автоответчик |
|
Caller ID |
|
Стандарт DECT |
|
АОН |
|
Спикерфон |
|
Шрифты и языки управления |
|
Языки управления |
|
PostScript 3 |
![]() |
PostScript |
![]() |
PCL 5c |
![]() |
PCL 6 |
![]() |
![]() |
|
PostScript 2 |
|
Количество установленных шрифтов |
|
PCL | 93 |
PostScript | 93 |
Лотки |
|
Емкость лотка ручной подачи |
100 |
Подача бумаги |
|
Максимальная | 2 600 |
Стандартная | 600 |
Вывод бумаги |
|
Стандартный | 500 |
Финишер |
|
Сортер |
|
Брошюровщик |
|
Степлер |
|
Интерфейсы |
|
USB |
![]() |
Устройство для чтения карт памяти |
![]() |
Веб-интерфейс |
![]() |
Поддержка iOS |
![]() |
AirPrint |
![]() |
Ethernet (RJ-45) |
![]() |
RS-232 |
|
Инфракрасный порт |
|
LPT |
|
Bluetooth |
|
Wi-Fi |
|
FireWire (IEEE 1394) |
|
Количество слотов расширения |
1 |
Количество свободных слотов расширения |
1 |
Версия USB |
2,0 |
Поддержка карт памяти |
|
Secure Digital |
![]() |
Память/Процессор |
|
Макс, объем памяти |
2 560 |
Частота процессора |
1 200 |
Объем памяти |
512 |
Дополнительная информация |
|
Работа от аккумулятора |
|
Экран |
|
Поддержка ОС |
|
Linux |
![]() |
Mac OS |
![]() |
Windows |
![]() |
DOS |
|
Потребляемая мощность |
|
При работе | 636 |
В режиме ожидания | 10 |
Уровень шума |
|
При работе | 53,2 |
В режиме ожидания | 26,9 |
Габариты |
|
Ширина |
396 |
Вес |
15,5 |
Глубина |
421 |
Высота |
342 |
Модули
(Электронные компоненты)
Image Formation Section
PAPER FEED SECTION
FRAMES
DRIVE SECTION
COVERS
Exit Section
COVERS and LABELS
PAPER CASSETTE
PAPER FEED
CASSETTE ASSEMBLY
Developer Section
Fuser Section
FRAME L
Детали None
Деталь: | LASER SCANNER ASSY |
Парткод: | LK-3170 |
Цена: | 7 300 ₽ |
Деталь: | MC-3100 |
Парткод: | 302LV93010 |
Деталь: | PARTS SHEET DRUM CUSHION SET SP |
Парткод: | 302LV94460 |
Деталь: | STOPPER PROCESS |
Парткод: | 302LV02110 |
Деталь: | STOPPER PROCESS L |
Парткод: | 302LV02200 |
Деталь: | WT-3100 |
Парткод: | 302LV93020 |
Деталь: | PARTS TONER FULL DETECT ASSY SP |
Парткод: | 302LV94121 |
Деталь: | DK-3171 (J) |
Парткод: | 302T993080 |
Деталь: | DK-3172(U) |
Парткод: | 302T993070 |
Деталь: | DK-3170(E) |
Парткод: | 302T993060 |
Деталь: | DK-3174(AO) |
Парткод: | 302T993090 |
Деталь: | DK-3191 (J) |
Парткод: | 302T693050 |
Деталь: | DK-3192(U) |
Парткод: | 302T693040 |
Деталь: | DK-3190(E) |
Парткод: | 302T693030 |
Деталь: | DK-3194(AO) |
Парткод: | 302T693060 |
Деталь: | PARTS PWB ASSY DRUM CONNECT SP |
Парткод: | 302T694080 |
Деталь: | PARTS ROLLER REGIST LOW SP |
Парткод: | 302LV94170 |
Деталь: | PARTS ROLLER REGIST UP SP |
Парткод: | 302LV94180 |

Деталь: | BUSH TRANSFER R |
Парткод: | 302F924190 |
Цена: | 150 ₽ |
Деталь: | BUSH TRANSFER L |
Парткод: | 302LV24360 |

Деталь: | PARTS ROLLER TRANSFER SP |
Парткод: | 302LV94130 |
Цена: | 3 000 ₽ |
Деталь: | PARTS GUIDE PAPER CHUTE SP |
Парткод: | 302LV94261 |
Деталь: | ACTUATOR IMAGE |
Парткод: | 302LV24100 |
Деталь: | ACTUATOR REGIST |
Парткод: | 302L224030 |
Цена: | 80 ₽ |
Деталь: | PARTS ACTUATOR DU SET SP |
Парткод: | 302LV94540 |

Деталь: | PARTS HIGH VOLTAGE UNIT SP |
Парткод: | 302L294030 |
Цена: | 8 900 ₽ |

Деталь: | PARTS HIGH VOLTAGE UNIT SP |
Парткод: | 302LV94060 |
Цена: | 7 300 ₽ |
Деталь: | PARTS COVER MPF ASSY SP |
Парткод: | 302LV94041 |
Деталь: | ACTUATOR MPF |
Парткод: | 302LV08180 |
Цена: | 180 ₽ |
Деталь: | PARTS SENSOR OPT SP |
Парткод: | 303M894260 |

Деталь: | ROLLER M/P ASSY |
Парткод: | 302HS08260 |
Цена: | 700 ₽ |
Деталь: | ACTUATOR PE |
Парткод: | 302LV29090 |
Деталь: | ACTUATOR ENVELOPE |
Парткод: | 302LV24450 |

Деталь: | PULLEY FEED ASSY |
Парткод: | 302F906230 |
Цена: | 750 ₽ |
Деталь: | GEAR FEED Z26H |
Парткод: | 302F906030 |
Деталь: | GEAR FEED Z30H |
Парткод: | 302F906280 |

Деталь: | PULLEY PICKUP ASSY |
Парткод: | 302HN06080 |
Цена: | 480 ₽ |
Деталь: | BUSH 4 |
Парткод: | 302K306460 |
Деталь: | PAD SEPARATOR MPF |
Парткод: | 302F908250 |
Цена: | 700 ₽ |
Деталь: | SPRING PICKUP B |
Парткод: | 3V2LV06090 |
Деталь: | GUIDE FEED SIDE |
Парткод: | 3V2LV06030 |
Деталь: | HOLDER SEPARATION MPF |
Парткод: | 3V2LV08070 |
Деталь: | COVER FRONT |
Парткод: | 302LV04160 |
Деталь: | GUIDE TURN MPF A |
Парткод: | 302LV08150 |
Деталь: | SHEET GUIDE TURN A |
Парткод: | 302LV08220 |
Деталь: | GEAR Z22R TC |
Парткод: | 302LV24140 |
Деталь: | GEAR Z22L REGIST LOW |
Парткод: | 302LV24150 |
Деталь: | GEAR Z19R-Z22R REGIST UP |
Парткод: | 302LV24160 |
Деталь: | BUSH 6 EW |
Парткод: | 302LV24520 |
Деталь: | PULLEY FEED |
Парткод: | 3V2LV08210 |
Деталь: | SPRING ACTUATOR MPF |
Парткод: | 302LV08201 |

Деталь: | PARTS HOLDER FEED ASSY SP |
Парткод: | 302LV94270 |
Цена: | 2 500 ₽ |
Деталь: | FOOT |
Парткод: | 302HN02611 |
Деталь: | PARTS PWB ASSY CONNECT-L SP |
Парткод: | 302T994040 |
Деталь: | PARTS PWB ASSY CONNECT-L SP |
Парткод: | 302T694070 |
Деталь: | FAN LSU 60-25 |
Парткод: | 302GR44080 |
Цена: | 2 800 ₽ |
Деталь: | SW.PUSH |
Парткод: | 7SP01000006+H01 |
Деталь: | CONNCORD ASSY FFC ENGINE CONNECT-L |
Парткод: | 302T646070 |
Деталь: | SHEET FAN L |
Парткод: | 302LV02610 |
Деталь: | CONN.CORD ASSY S03737 |
Парткод: | 302LV46420 |
Деталь: | PARTS PWB ASSY TH CONNECT SP |
Парткод: | 302LV94220 |
Деталь: | PARTS PWB ASSY ENGINE SP |
Парткод: | 302T994030 |
Деталь: | PARTS PWB ASSY ENGINE SP |
Парткод: | 302T694060 |
Деталь: | INTER LOCK SWITCH |
Парткод: | 2FB27160 |
Деталь: | PARTS PWB ASSY SWITCH SP |
Парткод: | 302LV94210 |
Деталь: | PARTS,FAN COOLING CONVEYING SP |
Парткод: | 302FZ94420 |
Деталь: | PARTS UNIT POWER SUPPLY 120 SP |
Парткод: | 302T694100 |
Деталь: | PARTS UNIT POWER SUPPLY 230 SP |
Парткод: | 302T694110 |
Деталь: | LK-3170 |
Парткод: | 302T993040 |
Деталь: | LK-3190 |
Парткод: | 302T693010 |
Деталь: | CONN.CORD ASSY S03681 |
Парткод: | 302LV46290 |
Деталь: | PARTS PWB ASSY MAIN SP |
Парткод: | 302T694040 |
Деталь: | PARTS PWB ASSY MAIN SP EU |
Парткод: | 302T694050 |
Деталь: | SCREW BOX |
Парткод: | 302F939082 |
Деталь: | GUIDE CONTAINER |
Парткод: | 302LV11240 |
Деталь: | PARTS FAN MOTOR ASSY SP |
Парткод: | 302LV94430 |
Цена: | 4 500 ₽ |
Деталь: | PARTS DRIVE FEED ASSY SP |
Парткод: | 302LV94253 |
Цена: | 5 400 ₽ |
Деталь: | GEAR Z32L REG CLUTCH |
Парткод: | 3V2LV31190 |
Деталь: | GEAR Z32L REG CL |
Парткод: | 302LV31440 |

Деталь: | CLUTCH 50 Z35R |
Парткод: | 302KV44041 |
Цена: | 900 ₽ |
Деталь: | PARTS CLUTCH 20-2W Z35R |
Парткод: | 302LV94161 |
Деталь: | GEAR Z26L DLP CLUTCH |
Парткод: | 302LV31180 |
Деталь: | RAIL PWB MAIN B |
Парткод: | 302LV39040 |
Деталь: | PARTS MOTOR-BL W30 SP |
Парткод: | 302K394201 |
Деталь: | SPRING COUPLING DRUM |
Парткод: | 302LV31290 |
Деталь: | CUT WASHER 5 |
Парткод: | 2C904550 |
Деталь: | CUT WASHER 7 |
Парткод: | 302K914570 |
Деталь: | PLATE DRIVE |
Парткод: | 302LV31010 |
Деталь: | GEAR Z80R-Z36L |
Парткод: | 302LV31060 |
Деталь: | GEAR Z119R |
Парткод: | 302LV31050 |
Деталь: | PLATE DRIVE |
Парткод: | 302L231030 |
Деталь: | GEAR Z128R |
Парткод: | 302L231040 |
Деталь: | GEAR Z86R-Z36L |
Парткод: | 302L231050 |
Деталь: | PARTS DC MOTOR ASSY SP |
Парткод: | 302LV94230 |
Деталь: | CONN.CORD ASSY S03656 |
Парткод: | 302LV46040 |
Деталь: | HOLDER CLUTCH |
Парткод: | 302LV31040 |
Деталь: | GEAR Z46L FREE |
Парткод: | 3V2LV31120 |
Деталь: | GEAR Z37S FREE |
Парткод: | 3V2LV31130 |
Деталь: | PARTS COVER RIGHT LOW ASSY SP |
Парткод: | 302LV94500 |
Деталь: | COVER RIGHT FRONT |
Парткод: | 302LV04080 |
Деталь: | Cover Right Rear |
Парткод: | 302LV04270 |
Деталь: | PARTS COVER RIGHT UP ASSY SP |
Парткод: | 302T694030 |
Деталь: | COVER LEFT LOW |
Парткод: | 302LV04050 |
Деталь: | COVER LEFT UP |
Парткод: | 302LV04040 |
Деталь: | COVER LEFT LOW REAR |
Парткод: | 302LV04260 |
Деталь: | COVER LEFT UP REAR |
Парткод: | 302LV04250 |
Деталь: | COVER SIDE LOW |
Парткод: | 302LV04190 |
Деталь: | COVER SIDE UP |
Парткод: | 302LV04170 |
Деталь: | COVER CONT LOW |
Парткод: | 302T604050 |
Деталь: | COVER CONT MIDDLE |
Парткод: | 302T604040 |
Деталь: | COVER CONT UP |
Парткод: | 302LV04130 |
Деталь: | PARTS COVER TOP ASSY SP |
Парткод: | 302T994010 |
Деталь: | PARTS TRAY TOP ASSY SP |
Парткод: | 302L294110 |
Деталь: | PARTS LID TOP ASSY SP |
Парткод: | 302T994020 |
Деталь: | CONN.CORD ASSY FFC PRN PANEL L |
Парткод: | 302T946010 |
Деталь: | PARTS PWB ASSY PANEL SP |
Парткод: | 302T694090 |
Деталь: | SHEET OPE J |
Парткод: | 302LV05240 |
Деталь: | SHEET OPE E |
Парткод: | 302LV05140 |
Деталь: | PANEL LCD J |
Парткод: | 302T604110 |
Деталь: | PANEL LCD |
Парткод: | 302T604090 |
Деталь: | COVER CABLE |
Парткод: | 302T604060 |
Деталь: | PARTS COVER TOP ASSY SP |
Парткод: | 302T694010 |
Деталь: | PARTS TRAY TOP ASSY SP |
Парткод: | 302LV94280 |
Деталь: | PARTS LID TOP ASSY SP |
Парткод: | 302T894010 |
Деталь: | PARTS LID TOP ASSY SP |
Парткод: | 302T794010 |
Деталь: | PARTS LID TOP ASSY SP |
Парткод: | 302T694020 |
Деталь: | CONN.CORD ASSY FFC PRN PANEL H |
Парткод: | 302T646040 |
Деталь: | COVER TOP B |
Парткод: | 302T904020 |
Деталь: | COVER TOP B |
Парткод: | 302T604020 |
Деталь: | STOPPER LID TOP |
Парткод: | 302T604070 |
Деталь: | SPRING STOPPER LID TOP |
Парткод: | 302T604080 |
Деталь: | GEAR Z66R Z34S |
Парткод: | 302L228041 |
Цена: | 70 ₽ |
Деталь: | GEAR Z21S EXIT |
Парткод: | 302L228030 |
Цена: | 80 ₽ |
Деталь: | ACTUATOR OVERFLOW |
Парткод: | 302L228090 |
Цена: | 110 ₽ |

Деталь: | MOTOR EJECT |
Парткод: | 302F944131 |
Цена: | 4 400 ₽ |
Деталь: | GEAR Z22S |
Парткод: | 302LV28050 |
Цена: | 80 ₽ |
Деталь: | GEAR Z66R-Z40S |
Парткод: | 302LV28031 |
Цена: | 90 ₽ |
Деталь: | GEAR Z17S |
Парткод: | 302LV28040 |
Цена: | 60 ₽ |
Деталь: | ACTUATOR OVERFLOW |
Парткод: | 302LV28141 |
Цена: | 120 ₽ |
Деталь: | PARTS SENSOR OPT SP |
Парткод: | 303M894260 |
Деталь: | COVER REAR UP |
Парткод: | 302L204040 |
Деталь: | COVER REAR LOW |
Парткод: | 302LV04110 |
Деталь: | LABEL PUSH |
Парткод: | 302MC34040 |
Деталь: | COVER CASSETTE |
Парткод: | 302LV04120 |
Деталь: | GEAR Z20S |
Парткод: | 302LV28090 |
Деталь: | GEAR Z22S B |
Парткод: | 302LV28191 |
Деталь: | GEAR Z22S A |
Парткод: | 302LV28100 |
Деталь: | COVER REAR UP |
Парткод: | 302LV04100 |
Деталь: | ACTUATOR DU |
Парткод: | 3V2LV28070 |
Деталь: | PARTS,FAN IMAGE SP |
Парткод: | 302FZ94660 |
Деталь: | SEAL EXIT C |
Парткод: | 302LV28461 |
Деталь: | PARTS MOTOR EJECT SP |
Парткод: | 302T994050 |
Цена: | 4 400 ₽ |
Деталь: | SEAL EXIT |
Парткод: | 302L228110 |
Деталь: | PARTS COVER REAR ASSY SP |
Парткод: | 302MS94041 |
Деталь: | PARTS COVER REAR ASSY J SP |
Парткод: | 302LV94153 |
Деталь: | PARTS COVER REAR ASSY SP |
Парткод: | 302LV94143 |
Деталь: | Накладка на панель управления |
Парткод: | 302LV05210 |
Цена: | 120 ₽ |
Деталь: | HOLDER RETARD B |
Парткод: | 3V2LV09311 |
Деталь: | GUIDE RETARD C |
Парткод: | 302LV09340 |
Деталь: | SPRING RETARD B |
Парткод: | 302LV09330 |

Деталь: | RETARD ROLLER ASSY |
Парткод: | 302F909171 |
Цена: | 900 ₽ |
Деталь: | GEAR CASSETTE /A-49 CASSETTE A4 |
Парткод: | 5MVG127DN071 |
Деталь: | GEAR Z48S LIFT |
Парткод: | 302LV09241 |
Деталь: | GEAR Z15S JOINT |
Парткод: | 302LV09220 |
Деталь: | COVER LIFT GEAR |
Парткод: | 302LV09201 |
Деталь: | CURSOR RIGHT B |
Парткод: | 302LV09350 |
Деталь: | CURSOR LEFT |
Парткод: | 302LV09070 |
Деталь: | CT-3100 |
Парткод: | 302MS93015 |
Деталь: | CT-3130 |
Парткод: | 302LV93035 |

Деталь: | Блок проявки |
Парткод: | DV-3100 |
Цена: | 5 300 ₽ |

Деталь: | Узел переноса заряда в драм-картридже, в сборе |
Парткод: | MC-3100 |
Цена: | 6 100 ₽ |

Деталь: | Вал переноса заряда в драм-картридже |
Парткод: | CET6652 |
Цена: | 1 600 ₽ |
Деталь: | Пружина подшипника вала переноса заряда |
Парткод: | 302F924400 |
Цена: | 240 ₽ |

Деталь: | Ролик отделения бумаги в держателе, в сборе |
Парткод: | CET4322 |
Цена: | 450 ₽ |

Деталь: | Резина ролика отделения бумаги |
Парткод: | CET4322PT |
Цена: | 110 ₽ |

Деталь: | Cassette Tray Assembly |
Парткод: | CT-3130 |
Цена: | 12 500 ₽ |
Деталь: | Резина ролика захвата бумаги |
Парткод: | CET7806BPT |
Цена: | 110 ₽ |
Деталь: | Флажок датчика подачи бумаги |
Парткод: | 303K806030 |

Деталь: | Резина ролика подачи бумаги |
Парткод: | CET7829 |
Цена: | 150 ₽ |

Деталь: | Муфта |
Парткод: | 302NR94010 |
Деталь: | DV-3100 |
Парткод: | 302LV93081 |
Деталь: | FK-3171(J) |
Парткод: | 302T993030 |
Деталь: | FK-3172(U) |
Парткод: | 302T993020 |
Деталь: | FK-3170(E) |
Парткод: | 302T993010 |
Деталь: | FK-3130(J) |
Парткод: | 302LV93126 |
Деталь: | FK-3130(U) |
Парткод: | 302LV93136 |
Деталь: | FK-3130(E) |
Парткод: | 302LV93116 |

Деталь: | PANEL UNIT, MFC9840CDW |
Парткод: | FK-3130 |
Цена: | 12 900 ₽ |

Деталь: | Тефлоновый вал |
Парткод: | CET7814 |
Цена: | 850 ₽ |

Деталь: | Прижимной вал |
Парткод: | CET7815 |
Цена: | 1 400 ₽ |

Деталь: | (Long Life) Тефлоновый вал |
Парткод: | CET78147777 |
Цена: | 1 000 ₽ |
Коды ошибок
0100
0120
0130
0140
0150
0160
0170
0190
0800
0840
1010
1020
1030
1040
1050
1140
1150
1800
1810
1820
1830
1900
1910
1920
1930
2000
2010
2200
2210
2330
2340
2600
2610
2620
2630
4000
4200
5100
6000
6020
6030
6120
6130
6400
7100
7400
7410
7800
7810
7900
F000
F010
F020
F040
F050
F15X
F17X
F18X
F1DX
F21X, F22X, F23X
F24X
F25X
F26X, F27X, F28X
F29X, F2AX
F2BX, F2CX, F2DX
F2EX, F2FX, F30X
F31X, F32X
F35X
F38X
F3AX, F3BX, F3CX
F3DX, F3EX, F3FX
F40X, F41X, F42X
F43X, F44X, F45X
F46X
F47X
F4DX, F4EX
F4FX
F51X, F52X, F53X
F55X, F56X, F57X
F5FX
F62X
F63X
Описание
Error code: | 0100 |
Display: | MAINTENANCE CALL 0100 |
Description: | Backup memory device error |
Causes: | Defective flash memory. Defective main PWB. |
Remedy: | EEPROM (main PWB) 1. Turn the main power swtch off and after 5 seconds, then turn power on. 2. Check that the EEPROM on the main circuit PWB is peroperly installed on the main circuit PWB and, if not, re-install it. 3. Replace the main PWB |
Error code: | 0120 |
Description: | There is a problem with Thermistor for Pre-Heater. |
Causes: | Thermistor Cable has short circuited or cutline. Thermistor has a problem. |
Remedy: | Check Cable connection around Thermistor Thermistor replacement |
Error code: | 0130 |
Description: | There is a problem with Thermistor for Print Heater. |
Causes: | Thermistor cable has short circuited or cutline. Thermistor has a problem. |
Remedy: | Check Cable connection around Thermistor Thermistor replacement |
Error code: | 0140 |
Description: | There is a problem with Thermistor for dryer. |
Causes: | Thermistor cable has short circuited or cutline. Thermistor has a problem. |
Remedy: | Check Cable connection around Thermistor Thermistor replacement |
Error code: | 0150 |
Description: | Even though the machine carries out the regular movement, the output of Slider Sensor does not reach the expected value. |
Causes: | Slider Motor has a problem. Slider Sensor has a problem. Wiring or Flexible Cable has short circuitted or cut-line. Servo Board has a problem. |
Remedy: | Check Cable connection of Servo Board Check Cable connection of Junction Board Slider Motor replacement Slider Sensor replacement Wiring or Flexible Cable replacement Servo Board replacement |
Error code: | 0160 |
Description: | Even though the machine carries out the regular movement, the output of Pressure Pump 1 Sensor does not reach the expected value. |
Causes: | Pressure Pump 1 Motor has a problem. Pressure Pump 1 Sensor has a problem. Pressure Pump 1 Magnet has dropped out. Wiring or Flexible Cable has short circuitted or cut-line. Pump Drive Board has a problem. Servo Board has a problem. |
Remedy: | Check Cable connection of Servo Board Check Cable connection of Junction Board Check Pressure Pump 1 Magnet Pressure Pump 1 Motor replacement Pressure Pump 1 Sensor replacement Wiring or Flexible Cable replacement Pump Drive Board replacement Servo Board replacement |
Error code: | 0170 |
Description: | Even though the machine carries out the regular movement, the output of Supply Pump 1 Sensor does not reach the expected value. |
Causes: | Supply Pump 1 Motor has a problem. Supply Pump 1 Sensor has a problem. Supply Pump 1 Magnet has dropped out. Wiring or Flexible Cable has short circuitted or cut-line. Pump Drive Board has a problem. Servo Board has a problem. |
Remedy: | Check Cable connection of Servo Board Check Cable connection of Junction Board Check Supply Pump 1 Magnet Supply Pump 1 Motor replacement Supply Pump 1 Sensor replacement Wiring or Flexible Cable replacement Pump Drive Board replacement Servo Board replacement |
Error code: | 0190 |
Description: | Thermistor under the BED has a problem. |
Causes: | Device has a problem. Thermistor Cable has short circuited or cutline. |
Remedy: | Thermistor replacement Check Cable connection Heater Board replacement |
Error code: | 0800 |
Display: | Print Unable 08 Turn the power off and then back on again. |
Description: | Image processing error JAM010X is detected twice. |
Causes: | Defective main PWB. |
Remedy: | Main PWB Replace the main PWB. |
Error code: | 0840 |
Description: | Faults of RTC (“Time for maintenance T” is displayed) [Check at power up] The RTC setting has reverted to a previous state. The machine has not been powered for 5 years (compared to the settings stored periodically in the EEPROM). The RTC setting is older than 00:01 on January 1, 2000. [Checked periodically (in 5- minute interval) after powered up] The RTC setting has reverted to a state older than the last time it was checked. 10 minutes have been passed since the previous check. After C840 is detected, the machine enters in disconnection mode after the main power switch has been switched on and off and indicates ‘Maintenance T.’ |
Causes: | The battery is disconnected from the main PWB Defective main PWB. |
Remedy: | Battery (main PWB) 1. Make sure that the back-up batteries on the main PWB are not short-circuited. 2. Reset Maintenance T by executing U906. 3. If the same C call is displayed when power is switched on and off, replace the back up battery. 4. If communication error (due to a noise, etc.) is present with the RTC on the main circuit PWB, check the PWB is properly grounded. Main PWB Replace the main PWB |
Error code: | 1010 |
Display: | Problem with Printhead L/R Chk printing results |
Description: | Lift motor 1 error After cassette 1 is inserted, lift sensor 1 does not turn on within 12 s. This error is detected 4 times successively. The lock signal of the motor is detected continuously for 1 s. This error is detected 4 times successively. |
Causes: | Defective bottom plate elevation mechanism in the cassette. Defective connector cable or poor contact in the connector. Defective drive transmission system of motor. Defective lift motor 1. Defective engine PWB. |
Remedy: | Cassette lift base elevating mechanism Check that the cassette base can be manipulated smoothly, if not, repair or replace. Lift motor 1 1. Check that the cassette base has been ascended. 2. Check the drive gear can rotate or they are not unusually loaded and, if necessary, replace. 3. Confirm that the wiring connector is firmly connected and, if necessary, connect the connector all the way in. Lift motor 1 and Feed PWB 2 (YC3) Feed PWB 2 (YC1) and Engine PWB (YC4) 4. If the wiring is disconnected, shorted or grounded, replace the wiring. 5. Replace the lift motor 1. Lift sensor 1 1. Check that the sensor is correctly positioned. 2. Confirm that the wiring connector is firmly connected and, if necessary, connect the connector all the way in. Lift sensor 1 and Feed PWB 2 (YC8) Feed PWB 2 (YC1) and Engine PWB (YC4) 3. If the wiring is disconnected, shorted or grounded, replace the wiring. 4. Replace the lift sensor1. Feed PWB 2 Replace the Feed PWB 2. Engine PWB 1. Check the engine software and upgrade to the latest, if necessary. 2. Replace the engine PWB. |
Error code: | 1020 |
Description: | Lift motor 2 error After cassette 2 is inserted, lift sensor 2 does not turn on within 12 s. This error is detected 4 times successively. The lock signal of the motor is detected continuously for 1 s. This error is detected 4 times successively. |
Causes: | Defective bottom plate elevation mechanism in the cassette. Defective connector cable or poor contact in the connector. Defective drive transmission system of motor. Defective lift motor 2. Defective engine PWB. |
Remedy: | Cassette lift base elevating mechanism Check that the cassette base can be manipulated smoothly, if not, repair or replace. Lift motor 2 1. Check that the cassette base has been ascended. 2. Check the drive gear can rotate or they are not unusually loaded and, if necessary, replace. 3. Confirm that the wiring connector is firmly connected and, if necessary, connect the connector all the way in. Lift motor 2 and Feed PWB 2 (YC3) Feed PWB 2 (YC1) and Engine PWB (YC4) 4. If the wiring is disconnected, shorted or grounded, replace the wiring. 5. Replace the lift motor 2. Lift sensor 2 1. Check that the sensor is correctly positioned. 2. Confirm that the wiring connector is firmly connected and, if necessary, connect the connector all the way in. Lift sensor 2 and Feed PWB 2 (YC8) Feed PWB 2 (YC1) and Engine PWB (YC4) 3. If the wiring is disconnected, shorted or grounded, replace the wiring. 4. Replace the lift sensor2. Feed PWB 2 Replace the Feed PWB 2. Engine PWB 1. Check the engine software and upgrade to the latest, if necessary. 2. Replace the engine PWB. |
Error code: | 1030 |
Display: | GARO W1221 |
Description: | PF lift motor 1 error (paper feeder) After cassette 3 is inserted, PF lift sensor 1 does not turn on within 12 s. This error is detected 5 times successively. During driving the motor, the lift overcurrent protective monitor signal is detected for 1 s or more 5 times successively. However, the first 1 s after motor is turned on is excluded from detection. |
Causes: | Defective bottom plate elevation mechanism in the cassette. Defective connector cable or poor contact in the connector. Defective drive transmission system of motor. Defective PF lift motor 1. Defective PF main PWB. |
Remedy: | Defective bottom plate elevation mechanism in the cassette. Check to see if the bottom plate can move smoothly and repair it if any problem is found. Defective connector cable or poor contact in the connector. Reinsert the connector. Also check for continuity within the connector cable. If none, replace the cable. PF lift motor 1 and PF main PWB (YC7) Defective drive transmission system of motor. Check if the gears rotate smoothly. If not, grease the bushes and gears. Check for broken gears and replace if any. Defective PF lift motor 1. Replace the PF lift motor 1. Defective PF main PWB. Replace the PF main PWB (Refer to the service manual for the paper feeder). |
Error code: | 1040 |
Display: | GL2: W0501 The memory is full. |
Description: | PF lift motor 2 error (paper feeder) After cassette 4 is inserted, PF lift sensor 2 does not turn on within 12 s. This error is detected 5 times successively. During driving the motor, the lift overcurrent protective monitor signal is detected for 1 s or more 5 times successively. However, the first 1 s after motor is turned on is excluded from detection. |
Causes: | Defective bottom plate elevation mechanism in the cassette. Defective connector cable or poor contact in the connector. Defective drive transmission system of motor. Defective PF lift motor 2. Defective PF main PWB. |
Remedy: | Defective bottom plate elevation mechanism in the cassette. Check to see if the bottom plate can move smoothly and repair it if any problem is found. Defective connector cable or poor contact in the connector. Reinsert the connector. Also check for continuity within the connector cable. If none, replace the cable. PF lift motor 2 and PF main PWB (YC7) Defective drive transmission system of motor. Check if the gears rotate smoothly. If not, grease the bushes and gears. Check for broken gears and replace if any. Defective PF lift motor 2. Replace the PF lift motor 2. Defective PF main PWB. Replace the PF main PWB (Refer to the service manual for the paper feeder). |
Error code: | 1050 |
Display: | Blue platen switch is dirty. Please clean the switch. |
Description: | SM lift motor error (side multi tray) After cassette 5 is inserted, SM lift sensor does not turn on within 12 s. This error is detected 5 times successively. (Time to detect is 2 seconds at the second time and later.) During driving the motor, the lift overcurrent protective monitor signal is detected for 1 s or more 5 times successively. However, the first 1 s after motor is turned on is excluded from detection. |
Causes: | Defective bottom plate elevation mechanism in the cassette. Defective connector cable or poor contact in the connector. Defective drive transmission system of motor Defective SM lift motor. Defective SM main PWB. |
Remedy: | Cassette lift base elevating mechanism Check that the cassette base can be manipulated smoothly, if not, repair or replace. SM Lift motor 1. Check that the cassette base has been ascended. 2. Check the drive gear can rotate or they are not unusually loaded and, if necessary, replace. 3. Confirm that the wiring connector is firmly connected and, if necessary, connect the connector all the way in. SM Lift motor and SM main PWB (YC5) 4. If the wiring is disconnected, shorted or grounded, replace the wiring. 5. Replace the SM Lift motor. SM Lift sensor 1. Check that the sensor is correctly positioned. 2. Confirm that the wiring connector is firmly connected and, if necessary, connect the connector all the way in. SM Lift sensor and SM main PWB (YC7) 3. If the wiring is disconnected, shorted or grounded, replace the wiring. 4. Replace the SM Lift sensor. SM main PWB Replace the SM main PWB (Refer to the service manual for the paper feeder). |
Error code: | 1140 |
Description: | SD lift motor error (side deck) After cassette 5 is inserted, SD lift sensor does not turn on within 30 s. The lock signal of the motor is detected continuously for 200 ms. |
Causes: | Defective connector cable or poor contact in the connector. Defective drive transmission system of motor. Defective SD lift motor. Defective SD main PWB. |
Remedy: | Paper feeder lift base elevating mechanism Check that the cassette base can be manipulated smoothly, if not, repair or replace. SD Lift motor 1. Check that the cassette base has been ascended. 2. Check the drive gear can rotate or they are not unusually loaded and, if necessary, replace. 3. Confirm that the wiring connector is firmly connected and, if necessary, connect the connector all the way in. SD Lift motor and SD main PWB (YC8) 4. If the wiring is disconnected, shorted or grounded, replace the wiring. 5. Replace the SD Lift motor. SD Lift sensor 1. Check that the sensor is correctly positioned. 2. Confirm that the wiring connector is firmly connected and, if necessary, connect the connector all the way in. SD Lift sensor and SD main PWB (YC5) 3. If the wiring is disconnected, shorted or grounded, replace the wiring. 4. Replace the SD Lift sensor. SD main PWB Replace the SD main PWB (Refer to the service manual for the paper feeder). |
Error code: | 1150 |
Description: | Lift motor descent error *40/42 and 45/47 ppm printers (EUR/ USA model) only Optional bulk paper feeder’s tray bottom position sensor does not turn on. Lift motor lock error occurred 3 times. |
Causes: | Defective bulk paper feeder’s tray bottom position sensor. Defective harness between bulk paper feeder’s tray bottom position sensor and main PWB (YC8), or improper connector insertion. Defective bulk paper feeder’s main PWB. |
Remedy: | Defective bulk paper feeder’s tray bottom position sensor. Replace the bulk paper feeder’s tray bottom position sensor. Defective harness between bulk paper feeder’s tray bottom position sensor and main PWB (YC8), or improper connector insertion. Reinsert the connector. Also check for continuity within the connector harness. If none, remedy or replace the harness. Defective bulk paper feeder’s main PWB. Replace the bulk paper feeder’s main PWB. |
Error code: | 1800 |
Description: | Paper feeder communication error A communication error from paper feeder is detected 10 times in succession. |
Causes: | Improper installation paper feeder. Defective connector cable or poor contact in the connector. Defective engine PWB. Defective PF main PWB. |
Remedy: | Paper feeder Check the wiring connection status with the main unit and, if necessary, try connecting it again. PF main PWB 1. Confirm that the wiring connector is firmly connected and, if necessary, connect the connector all the way in. PF main PWB (YC13) and Engine PWB (YC19) 2. If the wiring is disconnected, shorted or grounded, replace the wiring. 3. Replace the PF main PWB (Refer to the service manual for the paper feeder). Engine PWB 1. Check the engine software and upgrade to the latest, if necessary. 2. Replace the engine PWB. |
Error code: | 1810 |
Description: | Side multi tray communication error A communication error from side multi tray is detected 10 times in succession. |
Causes: | Improper installation side multi tray. Defective connector cable or poor contact in the connector. Defective engine PWB. Defective SM main PWB. |
Remedy: | Side multi tray Check the wiring connection status with the main unit and, if necessary, try connecting it again. SM main PWB 1. Confirm that the wiring connector is firmly connected and, if necessary, connect the connector all the way in. SM main PWB (YC1) and Engine PWB (YC19) 2. If the wiring is disconnected, shorted or grounded, replace the wiring. 3. Replace the SM main PWB (Refer to the service manual for the paper feeder). Engine PWB Check the engine software and upgrade to the latest, if necessary. Replace the engine PWB. SM main PWB Replace the SM main PWB (Refer to the service manual for the paper feeder). |
Error code: | 1820 |
Description: | Side paper feeder communication error A communication error from paper feeder is detected 10 times in succession. |
Causes: | Improper installation side paper feeder. Defective connector cable or poor contact in the connector. Defective engine PWB. Defective SM main PWB. Defective PF main PWB. |
Remedy: | Side paper feeder Check the wiring connection status with the main unit and, if necessary, try connecting it again. SM main PWB 1. Confirm that the wiring connector is firmly connected and, if necessary, connect the connector all the way in. SM main PWB (YC1) and Engine PWB (YC19) 2. If the wiring is disconnected, shorted or grounded, replace the wiring. 3. Replace the SM main PWB (Refer to the service manual for the paper feeder). PF main PWB 1. Confirm that the wiring connector is firmly connected and, if necessary, connect the connector all the way in. PF main PWB (YC13) and SM main PWB (YC4) 2. If the wiring is disconnected, shorted or grounded, replace the wiring. 3. Replace the PF main PWB (Refer to the service manual for the paper feeder). Engine PWB 1. Check the engine software and upgrade to the latest, if necessary. 2. Replace the engine PWB. |
Error code: | 1830 |
Description: | Paper feeder communication error (third cassette) A communication error from paper feeder is detected 10 times in succession. |
Remedy: | Paper feeder 3 Check the wiring connection status with PF2, and if necessary, reconnect it. PF3 main PWB 1. Confirm that the wiring connector is firmly connected, and if necessary, connect the connector all the way in. PF2 main PWB (YC3 and PF3 main PWB (YC5,4) 2. If the wiring is disconnected, short-circuited or has ground fault, replace the wire. 3. Reinstall the PF firmware. 4. Replace the PF3 main PWB. PF2 main PWB Replace the PF2 main PWB. |
Error code: | 1900 |
Description: | Paper feeder EEPROM error When writing the data, read and write data does not match 3 times in succession. |
Causes: | Defective PF main PWB. Device damage of EEPROM. |
Remedy: | PF main PWB (EEPROM) 1. Confirm that the wiring connector is firmly connected and, if necessary, connect the connector all the way in. 2. Replace the PF main PWB (Refer to the service manual for the paper feeder). |
Error code: | 1910 |
Description: | Side multi tray EEPROM error When writing the data, read and write data does not match 3 times in succession. |
Causes: | Defective SM main PWB. Device damage of EEPROM. |
Remedy: | SM main PWB (EEPROM) 1. Confirm that the wiring connector is firmly connected and, if necessary, connect the connector all the way in. 2. Replace the SM main PWB (Refer to the service manual for the paper feeder). |
Error code: | 1920 |
Description: | Side paper feeder EEPROM error When writing the data, read and write data does not match 3 times in succession. |
Causes: | Defective PF main PWB. Device damage of EEPROM. |
Remedy: | PF main PWB 1. Confirm that the wiring connector is firmly connected and, if necessary, connect the connector all the way in. 2. Replace the PF main PWB (Refer to the service manual for the paper feeder). |
Error code: | 1930 |
Description: | Paper feeder 4 EEPROM error When writing the data, the write data and the read data is not in agreement. |
Causes: | Defective PF main PWB. Device damage of EEPROM. |
Remedy: | Defective PF main PWB. Replace the PF main PWB. Device damage of EEPROM. Replace the PF main PWB. |
Error code: | 2000 |
Description: | DDA Communication Error. |
Causes: | The communication error occurs when the IC4 or IC22 on the Main Board is broken. And it causes the Motor Error. |
Remedy: | Replace the Main Board. |
Error code: | 2010 |
Display: | Paper loaded askew. Press Load/Eject and reload the paper. |
Description: | Main motor startup error Main motor is not stabilized within 1 s since the motor is activated. |
Causes: | Main motor. Engine PWB |
Remedy: | Main motor 1. To check the motor operation execute U030 Main (main motor). 2. Confirm that the wiring connector is firmly connected and, if necessary, connect the connector all the way in. Main motor and Engine PWB (YC13) 3. If the wiring is disconnected, shorted or grounded, replace the wiring. 4. Replace the main motor. Engine PWB 1. Check the engine software and upgrade to the latest, if necessary. 2. Replace the engine PWB. |
Error code: | 2200 |
Description: | Main motor steady-state error After main motor is stabilized, the ready signal is at the H level for 2 s continuously. |
Causes: | Main motor. Engine PWB. |
Remedy: | Main motor 1. To check the motor operation execute U030 Main (main motor). 2. Check the drive gear can rotate or they are not unusually loaded and, if necessary, replace. 3. Confirm that the wiring connector is firmly connected and, if necessary, connect the connector all the way in. Main motor and Engine PWB (YC16) 4. If the wiring is disconnected, shorted or grounded, replace the wiring. 5. Replace the main motor. Engine PWB 1. Check the engine software and upgrade to the latest, if necessary. 2. Replace the engine PWB. |
Error code: | 2210 |
Description: | Drum motor steady-state error Stable OFF is detected for 4 s continuously after drum motor stabilized. |
Remedy: | Defective connector cable or poor contact in the connector. Reinsert the connector. Also check for continuity within the connector cable. If none, replace the cable. Drum motor and engine PWB (YC4) Defective drive transmission system of the drum motor. Check if the rollers and gears rotate smoothly. If not, grease the bushes and gears. Check for broken gears and replace if any. Defective drum motor. Replace the drum motor. Defective engine PWB. Replace the engine PWB and check for correct operation. |
Error code: | 2330 |
Description: | Fuser pressure release motor error When the fuser pressure release motor is driven, the motor over-current detection signal is detected continuously for 8 times (800 ms) at 100 ms intervals. |
Causes: | Defective connector cable or poor contact in the connector. Defective drive transmission system of the fuser pressure release motor. Defective fuser pressure release motor. Defective engine PWB. |
Remedy: | Defective connector cable or poor contact in the connector. Reinsert the connector. Also check for continuity within the connector cable. If none, replace the cable. Fuser pressure release motor and engine PWB (YC38) Defective drive transmission system of the fuser pressure release motor. Check if the rollers and gears rotate smoothly. If not, grease the bushes and gears. Check for broken gears and replace if any. Defective fuser pressure release motor. Replace the fuser pressure release motor. Defective engine PWB. Replace the engine PWB and check for correct operation. |
Error code: | 2340 |
Description: | Fuser pressure release motor time-out error When the fuser pressure release motor is driven, the envelope switch (EVSW) is not detectable for 6 s. |
Causes: | Defective connector cable or poor contact in the connector.Defective drive transmission system of the fuser pressure release motor. Defective fuser pressure release motor. Defective engine PWB. |
Remedy: | Defective connector cable or poor contact in the connector. Reinsert the connector. Also check for continuity within the connector cable. If none, replace the cable. Fuser pressure release motor and engine PWB (YC38) Defective drive transmission system of the fuser pressure release motor. Check if the rollers and gears rotate smoothly. If not, grease the bushes and gears. Check for broken gears and replace if any. Defective fuser pressure release motor. Replace the fuser pressure release motor. Defective engine PWB. Replace the engine PWB and check for correct operation. |
Error code: | 2600 |
Description: | PF paper feed motor error (large capacity feeder) After PF paper feed motor is driven, the ready signal does not turn to L within 2 s. |
Causes: | Defective connector cable or poor contact in the connector. Defective drive transmission system of motor. Defective PF paper feed motor. Defective PF main PWB. |
Remedy: | PF paper feed motor 1. To check the feed unit operation, execute U247 LCF- Motor ON. 2. Check the paper feed roller and drive gear can rotate or they are not unusually loaded and, if necessary, replace. 3. Confirm that the wiring connector is firmly connected and, if necessary, connect the connector all the way in. PF paper feed motor and PF main PWB (YC16) 4. If the wiring is disconnected, shorted or grounded, replace the wiring. 5. Replace the paper feed motor. PF main PWB Replace the PF main PWB (Refer to the service manual for the paper feeder). |
Error code: | 2610 |
Description: | PF paper feed motor error (paper feeder) After PF paper feed motor is driven, the ready signal does not turn to L within 2 s. |
Causes: | Defective connector cable or poor contact in the connector. Defective drive transmission system of motor. Defective PF paper feed motor. Defective PF main PWB. |
Remedy: | PF paper feed motor 1. To check the feed unit operation, execute U247 2PF - Motor ON. 2. Check the paper feed roller and drive gear can rotate or they are not unusually loaded and, if necessary, replace. 3. Confirm that the wiring connector is firmly connected and, if necessary, connect the connector all the way in. PF paper feed motor and PF main PWB (YC16) 4. If the wiring is disconnected, shorted or grounded, replace the wiring. 5. Replace the paper feed motor. PF main PWB Replace the PF main PWB (Refer to the service manual for the paper feeder). |
Error code: | 2620 |
Description: | PF drive motor 3 error (PF3) During the motor drive, the stable signal is not turned on for continuous 5 s. |
Remedy: | Defective connector cable or poor contact in the connector 1. Reinsert the connector. 2. Check continuity within the connector wire. If none, replace the wire. PF drive motor 3 and PF main PWB (YC6) Drive transmission system for the PF drive motor 1. Check if the rollers and gears rotate smoothly. If not, clean or grease the bushes and gears. 2. Replace the gears, if damaged. PF drive motor Replace the PF drive motor 3. PF main PWB Replace the PF main PWB. |
Error code: | 2630 |
Description: | Paper feed motor error (bottom) The notification that was received, the motor clock sensor cannot detect the revolution of the paper feed motor of the optional paper feeder (third). |
Causes: | Defective paper feeder. Defective engine controller PWB (A0004). |
Remedy: | Defective paper feeder. Refer to the paper feeder`s service manual. Defective engine controller PWB (A0004). Replace the engine controller PWB (A0004). |
Error code: | 4000 |
Display: | Supplies Drum End Soon. |
Description: | Command Communication Error. |
Causes: | The communication error occurs when the IC4 or IC22 on the Main Board is broken. And it causes the Motor Error. |
Remedy: | Replace the Main Board. |
Error code: | 4200 |
Display: | Supplies Replace Drum |
Description: | BD steady-state error The BD signal is not detected. |
Causes: | APC PWB (LSU). Main/Engine PWB. |
Remedy: | APC PWB (LSU) 1. Confirm that the FCC wiring connector is not distorted and connect the FCC wiring all the way in. Laser scanner unit and main/engine PWB (YC2010) 2. If the FCC wiring is disconnected, shorted or grounded, replace the FCC wiring. 3. Replace the laser scanner unit. Main/Engine PWB 1. Check the main/engine software and upgrade to the latest, if necessary. 2. Replace the main/engine PWB. |
Error code: | 5100 |
Description: | Short-circuited main charger output Five pages have been printed with the main charger output short-circuited. |
Causes: | Drum unit installed incorrectly. Engine PWB installed incorrectly. Defective engine PWB |
Remedy: | Drum unit installed incorrectly. Verify harness is not pinched in the drum unit. Engine PWB installed incorrectly. Verify harness is not pinched in the engine PWB. Defective engine PWB. Replace the engine PWB. |
Error code: | 6000 |
Description: | Broken fuser heater wire Fuser thermistor 1 does not reach 100° C/212 °F even after 30 s during warming up. The detected temperature of fuser thermistor 1 does not reach the specified temperature (ready indication temperature) for 420 s in warming up after reached to 100° C/212 °F. |
Causes: | Defective connector cable or poor contact in the connector. Deformed connector pin. Defective triac. Fuser thermostat triggered. Defective fuser heater. Defective engine PWB. |
Remedy: | Fuser unit 1. Check that no paper jam is present. 2. Confirm that the wiring connector is firmly connected and, if necessary, connect the connector all the way in. Fuser unit and Engine PWB (YC26) 3. If the wiring is disconnected, shorted or grounded, replace the wiring. 4. Replace the Fuser unit Replace the Fuser unit. (Deteriorated sensitivity due to the toner adhered to the center thermistor.) Engine PWB 1. Check the engine software and upgrade to the latest, if necessary. 2. Replace the engine PWB. Power source PWB 1. Confirm that the wiring connector is firmly connected and, if necessary, connect the connector all the way in. Power source PWB (YC3) and fuser heater PWB (YC3) Fuser heater PWB (YC2) and feed PWB 1 (YC27) Feed PWB 1 (YC1) and Engine PWB (YC6) Fuser heater 1. Replace the fuser unit. |
Error code: | 6020 |
Description: | Abnormally high fuser thermistor 1 temperature Fuser thermistor 1 detects a temperature higher than 240°C/464°F for 1 s. |
Causes: | Deformed connector pin. Defective triac. Shorted fuser thermistor 1. Defective engine PWB. |
Remedy: | Fuser unit 1. Confirm that the wiring connector is firmly connected and, if necessary, connect the connector all the way in. Fuser unit and Engine PWB (YC26) 2. If the wiring is disconnected, shorted or grounded, replace the wiring. 3. Replace the Fuser unit. Engine PWB 1. Check the engine software and upgrade to the latest, if necessary. 2. Replace the engine PWB. |
Error code: | 6030 |
Description: | Broken fuser thermistor 1 wire Input from fuser center thermistor 1 is 1010 or more (A/D value) continuously for 1 s. Verify if A/D read in the differential output won’t change by 4 or more when it was turned on for 10 seconds in a lowtemperature environment. |
Causes: | Defective connector cable or poor contact in the connector. Deformed connector pin. Defective triac. Broken fuser thermistor 1 wire. Fuser thermostat triggered. Defective fuser heater. Defective engine PWB. |
Remedy: | Fuser unit 1. Check that no paper jam is present. 2. Confirm that the wiring connector is firmly connected and, if necessary, connect the connector all the way in. Fuser unit and Engine PWB (YC26) 3. If the wiring is disconnected, shorted or grounded, replace the wiring. 4. Replace the Fuser unit. (Deteriorated sensitivity due to the toner adhered to the center thermistor.) Engine PWB 1. Check the engine software and upgrade to the latest, if necessary. 2. Replace the engine PWB. Fuser thermistor 1 1. Replace the Fuser unit. Fuser thermostat (triggered) 1. Confirm that the wiring connector is firmly connected and, if necessary, connect the connector all the way in. Fuser unit and fuser heater PWB (YC1) 2. If the wiring is disconnected, shorted or grounded, replace the wiring. 3. Replace the Fuser unit. |
Error code: | 6120 |
Description: | Abnormally high fuser press thermistor 5 temperature Fuser press thermistor 5 detects a temperature higher than 190°C/ 374°F for 1 s. |
Causes: | Deformed connector pin. Defective triac. Shorted fuser thermistor 5. Defective engine PWB. |
Remedy: | Fuser unit 1. Confirm that the wiring connector is firmly connected and, if necessary, connect the connector all the way in. Fuser unit and Engine PWB (YC26) 2. If the wiring is disconnected, shorted or grounded, replace the wiring. 3. Replace the Fuser unit. Engine PWB 1. Check the engine software and upgrade to the latest, if necessary. 2. Replace the engine PWB. |
Error code: | 6130 |
Description: | Broken fuser press thermistor 5 wire The input from the fuser press thermistor 5 has been less than 30°C/ 86°F (A/D: greater thann992) for 60 seconds continuously. |
Causes: | Defective connector cable or poor contact in the connector. Deformed connector pin. Defective triac. Broken fuser thermistor 5 wire. Defective fuser IH. Defective engine PWB. |
Remedy: | Fuser unit 1. Confirm that the wiring connector is firmly connected and, if necessary, connect the connector all the way in. Fuser unit and Engine PWB (YC26) Fuser IH PWB(YC4) 2. If the wiring is disconnected, shorted or grounded, replace the wiring. 3. Replace the Fuser unit. Engine PWB 1. Check the engine software and upgrade to the latest, if necessary. 2. Replace the engine PWB. Fuser IH PWB 1. Confirm that the wiring connector is firmly connected and, if necessary, connect the connector all the way in. Fuser IH PWB(YC4) and Engine PWB (YC26) 2. Replace the fuser IH PWB. Fuser IH unit 1. Confirm that the wiring connector is firmly connected and, if necessary, connect the connector all the way in. Fuser IH unit and Fuser IH PWB (YC9 and 10) 2. If the wiring is disconnected, shorted or grounded, replace the wiring. 3. Replace the fuser IH unit. |
Error code: | 6400 |
Display: | No Belt Unit Open the Front Cover, pull out all Drum Units completely and install the Belt Unit. |
Description: | Zero-cross signal error While fuser heater ON/OFF control is performed, the zerocross signal is not input within 3 s. |
Causes: | Fuser unit. |
Remedy: | Fuser unit 1. Confirm that the wiring connector is firmly connected and, if necessary, connect the connector all the way in. Fuser heater PWB (YC2) and feed PWB 1 (YC27) 2. If the wiring is disconnected, shorted or grounded, replace the wiring. 3. Replace the fuser heater PWB. |
Error code: | 7100 |
Display: | Jam Rear Open the Back Cover and remove the jammed paper, then press [Start]. |
Description: | Toner sensor error Sensor output value of 8 or less. |
Causes: | Toner sensor. Toner motor. Main/Engine PWB. |
Remedy: | Toner sensor 1. Check the toner sensor output by U150. 2. Confirm that the wiring connector is firmly connected and, if necessary, connect the connector all the way in. Toner sensor and main/engine PWB (YC9) 3. If the wiring is disconnected, shorted or grounded, replace the wiring. 4. Check that the gears of the Developer unit are not damaged and the spiral can rotate. 5. Replace the Developer unit. Toner motor 1. Draw out the toner container and execute U135 to check the toner motor operation. 2. Check the drive gear can rotate or they are not unusually loaded and, if necessary, replace. 3. Confirm that the wiring connector is firmly connected and, if necessary, connect the connector all the way in. Toner motor and main/engine PWB (YC12) 4. If the wiring is disconnected, shorted or grounded, replace the wiring. 5. Replace the Toner motor. Main/Engine PWB 1. Check the main/engine software and upgrade to the latest, if necessary. 2. Replace the main/engine PWB. |
Error code: | 7400 |
Display: | Jam Tray 2 Pull the paper tray2 completely out of the machine and remove the jammed paper. |
Description: | Developing unit connector insertion problem Absence of the developing unit is detected. |
Causes: | Developing unit connector inserted incorrectly. Defective developing unit connector. |
Remedy: | Developing unit connector inserted incorrectly. Reinsert the developing unit connector if necessary. Defective developing unit connector. Replace the developing unit. |
Error code: | 7410 |
Description: | Drum unit connector insertion problem Absence of the drum unit is detected.c |
Causes: | Drum unit connector inserted incorrectly. Defective drum unit connector. |
Remedy: | Drum unit connector inserted incorrectly. Reinsert the drum unit connector if necessary. Defective drum unit connector. Replace the drum unit. |
Error code: | 7800 |
Description: | Broken outer temperature sensor wire The device did not respond for more than 5 ms during reading, in 5 times. |
Causes: | Defective connector cable or poor contact in the connector. Defective outer temperature sensor. Defective engine PWB. |
Remedy: | Outer temperature sensor 1. Confirm that the wiring connector is firmly connected and, if necessary, connect the connector all the way in. Outer temperature sensor and Front PWB (YC8) Front PWB (YC2) and Engine PWB (YC8) 2. If the wiring is disconnected, shorted or grounded, replace the wiring. 3. Replace the Outer temperature sensor. Front PWB Replace the front PWB Engine PWB 1. Check the engine software and upgrade to the latest, if necessary. 2. Replace the engine PWB. |
Error code: | 7810 |
Description: | Short-circuited outer temperature sensor 1 The sensor input sampling is less than 0. |
Causes: | Defective connector cable or poor contact in the connector. Defective outer temperature sensor 1. Defective engine PWB. |
Remedy: | Defective connector cable or poor contact in the connector. Reinsert the connector. Also check for continuity within the connector cable. If none, replace the cable. Outer temperature sensor and front PWB (YC16) Front PWB (YC2) and engine PWB (YC10) Defective outer temperature sensor. Replace outer temperature sensor. Defective engine PWB. Replace the engine PWB and check for correct operation. |
Error code: | 7900 |
Display: | Jam Manual Feed Pull out the jammed paper from Manual Feed and press Start |
Description: | Drum unit EEPROM error No response is issued from the device in reading/writing for 5 ms or more and this problem is repeated five times successively. Mismatch of reading data from two locations occurs eight times successively. Mismatch between writing data and reading data occurs eight times successively. |
Causes: | Defective connector cable or poor contact in the connector. Defective drum unit. |
Remedy: | Defective connector cable or poor contact in the connector. Reinsert the connector. Also check for continuity within the connector cable. If none, replace the cable. Drum unit and engine PWB (YC15) Defective drum unit. Replace the drum unit. |
Error code: | F000 |
Description: | Communication error between the main unit and CPU |
Causes: | The panel cannot be detected since the CPU communication between the main PWB and the operation panel main PWB is unavailable. |
Remedy: | 1 Resetting the main power The communication between the main PWB and the operation panel main PWB is faulty. Remove the original and check the sensor. Next, turn off the power switch and main switch. Then, turn on the main switch and power switch when passing 5 seconds. 2 Checking the connection The connector is not properly connected. The wire or the SATA cable is faulty. Clean the terminal of the following SATA cable connector and the wire connectors and reconnect the connectors. If there is no continuity, replace the SATA cable or the wire. • Main PWB - Operation panel main PWB Wiring diagram 3 Executing U021 The backup RAM data is faulty. Execute U021 to initialize the backup RAM data. Executing U021 4 Replacing the main PWB The main PWB is faulty. Replace the main PWB. 5 Replacing the operation panel main PWB The operation panel main PWB is faulty. Replace the panel main PWB. |
Error code: | F010 |
Description: | Program read error (SSD) |
Causes: | The garbled 2bit data was detected during the program read from the flash memory. |
Remedy: | 1 (When the service call error appears after replacing the SSD) Replacing the SSD along the correct procedures The firmware is not stored in the SSD. Insert the USB memory device containing all released firmware into the main unit, and turn the main power on. Firmware Update 2 Checking the SSD (if lit after replacing the SSD) An SSD out of specification is installed. Install the SSD matching the memory capacity specification. 3 Resetting the main power The communication between the main PWB and the operation panel main PWB is faulty. Remove the original and check the sensor. Next, turn off the power switch and main switch. Then, turn on the main switch and power switch when passing 5 seconds. 4 Checking the SSD The SSD is not properly attached. Check if the SSD terminal is not faulty and clean it. Then, reinstall the SSD. 5 Checking the connection The connector is not properly connected. The wire or the SATA cable is faulty. Clean the terminal of the following SATA cable connector and the wire connectors and reconnect the connectors. If there is no continuity, replace the SATA cable or the wire. • Main PWB - Operation panel main PWB Wiring diagram 6 Executing U021 The backup RAM data is faulty. Execute U021 to initialize the backup RAM data. Executing U021 7 Replacing the SSD The SSD is faulty. Backup the data in the SSD at U026. Then, replace the SSD and turn the main power on while installing the USB memory storing the firmware for the affected model n the main unit. 8 Replacing the main PWB The main PWB is faulty. Replace the main PWB. |
Error code: | F020 |
Description: | System memory error (RAM reading/writing error or CPU memory error) |
Causes: | The error appears during the reading/writing check of the RAM for the CPU when the main unit starts up. |
Remedy: | 1 Resetting the main power The communication between the main PWB and the operation panel main PWB is faulty. Remove the original and check the sensor. Next, turn off the power switch and main switch. Then, turn on the main switch and power switch when passing 5 seconds. 2 Executing U021 The backup RAM data is faulty. Execute U021 to initialize the backup RAM data. Executing U021 3 Checking the main PWB The connector or the FFC is not properly connected. The wire, the FFC or the PWB is faulty. Clean the connectors on the main PWB and the FFC terminal. Then, reconnect the wire connector and the FFC. At that time, if the wire is pinched by other parts or it is damaged, repair or replace the wire. If the FFC terminal section is deformed or FFC is broken, replace the FFC. If the issue is not resolved, replace the main PWB. |
Error code: | F040 |
Description: | Option installation error |
Causes: | The size of the attached main memory is 2 GB when the DSDF is installed. |
Remedy: | Main memory Replace the main memory with a 4 GB one. DSDF • Remove the DSDF. • Replace the DSDF with an RADF. |
Error code: | F050 |
Description: | Engine main program error |
Causes: | The engine program cannot start up. |
Remedy: | 1 Firmware upgrade The firmware is not the latest version. Upgrade the engine firmware to the latest version Firmware Update 2 Resetting the main power The print engine ROM checksum is faulty. Remove the original and check the sensor. Next, turn off the power switch and main switch. Then, turn on the main switch and power switch when passing 5 seconds. 3 Checking the EEPROM The EEPROM is not properly attached. Reattach the EEPROM. 4 Checking the engine PWB The connector or the FFC is not properly connected. The wire, the FFC or the PWB is faulty. Clean the connectors on the engine PWB and the FFC terminal. Then, reconnect the wire connector and the FFC. At that time, if the wire is pinched by other parts or it is damaged, repair or replace the wire. If the FFC terminal section is deformed or FFC is broken, replace the FFC. If the issue is not resolved, replace the engine PWB. |
Error code: | F15X |
Description: | An error is detected at the authentication device control section |
Remedy: | 1) Check connection of the harness (Authentication device - Main board) and connectors and check function. 2) Format the HDD and check function. (U024 FULL formatting) 3) Execute the U021 Memory initializing to initialize the controller backup memory and check function. 4) Replace the main board and check function. 5) Replace the HDD and check function. 6) Retrieve the USBLOG and contact the Service Administrative Division. |
Error code: | F17X |
Description: | An error is detected at the print data control section |
Remedy: | 1) Format the HDD and check function. (U024 FULL formatting) 2) Execute the U021 Memory initializing to initialize the controller backup memory and check function. 3) Replace the main board and check function. 4) Replace the HDD and check function. 5) Retrieve the USBLOG and contact the Service Administrative Division. |
Error code: | F18X |
Description: | An error is detected at the Video control secion |
Remedy: | 1) Check connection of the harness (Engine - Main board) and connectors and check function. 2) Format the HDD and check function. (U024 FULL formatting) 3) Execute the U021 Memory initializing to initialize the controller backup memory and check function. 4) Replace the engine board and check function. 5) Replace the main board and check function. 6) Retrieve the USBLOG and contact the Service Administrative Division. |
Error code: | F1DX |
Description: | An error is detected at the Image memory management section |
Remedy: | 1) Format the HDD and check function. (U024 FULL formatting) 2) Execute the U021 Memory initializing to initialize the controller backup memory and check function. 3) Replace the main board and check function. 4) Replace the HDD and check function. 5) Retrieve the USBLOG and contact the Service Administrative Division. *The F1D4 error is RAM allocation error. -1Check it with the U340 -2Initialize the setting valued with the U021 |
Error code: | F21X, F22X, F23X |
Description: | An error is detected at the Image processing section |
Remedy: | 1) Check contact of the DDR memory and check function. 2) Format the HDD and check function. (U024 FULL formatting) 3) Execute the U021 Memory initializing to initialize the controller backup memory and check function. 4) Replace the main board and check function. 5) Replace the HDD and check function. 6) Retrieve the USBLOG and contact the Service Administrative Division. |
Error code: | F24X |
Description: | An error is detected at the System management section |
Remedy: | 1) Check contact of the DDR memory and check function. 2) Format the HDD and check function. (U024 FULL formatting) 3) Execute the U021 Memory initializing to initialize the controller backup memory and check function. 4) Replace the main board and check function. 5) Replace the HDD and check function. 6) Retrieve the USBLOG and contact the Service Administrative Division. |
Error code: | F25X |
Description: | An error is detected at the Network management section |
Remedy: | 1) Format the HDD and check function. (U024 FULL formatting) 2) Execute the U021 Memory initializing to initialize the controller backup memory and check function. 3) Replace the main board and check function. 4) Retrieve the USBLOG and contact the Service Administratuve Division. (or retrieve the packet capture data depending on the reult of analysis) |
Error code: | F26X, F27X, F28X |
Description: | Abnormality detecting in the system Management Department |
Remedy: | (1) Initialize HDD and perform an operation check. (FULL of U024) * ( 2) Carry out U021 Main backup initialization and perform an operation check. (3) Exchange a Main board and perform an operation check. (4) Exchange HDD and perform an operation check. * (5) Get USBLOG and contact service headquarters. * Only HDD standard model |
Error code: | F29X, F2AX |
Description: | Abnormality detecting in the system Management Department |
Remedy: | (1) Initialize HDD and perform an operation check. (FULL of U024) * ( 2) Carry out U021 Main backup initialization and perform an operation check. (3) Exchange a Main board and perform an operation check. (4) Exchange HDD and perform an operation check. * (5) Get USBLOG and contact service headquarters. * Only HDD standard model |
Error code: | F2BX, F2CX, F2DX |
Description: | Abnormality detecting in a network control part |
Remedy: | (1) Initialize HDD and perform an operation check. (FULL of U024) * ( 2) Carry out U021 Main backup initialization and perform an operation check. (3) Exchange a Main board and perform an operation check. (4) Get USBLOG and contact service headquarters. (Depending on an analysis result, it is packet capture acquisition) * Only HDD standard model |
Error code: | F2EX, F2FX, F30X |
Description: | Abnormality detecting in a network control part |
Remedy: | (1) Initialize HDD and perform an operation check. (FULL of U024) * ( 2) Carry out U021 Main backup initialization and perform an operation check. (3) Exchange a Main board and perform an operation check. (4) Get USBLOG and contact service headquarters. (Depending on an analysis result, it is packet capture acquisition) * Only HDD standard model |
Error code: | F31X, F32X |
Description: | Abnormality detecting in a network control part |
Remedy: | (1) Initialize HDD and perform an operation check. (FULL of U024) * ( 2) Carry out U021 Main backup initialization and perform an operation check. (3) Exchange a Main board and perform an operation check. (4) Get USBLOG and contact service headquarters. (Depending on an analysis result, it is packet capture acquisition) * Only HDD standard model |
Error code: | F35X |
Description: | An error is detected at the Print control section |
Remedy: | 1) Format the HDD and check function. (U024 FULL formatting) 2) Execute the U021 Memory initializing to initialize the controller backup memory and check function. 3) Replace the main board and check function. 4) Replace the HDD and check function. 5) Retrieve the USBLOG and contact the Service Administrative Division. |
Error code: | F38X |
Description: | An error is detected at the Authentication/permit management section |
Remedy: | 1) Format the HDD and check function. (U024 FULL formatting) 2) Execute the U021 Memory initializing to initialize the controller backup memory and check function. 3) Replace the main board and check function. 4) Replace the HDD and check function. 5) Retrieve the USBLOG and contact the Service Administrative Division. |
Error code: | F3AX, F3BX, F3CX |
Description: | Abnormality detecting in the Entity Management Department |
Remedy: | (1) Initialize HDD and perform an operation check. (FULL of U024) * ( 2) Carry out U021 Main backup initialization and perform an operation check. (3) Exchange a Main board and perform an operation check. (4) Exchange HDD and perform an operation check. * (5) Get USBLOG and contact service headquarters. * Only HDD standard model |
Error code: | F3DX, F3EX, F3FX |
Description: | Abnormality detecting in the Entity Management Department |
Remedy: | (1) Initialize HDD and perform an operation check. (FULL of U024) * ( 2) Carry out U021 Main backup initialization and perform an operation check. (3) Exchange a Main board and perform an operation check. (4) Exchange HDD and perform an operation check. * (5) Get USBLOG and contact service headquarters. * Only HDD standard model |
Error code: | F40X, F41X, F42X |
Description: | Abnormality detecting in the Entity Management Department |
Remedy: | (1) Initialize HDD and perform an operation check. (FULL of U024) * ( 2) Carry out U021 Main backup initialization and perform an operation check. (3) Exchange a Main board and perform an operation check. (4) Exchange HDD and perform an operation check. * (5) Get USBLOG and contact service headquarters. * Only HDD standard model |
Error code: | F43X, F44X, F45X |
Description: | Abnormality detecting in the Entity Management Department |
Remedy: | (1) Initialize HDD and perform an operation check. (FULL of U024) * ( 2) Carry out U021 Main backup initialization and perform an operation check. (3) Exchange a Main board and perform an operation check. (4) Exchange HDD and perform an operation check. * (5) Get USBLOG and contact service headquarters. * Only HDD standard model |
Error code: | F46X |
Description: | An error is detected at the Print image process section |
Remedy: | 1) Replace the main board and check function. 2) Retrieve the USBLOG (or retrieve the print capture data by case) |
Error code: | F47X |
Description: | Abnormality detecting of an image editing processing part |
Remedy: | (1) Initialize SSD and perform an operation check. * (2) Carry out U021 Main backup initialization and perform an operation check. (3) Exchange a Main board and perform an operation check. (4) Exchange SSD and perform an operation check. * (5) Get USBLOG and contact service headquarters. * Only SSD standard model |
Error code: | F4DX, F4EX |
Description: | An error is detected at the Entity control section |
Remedy: | 1) Format the HDD and check function. (U024 FULL formatting) 2) Execute the U021 Memory initializing to initialize the controller backup memory and check function. 3) Replace the main board and check function. 4) Replace the HDD and check function. 5) Retrieve the USBLOG and contact the Service Administrative Division. |
Error code: | F4FX |
Description: | An error is detected at the Job control section |
Remedy: | 1) Format the HDD and check function. (U024 FULL formatting) 2) Execute the U021 Memory initializing to initialize the controller backup memory and check function. 3) Replace the main board and check function. 4) Replace the HDD and check function. 5) Retrieve the USBLOG and contact the Service Administrative Division. |
Error code: | F51X, F52X, F53X |
Description: | Abnormality detecting in a JOB execution part |
Remedy: | (1) Initialize HDD and perform an operation check. (FULL of U024) * ( 2) Carry out U021 Main backup initialization and perform an operation check. (3) Exchange a Main board and perform an operation check. (4) Exchange HDD and perform an operation check. * (5) Get USBLOG and contact service headquarters. * Only HDD standard model |
Error code: | F55X, F56X, F57X |
Description: | Abnormality detecting in a JOB execution part |
Remedy: | (1) Initialize HDD and perform an operation check. (FULL of U024) * ( 2) Carry out U021 Main backup initialization and perform an operation check. (3) Exchange a Main board and perform an operation check. (4) Exchange HDD and perform an operation check. * (5) Get USBLOG and contact service headquarters. * Only HDD standard model |
Error code: | F5FX |
Description: | An error is detected at the Service execution section |
Remedy: | 1) Format the HDD and check function. (U024 FULL formatting) 2) Execute the U021 Memory initializing to initialize the controller backup memory and check function. 3) Replace the main board and check function. 4) Replace the HDD and check function. 5) Retrieve the USBLOG and contact the Service Administrative Division. |
Error code: | F62X |
Description: | An error is detected at the Service execution section |
Remedy: | 1) Format the HDD and check function. (U024 FULL formatting) 2) Execute the U021 Memory initializing to initialize the controller backup memory and check function. 3) Replace the main board and check function. 4) Replace the HDD and check function. 5) Retrieve the USBLOG and contact the Service Administrative Division. |
Error code: | F63X |
Description: | An error is detected at the Device control section |
Remedy: | 1) Format the HDD and check function. (U024 FULL formatting) 2) Execute the U021 Memory initializing to initialize the controller backup memory and check function. 3) Replace the main board and check function. 4) Replace the HDD and check function. 5) Retrieve the USBLOG and contact the Service Administrative Division. |