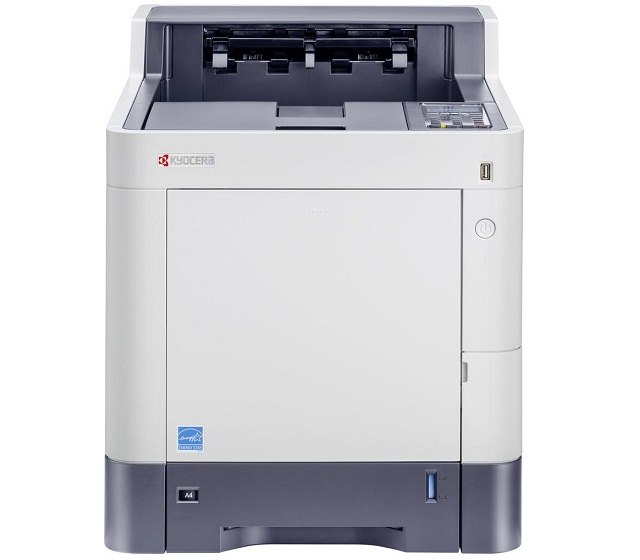
Kyocera ECOSYS P6035cdn
Рейтинг
Снят с производства
Тип устройства
Принтер
Технология печати
лазерная
Макс. формат
A4
Скорость печати
A4
35
Цветность печати
цветная
Общие характеристики |
|
---|---|
Тип |
лазерный/светодиодный |
Технология печати |
лазерная |
Печать фотографий |
|
Сканер |
|
Телефон |
|
Факс |
|
Копир |
|
Макс. формат |
A4 |
Тип устройства |
Принтер |
Цветность печати |
цветная |
Размещение |
настольный |
Принтер |
|
Макс, ширина отпечатка |
216 |
Система непрерывной подачи чернил |
|
Печать без полей |
|
Двусторонняя печать |
![]() |
Прямая печать |
![]() |
Пигментные чернила |
|
Время разогрева |
25 |
Количество цветов |
4 |
Макс, длина отпечатка |
356 |
Макс, разрешение для ч/б печати |
|
По X | 600 |
По Y | 600 |
Скорость ч/б печати |
|
A4 | 35 |
Макс, разрешение для цветной печати |
|
По X | 9 600 |
Время выхода первого отпечатка |
|
Цветн, | 7,5 |
Ч/б | 6,5 |
Сканер |
|
Стандарт TWAIN |
|
Слайд-адаптер |
|
Отправка изображения по e-mail |
|
Стандарт WIA |
|
Расходные материалы |
|
Количество картриджей |
4 |
Ресурс ч/б картриджа/тонера |
12 000 |
Ресурс цветного картриджа/тонера |
10 000 |
Печать на: |
|
Этикетках |
![]() |
Фотобумаге |
|
Матовой бумаге |
![]() |
Конвертах |
![]() |
Глянцевой бумаге |
![]() |
Пленках |
![]() |
Карточках |
![]() |
Рулоне |
|
CD/DVD |
|
Плотность бумаги |
|
Минимальная | 60 |
Максимальная | 220 |
Факс |
|
Цветной |
|
PC Fax |
|
Телефон |
|
Автоответчик |
|
Стандарт DECT |
|
АОН |
|
Беспроводная трубка |
|
Caller ID |
|
Проводная трубка |
|
Спикерфон |
|
Шрифты и языки управления |
|
Языки управления |
|
PCL 5c |
|
PostScript |
![]() |
PostScript 3 |
![]() |
PPDS |
|
![]() |
|
PostScript 2 |
|
PCL 6 |
![]() |
PCL 5e |
|
Количество установленных шрифтов |
|
PCL | 93 |
PostScript | 136 |
Лотки |
|
Емкость лотка ручной подачи |
100 |
Подача бумаги |
|
Максимальная | 2 100 |
Стандартная | 600 |
Вывод бумаги |
|
Максимальный | 500 |
Стандартный | 500 |
Финишер |
|
Степлер |
|
Брошюровщик |
|
Сортер |
|
Электронная сортировка |
|
Сортировка со сдвигом |
|
Интерфейсы |
|
AirPrint |
![]() |
Поддержка iOS |
![]() |
Веб-интерфейс |
![]() |
Устройство для чтения карт памяти |
![]() |
FireWire (IEEE 1394) |
|
Wi-Fi |
|
Wi-Fi 802.11n |
|
Bluetooth |
|
LPT |
|
Инфракрасный порт |
|
RS-232 |
|
USB |
![]() |
Ethernet (RJ-45) |
![]() |
Версия USB |
2,0 |
Поддержка карт памяти |
|
Secure Digital |
![]() |
MultiMedia Card |
![]() |
Память/Процессор |
|
Объем памяти |
512 |
Процессор |
Power PC 465S |
Макс, объем памяти |
2 048 |
Частота процессора |
1 000 |
Дополнительная информация |
|
Работа от аккумулятора |
|
Поддержка ОС |
|
Mac OS |
![]() |
Windows |
![]() |
DOS |
|
Linux |
![]() |
Потребляемая мощность |
|
При работе | 523 |
В режиме ожидания | 65 |
Уровень шума |
|
В режиме ожидания | 48 |
При работе | 51 |
Габариты |
|
Вес |
29 |
Высота |
469 |
Глубина |
532 |
Ширина |
390 |
Модули
PAPER FEED SECTION 2
Paper Feed Section 1
Image Formation Section
Laser Scanner Section
PAPER FEED
FRAME L
Conveying Section 1
TRANSFER SECTION
(Комплекты)
Electrical Components 1
PAPER CASSETTE
Fuser Section
DRIVE SECTION
ELECTRICAL COMPONENTS 2
Conveying Section 2
Developer Section
COVERS
PANEL
Operation Section
CASSETTE ASSEMBLY
Детали TRANSFER SECTION
Деталь: | SPRING PULLEY MPF |
Парткод: | 302NR08220 |
Деталь: | CAP SPRING/B-11 ENCLOSURE A4 |
Парткод: | 2FM04150 |
Деталь: | SHAFT EXIT |
Парткод: | 302NR28090 |
Деталь: | PULLEY FEED DU |
Парткод: | 302F929050 |
Деталь: | PARTS COVER MPF ASSY SP |
Парткод: | 302NR94210 |
Деталь: | FRAME MPF |
Парткод: | 302NR08040 |
Деталь: | PARTS PLATE BOTTOM MPF ASSY SP |
Парткод: | 302NR94220 |
Деталь: | PARTS SEPARATOR MPF ASSY SP |
Парткод: | 302NR94270 |
Деталь: | GUIDE MPF FEED LOW B |
Парткод: | 302NR08130 |
Деталь: | GUIDE MPF FEED LOW A |
Парткод: | 302NR08110 |

Деталь: | ROLLER M/P ASSY |
Парткод: | 302HS08260 |
Цена: | 700 ₽ |
Деталь: | GUIDE MPF FEED UP |
Парткод: | 302NR08101 |
Деталь: | PARTS SENSOR OPT. SP |
Парткод: | 302P794010 |
Деталь: | P.W.BOARD ASSY FUSER ZENER |
Парткод: | 302HN01240 |
Деталь: | P.W.BOARD ASSY FUSER ZENER |
Парткод: | 302J901030 |
Деталь: | PARTS PWB ASSY CASSETTE SP |
Парткод: | 302KV94340 |
Деталь: | FRAME FEED |
Парткод: | 302NR06511 |
Деталь: | GUIDE PICK HOLDER |
Парткод: | 302NR06210 |
Деталь: | SHAFT FEED |
Парткод: | 302KV06151 |
Деталь: | PARTS HOLDER FEED ASSY SP |
Парткод: | 302KV94191 |
Деталь: | PIN FEED |
Парткод: | 302KV06370 |
Деталь: | RELEASE ACTUATOR PE |
Парткод: | 302KV06180 |
Деталь: | SPRING ACTUATOR A |
Парткод: | 302KV06350 |
Деталь: | ACTUATOR B |
Парткод: | 302KV06341 |
Деталь: | SPRING ACT |
Парткод: | 302KV06201 |
Деталь: | PARTS MIDDLE ROLLER ASSY SP |
Парткод: | 302NR94250 |
Деталь: | COVER RETARD |
Парткод: | 302NR06040 |
Деталь: | GUIDE CASSETTE |
Парткод: | 302NT06010 |
Деталь: | ACTUATOR PE |
Парткод: | 302KV06170 |
Деталь: | PARTS ROLLER RETARD ASSY SP |
Парткод: | 302NG94110 |
Деталь: | HOLDER RETARD A |
Парткод: | 302NT06040 |
Деталь: | PARTS RETARD ASSY SP |
Парткод: | 302NT94060 |
Деталь: | MC-5140 |
Парткод: | 302NR93140 |
Деталь: | MC-5160 |
Парткод: | 302NT93130 |
Деталь: | DK-5140 |
Парткод: | 302NR93010 |
Деталь: | DK-5160 |
Парткод: | 302NT93010 |
Деталь: | LK-5140A |
Парткод: | 302NR93070 |
Деталь: | LK-5160A |
Парткод: | 302NT93070 |
Деталь: | LK-5140B |
Парткод: | 302NR93080 |
Деталь: | LK-5160B |
Парткод: | 302NT93080 |

Деталь: | Вал переноса заряда, в сборе |
Парткод: | 302NR94061 |
Цена: | 4 400 ₽ |

Деталь: | Блок проявки |
Парткод: | DV-5150C |
Цена: | 8 200 ₽ |

Деталь: | Блок проявки |
Парткод: | DV-5150K |
Цена: | 8 200 ₽ |

Деталь: | Блок проявки |
Парткод: | DV-5150M |
Цена: | 8 200 ₽ |

Деталь: | Блок проявки |
Парткод: | DV-5150Y |
Цена: | 8 700 ₽ |
Деталь: | Узел переноса заряда в драм-картридже, в сборе |
Парткод: | MC-5140 |
Цена: | 5 100 ₽ |

Деталь: | Узел переноса изображения |
Парткод: | TR-5140 |
Цена: | 12 100 ₽ |
Деталь: | PANEL UNIT, MFC9840CDW |
Парткод: | FK-5160 |
Цена: | 13 200 ₽ |
Деталь: | HOOK DU RELEASE |
Парткод: | 302NR29020 |
Деталь: | SHAFT EXIT |
Парткод: | 302NR28090 |
Деталь: | LABEL PUSH |
Парткод: | 302MC34040 |
Деталь: | CAP SPRING/B-11 ENCLOSURE A4 |
Парткод: | 2FM04150 |
Деталь: | PARTS PWB ASSY EXIT SP |
Парткод: | 302NR94130 |
Деталь: | PARTS PWB ASSY EXIT SP |
Парткод: | 302NS94050 |
Деталь: | LABEL PUSH SET |
Парткод: | 302NR34090 |
Деталь: | FAN MOTOR |
Парткод: | 302HN44210 |
Деталь: | PARTS,FAN COOLING CONVEYING SP |
Парткод: | 302FZ94420 |
Деталь: | PARTS REAR COVER 250 PRT ASSY SP |
Парткод: | 302NR94230 |
Деталь: | PARTS REAR COVER 500 PRT ASSY SP |
Парткод: | 302NS94080 |
Деталь: | PARTS REAR COVER 500 PRT ASSY EU SP |
Парткод: | 302NT94070 |
Деталь: | TR-5140 |
Парткод: | 302NR93060 |
Деталь: | TR-5160 |
Парткод: | 302NT93060 |
Деталь: | Комплект для технического обслуживания |
Парткод: | MK-5150 |
Цена: | 51 200 ₽ |
Деталь: | 2NR94110 |
Парткод: | 302NR94110 |
Деталь: | 2NS94040 |
Парткод: | 302NS94040 |
Деталь: | 2NT94030 |
Парткод: | 302NT94030 |
Деталь: | 2NR94020 |
Парткод: | 302NR94020 |
Деталь: | 3NW94040 |
Парткод: | 303NW94040 |
Деталь: | 2NR94080 |
Парткод: | 302NR94080 |
Деталь: | 2NR94200 |
Парткод: | 302NR94200 |
Деталь: | 2NR94100 |
Парткод: | 302NR94100 |
Деталь: | SP136500 |
Парткод: | 7SP01000004+H01 |
Деталь: | 2NR33020 |
Парткод: | 302NR33020 |
Деталь: | 2NG94050 |
Парткод: | 302NG94050 |
Деталь: | 2NR94120 |
Парткод: | 302NR94120 |
Деталь: | 2NT94020 |
Парткод: | 302NT94020 |
Деталь: | 2NS02192 |
Парткод: | 302NS02192 |
Деталь: | 2HN44180 |
Парткод: | 302HN44180 |
Деталь: | 2NR31080 |
Парткод: | 302NR31080 |
Деталь: | 2KV02B80 |
Парткод: | 302KV02B80 |
Деталь: | 2NR02930 |
Парткод: | 302NR02930 |
Деталь: | 2NS02230 |
Парткод: | 302NS02230 |
Деталь: | 2NR94090 |
Парткод: | 302NR94090 |
Деталь: | 2NR31570 |
Парткод: | 302NR31570 |
Деталь: | 2NR02170 |
Парткод: | 302NR02170 |
Деталь: | 2NR02330 |
Парткод: | 302NR02330 |
Деталь: | 2NR02340 |
Парткод: | 302NR02340 |
Деталь: | 2FZ94420 |
Парткод: | 302FZ94420 |
Деталь: | 2NT94090 |
Парткод: | 302NT94090 |
Деталь: | 3MH04040 |
Парткод: | 303MH04040 |
Деталь: | GEAR Z13S JOINT |
Парткод: | 302HN09170 |
Деталь: | GEAR Z13 |
Парткод: | 302KV09250 |
Деталь: | WORKPLATE LIFT |
Парткод: | 302NR09070 |
Деталь: | GEAR Z48S LIFT |
Парткод: | 302NT09100 |
Деталь: | CT-5140 |
Парткод: | 302NR93120 |
Деталь: | FK-5140 |
Парткод: | 302NR93090 |
Деталь: | FK-5142 |
Парткод: | 302NR93110 |
Деталь: | FK-5141 |
Парткод: | 302NR93100 |
Деталь: | FK-5160 |
Парткод: | 302NT93090 |
Деталь: | FK-5162 |
Парткод: | 302NT93110 |
Деталь: | FK-5170 |
Парткод: | 302NT93160 |
Деталь: | FK-5171 |
Парткод: | 302NT93170 |
Деталь: | FK-5172 |
Парткод: | 302NT93180 |
Деталь: | DR-5140 |
Парткод: | 302NR93130 |
Деталь: | DR-5150 |
Парткод: | 302NT93120 |
Деталь: | DR-5160 |
Парткод: | 302NT93210 |
Деталь: | BUSH DRIVE |
Парткод: | 302KV31410 |
Цена: | 40 ₽ |
Деталь: | GEAR Z23L |
Парткод: | 302KV31440 |
Деталь: | HOUSING MPF DRIVE A |
Парткод: | 302NR31150 |
Деталь: | SPRING INPUT MPF |
Парткод: | 302HN31650 |
Цена: | 150 ₽ |
Деталь: | SOLENOID TONER |
Парткод: | 302GR44150 |
Цена: | 400 ₽ |
Деталь: | GEAR Z14L MPF |
Парткод: | 302NR31810 |
Деталь: | GEAR Z31R-Z24S |
Парткод: | 302NR31180 |
Деталь: | GEAR INPUT A Z36S |
Парткод: | 302NR31190 |
Деталь: | GEAR INPUT B Z36S |
Парткод: | 302NR31200 |
Деталь: | HOUSING MPF DRIVE B |
Парткод: | 302NR31160 |
Деталь: | PIN DRIVE MPF A |
Парткод: | 302NR31210 |
Деталь: | CAM MPF |
Парткод: | 302NR31630 |
Деталь: | GEAR Z24L |
Парткод: | 302NR31060 |
Деталь: | PARTS MOTOR-BL W20 SP |
Парткод: | 302K994323 |
Деталь: | PARTS MOTOR-PM MOVING SP |
Парткод: | 303NB94040 |
Деталь: | GEAR Z44R-Z16S |
Парткод: | 302NR31250 |
Деталь: | GEAR Z35R |
Парткод: | 302NR31230 |
Деталь: | GEAR Z26S |
Парткод: | 302NR31260 |
Деталь: | GEAR Z63R-Z24R |
Парткод: | 302NR31240 |
Деталь: | PLATE MIDDLE DRIVE |
Парткод: | 302NR31220 |
Деталь: | PARTS FAN MOTOR SP |
Парткод: | 302NG94220 |
Деталь: | PARTS MOTOR-BL W10 SP |
Парткод: | 302LC94291 |

Деталь: | PARTS CLUTCH 35 Z35R SP |
Парткод: | 302NR94010 |

Деталь: | CLUTCH 50 Z35R |
Парткод: | 302KV44041 |
Цена: | 900 ₽ |
Деталь: | PARTS MOTOR EJECT SP |
Парткод: | 302P794060 |
Деталь: | PARTS MOTOR-PM FUSER SP |
Парткод: | 302NT94140 |
Деталь: | PLATE MIDDLE DRIVE A |
Парткод: | 302NT31090 |
Деталь: | GEAR Z43R-Z16S |
Парткод: | 302NT31100 |
Деталь: | GEAR Z26S |
Парткод: | 302NT31110 |
Деталь: | PARTS FEED DRIVE ASSY SP |
Парткод: | 302NR94260 |
Деталь: | PARTS FEED DRIVE ASSY SP |
Парткод: | 302NT94081 |
Деталь: | PARTS PWB ASSY MAIN SP |
Парткод: | 302NR94170 |
Деталь: | PARTS PWB ASSY MAIN EU SP |
Парткод: | 302NR94180 |
Деталь: | PARTS PWB ASSY MAIN JP SP |
Парткод: | 302NR94280 |
Деталь: | PARTS PWB ASSY MAIN SP |
Парткод: | 302NS94060 |
Деталь: | PARTS PWB ASSY MAIN EU SP |
Парткод: | 302NS94070 |
Деталь: | PARTS PWB ASSY MAIN SP |
Парткод: | 302NT94040 |
Деталь: | PARTS PWB ASSY MAIN EU SP |
Парткод: | 302NT94050 |
Деталь: | PARTS PWB ASSY MAIN JP SP |
Парткод: | 302NT94100 |
Деталь: | PARTS HIGH VOLTAGE UNIT SP |
Парткод: | 302NR94030 |
Деталь: | PARTS HIGH VOLTAGE UNIT SP |
Парткод: | 302NT94010 |
Деталь: | PARTS SWITCHING REGULATOR 230V SP |
Парткод: | 302NR94050 |
Деталь: | PARTS SWITCHING REGULATOR 230V SP |
Парткод: | 302NS94020 |
Деталь: | PARTS SWITCHING REGULATOR 100V SP |
Парткод: | 302NR94040 |
Деталь: | PARTS SWITCHING REGULATOR 100V SP |
Парткод: | 302NS94010 |
Деталь: | SW. MICRO |
Парткод: | 7SM010104+++H01 |
Деталь: | PARTS,FAN COOLING CONVEYING SP |
Парткод: | 302FZ94420 |
Деталь: | SW.PUSH |
Парткод: | 7SP01000004+H01 |
Деталь: | PARTS PWB ASSY SWITCH SP |
Парткод: | 302NR94160 |
Деталь: | BRACKET FRONT HV |
Парткод: | 302NR39011 |
Деталь: | PARTS SENSOR OPT. SP |
Парткод: | 302P794010 |
Деталь: | FOOT |
Парткод: | 302HN02611 |
Деталь: | LEVER INTERLOCK |
Парткод: | 302NR02140 |
Деталь: | PARTS TONER FULL DETECT ASSY SP |
Парткод: | 302NR94070 |
Деталь: | GUIDE TOP RIGHT |
Парткод: | 302NR02180 |
Деталь: | PARTS PWB ASSY THERMISTOR SP |
Парткод: | 302M294130 |
Деталь: | PARTS HVU2 SP |
Парткод: | 302K094271 |
Деталь: | WT-5140 |
Парткод: | 302NR93150 |
Деталь: | AC CORD ASSY JP |
Парткод: | 7AAACCJP+15H007 |
Деталь: | POWER CORD(120) |
Парткод: | 3019527401 |
Деталь: | PARTS AC CORD EU SP |
Парткод: | 302FV94010 |
Деталь: | AC CORD ASSY |
Парткод: | 302FV45040 |
Деталь: | FAN MOTOR |
Парткод: | 302HN44210 |
Деталь: | PARTS ROLLER TRANSFER SP |
Парткод: | 302NR94060 |
Деталь: | PARTS CONVEYING 250 ASSY SP |
Парткод: | 302NR94190 |
Деталь: | PARTS CONVEYING 500 ASSY SP |
Парткод: | 302NS94100 |
Деталь: | PARTS CONVEYING 500 SI ASSY SP |
Парткод: | 302NT94130 |
Деталь: | DV-5140(K) |
Парткод: | 302NR93020 |
Деталь: | DV-5150(K) |
Парткод: | 302NS93010 |
Деталь: | DV-5160(K) |
Парткод: | 302NT93020 |
Деталь: | DV-5140(M) |
Парткод: | 302NR93040 |
Деталь: | DV-5150(M) |
Парткод: | 302NS93030 |
Деталь: | DV-5160(M) |
Парткод: | 302NT93040 |
Деталь: | DV-5140(C) |
Парткод: | 302NR93050 |
Деталь: | DV-5150(C) |
Парткод: | 302NS93040 |
Деталь: | DV-5160(C) |
Парткод: | 302NT93050 |
Деталь: | DV-5140(Y) |
Парткод: | 302NR93030 |
Деталь: | DV-5150(Y) |
Парткод: | 302NS93020 |
Деталь: | DV-5160(Y) |
Парткод: | 302NT93030 |
Деталь: | COVER LEFT |
Парткод: | 302NR04030 |
Деталь: | COVER FRONT |
Парткод: | 302NR04050 |
Деталь: | COVER MEMORY |
Парткод: | 302NR04190 |
Деталь: | COVER WASTE |
Парткод: | 302NR04090 |
Деталь: | COVER FRONT UPPER |
Парткод: | 302NR04080 |
Деталь: | HOLDER MAIN SWITCH |
Парткод: | 302NR04250 |
Деталь: | STRAP COVER REAR |
Парткод: | 302KV04130 |
Деталь: | KEY SW |
Парткод: | 3V2LV04180 |
Деталь: | LUTCH |
Парткод: | 302HN08140 |
Деталь: | COVER RIGHT BOTTOM |
Парткод: | 302NS04180 |
Деталь: | COVER RIGHT |
Парткод: | 302NR04040 |
Деталь: | COVER RIGHT UPPER |
Парткод: | 302NR04070 |
Деталь: | COVER RIGHT UPPER |
Парткод: | 302NS04070 |
Деталь: | COVER LEFT UPPER |
Парткод: | 302NR04060 |
Деталь: | COVER LEFT UPPER |
Парткод: | 302NS04060 |
Деталь: | COVER INNER LEFT |
Парткод: | 302NR04140 |
Деталь: | COVER WASTE LOW |
Парткод: | 302NS04100 |
Деталь: | COVER INNER RIGHT |
Парткод: | 302NR04150 |
Деталь: | Label JAM |
Парткод: | 302NR34020 |
Деталь: | COVER CONNECTOR |
Парткод: | 302NR04110 |
Деталь: | LID TOP PRINTER |
Парткод: | 302NR04020 |
Деталь: | COVER LEFT BOTTOM |
Парткод: | 302NS04170 |
Деталь: | DUCT LID TOP |
Парткод: | 302NR04210 |
Деталь: | COVER TOP |
Парткод: | 302NR04010 |
Деталь: | COVER TOP |
Парткод: | 302NS04011 |
Деталь: | SHEET EMBLEM |
Парткод: | 302NR34010 |
Деталь: | SEAL LID TOP A |
Парткод: | 302NT04010 |
Деталь: | SEAL LID TOP B |
Парткод: | 302NT04020 |
Деталь: | STAY LID TOP |
Парткод: | 302NR04220 |
Деталь: | Блок лазера |
Парткод: | LK-5140A |
Цена: | 16 200 ₽ |
Деталь: | Блок лазера |
Парткод: | LK-5140B |
Цена: | 13 100 ₽ |
Деталь: | PARTS PWB ASSY LCDCONT SP |
Парткод: | 302NR94140 |
Деталь: | PARTS PWB ASSY LCDCONT SP |
Парткод: | 302NS94030 |
Деталь: | COVER OPERATION |
Парткод: | 302NR05010 |
Деталь: | COVER OPERATION |
Парткод: | 302NS05010 |
Деталь: | STOPPER PANEL |
Парткод: | 302NR05080 |
Деталь: | SHEET OPE |
Парткод: | 302NR05200 |
Деталь: | SHEET OPE ENG |
Парткод: | 302NR05210 |
Деталь: | SHEET OPE |
Парткод: | 302NS05200 |
Деталь: | SHEET OPE ENG |
Парткод: | 302NS05210 |
Деталь: | COVER PANEL |
Парткод: | 302NR05070 |
Деталь: | COVER PANEL |
Парткод: | 302NS05040 |
Деталь: | COVER PANEL |
Парткод: | 302NT05010 |
Деталь: | PARTS OPERATION ASSY SP |
Парткод: | 302NR94240 |
Деталь: | PARTS OPERATION ASSY SP |
Парткод: | 302NS94090 |

Деталь: | Узел подачи бумаги из кассеты, в сборе |
Парткод: | 302KV94192 |
Цена: | 2 800 ₽ |

Деталь: | Узел отделения бумаги из кассеты, в сборе |
Парткод: | 302NT94062 |
Цена: | 6 000 ₽ |
Коды ошибок
0100
0120
0130
0140
0150
0160
0170
0190
0360
0800
0840
1010
1020
1030
1040
1810
1820
1830
1900
1910
1920
2101
2111
2201
2202
2211
2212
2500
2600
2610
2620
2760
2820
4001
4002
4011
4012
4101
4102
4103
4104
4201
4202
4203
4204
4600
4700
5101
5102
5103
5104
6000
6020
6030
6040
6050
6200
6220
6230
6250
6400
6610
7001
7002
7003
7004
7101
7102
7103
7104
7200
7221
7222
7401
7402
7403
7404
7411
7412
7413
7414
7601
7602
7611
7612
7613
7614
7620
7800
7901
7902
7903
7904
7911
7912
7913
7914
F000
F010
F020
F040
F050
Описание
Error code: | 0100 |
Display: | MAINTENANCE CALL 0100 |
Description: | Backup memory device error |
Causes: | Defective flash memory. Defective main PWB. |
Remedy: | EEPROM (main PWB) 1. Turn the main power swtch off and after 5 seconds, then turn power on. 2. Check that the EEPROM on the main circuit PWB is peroperly installed on the main circuit PWB and, if not, re-install it. 3. Replace the main PWB |
Error code: | 0120 |
Description: | There is a problem with Thermistor for Pre-Heater. |
Causes: | Thermistor Cable has short circuited or cutline. Thermistor has a problem. |
Remedy: | Check Cable connection around Thermistor Thermistor replacement |
Error code: | 0130 |
Description: | There is a problem with Thermistor for Print Heater. |
Causes: | Thermistor cable has short circuited or cutline. Thermistor has a problem. |
Remedy: | Check Cable connection around Thermistor Thermistor replacement |
Error code: | 0140 |
Description: | There is a problem with Thermistor for dryer. |
Causes: | Thermistor cable has short circuited or cutline. Thermistor has a problem. |
Remedy: | Check Cable connection around Thermistor Thermistor replacement |
Error code: | 0150 |
Description: | Even though the machine carries out the regular movement, the output of Slider Sensor does not reach the expected value. |
Causes: | Slider Motor has a problem. Slider Sensor has a problem. Wiring or Flexible Cable has short circuitted or cut-line. Servo Board has a problem. |
Remedy: | Check Cable connection of Servo Board Check Cable connection of Junction Board Slider Motor replacement Slider Sensor replacement Wiring or Flexible Cable replacement Servo Board replacement |
Error code: | 0160 |
Description: | Even though the machine carries out the regular movement, the output of Pressure Pump 1 Sensor does not reach the expected value. |
Causes: | Pressure Pump 1 Motor has a problem. Pressure Pump 1 Sensor has a problem. Pressure Pump 1 Magnet has dropped out. Wiring or Flexible Cable has short circuitted or cut-line. Pump Drive Board has a problem. Servo Board has a problem. |
Remedy: | Check Cable connection of Servo Board Check Cable connection of Junction Board Check Pressure Pump 1 Magnet Pressure Pump 1 Motor replacement Pressure Pump 1 Sensor replacement Wiring or Flexible Cable replacement Pump Drive Board replacement Servo Board replacement |
Error code: | 0170 |
Description: | Even though the machine carries out the regular movement, the output of Supply Pump 1 Sensor does not reach the expected value. |
Causes: | Supply Pump 1 Motor has a problem. Supply Pump 1 Sensor has a problem. Supply Pump 1 Magnet has dropped out. Wiring or Flexible Cable has short circuitted or cut-line. Pump Drive Board has a problem. Servo Board has a problem. |
Remedy: | Check Cable connection of Servo Board Check Cable connection of Junction Board Check Supply Pump 1 Magnet Supply Pump 1 Motor replacement Supply Pump 1 Sensor replacement Wiring or Flexible Cable replacement Pump Drive Board replacement Servo Board replacement |
Error code: | 0190 |
Description: | Thermistor under the BED has a problem. |
Causes: | Device has a problem. Thermistor Cable has short circuited or cutline. |
Remedy: | Thermistor replacement Check Cable connection Heater Board replacement |
Error code: | 0360 |
Description: | Communication error between the engine ASIC During the readback data checked after data transmission, the checksum error or the video signal is not inverted. (failed 10 consecutive times) |
Causes: | Defective connector cable or poor contact in the connector. Engine relay PWB Main/Engine PWB |
Remedy: | Engine PWB: 1. Unplug the power cord from the wall outlet, and wait five seconds. Then plug in the power cord and then turn on the power switch. 2. Check that the connectors on the engine PWB are properly connected, and if not, re-connect them. 3. Replace the engine PWB. |
Error code: | 0800 |
Display: | Print Unable 08 Turn the power off and then back on again. |
Description: | Image processing error JAM010X is detected twice. |
Causes: | Defective main PWB. |
Remedy: | Main PWB Replace the main PWB. |
Error code: | 0840 |
Description: | Faults of RTC (“Time for maintenance T” is displayed) [Check at power up] The RTC setting has reverted to a previous state. The machine has not been powered for 5 years (compared to the settings stored periodically in the EEPROM). The RTC setting is older than 00:01 on January 1, 2000. [Checked periodically (in 5- minute interval) after powered up] The RTC setting has reverted to a state older than the last time it was checked. 10 minutes have been passed since the previous check. After C840 is detected, the machine enters in disconnection mode after the main power switch has been switched on and off and indicates ‘Maintenance T.’ |
Causes: | The battery is disconnected from the main PWB Defective main PWB. |
Remedy: | Battery (main PWB) 1. Make sure that the back-up batteries on the main PWB are not short-circuited. 2. Reset Maintenance T by executing U906. 3. If the same C call is displayed when power is switched on and off, replace the back up battery. 4. If communication error (due to a noise, etc.) is present with the RTC on the main circuit PWB, check the PWB is properly grounded. Main PWB Replace the main PWB |
Error code: | 1010 |
Display: | Problem with Printhead L/R Chk printing results |
Description: | Lift motor 1 error After cassette 1 is inserted, lift sensor 1 does not turn on within 12 s. This error is detected 4 times successively. The lock signal of the motor is detected continuously for 1 s. This error is detected 4 times successively. |
Causes: | Defective bottom plate elevation mechanism in the cassette. Defective connector cable or poor contact in the connector. Defective drive transmission system of motor. Defective lift motor 1. Defective engine PWB. |
Remedy: | Cassette lift base elevating mechanism Check that the cassette base can be manipulated smoothly, if not, repair or replace. Lift motor 1 1. Check that the cassette base has been ascended. 2. Check the drive gear can rotate or they are not unusually loaded and, if necessary, replace. 3. Confirm that the wiring connector is firmly connected and, if necessary, connect the connector all the way in. Lift motor 1 and Feed PWB 2 (YC3) Feed PWB 2 (YC1) and Engine PWB (YC4) 4. If the wiring is disconnected, shorted or grounded, replace the wiring. 5. Replace the lift motor 1. Lift sensor 1 1. Check that the sensor is correctly positioned. 2. Confirm that the wiring connector is firmly connected and, if necessary, connect the connector all the way in. Lift sensor 1 and Feed PWB 2 (YC8) Feed PWB 2 (YC1) and Engine PWB (YC4) 3. If the wiring is disconnected, shorted or grounded, replace the wiring. 4. Replace the lift sensor1. Feed PWB 2 Replace the Feed PWB 2. Engine PWB 1. Check the engine software and upgrade to the latest, if necessary. 2. Replace the engine PWB. |
Error code: | 1020 |
Description: | Lift motor 2 error After cassette 2 is inserted, lift sensor 2 does not turn on within 12 s. This error is detected 4 times successively. The lock signal of the motor is detected continuously for 1 s. This error is detected 4 times successively. |
Causes: | Defective bottom plate elevation mechanism in the cassette. Defective connector cable or poor contact in the connector. Defective drive transmission system of motor. Defective lift motor 2. Defective engine PWB. |
Remedy: | Cassette lift base elevating mechanism Check that the cassette base can be manipulated smoothly, if not, repair or replace. Lift motor 2 1. Check that the cassette base has been ascended. 2. Check the drive gear can rotate or they are not unusually loaded and, if necessary, replace. 3. Confirm that the wiring connector is firmly connected and, if necessary, connect the connector all the way in. Lift motor 2 and Feed PWB 2 (YC3) Feed PWB 2 (YC1) and Engine PWB (YC4) 4. If the wiring is disconnected, shorted or grounded, replace the wiring. 5. Replace the lift motor 2. Lift sensor 2 1. Check that the sensor is correctly positioned. 2. Confirm that the wiring connector is firmly connected and, if necessary, connect the connector all the way in. Lift sensor 2 and Feed PWB 2 (YC8) Feed PWB 2 (YC1) and Engine PWB (YC4) 3. If the wiring is disconnected, shorted or grounded, replace the wiring. 4. Replace the lift sensor2. Feed PWB 2 Replace the Feed PWB 2. Engine PWB 1. Check the engine software and upgrade to the latest, if necessary. 2. Replace the engine PWB. |
Error code: | 1030 |
Display: | GARO W1221 |
Description: | PF lift motor 1 error (paper feeder) After cassette 3 is inserted, PF lift sensor 1 does not turn on within 12 s. This error is detected 5 times successively. During driving the motor, the lift overcurrent protective monitor signal is detected for 1 s or more 5 times successively. However, the first 1 s after motor is turned on is excluded from detection. |
Causes: | Defective bottom plate elevation mechanism in the cassette. Defective connector cable or poor contact in the connector. Defective drive transmission system of motor. Defective PF lift motor 1. Defective PF main PWB. |
Remedy: | Defective bottom plate elevation mechanism in the cassette. Check to see if the bottom plate can move smoothly and repair it if any problem is found. Defective connector cable or poor contact in the connector. Reinsert the connector. Also check for continuity within the connector cable. If none, replace the cable. PF lift motor 1 and PF main PWB (YC7) Defective drive transmission system of motor. Check if the gears rotate smoothly. If not, grease the bushes and gears. Check for broken gears and replace if any. Defective PF lift motor 1. Replace the PF lift motor 1. Defective PF main PWB. Replace the PF main PWB (Refer to the service manual for the paper feeder). |
Error code: | 1040 |
Display: | GL2: W0501 The memory is full. |
Description: | PF lift motor 2 error (paper feeder) After cassette 4 is inserted, PF lift sensor 2 does not turn on within 12 s. This error is detected 5 times successively. During driving the motor, the lift overcurrent protective monitor signal is detected for 1 s or more 5 times successively. However, the first 1 s after motor is turned on is excluded from detection. |
Causes: | Defective bottom plate elevation mechanism in the cassette. Defective connector cable or poor contact in the connector. Defective drive transmission system of motor. Defective PF lift motor 2. Defective PF main PWB. |
Remedy: | Defective bottom plate elevation mechanism in the cassette. Check to see if the bottom plate can move smoothly and repair it if any problem is found. Defective connector cable or poor contact in the connector. Reinsert the connector. Also check for continuity within the connector cable. If none, replace the cable. PF lift motor 2 and PF main PWB (YC7) Defective drive transmission system of motor. Check if the gears rotate smoothly. If not, grease the bushes and gears. Check for broken gears and replace if any. Defective PF lift motor 2. Replace the PF lift motor 2. Defective PF main PWB. Replace the PF main PWB (Refer to the service manual for the paper feeder). |
Error code: | 1810 |
Description: | Side multi tray communication error A communication error from side multi tray is detected 10 times in succession. |
Causes: | Improper installation side multi tray. Defective connector cable or poor contact in the connector. Defective engine PWB. Defective SM main PWB. |
Remedy: | Side multi tray Check the wiring connection status with the main unit and, if necessary, try connecting it again. SM main PWB 1. Confirm that the wiring connector is firmly connected and, if necessary, connect the connector all the way in. SM main PWB (YC1) and Engine PWB (YC19) 2. If the wiring is disconnected, shorted or grounded, replace the wiring. 3. Replace the SM main PWB (Refer to the service manual for the paper feeder). Engine PWB Check the engine software and upgrade to the latest, if necessary. Replace the engine PWB. SM main PWB Replace the SM main PWB (Refer to the service manual for the paper feeder). |
Error code: | 1820 |
Description: | Side paper feeder communication error A communication error from paper feeder is detected 10 times in succession. |
Causes: | Improper installation side paper feeder. Defective connector cable or poor contact in the connector. Defective engine PWB. Defective SM main PWB. Defective PF main PWB. |
Remedy: | Side paper feeder Check the wiring connection status with the main unit and, if necessary, try connecting it again. SM main PWB 1. Confirm that the wiring connector is firmly connected and, if necessary, connect the connector all the way in. SM main PWB (YC1) and Engine PWB (YC19) 2. If the wiring is disconnected, shorted or grounded, replace the wiring. 3. Replace the SM main PWB (Refer to the service manual for the paper feeder). PF main PWB 1. Confirm that the wiring connector is firmly connected and, if necessary, connect the connector all the way in. PF main PWB (YC13) and SM main PWB (YC4) 2. If the wiring is disconnected, shorted or grounded, replace the wiring. 3. Replace the PF main PWB (Refer to the service manual for the paper feeder). Engine PWB 1. Check the engine software and upgrade to the latest, if necessary. 2. Replace the engine PWB. |
Error code: | 1830 |
Description: | Paper feeder communication error (third cassette) A communication error from paper feeder is detected 10 times in succession. |
Remedy: | Paper feeder 3 Check the wiring connection status with PF2, and if necessary, reconnect it. PF3 main PWB 1. Confirm that the wiring connector is firmly connected, and if necessary, connect the connector all the way in. PF2 main PWB (YC3 and PF3 main PWB (YC5,4) 2. If the wiring is disconnected, short-circuited or has ground fault, replace the wire. 3. Reinstall the PF firmware. 4. Replace the PF3 main PWB. PF2 main PWB Replace the PF2 main PWB. |
Error code: | 1900 |
Description: | Paper feeder EEPROM error When writing the data, read and write data does not match 3 times in succession. |
Causes: | Defective PF main PWB. Device damage of EEPROM. |
Remedy: | PF main PWB (EEPROM) 1. Confirm that the wiring connector is firmly connected and, if necessary, connect the connector all the way in. 2. Replace the PF main PWB (Refer to the service manual for the paper feeder). |
Error code: | 1910 |
Description: | Side multi tray EEPROM error When writing the data, read and write data does not match 3 times in succession. |
Causes: | Defective SM main PWB. Device damage of EEPROM. |
Remedy: | SM main PWB (EEPROM) 1. Confirm that the wiring connector is firmly connected and, if necessary, connect the connector all the way in. 2. Replace the SM main PWB (Refer to the service manual for the paper feeder). |
Error code: | 1920 |
Description: | Side paper feeder EEPROM error When writing the data, read and write data does not match 3 times in succession. |
Causes: | Defective PF main PWB. Device damage of EEPROM. |
Remedy: | PF main PWB 1. Confirm that the wiring connector is firmly connected and, if necessary, connect the connector all the way in. 2. Replace the PF main PWB (Refer to the service manual for the paper feeder). |
Error code: | 2101 |
Description: | Developer motor error After developer motor is driven, the ready signal does not turn to L within 2 s. After developer motor is stabilized, the ready signal is at the H level for 1 s continuously. |
Causes: | Defective connector cable or poor contact in the connector. Defective drive transmission system of motor. Defective developer motor. Defective engine PWB. |
Remedy: | Developer unit 1. Check that the developer waste lock has been released and, if not, release the lock. 2. Check that the gears and spiral screw of the developer unit are not damaged. 3. Confirm that the developer roller can rotate. 4. If it won`t rotate, replace the developer unit. Developer motor 1. To check the motor operation, execute DLP(K) by U030. 2. Check the drive gear can rotate or they are not unusually loaded and, if necessary, replace. 3. Confirm that the wiring connector is firmly connected and, if necessary, connect the connector all the way in. Developer motor and Feed PWB 1 (YC8) Feed PWB 1 (YC2) and Engine PWB (YC5) 4. If the wiring is disconnected, shorted or grounded, replace the wiring. 5. Replace the Developer motor. Engine PWB. 1. Check the engine software and upgrade to the latest, if necessary. 2. Replace the engine PWB. |
Error code: | 2111 |
Description: | Developer motor startup error (C,M,Y) After the motor starting, the stable signal is not turned ON within 3 s. |
Remedy: | Developer unit 1. Check that the developer roller can be rotated by hand, and if it is locked, replace the developer unit. Developer motor 1. Check if the couplings and gears rotate smoothly, and if necessary replace them. 2. Reinsert the connector. 3. Check continuity within the connector wire. If none, replace the wire. Developer motor and Engine relay PWB (YC12) Engine relay PWB (YC1) and Main/ Engine PWB (YC4) 4. Replace the developer motor Engine relay PWB Replace the engine relay PWB. Main/Engine PWB 1. Check the engine firmware and upgrade to the latest version if necessary. 2. Replace the Main/Engine PWB. |
Error code: | 2201 |
Description: | drum motor steady-state error After drum motor is stabilized, the ready signal is at the H level for 1 s continuously. |
Causes: | Defective connector cable or poor contact in the connector. Defective drive transmission system of motor. Defective drum motor. Defective engine PWB. |
Remedy: | Drum unit 1. Confirm that the drum or the drum screw can rotate. 2. If it won’t rotate, replace the drum unit. Drum motor 1. Check the drive gear can rotate or they are not unusually loaded and, if necessary, replace. 2. Confirm that the wiring connector is firmly connected and, if necessary, connect the connector all the way in. drum motor and Feed PWB 1 (YC9) Feed PWB 1 (YC2) and Engine PWB (YC5) 3. If the wiring is disconnected, shorted or grounded, replace the wiring. 4. Replace the drum motor. Engine PWB 1. Check the engine software and upgrade to the latest, if necessary. 2. Replace the engine PWB. |
Error code: | 2202 |
Description: | Drum motor C steady-state error The motor revolution fluctuates more than +/-6.2% of the normal revolution for 5s continuously, after the drum motor C has stabilized. The counter achieved by timer capture is less than 2200 in 10 times in a row. |
Causes: | Defective connector cable or poor contact in the connector. Defective drive transmission system of motor. Defective drum motor C. Defective engine PWB. |
Remedy: | Drum unit 1. Execute U030 Belt Meand (transfer Motor) and check that the drum motor can rotate. 2. Check the drive gear can rotate or they are not unusually loaded and, if necessary, replace. 3. Confirm that the drum or the drum screw can rotate. 4. If it won’t rotate, replace the drum unit. Drum motor C 1. Confirm that the wiring connector is firmly connected and, if necessary, connect the connector all the way in. Drum motor C and Motor control PWB (YC4) Motor control PWB (YC3) and Engine PWB (YC9) 2. If the wiring is disconnected, shorted or grounded, replace the wiring. 3. Replace the Drum motor C. Motor control PWB Replace the Motor control PWB Engine PWB 1. Check the engine software and upgrade to the latest, if necessary. 2. Replace the engine PWB. |
Error code: | 2211 |
Description: | Drum motor startup error Drum motor is not stabilized within 2 s since the motor is activated. |
Causes: | Defective connector cable or poor contact in the connector. Defective drive transmission system of motor. Defective drum motor K. Defective engine PWB. |
Remedy: | Drum unit 1. Check the drive gear can rotate or they are not unusually loaded and, if necessary, replace. 2. Confirm that the drum or the drum screw can rotate. 3. If it won’t rotate, replace the drum unit. Drum motor 1. Confirm that the wiring connector is firmly connected and, if necessary, connect the connector all the way in. drum motor and Feed PWB 1 (YC9) Feed PWB 1 (YC2) and Engine PWB (YC5) 2. If the wiring is disconnected, shorted or grounded, replace the wiring. 3. Replace the drum motor. Engine PWB 1. Check the engine software and upgrade to the latest, if necessary. 2. Replace the engine PWB. |
Error code: | 2212 |
Description: | Drum motor C startup error Drum motor C is not stabilized within 5 s since the motor is activated. |
Causes: | Defective connector cable or poor contact in the connector. Defective drive transmission system of motor. Defective drum motor C. Defective engine PWB. |
Remedy: | Drum unit 1. To check the motor operation, execute U030 Belt Mea nd (transfer motor).. 2. Check the drive gear can rotate or they are not unusually loaded and, if necessary, replace. 3. Decrease Vpp using U100. Change “set ac gain” of U100 from Auto to mode1. 4. Confirm that the drum or the drum screw can rotate. 5. If it won’t rotate, replace the drum unit. Drum motor C 1. Confirm that the wiring connector is firmly connected and, if necessary, connect the connector all the way in. Drum motor C and Motor control PWB (YC5) Motor control PWB (YC3) and Engine PWB (YC9) 2. If the wiring is disconnected, shorted or grounded, replace the wiring. 3. Replace the Drum motor C. Motor control PWB Replace the Motor control PWB Engine PWB 1. Check the engine software and upgrade to the latest, if necessary. 2. Replace the engine PWB. |
Error code: | 2500 |
Description: | Paper feed motor error After paper feed motor is driven, the ready signal does not turn to L within 2 s. After paper feed motor is stabilized, the ready signal is at the H level for 1 s continuously. |
Causes: | Defective connector cable or poor contact in the connector. Defective drive transmission system of motor. Defective paper feed motor. Defective engine PWB. |
Remedy: | Paper feed motor 1. To check the motor operation execute U030 Feed (paper feed motor). 2. Check the paper feed roller and drive gear can rotate or they are not unusually loaded and, if necessary, replace. 3. Confirm that the wiring connector is firmly connected and, if necessary, connect the connector all the way in. Paper feed motor and Feed PWB 2(YC2) Feed PWB 2(YC1) and Engine PWB (YC4) 4. If the wiring is disconnected, shorted or grounded, replace the wiring. 5. Replace the paper feed motor. Engine PWB 1. Check the engine software and upgrade to the latest, if necessary. 2. Replace the engine PWB. |
Error code: | 2600 |
Description: | PF paper feed motor error (large capacity feeder) After PF paper feed motor is driven, the ready signal does not turn to L within 2 s. |
Causes: | Defective connector cable or poor contact in the connector. Defective drive transmission system of motor. Defective PF paper feed motor. Defective PF main PWB. |
Remedy: | PF paper feed motor 1. To check the feed unit operation, execute U247 LCF- Motor ON. 2. Check the paper feed roller and drive gear can rotate or they are not unusually loaded and, if necessary, replace. 3. Confirm that the wiring connector is firmly connected and, if necessary, connect the connector all the way in. PF paper feed motor and PF main PWB (YC16) 4. If the wiring is disconnected, shorted or grounded, replace the wiring. 5. Replace the paper feed motor. PF main PWB Replace the PF main PWB (Refer to the service manual for the paper feeder). |
Error code: | 2610 |
Description: | PF paper feed motor error (paper feeder) After PF paper feed motor is driven, the ready signal does not turn to L within 2 s. |
Causes: | Defective connector cable or poor contact in the connector. Defective drive transmission system of motor. Defective PF paper feed motor. Defective PF main PWB. |
Remedy: | PF paper feed motor 1. To check the feed unit operation, execute U247 2PF - Motor ON. 2. Check the paper feed roller and drive gear can rotate or they are not unusually loaded and, if necessary, replace. 3. Confirm that the wiring connector is firmly connected and, if necessary, connect the connector all the way in. PF paper feed motor and PF main PWB (YC16) 4. If the wiring is disconnected, shorted or grounded, replace the wiring. 5. Replace the paper feed motor. PF main PWB Replace the PF main PWB (Refer to the service manual for the paper feeder). |
Error code: | 2620 |
Description: | PF drive motor 3 error (PF3) During the motor drive, the stable signal is not turned on for continuous 5 s. |
Remedy: | Defective connector cable or poor contact in the connector 1. Reinsert the connector. 2. Check continuity within the connector wire. If none, replace the wire. PF drive motor 3 and PF main PWB (YC6) Drive transmission system for the PF drive motor 1. Check if the rollers and gears rotate smoothly. If not, clean or grease the bushes and gears. 2. Replace the gears, if damaged. PF drive motor Replace the PF drive motor 3. PF main PWB Replace the PF main PWB. |
Error code: | 2760 |
Description: | Transfer motor startup error Transfer motor is not stabilized within 5 s since the motor is activated. |
Causes: | Defective connector cable or poor contact in the connector. Defective drive transmission system of motor Defective transfer motor. Defective engine PWB. |
Remedy: | Transfer motor 1. To check the motor operation, execute U030 Belt Meand. 2. Rotate the drive gear, the belt and the roller by the hand and check that they are not unusually loaded. 3. Clean the Intermediate transfer belt unit. 4. Confirm that the wiring connector is firmly connected and, if necessary, connect the connector all the way in. Transfer motor and Feed PWB 1 (YC13) Feed PWB 1(YC2) and Engine PWB (YC5) 5. If the wiring is disconnected, shorted or grounded, replace the wiring. 6. Replace the Transfer motor. Feed PWB 1 Replace the Feed PWB 1. Engine PWB 1. Check the engine software and upgrade to the latest, if necessary. 2. Replace the engine PWB. |
Error code: | 2820 |
Display: | Cannot adjust printhead. Press Online to clear the error and readjust printhead. |
Description: | Intermediate transfer belt motor steady-state error After transfer motor is stabilized, the ready signal is at the H level for 5 s continuously. The counter value obtained by timer capture is lower than 2200 for 10 times in a row. |
Causes: | Defective connector cable or poor contact in the connector. Defective drive transmission system of motor. Defective transfer motor. Defective engine PWB. |
Remedy: | Transfer motor 1. To check the motor operation, execute U030 Belt Meand. 2. Rotate the roller, driving gear by the hand and check that they are not unusually loaded. 3. Clean the intermediate transfer belt unit. 4. Confirm that the wiring connector is firmly connected and, if necessary, connect the connector all the way in. Transfer motor and Feed PWB 1(YC13) Feed PWB 1(YC2) and Engine PWB (YC5) 5. If the wiring is disconnected, shorted or grounded, replace the wiring. 6. Replace the Transfer motor. Feed PWB 1 Replace the Feed PWB 1. Engine PWB 1. Check the engine software and upgrade to the latest, if necessary. 2. Replace the engine PWB. |
Error code: | 4001 |
Display: | ERROR E146-4001 Call for service. |
Description: | Polygon motor synchronization error After polygon motor is driven, the ready signal does not turn to L within 30 s. The polygon motor speed won’t stabilize within 10 s. |
Causes: | Defective connector cable or poor contact in the connector. Defective polygon motor. Defective engine PWB. |
Remedy: | Polygon motor (LSU) 1. Confirm that the wiring connector is firmly connected and, if necessary, connect the connector all the way in. Polygon motor and Engine PWB (YC15) 2. If the wiring is disconnected, shorted or grounded, replace the wiring. 3. Replace the laser scanner unit. Engine PWB 1. Check the engine software and upgrade to the latest, if necessary. 2. Replace the engine PWB. |
Error code: | 4002 |
Display: | Drum End Soon:Y |
Description: | Polygon motor C synchronization error After polygon motor C is driven, the ready signal does not turn to L within 30 s. The polygon motor speed won’t stabilize within 10 s. |
Causes: | Defective connector cable or poor contact in the connector. Defective polygon motor C. Defective engine PWB. |
Remedy: | Polygon motor C (LSU) 1. Confirm that the wiring connector is firmly connected and, if necessary, connect the connector all the way in. Polygon motor C and LSU relay PWB (YC9) LSU relay PWB (YC3) and Engine PWB (YC12) 2. If the wiring is disconnected, shorted or grounded, replace the wiring. 3. Replace the laser scanner unit. Engine PWB 1. Check the engine software and upgrade to the latest, if necessary. 2. Replace the engine PWB. |
Error code: | 4011 |
Description: | Polygon motor steady-state error After Polygon motor is stabilized, the ready signal is at the H level for 15 s continuously. |
Causes: | Defective connector cable or poor contact in the connector. Defective polygon motor. Defective engine PWB. |
Remedy: | Polygon motor (LSU) 1. Confirm that the wiring connector is firmly connected and, if necessary, connect the connector all the way in. Polygon motor and Engine PWB (YC15) 2. If the wiring is disconnected, shorted or grounded, replace the wiring. 3. Replace the laser scanner unit. Engine PWB 1. Check the engine software and upgrade to the latest, if necessary. 2. Replace the engine PWB. |
Error code: | 4012 |
Description: | Polygon motor C steadystate error After polygon motor C is stabilized, the ready signal is at the H level for 15 s continuously |
Causes: | Defective connector cable or poor contact in the connector. Defective polygon motor C. Defective engine PWB. |
Remedy: | Polygon motor C (LSU) 1. Confirm that the wiring connector is firmly connected and, if necessary, connect the connector all the way in. Polygon motor C and LSU relay PWB (YC9) LSU relay PWB (YC3) and Engine PWB (YC12) 2. If the wiring is disconnected, shorted or grounded, replace the wiring. 3. Replace the laser scanner unit. Engine PWB 1. Check the engine software and upgrade to the latest, if necessary. 2. Replace the engine PWB. |
Error code: | 4101 |
Description: | BD initialization error K After Polygon motor is driven, the BD signal is not detected for 1 s. |
Causes: | Defective connector cable or poor contact in the connector. Defective PD PWB. Defective engine PWB. |
Remedy: | PD PWB K (LSU) 1. Confirm that the FFC wiring connector is not distorted and connect the FFC wiring all the way in. Laser scanner unit and LSU relay PWB (YC3) LSU relay PWB (YC2) and Engine PWB (YC11) 2. If the FFC wiring is disconnected, replace the FFC wiring. 3. Replace the laser scanner unit. Engine PWB 1. Check the engine software and upgrade to the latest, if necessary. 2. Replace the engine PWB. |
Error code: | 4102 |
Description: | BD initialization error C After polygon motor C is driven, the BD signal is not detected for 1 s. |
Causes: | Defective connector cable or poor contact in the connector. Defective PD PWB C. Defective engine PWB. |
Remedy: | PD PWB C (LSU) 1. Confirm that the FFC wiring connector is not distorted and connect the FFC wiring all the way in. Laser scanner unit and LSU relay PWB (YC10) LSU relay PWB (YC3) and Engine PWB (YC12) 2. If the FFC wiring is disconnected, replace the FFC wiring. 3. Replace the laser scanner unit. Engine PWB 1. Check the engine software and upgrade to the latest, if necessary. 2. Replace the engine PWB. |
Error code: | 4103 |
Description: | BD initialization error M After polygon motor M is driven, the BD signal is not detected for 1 s. |
Causes: | Defective connector cable or poor contact in the connector. Defective PD PWB M. Defective engine PWB. |
Remedy: | PD PWB M (LSU) 1. Confirm that the FFC wiring connector is not distorted and connect the FFC wiring all the way in. Laser scanner unit and LSU relay PWB (YC8) LSU relay PWB (YC3) and Engine PWB (YC12) 2. If the FFC wiring is disconnected, replace the FFC wiring. 3. Replace the laser scanner unit. Engine PWB 1. Check the engine software and upgrade to the latest, if necessary. 2. Replace the engine PWB. |
Error code: | 4104 |
Description: | BD initialization error Y After polygon motor Y is driven, the BD signal is not detected for 1 s. |
Causes: | Defective connector cable or poor contact in the connector. Defective PD PWB Y. Defective engine PWB. |
Remedy: | PD PWB Y (LSU) 1. Confirm that the FFC wiring connector is not distorted and connect the FFC wiring all the way in. Laser scanner unit and LSU relay PWB (YC12) LSU relay PWB (YC3) and Engine PWB (YC12) 2. If the FFC wiring is disconnected, replace the FFC wiring. 3. Replace the laser scanner unit. Engine PWB 1. Check the engine software and upgrade to the latest, if necessary. 2. Replace the engine PWB. |
Error code: | 4201 |
Display: | Replace Drum:BK |
Description: | BD steady-state error K The BD signal is not detected. |
Causes: | Defective connector cable or poor contact in the connector. Defective PD PWB. Defective engine PWB. |
Remedy: | PD PWB K (LSU) 1. Confirm that the FFC wiring connector is not distorted and connect the FFC wiring all the way in. Laser scanner unit and LSU relay PWB (YC3) LSU relay PWB (YC2) and Engine PWB (YC11) 2. If the FFC wiring is disconnected, shorted or grounded, replace the FFC wiring. 3. Replace the laser scanner unit. Engine PWB 1. Check the engine software and upgrade to the latest, if necessary. 2. Replace the engine PWB. |
Error code: | 4202 |
Display: | Replace Drum:Y |
Description: | BD steady-state error C The BD signal is not detected. |
Causes: | Defective connector cable or poor contact in the connector. Defective PD PWB C. Defective engine PWB. |
Remedy: | PD PWB C (LSU) 1. Confirm that the FFC wiring connector is not distorted and connect the FFC wiring all the way in. Laser scanner unit and LSU relay PWB (YC10) LSU relay PWB (YC3) and Engine PWB (YC12) 2. If the FFC wiring is disconnected, replace the FFC wiring. 3. Replace the laser scanner unit. Engine PWB 1. Check the engine software and upgrade to the latest, if necessary. 2. Replace the engine PWB. |
Error code: | 4203 |
Display: | Replace Drum:M |
Description: | BD steady-state error M The BD signal is not detected. |
Causes: | Defective connector cable or poor contact in the connector. Defective PD PWB M. Defective engine PWB. |
Remedy: | PD PWB M (LSU) 1. Confirm that the FFC wiring connector is not distorted and connect the FFC wiring all the way in. Laser scanner unit and LSU relay PWB (YC8) LSU relay PWB (YC3) and Engine PWB (YC12) 2. If the FFC wiring is disconnected, replace the FFC wiring. 3. Replace the laser scanner unit. Engine PWB 1. Check the engine software and upgrade to the latest, if necessary. 2. Replace the engine PWB. |
Error code: | 4204 |
Display: | Replace Drum:C |
Description: | BD steady-state error Y The BD signal is not detected. |
Causes: | Defective connector cable or poor contact in the connector. Defective PD PWB Y. Defective engine PWB |
Remedy: | PD PWB Y (LSU) 1. Confirm that the FFC wiring connector is not distorted and connect the FFC wiring all the way in. Laser scanner unit and LSU relay PWB (YC12) LSU relay PWB (YC3) and Engine PWB (YC12) 2. If the FFC wiring is disconnected, replace the FFC wiring. 3. Replace the laser scanner unit. Engine PWB 1. Check the engine software and upgrade to the latest, if necessary. 2. Replace the engine PWB. |
Error code: | 4600 |
Display: | Maintenance Replace Laser |
Description: | LSU cleaning motor error After LSU cleaning motor is driven, the ready signal does not turn to L within 2 s. After LSU cleaning motor is stabilized, the ready signal is at the H level for 1 s continuously. |
Causes: | Defective connector cable or poor contact in the connector. Defective drive transmission system of motor. Defective LSU cleaning motor. Defective engine PWB. |
Remedy: | LSU cleaning motor 1. Execute LSU cleaning using Adjustment/Maintenance of the system menu. 2. Rotate the drive gear and the cleaning spiral by the hand and check that they are not unusually loaded, and replace if it is damaged. 3. Confirm that the wiring connector is firmly connected and, if necessary, connect the connector all the way in. LSU cleaning motor and Engine PWB (YC21) 4. If the wiring is disconnected, shorted or grounded, replace the wiring. 5. Replace the LSU cleaning motor. Engine PWB 1. Check the engine software and upgrade to the latest, if necessary. 2. Replace the engine PWB. |
Error code: | 4700 |
Display: | Supplies WT Box End Soon |
Description: | VIDEO_ASIC device error Communication with the video ASIC has failed 5 times successively. After writing to the VIDEO ASIC, the error that the reading value from the same address does not match occurs 8 times successively. |
Causes: | Engine PWB. Main PWB |
Remedy: | Main PWB 1. Unplug the power cord from the wall outlet, and wait five seconds. Then plug in the power cord and then turn on the power switch. 2. Check that the connectors on the main PWB are properly connected, and if not, re-connect them. 3. Replace the main PWB. |
Error code: | 5101 |
Description: | Main high-voltage error K Measure the inflowing current when Vpp is varied in 3 steps and verify if the difference of the currents of 0 and step 2 is less than 42 (51 if lower highvoltage board). |
Causes: | Defective connector cable or poor contact in the connector. Defective high voltage PWB Defective engine PWB. |
Remedy: | Drum unit 1. Confirm that the drum or the drum screw can rotate. 2. If it won’t rotate, replace the drum unit. 3. Check that the discharger lamp is properly connected. Charger roller unit 1. Check that the high-voltage contacts are not distorted or adhered with foreign objects. 2. Reinstall the chrager roller unit.Or, replace the charger roller unit. High voltage PWB 1. Confirm that the wiring connector is firmly connected and, if necessary, connect the connector all the way in. High voltage PWB (YC2) and Engine PWB (YC16) 2. If the wiring is disconnected, shorted or grounded, replace the wiring. 3. Replace the High voltage PWB. Engine PWB 1. Check the engine software and upgrade to the latest, if necessary. 2. Replace the engine PWB. |
Error code: | 5102 |
Description: | Main high-voltage error C Measure the inflowing current when Vpp is varied in 3 steps and verify if the difference of the currents of 0 and step 2 is less than 42 (51 if lower highvoltage board). |
Causes: | Defective connector cable or poor contact in the connector. Defective high voltage PWB 1. Defective engine PWB. |
Remedy: | Drum unit 1. Execute U030 Belt Mean Drum Motor and check that the drum motor can rotate. 2. Confirm that the drum or the drum screw can rotate. 3. Check that the discharger lamp is properly connected. 4. If it won’t rotate, replace the drum unit. Charger roller unit 1. Check that the high-voltage contacts are not distorted or adhered with foreign objects. 2. Reinstall the chrager roller unit.Or, replace the charger roller unit. High voltage PWB 1 1. Confirm that the wiring connector is firmly connected and, if necessary, connect the connector all the way in. High voltage PWB 1(YC2) and Engine PWB (YC16) 2. If the wiring is disconnected, shorted or grounded, replace the wiring. 3. Replace the High voltage PWB 1. Engine PWB 1. Check the engine software and upgrade to the latest, if necessary. 2. Replace the engine PWB. |
Error code: | 5103 |
Description: | Main high-voltage error M Measure the inflowing current when Vpp is varied in 3 steps and verify if the difference of the currents of 0 and step 2 is less than 42 (51 if lower highvoltage board). |
Causes: | Defective connector cable or poor contact in the connector. Defective high voltage PWB 1. Defective engine PWB. |
Remedy: | Drum unit 1. Execute U030 Belt Mean Drum Motor and check that the drum motor can rotate. 2. Confirm that the drum or the drum screw can rotate. 3. Check that the discharger lamp is properly connected. 4. If it won’t rotate, replace the drum unit. Charger roller unit 1. Check that the high-voltage contacts are not distorted or adhered with foreign objects. 2. Reinstall the chrager roller unit.Or, replace the charger roller unit. High voltage PWB 1 1. Confirm that the wiring connector is firmly connected and, if necessary, connect the connector all the way in. High voltage PWB 1(YC3) and Engine PWB (YC17) 2. If the wiring is disconnected, shorted or grounded, replace the wiring. 3. Replace the High voltage PWB 1. Engine PWB 1. Check the engine software and upgrade to the latest, if necessary. 2. Replace the engine PWB. |
Error code: | 5104 |
Description: | Main high-voltage error Y Measure the inflowing current when Vpp is varied in 3 steps and verify if the difference of the currents of 0 and step 2 is less than 42 (51 if lower highvoltage board). |
Causes: | Defective connector cable or poor contact in the connector. Defective high voltage PWB 1. Defective engine PWB. |
Remedy: | Drum unit 1. Execute U030 Belt Mean Drum Motor and check that the drum motor can rotate. 2. Confirm that the drum or the drum screw can rotate. 3. Check that the discharger lamp is properly connected. 4. If it won’t rotate, replace the drum unit. Charger roller unit 1. Check that the high-voltage contacts are not distorted or adhered with foreign objects. 2. Reinstall the chrager roller unit.Or, replace the charger roller unit. High voltage PWB 1 1. Confirm that the wiring connector is firmly connected and, if necessary, connect the connector all the way in. High voltage PWB 1(YC1) and Engine PWB (YC16) 2. If the wiring is disconnected, shorted or grounded, replace the wiring. 3. Replace the High voltage PWB 1. Engine PWB 1. Check the engine software and upgrade to the latest, if necessary. 2. Replace the engine PWB. |
Error code: | 6000 |
Description: | Broken fuser heater wire Fuser thermistor 1 does not reach 100° C/212 °F even after 30 s during warming up. The detected temperature of fuser thermistor 1 does not reach the specified temperature (ready indication temperature) for 420 s in warming up after reached to 100° C/212 °F. |
Causes: | Defective connector cable or poor contact in the connector. Deformed connector pin. Defective triac. Fuser thermostat triggered. Defective fuser heater. Defective engine PWB. |
Remedy: | Fuser unit 1. Check that no paper jam is present. 2. Confirm that the wiring connector is firmly connected and, if necessary, connect the connector all the way in. Fuser unit and Engine PWB (YC26) 3. If the wiring is disconnected, shorted or grounded, replace the wiring. 4. Replace the Fuser unit Replace the Fuser unit. (Deteriorated sensitivity due to the toner adhered to the center thermistor.) Engine PWB 1. Check the engine software and upgrade to the latest, if necessary. 2. Replace the engine PWB. Power source PWB 1. Confirm that the wiring connector is firmly connected and, if necessary, connect the connector all the way in. Power source PWB (YC3) and fuser heater PWB (YC3) Fuser heater PWB (YC2) and feed PWB 1 (YC27) Feed PWB 1 (YC1) and Engine PWB (YC6) Fuser heater 1. Replace the fuser unit. |
Error code: | 6020 |
Description: | Abnormally high fuser thermistor 1 temperature Fuser thermistor 1 detects a temperature higher than 240°C/464°F for 1 s. |
Causes: | Deformed connector pin. Defective triac. Shorted fuser thermistor 1. Defective engine PWB. |
Remedy: | Fuser unit 1. Confirm that the wiring connector is firmly connected and, if necessary, connect the connector all the way in. Fuser unit and Engine PWB (YC26) 2. If the wiring is disconnected, shorted or grounded, replace the wiring. 3. Replace the Fuser unit. Engine PWB 1. Check the engine software and upgrade to the latest, if necessary. 2. Replace the engine PWB. |
Error code: | 6030 |
Description: | Broken fuser thermistor 1 wire Input from fuser center thermistor 1 is 1010 or more (A/D value) continuously for 1 s. Verify if A/D read in the differential output won’t change by 4 or more when it was turned on for 10 seconds in a lowtemperature environment. |
Causes: | Defective connector cable or poor contact in the connector. Deformed connector pin. Defective triac. Broken fuser thermistor 1 wire. Fuser thermostat triggered. Defective fuser heater. Defective engine PWB. |
Remedy: | Fuser unit 1. Check that no paper jam is present. 2. Confirm that the wiring connector is firmly connected and, if necessary, connect the connector all the way in. Fuser unit and Engine PWB (YC26) 3. If the wiring is disconnected, shorted or grounded, replace the wiring. 4. Replace the Fuser unit. (Deteriorated sensitivity due to the toner adhered to the center thermistor.) Engine PWB 1. Check the engine software and upgrade to the latest, if necessary. 2. Replace the engine PWB. Fuser thermistor 1 1. Replace the Fuser unit. Fuser thermostat (triggered) 1. Confirm that the wiring connector is firmly connected and, if necessary, connect the connector all the way in. Fuser unit and fuser heater PWB (YC1) 2. If the wiring is disconnected, shorted or grounded, replace the wiring. 3. Replace the Fuser unit. |
Error code: | 6040 |
Description: | Fuser heater error Input from fuser center thermistor 1 is abnormal value continuously for 1 s. |
Causes: | Defective connector cable or poor contact in the connector. Deformed connector pin. Defective triac. Broken fuser thermistor 1 wire. Defective fuser heater. Defective engine PWB. |
Remedy: | Fuser unit 1. Confirm that the wiring connector is firmly connected and, if necessary, connect the connector all the way in. Fuser unit and Engine PWB (YC26) 2. If the wiring is disconnected, shorted or grounded, replace the wiring. Engine PWB 1. Check the engine software and upgrade to the latest, if necessary. 2. Replace the engine PWB. Center thermistor 1 1. Replace the Fuser unit. Fuser thermostat (triggered) 1. Confirm that the wiring connector is firmly connected and, if necessary, connect the connector all the way in. Fuser unit and fuser heater PWB (YC1) 2. If the wiring is disconnected, shorted or grounded, replace the wiring. 3. Replace the Fuser unit. |
Error code: | 6050 |
Description: | Abnormally low fuser thermistor 1 temperature Fuser thermistor 1 detects a temperature lower than 100°C/212°F for 1 s after warming up, during ready or during print. |
Causes: | Deformed connector pin. Defective triac. Defective fuser thermistor 1. Defective fuser heater. Defective engine PWB. |
Remedy: | Power source 1. Check that the operating voltage falls within +/-10%. 2. Check no voltage drop is caused. The heater is deactivated at 70V or lower. 3. Relocate the AC outlet that supplies power. Fuser unit 1. Confirm that the wiring connector is firmly connected and, if necessary, connect the connector all the way in. Fuser unit and Engine PWB (YC26) 2. If the wiring is disconnected, shorted or grounded, replace the wiring. 3. Replace the Fuser unit. Engine PWB 1. Check the engine software and upgrade to the latest, if necessary. 1. Replace the engine PWB. Fuser thermistor 1 1. Replace the Fuser unit. Fuser thermostat (triggered) 1. Confirm that the wiring connector is firmly connected and, if necessary, connect the connector all the way in. Fuser unit and fuser heater PWB (YC1) 2. If the wiring is disconnected, shorted or grounded, replace the wiring. 3. Replace the Fuser unit. |
Error code: | 6200 |
Display: | No Drum Unit Install the Drum Unit. |
Description: | Broken fuser edge heater wire Fuser thermistor 2 does not reach 100° C/212 °F even after 60 s during warming up. The detected temperature of fuser thermistor 2 does not reach the specified temperature (ready indication temperature) for 420 s in warming up after reached to 100° C/212 °F. |
Causes: | Defective connector cable or poor contact in the connector. Deformed connector pin. Defective triac. Fuser thermostat triggered. Defective fuser IH. Defective engine PWB. |
Remedy: | Fuser unit 1. Confirm that the wiring connector is firmly connected and, if necessary, connect the connector all the way in. Fuser unit and Engine PWB (YC26) 2. If the wiring is disconnected, shorted or grounded, replace the wiring. 3. Replace the Fuser unit. Engine PWB 1. Check the engine software and upgrade to the latest, if necessary. 2. Replace the engine PWB. Fuser center thermistor 1 1. Replace the Fuser unit. |
Error code: | 6220 |
Description: | Abnormally high fuser edge thermistor temperature Fuser thermistor 2 detects a temperature higher than 240°C/464°F for 1 s. |
Causes: | Deformed connector pin. Defective triac. Shorted fuser thermistor 2. Defective engine PWB. |
Remedy: | Fuser unit 1. Confirm that the wiring connector is firmly connected and, if necessary, connect the connector all the way in. Fuser unit and Engine PWB (YC26) 2. If the wiring is disconnected, shorted or grounded, replace the wiring. 3. Replace the Fuser unit. Engine PWB 1. Check the engine software and upgrade to the latest, if necessary. 2. Replace the engine PWB. |
Error code: | 6230 |
Description: | Broken fuser edge thermistor wire The Input signal from the fuser thermistor 2 is 992 or more (A/D value) continuously for 1 s when the temperature at the fuser thermistor 1 is higher than 100°C/212°F. Fuser thermistor 2 detects a lower then 50°C/122°F for 15s during warming up. |
Causes: | Defective connector cable or poor contact in the connector. Deformed connector pin. Defective triac. Broken fuser thermistor 2 wire. Fuser thermostat triggered. Defective fuser IH. Defective engine PWB. |
Remedy: | Fuser unit 1. Confirm that the wiring connector is firmly connected and, if necessary, connect the connector all the way in. Fuser unit and Engine PWB (YC26) 2. If the wiring is disconnected, shorted or grounded, replace the wiring. 3. Replace the Fuser unit. Engine PWB 1. Check the engine software and upgrade to the latest, if necessary. 2. Replace the engine PWB. |
Error code: | 6250 |
Description: | Abnormally low fuser edge thermistor temperature Fuser thermistor 2 detects a temperature lower than 100°C/212°F for 1 s during ready or print. |
Causes: | Deformed connector pin. Defective triac. Defective fuser thermistor 2. Defective fuser IH. Defective engine PWB. |
Remedy: | Fuser unit 1. Confirm that the wiring connector is firmly connected and, if necessary, connect the connector all the way in. 2. Fuser unit and Engine PWB (YC26) If the wiring is disconnected, shorted or grounded, replace the wiring. 3. Replace the Fuser unit. Engine PWB 1. Check the engine software and upgrade to the latest, if necessary. 2. Replace the engine PWB. |
Error code: | 6400 |
Display: | No Belt Unit Open the Front Cover, pull out all Drum Units completely and install the Belt Unit. |
Description: | Zero-cross signal error While fuser heater ON/OFF control is performed, the zerocross signal is not input within 3 s. |
Causes: | Fuser unit. |
Remedy: | Fuser unit 1. Confirm that the wiring connector is firmly connected and, if necessary, connect the connector all the way in. Fuser heater PWB (YC2) and feed PWB 1 (YC27) 2. If the wiring is disconnected, shorted or grounded, replace the wiring. 3. Replace the fuser heater PWB. |
Error code: | 6610 |
Description: | Fuser release sensor error When the fuser release motor is driven, the fuser release sensor does not turn on/off for 5 s. |
Causes: | Defective connector cable or poor contact in the connector. Defective drive transmission system of motor. Defective fuser release motor. Defective engine PWB. |
Remedy: | Fuser release motor 1. To check the motor operation, execute U030 Fuser Release. 2. Check that the drive gear can be rotated and the separation is possible. 3. If the motor won’t rotate, confirm that the wiring connector is firmly connected and, if necessary, connect the connector all the way in. Fuser unit and Engine PWB (YC26) 4. If the wiring is disconnected, shorted or grounded, replace the wiring. 5. Replace the Fuser unit. Fuser release sensor 1. Check that the sensor is correctly positioned. 2. Check that the sensor is not contaminated or damaged. Engine PWB 1. Check the engine software and upgrade to the latest, if necessary. 2. Replace the engine PWB. |
Error code: | 7001 |
Description: | Toner motor error During the toner motor is driven, an event in which a locking was detected for 5 times in 200 ms intervals has occurred in 30 sets. |
Causes: | Defective connector cable or poor contact in the connector. Defective toner motor. Defective engine PWB. |
Remedy: | Toner container 1. Check that the spiral screw of the toner container can be rotated by the hand. 2. Check for broken gears and replace if any. Toner motor 1. Draw out the toner container and execute U135 to check the toner motor operation. 2. Check the drive gear can rotate or they are not unusually loaded and, if necessary, replace. 3. Confirm that the wiring connector is firmly connected and, if necessary, connect the connector all the way in. Toner motor and Engine PWB (YC27) 4. If the wiring is disconnected, shorted or grounded, replace the wiring. 5. Replace the Toner motor. Screw sensor 1. Check that the sensor is correctly positioned. 2. Confirm that the wiring connector is firmly connected and, if necessary, connect the connector all the way in. Screw sensor and Front PWB (YC5) Front PWB (YC2) and Engine PWB (YC7) 3. Replace the Screw sensor. Engine PWB 1. Check the engine software and upgrade to the latest, if necessary. 2. Replace the engine PWB. |
Error code: | 7002 |
Description: | Toner motor C error During the toner motor is driven, an event in which a locking was detected for 5 times in 200 ms intervals has occurred in 30 sets. |
Causes: | Defective connector cable or poor contact in the connector. Defective screw sensor C. Defective toner motor C. Defective engine PWB. |
Remedy: | Toner container C 1. Check that the spiral screw of the toner container can be rotated by the hand. 2. Check for broken gears and replace if any. Toner motor C 1. Draw out the toner container and execute U135 to check the toner motor operation. 2. Check the drive gear can rotate or they are not unusually loaded and, if necessary, replace. 3. Confirm that the wiring connector is firmly connected and, if necessary, connect the connector all the way in. Toner motor C and Engine PWB (YC27) 4. If the wiring is disconnected, shorted or grounded, replace the wiring. 5. Replace the Toner motor C. Screw sensor C 1. Check that the sensor is correctly positioned. 2. Confirm that the wiring connector is firmly connected and, if necessary, connect the connector all the way in. Screw sensor C and Engine PWB (YC27) 3. Replace the screw sensor C. Engine PWB 1. Check the engine software and upgrade to the latest, if necessary. 2. Replace the engine PWB. |
Error code: | 7003 |
Description: | Toner motor M error During the toner motor is driven, an event in which a locking was detected for 5 times in 200 ms intervals has occurred in 30 sets. |
Causes: | Defective connector cable or poor contact in the connector. Defective screw sensor M. Defective toner motor M. Defective engine PWB. |
Remedy: | Toner container M 1. Check that the spiral screw of the toner container can be rotated by the hand. 2. Check for broken gears and replace if any. Toner motor M 1. Draw out the toner container and execute U135 to check the toner motor operation. 2. Check the drive gear can rotate or they are not unusually loaded and, if necessary, replace. 3. Confirm that the wiring connector is firmly connected and, if necessary, connect the connector all the way in. Toner motor M and Engine PWB (YC27) 4. If the wiring is disconnected, shorted or grounded, replace the wiring. 5. Replace the Toner motor M. Screw sensor M 1. Check that the sensor is correctly positioned. 2. Confirm that the wiring connector is firmly connected and, if necessary, connect the connector all the way in. Screw sensor M and Engine PWB (YC27) 3. Replace the screw sensor M. Engine PWB 1. Check the engine software and upgrade to the latest, if necessary. 2. Replace the engine PWB. |
Error code: | 7004 |
Description: | Toner motor Y error During the toner motor is driven, an event in which a locking was detected for 5 times in 200 ms intervals has occurred in 30 sets. |
Causes: | Defective connector cable or poor contact in the connector. Defective screw sensor Y. Defective toner motor Y. Defective engine PWB. |
Remedy: | Toner container Y 1. Check that the spiral screw of the toner container can be rotated by the hand. 1. Check for broken gears and replace if any. Toner motor Y 1. Draw out the toner container and execute U135 to check the toner motor operation. 2. Check the drive gear can rotate or they are not unusually loaded and, if necessary, replace. 3. Confirm that the wiring connector is firmly connected and, if necessary, connect the connector all the way in. Toner motor Y and Engine PWB (YC27) 4. If the wiring is disconnected, shorted or grounded, replace the wiring. 5. Replace the Toner motor Y. Screw sensor Y 1. Check that the sensor is correctly positioned. 2. Confirm that the wiring connector is firmly connected and, if necessary, connect the connector all the way in. Screw sensor Y and Engine PWB (YC27) 3. Replace the screw sensor Y. Engine PWB 1. Check the engine software and upgrade to the latest, if necessary. 2. Replace the engine PWB. |
Error code: | 7101 |
Description: | Toner sensor error Sensor output value of 60 or less or 944 or more continued for 3 s. |
Causes: | Defective connector cable or poor contact in the connector. Defective toner sensor. Defective engine PWB. |
Remedy: | Failure of locking the developer waste slot at setup. If an abnormal noise is heard, check that the developer ejection outlet is released and, if not, release the outlet. Toner sensor 1. Check the toner sensor output by U155. 2. Confirm that the wiring connector is firmly connected and, if necessary, connect the connector all the way in. Toner sensor and Front PWB (YC7) Front PWB (YC2) and Engine PWB (YC8) 3. If the wiring is disconnected, shorted or grounded, replace the wiring. 4. Check that the gears of the Developer unit are not damaged and the spiral can rotate. 5. Replace the Developer unit. Toner motor 1. Draw out the toner container and execute U135 to check the toner motor operation. 2. Check the drive gear can rotate or they are not unusually loaded and, if necessary, replace. 3. Confirm that the wiring connector is firmly connected and, if necessary, connect the connector all the way in. Toner motor and Engine PWB (YC27) 4. If the wiring is disconnected, shorted or grounded, replace the wiring. 5. Replace the Toner motor. Engine PWB 1. Check the engine software and upgrade to the latest, if necessary. 2. Replace the engine PWB. |
Error code: | 7102 |
Description: | Toner sensor C error Sensor output value of 60 or less or 944 or more continued for 3 s. |
Causes: | Defective connector cable or poor contact in the connector. Defective engine PWB. |
Remedy: | Failure of locking the developer waste slot at setup. If an abnormal noise is heard, check that the developer ejection outlet is released and, if not, release the outlet. Toner sensor C 1. Check the toner sensor output by U155. 2. Confirm that the wiring connector is firmly connected and, if necessary, connect the connector all the way in. Toner sensor C and Front PWB (YC13) Front PWB (YC2) and Engine PWB (YC10) 3. If the wiring is disconnected, shorted or grounded, replace the wiring. 4. Check that the gears of the developer unit C are not damaged and the spiral can rotate. 5. Replace the Developer unit C. Toner motor C 1. Draw out the toner container and execute U135 to check the toner motor operation. 2. Check the drive gear can rotate or they are not unusually loaded and, if necessary, replace. 3. Confirm that the wiring connector is firmly connected and, if necessary, connect the connector all the way in. Toner motor C and Engine PWB (YC27) 4. If the wiring is disconnected, shorted or grounded, replace the wiring. 5. Replace the Toner motor C. Engine PWB 1. Check the engine software and upgrade to the latest, if necessary. 2. Replace the engine PWB. |
Error code: | 7103 |
Description: | Toner sensor M error Sensor output value of 60 or less or 944 or more continued for 3 s. |
Causes: | Defective connector cable or poor contact in the connector. Defective engine PWB. |
Remedy: | Failure of locking the developer waste slot at setup. If an abnormal noise is heard, check that the developer ejection outlet is released and, if not, release the outlet. Toner sensor M 1. Check the toner sensor output by U155. 2. Confirm that the wiring connector is firmly connected and, if necessary, connect the connector all the way in. Toner sensor M and Front PWB (YC11) Front PWB (YC2) and Engine PWB (YC10) 3. If the wiring is disconnected, shorted or grounded, replace the wiring. 4. Check that the gears of the developer unit M are not damaged and the spiral can rotate. 5. Replace the Developer unit M. Toner motor M 1. Draw out the toner container and execute U135 to check the toner motor operation. 2. Check the drive gear can rotate or they are not unusually loaded and, if necessary, replace. 3. Confirm that the wiring connector is firmly connected and, if necessary, connect the connector all the way in. Toner motor M and and Engine PWB (YC27) 4. If the wiring is disconnected, shorted or grounded, replace the wiring. 5. Replace the Toner motor M. Engine PWB 1. Check the engine software and upgrade to the latest, if necessary. 2. Replace the engine PWB. |
Error code: | 7104 |
Description: | Toner sensor Y error Sensor output value of 60 or less or 944 or more continued for 3 s. |
Causes: | Defective connector cable or poor contact in the connector Defective engine PWB. |
Remedy: | Failure of locking the developer waste slot at setup. If an abnormal noise is heard, check that the developer ejection outlet is released and, if not, release the outlet. Toner sensor Y 1. Check the toner sensor output by U155. 2. Confirm that the wiring connector is firmly connected and, if necessary, connect the connector all the way in. Toner sensor Y and Front PWB (YC15) Front PWB (YC2) and Engine PWB (YC10) 3. If the wiring is disconnected, shorted or grounded, replace the wiring. 4. Check that the gears of the developer unit Y are not damaged and the spiral can rotate. 5. Replace the Developer unit Y. Toner motor Y 1. Draw out the toner container and execute U135 to check the toner motor operation. 2. Check the drive gear can rotate or they are not unusually loaded and, if necessary, replace. 3. Confirm that the wiring connector is firmly connected and, if necessary, connect the connector all the way in. Toner motor Y and Engine PWB (YC27) 4. If the wiring is disconnected, shorted or grounded, replace the wiring. 5. Replace the Toner motor Y. Engine PWB 1. Check the engine software and upgrade to the latest, if necessary. 2. Replace the engine PWB. |
Error code: | 7200 |
Display: | Jam MP Tray Remove the jammed paper from MP Tray and press [Retry]. |
Description: | Broken outer temperature sensor 2 wire The sensor input sampling is greater than 230. |
Causes: | Defective connector cable or poor contact in the connector. Defective outer temperature sensor. Defective engine PWB. |
Remedy: | Outer temperature sensor 2 1. Confirm Ext/Int is displayed by U139 temperature and humidity. 2. Confirm that the wiring connector is firmly connected and, if necessary, connect the connector all the way in. Outer temperature sensor 2 and Front PWB (YC8) Front PWB (YC2) and Engine PWB (YC8) 3. If the wiring is disconnected, shorted or grounded, replace the wiring. 4. Replace the outer temperature sensor 2. Front PWB Replace the front PWB. Engine PWB 1. Check the engine software and upgrade to the latest, if necessary. 2. Replace the engine PWB. |
Error code: | 7221 |
Description: | Broken LSU thermistor wire The sensor input sampling is greater than 230. |
Causes: | Defective connector cable or poor contact in the connector. Defective LSU thermistor. Defective engine PWB. |
Remedy: | LSU thermistor 1. Confirm LSU is displayed by U139 temperature and humidity. 2. Confirm that the wiring connector is firmly connected and, if necessary, connect the connector all the way in. Laser scanner unit and LSU relay PWB (YC3) LSU relay PWB (YC2) and Engine PWB (YC11) 3. If the wiring is disconnected, shorted or grounded, replace the wiring. 4. Replace the laser scanner unit. LSU relay PWB REPLACE the LSU relay PWB. Engine PWB 1. Check the engine software and upgrade to the latest, if necessary. 2. Replace the engine PWB. |
Error code: | 7222 |
Description: | Broken LSU thermistor C wire The sensor input sampling is greater than 230. |
Causes: | Defective connector cable or poor contact in the connector. Defective LSU thermistor C. Defective engine PWB. |
Remedy: | LSU thermistor C 1. Confirm LSU is displayed by U139 temperature and humidity. 2. Confirm that the wiring connector is firmly connected and, if necessary, connect the connector all the way in. Laser scanner unit and LSU relay PWB (YC10) LSU relay PWB (YC3) and Engine PWB (YC12) 3. If the wiring is disconnected, shorted or grounded, replace the wiring. 4. Replace the laser scanner unit. LSU relay PWB REPLACE the LSU relay PWB. Engine PWB 1. Check the engine software and upgrade to the latest, if necessary. 2. Replace the engine PWB. |
Error code: | 7401 |
Description: | Developer unit type mismatch error Improper adaptation of the machine and developer unit is detected. |
Causes: | Defective connector cable or poor contact in the connector. Different type of the developer unit is installed. |
Remedy: | Different type of the developer unit is installed. Install the developer unit of the correct type. Developer unit 1. Confirm that the wiring connector is firmly connected and, if necessary, connect the connector all the way in. Developer unit and Front PWB (YC7) Front PWB (YC2) and Engine PWB (YC8) 2. If the wiring is disconnected, shorted or grounded, replace the wiring. |
Error code: | 7402 |
Description: | Developer unit C type mismatch error Absence of the developer unit C is detected. |
Causes: | Defective connector cable or poor contact in the connector. Different type of the developer unit is installed. |
Remedy: | Defective connector cable or poor contact in the connector. Reinsert the connector. Also check for continuity within the connector cable. If none, replace the cable. Developer unit C and front PWB (YC13) Front PWB (YC2) and engine PWB (YC10) Different type of the developer unit is installed. Install the correct developer unit. |
Error code: | 7403 |
Description: | Developer unit M type mismatch error Absence of the developer unit M is detected. |
Causes: | Defective connector cable or poor contact in the connector Different type of the developer unit is installed |
Remedy: | Defective connector cable or poor contact in the connector. Reinsert the connector. Also check for continuity within the connector cable. If none, replace the cable. Developer unit M and front PWB (YC11) Front PWB (YC2) and engine PWB (YC10) Different type of the developer unit is installed. Install the correct developer unit. |
Error code: | 7404 |
Description: | Developer unit Y type mismatch error Absence of the developer unit Y is detected. |
Causes: | Defective connector cable or poor contact in the connector. Different type of the developer unit is installed. |
Remedy: | Defective connector cable or poor contact in the connector. Reinsert the connector. Also check for continuity within the connector cable. If none, replace the cable. Developer unit Y and front PWB (YC15) Front PWB (YC2) and engine PWB (YC10) Different type of the developer unit is installed. Install the correct developer unit. |
Error code: | 7411 |
Description: | Drum unit type mismatch error Improper adaptation of the machine and developer unit is detected. |
Causes: | Defective connector cable or poor contact in the connector. Different type of the drum unit is installed. |
Remedy: | Different type of the drum unit is installed. Install the drum unit of the correct type. Drum unit 1. Confirm that the wiring connector is firmly connected and, if necessary, connect the connector all the way in. Drum unit and Front PWB (YC6) Front PWB (YC2) and Engine PWB (YC8) 2. If the wiring is disconnected, shorted or grounded, replace the wiring. |
Error code: | 7412 |
Description: | Drum unit type Mismatch error (Cyan) Improper adaptation of the main unit and drum unit is detected. |
Causes: | Drum unit C |
Remedy: | Drum unit 1. Check if the drum unit of different models is attached, and replace it to the correct one. 2. Confirm that the wiring connector is firmly connected, and if necessary, connect the connector all the way in. Drum unit - Drum/Developer relay PWB Drum/Developer relay PWB - Engine PWB(YC6) 3. If the wiring is disconnected, short-circuited or has a ground fault, replace the wire. Drum/developer relay PWB Replace the drum/developer relay PWB Engine PWB 1. Check the engine firmware and upgrade to the latest version if necessary. 2. Replace the engine PWB. |
Error code: | 7413 |
Description: | Drum unit type Mismatch error (Magenta) Improper adaptation of the main unit and drum unit is detected. |
Causes: | Drum unit M |
Remedy: | Drum unit 1. Check if the drum unit of different models is attached, and replace it to the correct one. 2. Confirm that the wiring connector is firmly connected, and if necessary, connect the connector all the way in. Drum unit - Drum/Developer relay PWB Drum/Developer relay PWB - Engine PWB(YC6) 3. If the wiring is disconnected, short-circuited or has a ground fault, replace the wire. Drum/developer relay PWB Replace the drum/developer relay PWB Engine PWB 1. Check the engine firmware and upgrade to the latest version if necessary. 2. Replace the engine PWB. |
Error code: | 7414 |
Description: | Drum unit type Mismatch error (Yellow) Improper adaptation of the main unit and drum unit is detected. |
Causes: | Drum unit Y |
Remedy: | Drum unit 1. Check if the drum unit of different models is attached, and replace it to the correct one. 2. Confirm that the wiring connector is firmly connected, and if necessary, connect the connector all the way in. Drum unit - Drum/Developer relay PWB Drum/Developer relay PWB - Engine PWB(YC6) 3. If the wiring is disconnected, short-circuited or has a ground fault, replace the wire. Drum/developer relay PWB Replace the drum/developer relay PWB Engine PWB 1. Check the engine firmware and upgrade to the latest version if necessary. 2. Replace the engine PWB. |
Error code: | 7601 |
Description: | ID sensor 1 error [Front] Dark potential error FrontDarkP and FrontDarkS are greater than 0.80V. Light potential error FrontBrightS is smaller than FrontDarkS. FrontBrightP is smaller than [FrontDarkP + 0.5V]. |
Causes: | Defective connector cable or poor contact in the connector. Defective engine PWB. |
Remedy: | ID sensor1 1. Execute U464 Calib for setting ID compensation operation and check the displayed values by U465 Boas Calib for ID compensation reference. 2. Clean the ID sensor on its surface. 3. Confirm that the wiring connector is firmly connected and, if necessary, connect the connector all the way in. ID sensor 1 (front) and relay PWB (YC10) Relay PWB (YC1) and Feed PWB 1 (YC14) Feed PWB 1 (YC1) and Engine PWB (YC6) 4. If the wiring is disconnected, shorted or grounded, replace the wiring. Feed PWB 1 Replace the Feed PWB 1. Engine PWB 1. Check the engine software and upgrade to the latest, if necessary. 2. Replace the engine PWB. |
Error code: | 7602 |
Description: | ID sensor 2 error [Rear] Dark potential error RearDarkP and RearDarkS are greater than 0.80V. Light potential error RearBrightS is smaller than RearDarkS. RearBrightP is smaller than [RearDarkP + 0.5V]. |
Causes: | Defective connector cable or poor contact in the connector. Defective engine PWB. |
Remedy: | ID sensor 2 1. Execute U464 Calib for setting ID compensation operation and check the displayed values by U465 Boas Calib for ID compensation reference. 2. Clean the ID sensor on its surface. 3. Confirm that the wiring connector is firmly connected and, if necessary, connect the connector all the way in. ID sensor2 (rear) and relay PWB (YC10) Relay PWB (YC1) and Feed PWB 1 (YC14) Feed PWB 1 (YC1) and Engine PWB (YC6) 4. If the wiring is disconnected, shorted or grounded, replace the wiring. Feed PWB 1 Replace the Feed PWB 1. Engine PWB 1. Check the engine software and upgrade to the latest, if necessary. 2. Replace the engine PWB. |
Error code: | 7611 |
Description: | Bias calibration reading value error (Black) During the calibration, the ID sensor cannot read a patch density on the primary transfer belt normally |
Causes: | Primary transfer unit ID sensor Drum unit Developer unit LSU Main/Engine PWB |
Remedy: | Primary transfer belt ID sensor 1. Unplug the power cord from the wall outlet, and wait five seconds. Then plug in the power cord and then turn on the power switch. 2. Execute [Calibration] using [Adjustment/Maintenance] of the system menu. 3. Check the occurrence of this service call error in the Event Log. 4. When the same service call error is detected again, clean if there is any dirt or stains on the primary transfer belt or the ID sensor surface. 5. Check whether or not the ID sensor shutter is open, by opening and closing the paper tray. 6. If not corrected, replace the primary transfer unit. 7. After performing the test print, if the poor density occurs, check whether there is any failure in the drum unit, developer unit, LSU. Engine PWB 1. Check the engine firmware and upgrade to the latest version if necessary. 2. Replace the engine PWB. |
Error code: | 7612 |
Description: | Bias calibration reading value error (Cyan) During the calibration, the ID sensor cannot read a patch density on the primary transfer belt normally. |
Causes: | Primary transfer unit ID sensor Drum unit Developer unit LSU Main/Engine PWB |
Remedy: | Primary transfer belt ID sensor 1. Unplug the power cord from the wall outlet, and wait five seconds. Then plug in the power cord and then turn on the power switch. 2. Execute [Calibration] using [Adjustment/Maintenance] of the system menu. 3. Check the occurrence of this service call error in the Event Log. 4. When the same service call error is detected again, clean if there is any dirt or stains on the primary transfer belt or the ID sensor surface. 5. Check whether or not the ID sensor shutter is open, by opening and closing the paper tray. 6. If not corrected, replace the primary transfer unit. 7. After performing the test print, if the poor density occurs, check whether there is any failure in the drum unit, developer unit, LSU. Engine PWB 1. Check the engine firmware and upgrade to the latest version if necessary. 2. Replace the engine PWB. |
Error code: | 7613 |
Description: | Bias calibration reading value error (Magenta) During the calibration, the ID sensor cannot read a patch density on the primary transfer belt normally. |
Causes: | Primary transfer unit ID sensor Drum unit Developer unit LSU Main/Engine PWB |
Remedy: | Primary transfer belt ID sensor 1. Unplug the power cord from the wall outlet, and wait five seconds. Then plug in the power cord and then turn on the power switch. 2. Execute [Calibration] using [Adjustment/Maintenance] of the system menu. 3. Check the occurrence of this service call error in the Event Log. 4. When the same service call error is detected again, clean if there is any dirt or stains on the primary transfer belt or the ID sensor surface. 5. Check whether or not the ID sensor shutter is open, by opening and closing the paper tray. 6. If not corrected, replace the primary transfer unit. 7. After performing the test print, if the poor density occurs, check whether there is any failure in the drum unit, developer unit, LSU. Engine PWB 1. Check the engine firmware and upgrade to the latest version if necessary. 2. Replace the engine PWB. |
Error code: | 7614 |
Description: | Bias calibration reading value error (Yellow) During the calibration, the ID sensor cannot read a patch density on the primary transfer belt normally. |
Causes: | Primary transfer unit ID sensor Drum unit Developer unit LSU Main/Engine PWB |
Remedy: | Primary transfer belt ID sensor 1. Unplug the power cord from the wall outlet, and wait five seconds. Then plug in the power cord and then turn on the power switch. 2. Execute [Calibration] using [Adjustment/Maintenance] of the system menu. 3. Check the occurrence of this service call error in the Event Log. 4. When the same service call error is detected again, clean if there is any dirt or stains on the primary transfer belt or the ID sensor surface. 5. Check whether or not the ID sensor shutter is open, by opening and closing the paper tray. 6. If not corrected, replace the primary transfer unit. 7. After performing the test print, if the poor density occurs, check whether there is any failure in the drum unit, developer unit, LSU. Engine PWB 1. Check the engine firmware and upgrade to the latest version if necessary. 2. Replace the engine PWB. |
Error code: | 7620 |
Description: | Color Registration timing of detection Color patches printed on the primary transfer belt are not within the ID sensor readable range. Or the poor density occurs. |
Causes: | Primary transfer unit ID sensor Drum unit Developer unit LSU Main/Engine PWB |
Remedy: | Primary transfer belt ID sensor LSU 1. Unplug the power cord from the wall outlet, and wait five seconds. Then plug in the power cord and then turn on the power switch. 2. Execute [Calibration] using [Adjustment/Maintenance] of the system menu. 3. Check the occurrence of this service call error in the Event Log. 4. When the same service call error is detected again, clean if there is any dirt or stains on the primary transfer belt or the ID sensor surface. 5. Check whether or not the ID sensor shutter is open, by opening and closing the paper tray. 6. If not corrected, replace the primary transfer unit. 7. After performing the test print, if the poor density occurs, check whether there is any failure in the drum unit, developer unit, LSU. 8. When checking the printing position of the color, if any color shift occurs, re-install the LSU and the drum unit. 9. If not corrected, replace the LSU. Engine PWB 1. Check the engine firmware and upgrade to the latest version if necessary. 2. Replace the engine PWB. |
Error code: | 7800 |
Description: | Broken outer temperature sensor wire The device did not respond for more than 5 ms during reading, in 5 times. |
Causes: | Defective connector cable or poor contact in the connector. Defective outer temperature sensor. Defective engine PWB. |
Remedy: | Outer temperature sensor 1. Confirm that the wiring connector is firmly connected and, if necessary, connect the connector all the way in. Outer temperature sensor and Front PWB (YC8) Front PWB (YC2) and Engine PWB (YC8) 2. If the wiring is disconnected, shorted or grounded, replace the wiring. 3. Replace the Outer temperature sensor. Front PWB Replace the front PWB Engine PWB 1. Check the engine software and upgrade to the latest, if necessary. 2. Replace the engine PWB. |
Error code: | 7901 |
Description: | Drum EEPROM error No response is issued from the device in reading/writing for 5 ms or more and this problem is repeated five times successively. Mismatch of reading data from two locations occurs 8 times successively. Mismatch between writing data and reading data occurs 8 times successively. |
Causes: | Defective connector cable or poor contact in the connector. Defective drum PWB. |
Remedy: | DR PWB 1. Confirm that the wiring connector is firmly connected and, if necessary, connect the connector all the way in. DR PWB and Front PWB (YC6) Front PWB (YC2) and Engine PWB (YC8) 2. If the wiring is disconnected, shorted or grounded, replace the wiring. 3. Replace the Drum unit. Front PWB Replace the front PWB Engine PWB 1. Check the engine software and upgrade to the latest, if necessary. 2. Replace the engine PWB. |
Error code: | 7902 |
Description: | Drum C EEPROM error No response is issued from the device in reading/writing for 5 ms or more and this problem is repeated five times successively. Mismatch of reading data from two locations occurs 8 times successively. Mismatch between writing data and reading data occurs 8 times successively. |
Causes: | Defective connector cable or poor contact in the connector. Defective drum PWB C. |
Remedy: | DR PWB- C 1. Confirm that the wiring connector is firmly connected and, if necessary, connect the connector all the way in. DR PWB- C and Front PWB (YC12) Front PWB (YC2) and Engine PWB (YC10) 2. If the wiring is disconnected, shorted or grounded, replace the wiring. 3. Replace the Drum unit C. Front PWB Replace the front PWB Engine PWB 1. Check the engine software and upgrade to the latest, if necessary. 2. Replace the engine PWB. |
Error code: | 7903 |
Description: | Drum M EEPROM error No response is issued from the device in reading/writing for 5 ms or more and this problem is repeated five times successively. Mismatch of reading data from two locations occurs 8 times successively. Mismatch between writing data and reading data occurs 8 times successively. |
Causes: | Defective connector cable or poor contact in the connector. Defective drum PWB M. |
Remedy: | DR PWB- M 1. Confirm that the wiring connector is firmly connected and, if necessary, connect the connector all the way in. DR PWB- M and Front PWB (YC10) Front PWB (YC2) and Engine PWB (YC10) 2. If the wiring is disconnected, shorted or grounded, replace the wiring. 3. Replace the Drum unit M. Front PWB Replace the front PWB Engine PWB 1. Check the engine software and upgrade to the latest, if necessary. 2. Replace the engine PWB. |
Error code: | 7904 |
Description: | Drum Y EEPROM error No response is issued from the device in reading/writing for 5 ms or more and this problem is repeated five times successively. Mismatch of reading data from two locations occurs 8 times successively. Mismatch between writing data and reading data occurs 8 times successively. |
Causes: | Defective connector cable or poor contact in the connector. Defective drum PWB Y. |
Remedy: | DRPWB- Y 1. Confirm that the wiring connector is firmly connected and, if necessary, connect the connector all the way in. DRPWB- Y and Front PWB (YC14) Front PWB (YC2) and Engine PWB (YC10) 2. If the wiring is disconnected, shorted or grounded, replace the wiring. 3. Replace the Drum unit Y. Front PWB Replace the front PWB Engine PWB 1. Check the engine software and upgrade to the latest, if necessary. 2. Replace the engine PWB. |
Error code: | 7911 |
Description: | Developer unit EEPROM error No response is issued from the device in reading/writing for 5 ms or more and this problem is repeated five times successively. Mismatch of reading data from two locations occurs 8 times successively. Mismatch between writing data and reading data occurs 8 times successively. |
Causes: | Defective connector cable or poor contact in the connector. Defective developer unit. |
Remedy: | Developer unit 1. Confirm that the wiring connector is firmly connected and, if necessary, connect the connector all the way in. Developer unit and Front PWB (YC7) Front PWB (YC2) and Engine PWB (YC8) 2. If the wiring is disconnected, shorted or grounded, replace the wiring. 3. Replace the Developer unit. Front PWB Replace the front PWB Engine PWB 1. Check the engine software and upgrade to the latest, if necessary. 2. Replace the engine PWB. |
Error code: | 7912 |
Description: | Developer unit C EEPROM error No response is issued from the device in reading/writing for 5 ms or more and this problem is repeated five times successively. Mismatch of reading data from two locations occurs 8 times successively. Mismatch between writing data and reading data occurs 8 times successively. |
Causes: | Defective connector cable or poor contact in the connector. Defective developer unit C. |
Remedy: | Developer unit C 1. Confirm that the wiring connector is firmly connected and, if necessary, connect the connector all the way in. Developer unit C and Front PWB (YC13) Front PWB (YC2) and Engine PWB (YC10) 2. If the wiring is disconnected, shorted or grounded, replace the wiring. 3. Replace the Developer unit C. Front PWB Replace the front PWB Engine PWB 1. Check the engine software and upgrade to the latest, if necessary. 2. Replace the engine PWB. |
Error code: | 7913 |
Description: | Developer unit M EEPROM error No response is issued from the device in reading/writing for 5 ms or more and this problem is repeated five times successively. Mismatch of reading data from two locations occurs 8 times successively. Mismatch between writing data and reading data occurs 8 times successively. |
Causes: | Defective connector cable or poor contact in the connector. Defective developer unit M. |
Remedy: | Developer unit M 1. Confirm that the wiring connector is firmly connected and, if necessary, connect the connector all the way in. Developer unit M and Front PWB (YC11) Front PWB (YC2) and Engine PWB (YC10) 2. If the wiring is disconnected, shorted or grounded, replace the wiring. 3. Replace the Developer unit M. Front PWB Replace the front PWB Engine PWB 1. Check the engine software and upgrade to the latest, if necessary. 2. Replace the engine PWB. |
Error code: | 7914 |
Description: | Developer unit Y EEPROM error No response is issued from the device in reading/writing for 5 ms or more and this problem is repeated five times successively. Mismatch of reading data from two locations occurs 8 times successively. Mismatch between writing data and reading data occurs 8 times successively. |
Causes: | Defective connector cable or poor contact in the connector. Defective developer unit Y. |
Remedy: | Developer unit Y 1. Confirm that the wiring connector is firmly connected and, if necessary, connect the connector all the way in. Developer unit Y and Front PWB (YC15) Front PWB (YC2) and Engine PWB (YC10) 2. If the wiring is disconnected, shorted or grounded, replace the wiring. 3. Replace the Developer unit Y. Front PWB Replace the front PWB Engine PWB 1. Check the engine software and upgrade to the latest, if necessary. 2. Replace the engine PWB. |
Error code: | F000 |
Description: | Communication error between the main unit and CPU |
Causes: | The panel cannot be detected since the CPU communication between the main PWB and the operation panel main PWB is unavailable. |
Remedy: | 1 Resetting the main power The communication between the main PWB and the operation panel main PWB is faulty. Remove the original and check the sensor. Next, turn off the power switch and main switch. Then, turn on the main switch and power switch when passing 5 seconds. 2 Checking the connection The connector is not properly connected. The wire or the SATA cable is faulty. Clean the terminal of the following SATA cable connector and the wire connectors and reconnect the connectors. If there is no continuity, replace the SATA cable or the wire. • Main PWB - Operation panel main PWB Wiring diagram 3 Executing U021 The backup RAM data is faulty. Execute U021 to initialize the backup RAM data. Executing U021 4 Replacing the main PWB The main PWB is faulty. Replace the main PWB. 5 Replacing the operation panel main PWB The operation panel main PWB is faulty. Replace the panel main PWB. |
Error code: | F010 |
Description: | Program read error (SSD) |
Causes: | The garbled 2bit data was detected during the program read from the flash memory. |
Remedy: | 1 (When the service call error appears after replacing the SSD) Replacing the SSD along the correct procedures The firmware is not stored in the SSD. Insert the USB memory device containing all released firmware into the main unit, and turn the main power on. Firmware Update 2 Checking the SSD (if lit after replacing the SSD) An SSD out of specification is installed. Install the SSD matching the memory capacity specification. 3 Resetting the main power The communication between the main PWB and the operation panel main PWB is faulty. Remove the original and check the sensor. Next, turn off the power switch and main switch. Then, turn on the main switch and power switch when passing 5 seconds. 4 Checking the SSD The SSD is not properly attached. Check if the SSD terminal is not faulty and clean it. Then, reinstall the SSD. 5 Checking the connection The connector is not properly connected. The wire or the SATA cable is faulty. Clean the terminal of the following SATA cable connector and the wire connectors and reconnect the connectors. If there is no continuity, replace the SATA cable or the wire. • Main PWB - Operation panel main PWB Wiring diagram 6 Executing U021 The backup RAM data is faulty. Execute U021 to initialize the backup RAM data. Executing U021 7 Replacing the SSD The SSD is faulty. Backup the data in the SSD at U026. Then, replace the SSD and turn the main power on while installing the USB memory storing the firmware for the affected model n the main unit. 8 Replacing the main PWB The main PWB is faulty. Replace the main PWB. |
Error code: | F020 |
Description: | System memory error (RAM reading/writing error or CPU memory error) |
Causes: | The error appears during the reading/writing check of the RAM for the CPU when the main unit starts up. |
Remedy: | 1 Resetting the main power The communication between the main PWB and the operation panel main PWB is faulty. Remove the original and check the sensor. Next, turn off the power switch and main switch. Then, turn on the main switch and power switch when passing 5 seconds. 2 Executing U021 The backup RAM data is faulty. Execute U021 to initialize the backup RAM data. Executing U021 3 Checking the main PWB The connector or the FFC is not properly connected. The wire, the FFC or the PWB is faulty. Clean the connectors on the main PWB and the FFC terminal. Then, reconnect the wire connector and the FFC. At that time, if the wire is pinched by other parts or it is damaged, repair or replace the wire. If the FFC terminal section is deformed or FFC is broken, replace the FFC. If the issue is not resolved, replace the main PWB. |
Error code: | F040 |
Description: | Option installation error |
Causes: | The size of the attached main memory is 2 GB when the DSDF is installed. |
Remedy: | Main memory Replace the main memory with a 4 GB one. DSDF • Remove the DSDF. • Replace the DSDF with an RADF. |
Error code: | F050 |
Description: | Engine main program error |
Causes: | The engine program cannot start up. |
Remedy: | 1 Firmware upgrade The firmware is not the latest version. Upgrade the engine firmware to the latest version Firmware Update 2 Resetting the main power The print engine ROM checksum is faulty. Remove the original and check the sensor. Next, turn off the power switch and main switch. Then, turn on the main switch and power switch when passing 5 seconds. 3 Checking the EEPROM The EEPROM is not properly attached. Reattach the EEPROM. 4 Checking the engine PWB The connector or the FFC is not properly connected. The wire, the FFC or the PWB is faulty. Clean the connectors on the engine PWB and the FFC terminal. Then, reconnect the wire connector and the FFC. At that time, if the wire is pinched by other parts or it is damaged, repair or replace the wire. If the FFC terminal section is deformed or FFC is broken, replace the FFC. If the issue is not resolved, replace the engine PWB. |
Парткод
Название
Kyocera Блок фотобарабана
Kyocera Блок проявки голубой
Kyocera Блок проявки черный
Kyocera Блок проявки пурпурный
Kyocera Блок проявки желтый
Kyocera Узел термозакрепления (печка)
Kyocera Сервисный комплект
Kyocera Тонер-картридж голубой
Kyocera Тонер-картридж черный
Kyocera Тонер-картридж пурпурный
Kyocera Тонер-картридж желтый