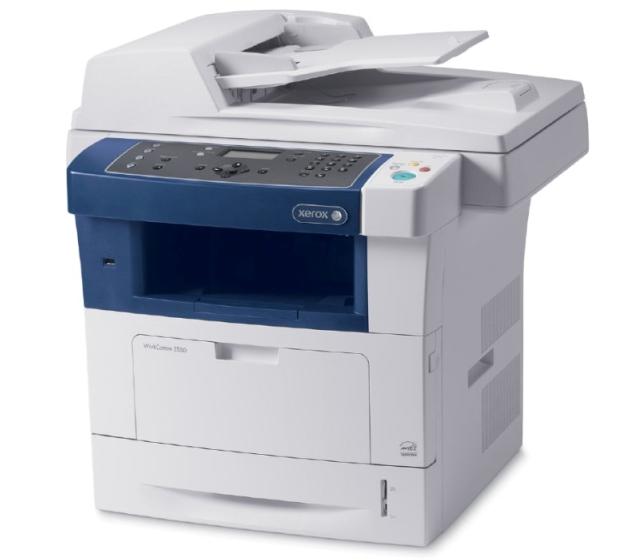
Xerox WorkCentre 3550
Рейтинг
Снят с производства
Тип устройства
МФУ
Технология печати
лазерная
Макс. формат
A4
Число страниц в месяц
75000
Скорость печати
A4
33
Цветность печати
черно-белая
Общие характеристики |
|
---|---|
Размещение |
настольный |
Макс. формат |
A4 |
Телефон |
|
Печать фотографий |
|
Сканер |
![]() |
Факс |
![]() |
Копир |
![]() |
Тип устройства |
МФУ |
Тип |
лазерный/светодиодный |
Цветность печати |
|
Технология печати |
лазерная |
Область применения |
средний офис |
Число страниц в месяц |
75 000 |
Принтер |
|
Двусторонняя печать |
![]() |
Прямая печать |
![]() |
Система непрерывной подачи чернил |
|
Печать без полей |
|
Пигментные чернила |
|
Время разогрева |
15 |
Макс, разрешение для ч/б печати |
|
По X | 1 200 |
По Y | 1 200 |
Скорость ч/б печати |
|
A4 | 33 |
Время выхода первого отпечатка |
|
Ч/б | 8,5 |
Копир |
|
Время выхода первой копии |
10 |
Макс, разрешение (ч/б) |
|
По X | 1 200 |
По Y | 1 200 |
Сканер |
|
Устройство автоподачи оригиналов |
двустороннее |
Макс. формат оригинала |
A4 |
Слайд-адаптер |
|
Стандарт TWAIN |
|
Стандарт WIA |
|
Отправка изображения по e-mail |
![]() |
Тип сканера |
планшетный/протяжный |
Разрешение сканера |
|
По Х (улучшенное) | 4 800 |
По Y | 4 800 |
Расходные материалы |
|
Количество картриджей |
1 |
Ресурс ч/б картриджа/тонера |
5 000 |
Печать на: |
|
Рулоне |
|
Фотобумаге |
|
CD/DVD |
|
Конвертах |
![]() |
Матовой бумаге |
![]() |
Глянцевой бумаге |
![]() |
Этикетках |
![]() |
Пленках |
![]() |
Карточках |
![]() |
Плотность бумаги |
|
Максимальная | 163 |
Минимальная | 60 |
Факс |
|
PC Fax |
![]() |
Цветной |
![]() |
Макс, скорость передачи данных |
33,6 Кбит/с |
Телефон |
|
Стандарт DECT |
|
Проводная трубка |
|
Беспроводная трубка |
|
АОН |
|
Caller ID |
|
Автоответчик |
|
Спикерфон |
|
Языки управления |
|
PCL 5c |
|
|
|
PPDS |
|
PostScript 2 |
|
PCL 6 |
![]() |
PostScript |
![]() |
PostScript 3 |
![]() |
PCL 5e |
![]() |
Лотки |
|
Емкость лотка ручной подачи |
50 |
Подача бумаги |
|
Максимальная | 1 050 |
Стандартная | 550 |
Вывод бумаги |
|
Стандартный | 250 |
Финишер |
|
Сортер |
|
Электронная сортировка |
|
Сортировка со сдвигом |
|
Степлер |
|
Брошюровщик |
|
Интерфейсы |
|
Wi-Fi |
|
FireWire (IEEE 1394) |
|
Wi-Fi 802.11n |
|
Bluetooth |
|
LPT |
|
AirPrint |
|
Инфракрасный порт |
|
RS-232 |
|
Веб-интерфейс |
|
Устройство для чтения карт памяти |
|
USB |
![]() |
Ethernet (RJ-45) |
![]() |
Версия USB |
2,0 |
Память/Процессор |
|
Частота процессора |
360 |
Макс, объем памяти |
512 |
Объем памяти |
256 |
Дополнительная информация |
|
Экран |
|
Работа от аккумулятора |
|
Поддержка ОС |
|
Mac OS |
![]() |
Windows |
![]() |
Linux |
|
DOS |
|
Потребляемая мощность |
|
В режиме ожидания | 20 |
При работе | 600 |
Уровень шума |
|
При работе | 55 |
В режиме ожидания | 39 |
Габариты |
|
Вес |
23,4 |
Глубина |
488 |
Ширина |
582 |
Высота |
554 |
Модули
DADF (6 of 7)
DADF (1 of 7)
Main PWB and Main Drive Assembly
Rear Cover Assembly
Duplex Drive Assembly
Fuser Assembly (1 of 3)
Registration Rolls
Front Duplex Guide Assembly
Tray 2 Assembly (2 of 2)
(Детали корпуса)
Exit Cover Assembly
Exit Feed Assembly
Main Covers
Stapler Assembly
PAPER TRAY
DADF (7 of 7)
DADF (5 of 7)
DADF (3 of 7)
FRONT COVER ASSEMBLY
User Interface
HVPS
DADF (2 of 7)
Print Cartridge
(Электронные компоненты)
DADF (4 of 7)
(Узел автоматической подачи оригиналов)
Fuser Assembly (3 of 3)
Bypass Feed Assembly (1 of 2)
Tray 2 Assembly (1 of 2)
SMPS
Scanner assembly
Duplex Assembly (1 of 3)
LSU
MAIN DRIVE ASSEMBLY
Fuser Assembly (2 of 3)
Детали None
Деталь: | Registration sensor (Q05-130) |
Парткод: | 130N01274 |
Деталь: | Transport assembly (Complete) |
Парткод: | 022N02360 |
Цена: | 3 500 ₽ |
Деталь: | DADF (Complete) |
Парткод: | 101 N01421 |

Деталь: | Left counterbalance |
Парткод: | 003N01031 |
Цена: | 1 200 ₽ |

Деталь: | Right counterbalance |
Парткод: | 003N01018 |
Цена: | 1 100 ₽ |
Деталь: | Connector Cover |
Парткод: | 002N02720 |
Деталь: | DADF harness |
Парткод: | 152N11751 |
Деталь: | FAX PWB (Parallel) |
Парткод: | 140N63304 |
Деталь: | SPEAKER |
Парткод: | 130N01532 |
Деталь: | FAX PWB (Serial) |
Парткод: | 140N63305 |
Деталь: | Main PWB (REP 3.1) |
Парткод: | 140N63297 |
Деталь: | SIM card holder |
Парткод: | 113N01308 |
Деталь: | Memory DIMM |
Парткод: | 140N63298 |
Деталь: | USB host PWB (REP 3.2) |
Парткод: | 140N63299 |
Деталь: | USB harness (REP 3.2) |
Парткод: | 117N01789 |
Деталь: | HARD DISK DRIVE |
Парткод: | 007N01596 |
Деталь: | Connection PWB |
Парткод: | 140N63303 |

Деталь: | Rear cover assembly (Complete) |
Парткод: | 002N02716 |
Цена: | 8 700 ₽ |
Деталь: | Duplex motor (MOT04-300) |
Парткод: | 127N07558 |
Деталь: | FUSER FAN |
Парткод: | 127N07485 |
Деталь: | Exit motor (MOT04-200) |
Парткод: | 127N07560 |
Цена: | 6 000 ₽ |

Деталь: | Exit drive assembly |
Парткод: | 007N01594 |
Цена: | 2 800 ₽ |
Деталь: | Duplex drive assembly |
Парткод: | 007N01592 |

Деталь: | Registration solenoid (SOL08-850) |
Парткод: | 121N01162 |
Цена: | 460 ₽ |
Деталь: | Tray 1 pickup solenoid (SOL08-810) |
Парткод: | 121N01163 |
Деталь: | Registration roll clutch |
Парткод: | 005N01031 |
Деталь: | Tray 1 paper empty sensor (Q07-110) |
Парткод: | 130N01274 |
Деталь: | Tray 1 pickup roll (NOTE) |
Парткод: | 022N02343 |
Деталь: | Front duplex guide assembly (Complete) (REP 10.3) |
Парткод: | 032N00490 |
Цена: | 6 800 ₽ |
Деталь: | Tray 2 paper empty sensor |
Парткод: | 130N01274 |
Деталь: | Tray 2 pickup solenoid (SOL08-820) |
Парткод: | 121N01164 |
Деталь: | Tray 2 PWB |
Парткод: | 140N63300 |
Деталь: | Tray 2 harness |
Парткод: | 152N11752 |

Деталь: | Clutch Assembly |
Парткод: | 007N01593 |
Цена: | 130 ₽ |
Деталь: | Pickup roll assembly |
Парткод: | 022N02345 |

Деталь: | ADF SCX-4729FD,SEC,SSDP,HIP HR-1360T,2.4 |
Парткод: | 101N01451 |
Деталь: | Плата импульсного питания (220В) |
Парткод: | 105N02190 |
Деталь: | Левая плата панели управления |
Парткод: | 140N63455 |
Деталь: | Правая плата панели управления |
Парткод: | 140N63454 |
Деталь: | MEA UNIT-COVER FRONT, ML-2571N,SAMSUNG,-, |
Парткод: | 002N02975 |
Деталь: | Out bin full sensor (Q08-720) |
Парткод: | 130N01274 |

Деталь: | Out bin full sensor actuator |
Парткод: | 120N00517 |
Цена: | 200 ₽ |
Деталь: | STATIC ELIMINATOR |
Парткод: | 125N00094 |

Деталь: | Exit cover assembly (Complete) |
Парткод: | 002N02714 |
Цена: | 1 900 ₽ |
Деталь: | Fuser terminal (REP 10.5) |
Парткод: | 152N11754 |
Деталь: | Idler assembly (REP 10.4) |
Парткод: | 130N01531 |
Деталь: | Exit roll (REP 10.4) |
Парткод: | 022N02344 |
Деталь: | Right cover (REP 28.1) |
Парткод: | 002N02713 |
Деталь: | Left cover (REP 28.1) |
Парткод: | 002N02715 |
Деталь: | Front mid cover (REP 28.3) |
Парткод: | 002N02717 |
Деталь: | Stapler |
Парткод: | 029N00395 |
Цена: | 27 200 ₽ |
Деталь: | Paper tray (Complete) |
Парткод: | 050N00518 |

Деталь: | Retard pad assembly |
Парткод: | 019N00947 |
Цена: | 1 300 ₽ |
Деталь: | Lead edge guide |
Парткод: | 055N00297 |
Деталь: | Lead edge guide spring |
Парткод: | 009N01604 |
Деталь: | Drive assembly (Complete) |
Парткод: | 007N01595 |
Цена: | 4 800 ₽ |
Деталь: | Scan motor (MOT05-200) |
Парткод: | 127N07562 |
Деталь: | Feed assembly (Complete) ( |
Парткод: | 022N02359 |
Деталь: | Retard pad assembly |
Парткод: | 003N01030 |
Деталь: | Document detect sensor (Q05-100) |
Парткод: | 130N01274 |
Деталь: | DADF paper length sensor (Q05-120) |
Парткод: | 130N01274 |
Деталь: | Input tray assembly (Complete) |
Парткод: | 002N02741 |
Деталь: | Front cover assembly (Complete) |
Парткод: | 002N02718 |
Цена: | 2 800 ₽ |
Деталь: | Start button label (French) |
Парткод: | 091N80276 |
Деталь: | Start button label (Symbol) |
Парткод: | 091 N80275 |
Деталь: | Services label (French) |
Парткод: | 091 N80278 |
Деталь: | Services label (Symbol) |
Парткод: | 091 N80277 |
Деталь: | Numeric key pad label (French) |
Парткод: | 091N80280 |
Деталь: | Numeric key pad label (Symbol) |
Парткод: | 091N80279 |
Деталь: | Front cover panel |
Парткод: | 140N63296 |
Деталь: | Start button label (English) |
Парткод: | 091 N80272 |
Деталь: | Language key |
Парткод: | 029N00384 |
Деталь: | Machine status key |
Парткод: | 029N00385 |
Деталь: | Login/out key |
Парткод: | 029N00386 |
Деталь: | Help key |
Парткод: | 029N00387 |
Деталь: | Numerical keys |
Парткод: | 029N00388 |
Деталь: | Power key |
Парткод: | 029N00389 |
Деталь: | Power key holder |
Парткод: | 029N00390 |
Деталь: | Interrupt Key |
Парткод: | 029N00391 |
Деталь: | Job interrupt key |
Парткод: | 029N00392 |
Деталь: | STOP KEY |
Парткод: | 029N00393 |
Деталь: | Start Key |
Парткод: | 029N00394 |
Деталь: | Rubber key mat (left hand side) |
Парткод: | 029N00396 |
Деталь: | Rubber key mat (right hand side) |
Парткод: | 029N00397 |
Деталь: | Right keys PWB |
Парткод: | 140N63295 |
Деталь: | Services label (English) |
Парткод: | 091 N80273 |
Деталь: | Numeric key pad label (English) |
Парткод: | 091N80274 |
Деталь: | Name label |
Парткод: | 015N00618 |
Деталь: | UI PWB (REP 2.2) |
Парткод: | 140N63294 |

Деталь: | Touch screen (REP 2.2) |
Парткод: | 123N00250 |
Цена: | 18 000 ₽ |
Деталь: | UI assembly (Complete) (REP 2.1) |
Парткод: | 123N00251 |
Деталь: | HVPS (REP 1.2) |
Парткод: | 105N02141 |
Деталь: | DADF lift solenoid (SOL05-320) (REP 5.2) |
Парткод: | 121 N01160 |
Деталь: | Document pad |
Парткод: | 095N00340 |
Деталь: | DADF PWB |
Парткод: | 140N63301 |

Деталь: | ADF SCX-4729FD,SEC,SSDP,HIP HR-1360T,2.4 |
Парткод: | 101N01451 |
Деталь: | Плата импульсного питания (220В) |
Парткод: | 105N02190 |
Деталь: | Левая плата панели управления |
Парткод: | 140N63455 |
Деталь: | Правая плата панели управления |
Парткод: | 140N63454 |
Деталь: | MEA UNIT-COVER FRONT, ML-2571N,SAMSUNG,-, |
Парткод: | 002N02975 |

Деталь: | Pickup roll assembly ( |
Парткод: | 130N01533 |
Цена: | 3 900 ₽ |

Деталь: | ADF SCX-4729FD,SEC,SSDP,HIP HR-1360T,2.4 |
Парткод: | 101N01451 |
Деталь: | Плата импульсного питания (220В) |
Парткод: | 105N02190 |
Деталь: | Левая плата панели управления |
Парткод: | 140N63455 |
Деталь: | Правая плата панели управления |
Парткод: | 140N63454 |
Деталь: | MEA UNIT-COVER FRONT, ML-2571N,SAMSUNG,-, |
Парткод: | 002N02975 |
Деталь: | Heat lamp (110V) |
Парткод: | 122N00260 |
Деталь: | Heat lamp (220V) |
Парткод: | 122N00261 |
Цена: | 4 600 ₽ |
Деталь: | Bypass paper empty sensor (Q07-510) |
Парткод: | 130N01274 |
Деталь: | Pickup Rubber |
Парткод: | 130N01534 |
Цена: | 180 ₽ |
Деталь: | Bypass feed assembly (Complete) |
Парткод: | 050N00520 |
Цена: | 7 200 ₽ |
Деталь: | Tray 2 drive assembly |
Парткод: | 127N07563 |
Деталь: | Tray 2 assembly (Complete) |
Парткод: | 050N00519 |

Деталь: | SMPS (220V) (REP 1.1) |
Парткод: | 105N02143 |
Цена: | 5 600 ₽ |
Деталь: | SMPS fan |
Парткод: | 127N07354 |
Деталь: | SMPS (110V) (REP 1.1) |
Парткод: | 105N02119 |
Деталь: | MAIN FAN |
Парткод: | 127N07559 |
Цена: | 2 500 ₽ |
Деталь: | CCD home sensor (A), Platen cover sensor (B) (REP 14.2) |
Парткод: | 130N01274 |
Деталь: | Scan motor drive assembly |
Парткод: | 127N07564 |
Цена: | 5 500 ₽ |
Деталь: | CCD module (REP 14.2) |
Парткод: | 133N23230 |
Цена: | 4 400 ₽ |
Деталь: | SCAN motor |
Парткод: | 127N07561 |
Деталь: | DADF connector |
Парткод: | 152N11750 |
Деталь: | CCD module belt |
Парткод: | 109N00542 |
Цена: | 2 300 ₽ |
Деталь: | Scanner cover (REP 14.2) |
Парткод: | 002N02719 |

Деталь: | CCD module cable |
Парткод: | 117N01788 |
Цена: | 2 400 ₽ |
Деталь: | Scanner assembly (Complete) (REP 14.1) |
Парткод: | 109N00688 |
Деталь: | Duplex assembly (Complete) |
Парткод: | 101 N01420 |
Коды ошибок
01-100
01-110
01-700
01A
02-100, 02-200
03-200 ... 03-250
03-300 ... 03-340
03-410, 03-411, 03-412
03-420, 03-421, 03-422
03-450
03-510, 03-520, 03-558, 03-559
03-600
03-800
03-900
03-940
03-970
05-100
05-500
05-600
05-700
05-900
05-920
06-100, 06-200
07-110
07-130
07-210
07-230
07-231
07-500
07-530
08-100
08-200
08-500
08-600
08-610
08-700
09-100
09-350
09-450
09-550, 09-820, 09-830
10-100, 10-200
10-300
10-500
10-510
14-100
15-100 ... 15-500
17-100 ... 17-610
17-700 ... 17-810
17-900
20-100 ... 20-900
20A
OF1
OF2
OF3
OF4
OF5
OF6
OF7
Описание
Error code: | 01-100 |
Display: | Door is open Close it |
Description: | Door Open RAP 01-100 The machine has detected that the right cover assembly is open. When the cover is open, there is no +24V supply to the motors or the HVPS. |
Causes: | The machine has detected that the front door is open. When the front door is open there is no +24V supply to the motors or the HVPS. |
Remedy: | 1. Switch off the machine, then switch on the machine. 2. Check that the interlock switch actuator on the right cover assembly, PL 7.30 Item 1 is not missing or damaged. 3. Check that the right cover assembly closes correctly. 4. Enter dC330 code 01-100. Check the side cover interlock switch assembly (S01-100), PL 4.15 Item 12. 5. Check the wiring between the side cover interlock switch and CN8 on the Main PWB. If necessary, install a side cover interlock switch assembly, PL 4.15 Item 12. 6. If necessary, install a new main PWB, PL 1.10 Item 1. |
Error code: | 01-110 |
Display: | Rear Door Open |
Description: | Fuser Door Open |
Causes: | The machine has detected that the fuser door is open. When the front door is open there is no +24V supply to the motors or the HVPS. |
Remedy: | 1. Switch off the machine, then switch on the machine. 2. Open the rear door, then the fuser door. 3. Check that the interlock switch actuator on the fuser door is not missing or damaged. If necessary, install a new fuser door. 4. Check that the fuser door assembly closes correctly. 5. If necessary, install a new HVPS. NOTE: The fuser door interlock switch is mounted on the HVPS. |
Error code: | 01-700 |
Description: | Stapler Door Open |
Causes: | The machine has detected that the stapler door is open. When the stapler door is open there is no +24V to the stapler |
Remedy: | 1. Switch off the machine, then switch on the machine. 2. Open the stapler door. 3. Check that the interlock switch actuator on the stapler door is not missing or damaged. If necessary, install a new stapler door. 4. Check that the stapler door assembly closes correctly. 5. Check the stapler door interlock switch. If necessary, install a new stapler door interlock switch. NOTE: There is no component control code for the stapler door interlock switch. 6. Check the wiring between the stapler door interlock switch and CN3 on the Connection PWB. 7. If necessary, install a new connection PWB. |
Error code: | 01A |
Description: | Power Failure RAP Use this RAP to identify the cause of a power supply failure. |
Remedy: | 1. Ensure the supply voltage is correct. If possible, connect the machine to a known good power supply. If the original power supply is faulty, inform the customer. 2. Disconnect the power cord from the power outlet and the machine. Check the continuity of the power cord. If necessary, install a new power cord. 3. Refer to Wiring Diagram 1. Disconnect CON01 on Power Supply Unit 1. Check for AC supply voltage between pins 1 and 2 on the connector. If necessary, install a new main power socket, PL 1.10 Item 6. 4. Check the fuse F01 on power supply unit 1. If necessary, install a new power supply unit 1, PL 1.10 Item 3. NOTE: Fuse F01 is not spared. 5. Disconnect CON7 from Power Supply Unit 2. Check for AC supply voltage between pins 1 and 2 on the connector. If necessary, install a new power supply 1, PL 1.10 Item 3 6. Remove the fuser, REP 10.1. Check for continuity across the fuser heat roll. Install new components as necessary, PL 10.26. NOTE: A cold fuser heat roll has a resistance of approximately 16.5 ohms (220V/240V) or 2 ohms (110V). 7. Check the fuse F1 on power supply unit 2. If necessary, install a new power supply unit 2, PL 1.10 Item 4. NOTE: Fuse F1 is not spared. 8. Switch off the power to the machine. Disconnect CON51 on Power Supply Unit 1. 9. Switch on the power to the machine. If the machine switches on, perform step 10. If the machine fails to switch on, go to step 11. 10. Reconnect CON51 on Power Supply Unit 1. Disconnect all connectors on Power Supply Unit 2. Sequentially reconnect CON2, CON3, CON8 and CON9 onto Power Supply Unit 2. If the faulty circuit is identified, repair the wiring or install components as necessary. If the machine fails to switch on, go to step 11. 11. Reconnect all connectors to Power Supply Unit 1 and Power Supply Unit 2. 12. Disconnect all connectors on the Main PWB except for the battery, CN29. Refer to Wiring Diagram 8. Check for +5V on CN27. If +5V is not present, check the wiring between CON71 on Power Supply Unit 1 and CN27 on the Main PWB. If necessary, install a new Power supply unit 1, PL 1.10 Item 3. 13. Reconnect CN27 to the Main PWB. Check for +24V on CN27. If +24V is not present, check the wiring between CON71 on Power Supply Unit 1 and CN27 on the Main PWB. If necessary, install a new Power supply unit 1, PL 1.10 Item 3. 14. Sequentially reconnect each connector onto the Main PWB. If the faulty circuit is identified, repair the wiring or install components as necessary. If the machine still fails to switch on, install a new main PWB, PL 1.10 Item 1. 15. If the fault is still present, install a new components as necessary: • Power supply unit 1, PL 1.10 Item 3. • Power supply unit 2, PL 1.10 Item 4. • HVPS, PL 1.10 Item 2 |
Error code: | 02-100, 02-200 |
Description: | USB Faults |
Causes: | 02-100 The USB device is invalid. Only SCSI type memory is supported. 02-200 The USB memory is full or there is no response from the USB memory |
Remedy: | 1. Make sure that the customer is using a valid USB device with sufficient free space. 2. Check the wiring between the USB host PWB and CN7 on the Main PWB. 3. Install new components as necessary: • USB harness • USB host PWB 4. Perform OF7 Main PWB Check RAP. |
Error code: | 03-200 ... 03-250 |
Description: | MSOK Faults |
Causes: | These are the faults displayed when the machine encounters MSOK problems. The faults are listed in code order, together with any recommended actions. |
Remedy: | 03-200 System Fault - IOT Serial Number Invalid, Call for Assistance The IOT serial number is invalid. Perform the following: 1. Contact Field Engineering for assistance. 03-210 System Fault - MSOK Invalid - Call for Assistance (MMSOK) The MSOK serial number is invalid. Perform the following: 1. Contact Field Engineering for assistance. 03-220 System Fault - MSOK Invalid - Call for Assistance MMSOK Bit The MSOK has the manufacturing SOK serial number but not the MMSOK part. Perform the following: 1. Contact Field Engineering for assistance. 03-230 System Fault - MSOK Page Count Exceeded The IOT has attempted to print more pages that the MMSOK can print. Perform the following: 1. Remove the MMSOK, then install the MSOK. 2. Contact Field Engineering for further assistance. 03-240 System Fault - Invalid Machine or MSOK SN The MSOK SN is empty. Perform the following: 1. Contact Field Engineering for assistance. 03-250 MSOK Missing The MSOK is not installed. Perform the following: 1. Check that the MSOK is connected to the main PWB. |
Error code: | 03-300 ... 03-340 |
Description: | OSOK Faults |
Causes: | These are the faults displayed when the machine encounters OSOK problems. The faults are listed in code order, together with any recommended actions. |
Remedy: | 03-300 System Fault - Message: Please Insert Option Key to Enable Machine Per BS The machine has detected that the OSOK is not installed. Perform the following: 1. Install the PEK. 2. Contact Field Engineering for further assistance. 03-310 System Fault - Message: OSOK Previously Used in Different Machine Per BS The machine has detected that the OSOK has previously been used in a different machine. Perform the following: 1. Obtain, then install a valid FEK. 2. Contact Field Engineering for further assistance. 03-320 System Fault - Option SIM Invalid The machine has detected that the OSOK has previously been used in a different machine. Perform the following: 1. Obtain, then install a valid FEK. 2. Contact Field Engineering for further assistance. 03-330 System Fault - Not Inserted Properly The machine has detected that the OSOK is not installed correctly. Perform the following: 1. Remove, then reinstall the OSOK. 2. Contact Field Engineering for further assistance. 03-340 Option Installed Remove SIM The option has been successfully installed. Perform the following: 1. Remove the FEK. 2. Contact Field Engineering for further assistance. |
Error code: | 03-410, 03-411, 03-412 |
Description: | Tray 1 Paper Information Mismatch |
Causes: | 03-410 The machine has detected a tray 1 paper colour, type or size mismatch during a print job. 03-411 The machine has detected a tray 1 paper type mismatch during a print job. 03-412 The machine has detected a tray 1 paper size mismatch during a print job. |
Remedy: | 1. If the fault is present when printing, check that the print driver and machine tray information are correct. 2. Go to GP 4 System Administration Tools. Check that the relevant tray paper type, colour and size settings are correct. |
Error code: | 03-420, 03-421, 03-422 |
Description: | Tray 2 Paper Information Mismatch |
Causes: | 03-420 The machine has detected a tray 2 paper colour, type or size mismatch during a print job. 03-421 The machine has detected a tray 2 paper type mismatch during a print job. 03-422 The machine has detected a tray 2 paper size mismatch during a print job. |
Remedy: | 1. If the fault is present when printing, check that the print driver and machine tray information are correct. 2. Go to GP 4 System Administration Tools. Check that the relevant tray paper type, colour and size settings are correct. |
Error code: | 03-450 |
Display: | Load A4 In Bypass or Paper mismatch Tray 1 Load [A4] [Plain] |
Description: | Bypass Tray Paper Information Mismatch |
Causes: | The machine has detected a bypass tray paper colour, type or size mismatch during a print job. |
Remedy: | 1. If the fault is present when printing, check that the print driver and machine tray information are correct. 2. Go to GP 4 System Administration Tools. Check that the relevant tray paper type, colour and size settings are correct. |
Error code: | 03-510, 03-520, 03-558, 03-559 |
Description: | Foreign Device Interface Fault |
Causes: | 03-510 The foreign device interface is not detected. 03-520 The foreign device interface is not active. 03-558 The foreign device interface is not active. 03-559 The foreign device interface is no longer active. |
Remedy: | 1. If there is credit in the foreign device, check the wiring between the foreign device and the foreign device interface PWB . 2. Check that the foreign device interface PWB is securely connected to CN13 the Main PWB. 3. If necessary: a. Install a new foreign device interface PWB . b. Perform OF7 Main PWB Check RAP. |
Error code: | 03-600 |
Display: | Memory Failure |
Description: | Memory Failure RAP 03-600 The machine has detected a memory access failure |
Causes: | The machine has detected a memory access failure. |
Remedy: | 1. Switch off the machine, then switch on the machine. 2. Remove, then reinstall the memory DIMM, PL 1.10 Item 22. 3. Install new components as necessary: • Memory DIMM, PL 1.10 Item 22. • Main PWB, PL 1.10 Item 1. |
Error code: | 03-800 |
Display: | Check Internal Drive |
Description: | Check HDD 03-800 The machine has detected a fault with the hard disk drive (HDD). |
Causes: | The machine has detected a fault with the hard disk drive (HDD). |
Remedy: | 1. Switch off the machine, then switch on the machine. 2. Check that the HDD PWB, PL 1.10 Item 17 is securely connected to CN20 on the Main PWB. 3. Check that the HDD ribbon cable, PL 1.10 Item 18 is securely connected to the HDD PWB and the HDD. 4. Install new components as necessary: • HDD harness, PL 1.10 Item 18. • HDD PWB, PL 1.10 Item 17. • HDD, PL 1.10 Item 11. • Main PWB, PL 1.10 Item 1. |
Error code: | 03-900 |
Description: | GUI to MCB Communications Fault RAP 03-900 A user interface to main PWB communications error has been detected |
Causes: | A user interface to main PWB communications error has been detected. |
Remedy: | 1. Switch off the machine, then switch on the machine. 2. Check the wiring between CN2 on the Main PWB and CN7 on the UI PWB. 3. Install new components as necessary: • UI PWB, PL 2.10 Item 4. • Main PWB, PL 1.10 Item 1. |
Error code: | 03-940 |
Description: | Main PWB to Tray 2 Communications Fault |
Causes: | A main PWB to tray 2 PWB communications error has been detected. |
Remedy: | 1. Switch off the machine, then switch on the machine. 2. Check the wiring between CN33 and CN34 on the Main PWB and CN7 on the Tray 2 PWB. 3. If necessary: a. Install new components: • Tray 2 connector . • Tray 2 PWB . b. Perform OF7 Main PWB Check RAP. |
Error code: | 03-970 |
Description: | Main PWB Watchdog Detects Software Lockup |
Causes: | The main PWB software has stopped responding. |
Remedy: | 1. Switch off the machine, then switch on the machine. 2. Reload the software, GP 6. 3. Perform OF7 Main PWB Check RAP. |
Error code: | 05-100 |
Display: | Original Paper Jam Paper jam inside of Doc Feeder. |
Description: | DADF Jam 1 RAP 05-100 The lead edge or trail edge of the document failed to actuate or deactuate the scan sensor within the correct time. |
Causes: | The lead edge of the document failed to actuate the scan sensor within the correct time after registration solenoid actuation. |
Remedy: | 1. Open the DADF top cover assembly, PL 5.15 Item 11. Remove all jammed paper. 2. Check the document path for damage or obstructions. 3. Check that the following components are clean and rotate freely. • Registration roll, PL 5.15 Item 21. • Registration roll idlers, PL 5.15 Item 28. 4. Remove the DADF left guide, PL 5.20 Item 9. 5. Check that the scan sensor actuator, PL 5.25 Item 28 moves freely and is not damaged. 6. Enter dC330 code 05-140. Check the scan sensor (Q05-140). NOTE: The scan sensor is mounted on the DADF PWB, PL 5.20 Item 6. 7. Remove the DADF rear cover, PL 5.10 Item 4. Enter dC330 code 05-200. Check that the DADF scan motor, PL 5.25 Item 12 runs and drives the scan roll, PL 5.25 Item 23. 8. Close the DADF top cover assembly. While the DADF scan motor runs, stack the code 05-310 to energize the registration clutch (CL05-310). Check that the registration roll, PL 5.15 Item 21 rotates. 9. Check the wiring between the DADF scan motor and CN4 on the DADF PWB. 10. Check the wiring between the registration clutch, PL 5.25 Item 19 and CN6 on the DADF PWB. If necessary, install a new registration clutch, PL 5.25 Item 19. 11. If necessary, install new components: • DADF PWB, PL 5.20 Item 6. • DADF scan motor, PL 5.25 Item 12. • DADF scan motor assembly, PL 5.25 Item 10. • Document transport assembly, PL 5.10 Item 2. |
Error code: | 05-500 |
Description: | DADF Jam 5 RAP 05-500 The machine has detected that the DADF, DADF top cover assembly or exit assembly are open during run. |
Causes: | The machine has detected that the DADF door assembly is open during run. |
Remedy: | 1. Open the DADF top cover assembly, PL 5.15 Item 11. Remove all jammed paper. 2. Raise the DADF input tray, PL 5.10 Item 5. Remove all jammed paper. 3. Open the DADF. Check that the platen cover sensor actuator, PL 14.10 Item 12 moves freely and is not damaged. 4. Enter dC330 code 05-400. Check the platen cover sensor (Q05-400), PL 14.10 Item 14. 5. Check the wiring between the platen cover sensor and CN3 on the Scanner PWB. If necessary, install a new platen cover sensor, PL 14.10 Item 14. 6. Open the DADF top cover assembly, PL 5.15 Item 11. Check that the door open switch actuator is not damaged. 7. Enter dC330 code 05-160. Check the DADF door open switch (S05-160), PL 5.25 Item 8. 8. Check the wiring between the DADF door open switch and CN6 on the DADF PWB. If necessary, install a new DADF door open switch, PL 5.25 Item 8. 9. Open the exit assembly, PL 5.20 Item 26. Check that the exit open sensor actuator is not damaged. 10. Enter dC330 code 05-180. Check the exit open sensor (Q05-180), PL 5.20 Item 16. 11. Check the wiring between the exit open sensor and CN6 on the DADF Sensor PWB. If necessary, install a new exit open sensor, PL 5.20 Item 16. 12. Check the wiring between CN1 on the DADF Sensor PWB and CN3 on the DADF PWB. 13. If necessary, install new components: • DADF PWB, PL 5.20 Item 6. • DADF sensor PWB, PL 5.20 Item 4. • Document transport assembly, PL 5.10 Item 2. • Scanner assembly, PL 14.10 Item 1. |
Error code: | 05-600 |
Display: | Original Paper Jam Paper jam inside of Doc Feeder. |
Description: | DADF Jam 6 RAP 05-600 The machine has detected that a DADF sensor is actuated when the machine is switched on. |
Causes: | The machine has detected that a DADF sensor is actuated when the machine is switched on. |
Remedy: | 1. Open the DADF top cover assembly, PL 5.15 Item 11. Remove all jammed paper. 2. Raise the DADF input tray, PL 5.10 Item 5. Remove all jammed paper. 3. Check the document path for damage or obstructions. 4. Check that the following actuators move freely and are not damaged: • Document detect sensor actuator, PL 5.20 Item 17. • Paper width sensor actuator, PL 5.20 Item 17. • Paper length sensor actuator, PL 5.10 Item 14. • Registration sensor actuator, PL 5.15 Item 12. • Scan sensor actuator, PL 5.25 Item 28. • Gate sensor actuator, PL 5.10 Item 26. • Duplex sensor actuator, PL 5.25 Item 27. 5. Enter dC330. Check the following sensors. Install new components as necessary: • Code 05-100, document detect sensor (Q05-100), PL 5.20 Item 13. • Code 05-110, paper width sensor (Q05-110), PL 5.20 Item 13. • Code 05-120, paper length sensor (Q05-120), PL 5.10 Item 12. • Code 05-130, registration sensor (Q05-130), PL 5.15 Item 14. • Code 05-140, scan sensor (Q05-140). • Code 05-150, gate sensor (Q05-150), PL 5.10 Item 24. • Code 05-170, duplex sensor (Q05-170). NOTE: The scan sensor and duplex sensor are mounted on the DADF PWB, PL 5.20 Item 6. 6. Check the following wiring: • Between the document detect sensor, and CN4 on the DADF Sensor PWB. • Between the paper width sensor and CN4 on the DADF Sensor PWB. • Between the paper length sensor and CN3 on the DADF Sensor PWB. • Between the registration sensor and CN5 on the DADF Sensor PWB. • Between the gate sensor and CN2 on the DADF Sensor PWB. • Between CN1 on the DADF Sensor PWB and CN3 on the DADF PWB. 7. If necessary, install new components: • DADF PWB, PL 5.20 Item 6. • DADF sensor PWB, PL 5.20 Item 4. • Document transport assembly, PL 5.10 Item 2. |
Error code: | 05-700 |
Description: | DADF Jam 7 RAP 05-700 The machine has detected that a oversize document has been fed. |
Causes: | The machine has detected that an oversize document has been fed. |
Remedy: | 1. Open the DADF top cover assembly, PL 5.15 Item 11. Remove all jammed paper. 2. Raise the DADF input tray, PL 5.10 Item 5. Remove all jammed paper. 3. Check that the customer is not attempting to feed documents outside of specification, refer to GP 8 DADF Document Feeding Specifications. 4. Check the feed roll assembly, PL 5.15 Item 5. If necessary, install a new feed roll assembly, PL 5.15 Item 5. 5. Check the retard pad, PL 5.20 Item 12. If necessary, install a new retard pad, PL 5.20 Item 12. 6. Check that the registration sensor actuator, PL 5.15 Item 12 moves freely and is not damaged. 7. Enter dC330 code 05-130. Check the registration sensor (Q05-130), PL 5.15 Item 14. 8. Check the wiring between the registration sensor and CN5 on the DADF Sensor PWB. If necessary, install a new registration sensor, PL 5.15 Item 14. 9. If necessary, install new components: • DADF PWB, PL 5.20 Item 6. • DADF sensor PWB, PL 5.20 Item 4. • Document transport assembly, PL 5.10 Item 2. |
Error code: | 05-900 |
Display: | Original Paper Jam Paper jam inside of Doc Feeder. |
Description: | DADF Jam 0 RAP 05-900 The lead edge of the document failed to actuate the registration sensor within the correct time. |
Causes: | The lead edge of the document failed to actuate the registration sensor within the correct time. |
Remedy: | 1. Remove all jammed paper from the DADF input tray. 2. Open the DADF top cover assembly, PL 5.15 Item 11. Check the document path for damage or obstructions. 3. Check the feed roll assembly, PL 5.15 Item 5. If necessary, install a new feed roll assembly, PL 5.15 Item 5. 4. Check the retard pad, PL 5.20 Item 12. If necessary, install a new retard pad, PL 5.20 Item 12. 5. Check that the registration sensor actuator, PL 5.15 Item 12 moves freely and is not damaged. 6. Enter dC330 code 05-130. Check the registration sensor (Q05-130), PL 5.15 Item 14. 7. Check the wiring between the registration sensor and CN5 on the DADF Sensor PWB. If necessary, install a new registration sensor, PL 5.15 Item 14. 8. Check the wiring between CN1 on the DADF Sensor PWB and CN3 on the DADF PWB. 9. Enter dC330 code 05-200. Check that the DADF scan motor (MOT05-200), PL 5.25 Item 12 runs. 10. While the DADF scan runs, stack the code 05-300 to energize the pick up clutch (CL05- 300). Check that the feed roll, PL 5.15 Item 5 rotates. 11. Check the wiring between the pick up clutch and CN6 on the DADF PWB. If necessary, install a new pick up clutch, PL 5.15 Item 4. 12. Check the wiring between the DADF scan motor and CN4 on the DADF PWB. 13. If necessary, install new components: • DADF PWB, PL 5.20 Item 6. • DADF sensor PWB, PL 5.20 Item 4. • DADF scan motor, PL 5.25 Item 12. • DADF scan motor assembly, PL 5.25 Item 10. • Document transport assembly, PL 5.10 Item 2. |
Error code: | 05-920 |
Display: | Scanner door Open |
Description: | DADF Door Open RAP 05-920 The machine has detected that the DADF door is open. |
Causes: | The machine has detected that the DADF door is open. |
Remedy: | 1. Open the DADF top cover assembly, PL 5.15 Item 11. Check that the DADF door open switch actuator on the top cover, PL 5.15 Item 22 is not missing or damaged. Install new components as necessary, PL 5.15. 2. Enter dC330 code 05-160. Check the DADF door open switch (S05-160), PL 5.25 Item 8. 3. Check the wiring between the DADF door open switch and CN6 on the DADF PWB. If necessary, install a new DADF door open switch, PL 5.25 Item 8. 4. If necessary, install new components: • DADF PWB, PL 5.20 Item 6. • Document transport assembly, PL 5.10 Item 2. |
Error code: | 06-100, 06-200 |
Description: | LSU Error RAP 06-100 The machine has detected that the LSU did not reach a ready state within the correct time. 06-200 The machine did not detect the laser beam within the correct time. |
Causes: | 06-100 The machine has detected that the LSU did not reach a ready state within the correct time. 06-200 The machine did not detect the laser beam within the correct time. |
Remedy: | 1. Switch off the machine, then switch on the machine. 2. Enter dC330 codes 06-100 and 06-110. Check that the LSU motor is up to the required speed. 3. Check the wiring between the LSU and CN5 on the Main PWB. 4. Install new components as necessary: • LSU, PL 6.10 Item 1. • Main PWB, PL 1.10 Item 1. |
Error code: | 07-110 |
Display: | Tray 1 Empty |
Description: | Paper Empty at Tray 1 RAP 07-110 The machine has detected that tray 1 is empty. |
Causes: | The machine has detected that tray 1 is empty. |
Remedy: | 1. Remove tray 1. Check that the tray 1 paper empty sensor actuator, PL 8.10 Item 4 moves freely and is not damaged. 2. Replace tray 1. Listen for the tray elevator to raise the knock-up plate. If the plate does not rise, check the wiring between the tray 1 elevator motor and CN19 on the Main PWB. If necessary, install new components: • Tray 1 elevator motor, PL 7.15 Item 8. • Tray feed assembly, PL 8.10 Item 1. 3. Enter dC330 code 07-110. Check the tray 1 paper empty sensor (S07-110), PL 8.10 Item 2. 4. Check the wiring between the tray 1 paper empty sensor and CN19 on the Main PWB. If necessary, install a new tray 1 paper empty sensor, PL 8.10 Item 2. 5. If necessary, install new components: • Tray 1 feed assembly, PL 8.10 Item 1. • Main PWB, PL 1.10 Item 1. |
Error code: | 07-130 |
Display: | Paper Jam in Tray 1 |
Description: | Jam 0 From Tray 1 RAP 07-130 The lead edge of the paper failed to actuate the registration sensor within the correct time after paper was fed from tray 1. |
Causes: | The lead edge of the paper failed to actuate the registration sensor within the correct time after paper was fed from tray 1. |
Remedy: | 1. Pull out tray 1. Remove all jammed paper. 2. Check the paper path for damage or obstructions. 3. Check that the registration sensor actuator, PL 8.15 Item 4 moves freely and is not damaged. If necessary, install a new registration sensor actuator assembly, PL 8.15 Item 13. 4. Enter dC330 code 08-500. Check the registration sensor (Q08-500), PL 8.15 Item 8. 5. Check the wiring between the registration sensor and CN13 on the Main PWB. If necessary, install a new registration sensor, PL 8.15 Item 8. 6. Check that the feed sensor actuator, PL 8.15 Item 5 moves freely and is not damaged. If necessary, install a new feed sensor actuator assembly, PL 8.15 Item 14. 7. Enter dC330 code 08-100. Check the feed sensor (Q08-100), PL 8.15 Item 8. 8. Check the wiring between the feed sensor and CN13 on the Main PWB. If necessary, install a new feed sensor, PL 8.15 Item 8. 9. Enter dC330 code 04-100 to run the main BLDC motor. 10. While the main BLDC motor runs, stack the code 08-810 to energize the tray 1 pickup clutch (CL08-810). Check that the tray 1 feed roll, PL 8.10 Item 12 rotates. 11. Check the wiring between the tray 1 pickup clutch and CN13 on the Main PWB. Install new components as necessary, PL 4.20, PL 7.15 and PL 8.10. 12. While the main BLDC motor runs, stack the code 08-850 to energize the registration clutch (CL08-850). Check that the registration roll, PL 4.15 Item 1 rotates. 13. Check the wiring between the registration clutch and CN13 on the Main PWB. Install new components as necessary, PL 4.15 and PL 4.20. 14. Check that the following components are clean and rotate freely, install new components as necessary: • Tray 1 feed roll, PL 8.10 Item 12. • Tray 1 nudger roll, PL 8.10 Item 12. • Tray 1 retard roll, PL 7.15 Item 20. • Registration roll, PL 4.15 Item 1. • Registration roll idler, PL 4.15 Item 7. 15. If necessary, install new components: • Tray feed assembly, PL 8.10 Item 1. • Main PWB, PL 1.10 Item 1. |
Error code: | 07-210 |
Display: | Tray 2 Empty |
Description: | Paper Empty at Tray 2 |
Causes: | The machine has detected that tray 2 is empty. |
Remedy: | 1. Pull out tray 2. Check that the paper empty actuator moves freely and is not damaged. 2. Enter dC330 code 07-230. Check the tray 2 paper empty sensor (S07-230) . 3. Check the wiring between the paper empty sensor and CN1 on the Tray 2 PWB. If necessary, install a new paper empty sensor . 4. Check the wiring between CN7 on the Tray PWB and CN33 and CN34 on the Main PWB. 5. If necessary: a. Install a new tray 2 PWB . b. Perform OF7 Main PWB Check RAP. |
Error code: | 07-230 |
Display: | Paper Jam in Tray 2 |
Description: | Jam 0 From Tray 2 |
Causes: | The lead edge of the paper failed to actuate the registration sensor within the correct time after paper was fed from tray 2. |
Remedy: | 1. Pull out tray 1 and tray 2. Remove all jammed paper. 2. Check the paper path for damage or obstructions. 3. Remove the pickup roll assembly . Check that the pickup roll is clean. If necessary, install a new pickup roll assembly . 4. Check the retard pad on tray 2. If necessary, install a new retard pad assembly . 5. Check that the following components are clean and rotate freely, install new components as necessary: • Registration roll . • Registration roll idler . 6. Check that the registration sensor actuator moves freely and is not damaged. If necessary, install a new registration sensor actuator . 7. Enter dC330 code 08-500. Check the registration sensor (Q08-500). If necessary, install a new HVPS . NOTE: The registration sensor is mounted on the HVPS. 8. Enter dC330 code 08-920 to run the tray 2 feed motor. 9. Check the wiring between the tray 2 feed motor and CN8 on the Tray 2 PWB. 10. While the tray 2 feed motor runs, stack the code 08-820 to energize the tray 2 pickup clutch (CL08-820). Check that the tray 2 pickup roll assembly and feed roll rotate. Install new components as necessary . 11. Check the wiring between the tray 2 pickup clutch and CN11 on the Tray 2 PWB. 12. Enter dC330 code 04-100 to run the main BLDC motor. 13. Check the wiring between the main BLDC motor and CN38 on the Main PWB. 14. While the main BLDC motor runs, stack the code 08-850 to energize the registration clutch (CL08-850). Check that the registration roll does not rotate. Install new components as necessary . 15. Check the wiring between the registration clutch and CN35 on the Main PWB. 16. If necessary: a. Install new components: • Front duplex guide assembly . • Tray 2 feed motor . • Tray 2 PWB . • Tray 2 assembly . b. Perform OF7 Main PWB Check RAP. |
Error code: | 07-231 |
Description: | Check the Tray Feed Area |
Causes: | The machine has detected that paper is jammed in the tray 2 paper feeding area at power on. |
Remedy: | 1. Pull out tray 2. Remove all jammed paper. 2. Remove the pickup roll assembly . Check that the pickup roll is clean. If necessary, install a new pickup roll assembly . 3. Enter dC330 code 08-920 to run the tray 2 feed motor. 4. Check the wiring between the tray 2 feed motor and CN8 on the Tray 2 PWB. 5. While the tray 2 feed motor runs, stack the code 08-820 to energize the tray 2 pickup clutch (CL08-820). Check that the tray 2 pickup roll assembly and feed roll rotate. Install new components as necessary . 6. Check the wiring between the tray 2 pickup clutch and CN11 on the Tray 2 PWB. 7. If necessary, install new components: • Tray 2 feed motor . • Tray 2 PWB . • Tray 2 assembly . |
Error code: | 07-500 |
Display: | Bypass Empty |
Description: | Paper Empty at Bypass Tray RAP 07-500 The machine has detected a failure to feed from the bypass tray. |
Causes: | The machine has detected a failure to feed from the bypass tray. |
Remedy: | 1. Open the right cover assembly, PL 7.30 Item 1. Check that the paper feed area at the bypass tray is clean. 2. Check the operation of the bypass paper empty sensor actuator, PL 8.20 Item 26. 3. Enter dC330 code 07-510. Check the bypass paper empty sensor (S07-510), PL 8.20 Item 26. 4. Check the wiring between the bypass paper empty sensor and CN21 on the Main PWB. If necessary, install a new bypass paper empty sensor, PL 8.20 Item 26. 5. If necessary, install new components: • Paper transport assembly, PL 8.20 Item 1. • Main PWB, PL 1.10 Item 1. |
Error code: | 07-530 |
Display: | Paper Jam in Bypass |
Description: | Jam 0 From the Bypass Tray RAP The feed sensor failed to actuate within the correct time after paper was fed from the bypass tray. |
Causes: | The registration sensor failed to actuate within the correct time after paper was fed from the bypass tray. |
Remedy: | 1. Switch off the machine, then switch on the machine. 2. Open the right cover assembly, PL 7.30 Item 1. Remove all jammed paper. 3. Check the paper path for damage or obstructions. 4. Check that the feed sensor actuator, PL 8.15 Item 5 moves freely and is not damaged. If necessary, install a new feed sensor actuator assembly, PL 8.15 Item 14. 5. Enter dC330 code 08-100. Check the feed sensor (Q08-100), PL 8.15 Item 8. 6. Check the wiring between the feed sensor and CN13 on the Main PWB. If necessary, install a new feed sensor, PL 8.15 Item 8. 7. Enter dC330 code 04-100 to run the main BLDC motor. 8. While the main BLDC motor runs, stack the code 08-800 to energize the bypass feed clutch (CL08-800). Check that the bypass tray feed roll, PL 8.20 Item 17 rotates. 9. Check the wiring between the bypass feed clutch, PL 8.20 Item 28 and CN21 on the Main PWB. Install new components as necessary, PL 8.20. 10. While the main BLDC motor runs, stack the code 08-850 to energize the registration clutch (CL08-850). Check that the registration roll, PL 4.15 Item 1 rotates. 11. Check the wiring between the registration clutch, PL 4.15 Item 4 and CN13 on the Main PWB. Install new components as necessary, PL 4.15. 12. Check that the following components are clean and rotate freely, install new components as necessary: • Bypass tray feed roll, PL 8.20 Item 17. • Registration roll, PL 4.15 Item 1. • Registration roll idler, PL 4.15 Item 7. 13. If necessary, install new components: • Paper transport assembly, PL 8.20 Item 1. • Main PWB, PL 1.10 Item 1. |
Error code: | 08-100 |
Display: | Jam inside machine |
Description: | Wait Sensor Jam Entry RAP 08-100 The lead edge of the paper failed to actuate the wait sensor within the correct time from feed sensor 1. |
Causes: | The lead edge of the document failed to actuate the fuser exit sensor within the correct time after registration. |
Remedy: | Identify the speed of the machine, refer to SCP 7 Machine features. Perform one of the steps that follow: • If the speed of the machine is 35-55 ppm, go to 08-100A Wait Sensor RAP (35-55 ppm) • If the speed of the machine is 65-90 ppm, go to 08-100B Wait Sensor RAP (65-90 ppm). |
Error code: | 08-200 |
Description: | Jam in Tray |
Causes: | The machine has detected a paper jam in the tray 2 feed area. |
Remedy: | 1. Pull out tray 1 and tray 2. Remove all jammed paper. 2. Check the paper path for damage or obstructions. 3. Remove the pickup roll assembly . Check that the pickup roll is clean. If necessary, install a new pickup roll assembly . 4. Check the retard pad on tray 2. If necessary, install a new retard pad assembly . 5. Check that the following components are clean and rotate freely, install new components as necessary: • Registration roll . • Registration roll idler . 6. Check that the registration sensor actuator moves freely and is not damaged. If necessary, install a new registration sensor actuator . 7. Enter dC330 code 08-500. Check the registration sensor (Q08-500). If necessary, install a new HVPS . NOTE: The registration sensor is mounted on the HVPS. 8. Enter dC330 code 08-920 to run the tray 2 feed motor. 9. Check the wiring between the tray 2 feed motor and CN8 on the Tray 2 PWB. 10. While the tray 2 feed motor runs, stack the code 08-820 to energize the tray 2 pickup clutch (CL08-820). Check that the tray 2 pickup roll assembly and feed roll rotate. Install new components as necessary . 11. Check the wiring between the tray 2 pickup clutch and CN11 on the Tray 2 PWB. 12. Enter dC330 code 04-100 to run the main BLDC motor. 13. Check the wiring between the main BLDC motor and CN38 on the Main PWB. 14. While the main BLDC motor runs, stack the code 08-850 to energize the registration clutch (CL08-850). Check that the registration roll does not rotate. Install new components as necessary . 15. Check the wiring between the registration clutch and CN35 on the Main PWB. 16. If necessary: a. Install new components: • Front duplex guide assembly . • Tray 2 feed motor . • Tray 2 PWB . • Tray 2 assembly . b. Perform OF7 Main PWB Check RAP. |
Error code: | 08-500 |
Display: | Jam in exit area |
Description: | Jam 2 RAP 08-500 The trail edge of the document failed to actuate the exit sensor within the correct time after registration. |
Causes: | The trail edge of the document failed to deactuate the exit sensor within the correct time after registration. |
Remedy: | 1. Open the right cover assembly, PL 7.30 Item 1. Remove all jammed paper. 2. Check the paper path for damage or obstructions. 3. Remove the fuser, PL 10.10 Item 4. Check that the exit sensor actuator, PL 10.25 Item 12 moves freely and is not damaged. If necessary, install a new exit sensor actuator, PL 10.25 Item 12. 4. Enter dC330 code 08-600. Check the exit sensor (Q08-600), PL 10.15 Item 2. 5. Check the wiring between the exit sensor and CN6 on the Main PWB. If necessary, install a new exit sensor, PL 10.15 Item 2. 6. Enter dC330 code 10-400. Check that the fuser motor (MOT10-400), PL 10.20 Item 3, runs and drives the fuser rolls and transport roll, PL 10.15 Item 22. 7. Check the wiring between the fuser motor and CN12 on the Main PWB. Install new components as necessary, PL 10.15 and PL 10.25. 8. Enter dC330 code 04-200. Check that the exit motor (MOT04-200), PL 10.20 Item 2, runs and drives the upper exit roll, PL 10.15 Item 23. 9. Check the wiring between the exit motor and CN12 on the Main PWB. Install new components as necessary, PL 10.15 and PL 10.20. 10. Check that the following components are clean and rotate freely: • Upper exit roll, PL 10.15 Item 23. • Lower exit roll, PL 10.15 Item 14. • Transport roll, PL 10.15 Item 22. • Transport roll idlers, PL 10.15 Item 19. 11. Install new components as necessary: • Fuser, PL 10.25 Item 1. • Exit assembly, PL 10.15 Item 1. • Main PWB, PL 1.10 Item 1. |
Error code: | 08-600 |
Display: | Jam bottom of duplex |
Description: | Duplex Jam 0 RAP 08-600 The lead edge of the document failed to actuate the feed sensor within the correct time. |
Causes: | The lead edge of the document failed to actuate the duplex jam 1 sensor within the correct time. |
Remedy: | 1. Open the right hand cover. Remove all jammed paper. 2. Check the paper path for damage or obstructions. 3. Check that the feed sensor actuator, PL 8.15 Item 5 moves freely and is not damaged. If necessary, install a new feed sensor actuator assembly, PL 8.15 Item 14. 4. Enter dC330 code 08-100. Check the feed sensor (Q08-100), PL 8.15 Item 8. 5. Check the wiring between the feed sensor and CN13 on the Main PWB. If necessary, install a new feed sensor, PL 8.15 Item 8. 6. Enter dC330 code 04-100 to run the main BLDC motor. 7. While the main BLDC motor runs, stack the code 08-850 to energize the registration clutch (CL08-850). Check that the registration roll, PL 4.15 Item 1 rotates. 8. Check the wiring between the registration clutch, PL 4.15 Item 4 and CN13 on the Main PWB. Install new components as necessary, PL 4.15. 9. Clean the registration roll, PL 4.15 Item 1 and the registration roll idler, PL 4.15 Item 7. Install new components as necessary. 10. If necessary, install a new main PWB, PL 1.10 Item 1. |
Error code: | 08-610 |
Display: | Jam top of duplex |
Description: | Duplex Jam 1 RAP 08-610 The lead edge of the document failed to actuate the duplex jam 1 sensor within the correct time in reverse mode. |
Causes: | The lead edge of the document failed to actuate the registration sensor after the duplex jam 1 sensor within the correct time. |
Remedy: | 1. Open the right hand cover. Remove all jammed paper. 2. Unclip the duplex assembly, PL 7.30 Item 28. Check that the paper path is clear and not damaged. 3. Check that the duplex jam 1 sensor actuator, PL 7.30 Item 20 moves freely and is not damaged. 4. Enter dC330 code 08-700. Check the duplex jam 1 sensor (Q08-700), PL 7.30 Item 18. 5. Check the wiring between the duplex jam 1 sensor and CN25 on the Main PWB. If necessary, install a new duplex jam 1 sensor, PL 7.30 Item 18. 6. Enter dC330 code 04-300, then code 04-310. Check that the duplex motor (MOT04-300), PL 10.20 Item 2, runs in forward and reverse and drives the duplex roll, PL 10.15 Item 22. 7. Check the wiring between the duplex motor and CN12 on the Main PWB. Install new components as necessary, PL 10.15 and PL 10.20. 8. Enter dC330 code 08-870. Check that the duplex gate solenoid (SOL08-870), PL 10.15 Item 4 energises and lowers the duplex gate, PL 10.15 Item 15. 9. Check the duplex gate for damage. If necessary, install a new duplex gate, PL 10.15 Item 15. 10. Check the wiring between the duplex gate solenoid and CN6 on the Main PWB. If necessary, install a new duplex gate solenoid, PL 10.15 Item 4. 11. Check that the following components are clean and rotate freely: • Duplex roll, PL 10.15 Item 22. • Duplex roll idlers, PL 10.15 Item 9. 12. If necessary, install new components: • Exit assembly, PL 10.15 Item 1. • Right cover assembly, PL 7.30 Item 1. • Main PWB, PL 1.10 Item 1. |
Error code: | 08-700 |
Display: | Output Bin full. Remove Paper |
Description: | Out Bin Full RAP 08-700 The machine has detected that the exit tray is full. |
Causes: | The machine has detected that the exit tray is full. |
Remedy: | 1. Remove all documents from the exit tray. Check that the out bin full sensor actuator, PL 10.15 Item 25 moves freely and is not damaged. 2. Enter dC330 code 08-720. Check the out bin full sensor (Q08-720), PL 10.15 Item 2. 3. Check the wiring between the out bin full sensor and CN6 on the Main PWB. If necessary, install a new out bin full sensor, PL 10.15 Item 2. 4. Enter dC330 code 04-200. Check that the exit motor (MOT04-200), PL 10.20 Item 2, runs and drives the upper exit roll, PL 10.15 Item 23. 5. Check the wiring between the exit motor and CN12 on the Main PWB. Install new components as necessary, PL 10.15 and PL 10.20. 6. If necessary, install new components: • Exit assembly, PL 10.15 Item 1. • Main PWB, PL 1.10 Item 1. |
Error code: | 09-100 |
Display: | Toner Low |
Description: | Toner Low RAP 09-100 The machine has detected that the toner module is almost empty. |
Causes: | The machine has detected that the print cartridge is almost empty. |
Remedy: | 1. No immediate action is necessary. Ensure that a replacement toner module, PL 9.10 Item 2 is in stock. NOTE: The toner low message is based on a pixel count, not a signal from a sensor. It cannot be reset by shaking the toner module. |
Error code: | 09-350 |
Display: | Replace Print Cart. |
Description: | Erase Lamp Failure RAP 09-350 The photoreceptor erase lamp has failed. |
Causes: | The print cartridge is near the end of the design life. The design life is 10,000 print pages. |
Remedy: | NOTE: The door interlock switch must be cheated when checking +24V components. Cheat the door interlock switch. Enter dC330 code 09-022, photoreceptor erase lamp. Press start.. Observe the erase lamp. All the LEDs of the erase lamp are lit. Y↓N→Some of the LEDs of the erase lamp are lit. Y↓N→Go to Flag 1. +24V is available at P/J17 pin 1 on the LVPS. Y↓N→Install a new LVPS and base module, PL 1.10 Item 3. Go to Flag 2. +24V is available at P/J41 pin 1. Y↓N→Go to Flag 1. Check the inline fuse. The fuse is good. Y↓N→Install a new fuse, GP 7, PL 1.10 Item 9. If the fuse blows again, go to 01G Fused Distribution Check. Go to: • Go to 01G +24V Distribution RAP. • 01B 0V Distribution RAP. Go to Flag 3. +13V is available at P/J5 pin 14. Y↓N→NOTE: To gain access to the erase lamp wiring, remove the main drive module, (35-55 ppm) PL 4.15 Item 1, (65-90 ppm) PL 4.10 Item 1. Check the wiring, GP 7, from the in-line fuse to P/J41, pin 2. The wiring is good. Y↓N→Repair the wiring. Perform the steps that follow: • Check that the connector PJ41 is located correctly in the IOT frame. • Install a new erase lamp, (35 ppm) PL 9.22 Item 1, (40-90 ppm) PL 9.20 Item 1. Perform OF7 IOT PWB Diagnostics RAP before a new IOT PWB is installed, PL 1.10 Item 2. Install a new erase lamp, (35 ppm) PL 9.22 Item 1, (40-90 ppm) PL 9.20 Item 1. The fault may be intermittent. Perform the steps that follow: • Check the wiring, GP 7 between P/J41 and P/J17 on the LVPS. • Ensure that the P/Js are correctly and securely connected. • Malfunction of the following associated circuits can cause 09-350 faults. – The inverter paper path and Inverter nip solenoid, go to 10-120, 10-121, 10-126 IOT Exit Sensor RAP. – The vacuum transport fan and Registration clutch, go to 10-101A, 10-102A, 10-103A Lead Edge Late to Fuser Exit Sensor RAP. |
Error code: | 09-450 |
Display: | Replace Print Cart. |
Description: | Replace Drum |
Causes: | The print cartridge has reached the end of the design life of 10,000 print pages. |
Remedy: | 1. Install a new print cartridge . |
Error code: | 09-550, 09-820, 09-830 |
Description: | Print Cartridge Communications Error |
Causes: | 09-550 The print cartridge is not installed or is not detected by the CRUM PWB. 09-820 A non Xerox print cartridge is installed. 09-830 A mismatch detected between the CRUM and MSOK. |
Remedy: | 1. Check that the print cartridge , is installed correctly. 2. Remove the print cartridge. Check the CRUM contact on the print cartridge. 3. Check the wiring between the print cartridge CRUM PWB and CN17 in the Main PWB. 4. If necessary: a. Install new components: • Print cartridge . • Print cartridge CRUM . b. Perform OF7 Main PWB Check RAP. |
Error code: | 10-100, 10-200 |
Display: | Open Fuser error Low Heat error |
Description: | Open Fuser Error/Low Heat Error RAP 10-100 During normal operation, the temperature of the fuser has dropped below the operating level. 10-200 The fuser has failed to reach the correct operating temperature. |
Causes: | 10-100 During normal operation, the temperature of the fuser has dropped below the operating level. 10-200 The fuser has failed to reach the correct operating temperature. |
Remedy: | 1. Switch off the machine, then switch on the machine. 2. Enter dC330 code 10-100 to heat the fuser to 180 degrees. Enter codes 10-200 and 10- 210 to verify the condition of the thermistors. 3. Enter code 10-300 to check power supply unit 2. If necessary, install a new power supply unit 2, PL 1.10 Item 4. 4. Switch off the machine. Remove the fuser assembly. Check that the thermistors, PL 10.25 Item 9 are clean and in good contact with the fuser heat roller. Check the wiring to the thermistors. Install new components as necessary, PL 10.25. 5. Check for continuity between the two pins on the fuser assembly connector, PL 10.25 Item 8. NOTE: A cold fuser has a resistance of approximately 11.5 ohms (220V/240V) or 2 ohms (110V). 6. Check that there is continuity through the fuser heater and across the over temperature cut-out. 7. Check the wiring between the fuser connector, PL 4.15 Item 20 and CON3, CON8 and CON9 on Power Supply Unit 2. If necessary, install a new fuser connector. 8. Check the wiring between CON4 on Power Supply Unit 2 and CN7 on the Main PWB. 9. Install new components as necessary: • Fuser assembly, PL 10.25 Item 1. • Main PWB, PL 1.10 Item 1. • HVPS, PL 1.10 Item 2. |
Error code: | 10-300 |
Display: | Over Heat error |
Description: | Over Heat Error RAP 10-300 The fuser temperature has risen above the normal level. Although the fuser unit can return to a normal operating temperature, the fuser may consequently be damaged. |
Causes: | The fuser temperature has risen above the normal level. Although the fuser unit can return to a normal operating temperature, the fuser may consequently be damaged. |
Remedy: | 1. Enter codes 10-200 and 10-210. Perform a fuser temperature check to verify the condition of the thermistors. 2. Switch off the machine. Remove the fuser assembly. Examine the fuser assembly for heat damage. Install new components as necessary, PL 10.25 and PL 10.26. 3. Check that the thermistors, PL 10.25 Item 9 are in good contact with the fuser heat roller and are clean. Check the wiring to the thermistors. Install new components as necessary, PL 10.25. 4. Check that there is continuity through the fuser heater and across the over temperature cut-out. If necessary, install a new thermostat assembly, PL 10.25 Item 2. 5. Check the wiring between the fuser connector, PL 4.15 Item 20 and CON3, CON8 and CON9 on Power Supply Unit 2. If necessary, install a new fuser connector. 6. Check the wiring between CON4 on Power Supply Unit 2 and CN7 on the Main PWB. 7. Check that the fuser fan is working. Go to the OF3 Air Systems RAP. 8. Install new components as necessary: • Power supply unit 2, PL 1.10 Item 4. • Main PWB, PL 1.10 Item 1. • HVPS, PL 1.10 Item 2. |
Error code: | 10-500 |
Description: | Fuser Warning |
Causes: | The machine has detected that the fuser assembly is near the end of its life. |
Remedy: | 1. No immediate action is necessary. Ensure that a replacement fuser assembly is in stock. |
Error code: | 10-510 |
Description: | Replace Fuser |
Causes: | The machine has detected that the fuser assembly has reached the end of its life. |
Remedy: | 1. Install a new fuser assembly . |
Error code: | 14-100 |
Display: | Scanner Lock |
Description: | CCD Lock RAP 14-100 The machine has detected a mechanical fault with the CCD module. |
Causes: | The machine has detected a mechanical fault with the CCD module. |
Remedy: | 1. If necessary, remove the finisher, REP 12.1. Check that the scanner lock, PL 14.10 Item 20 is completely unlocked. 2. Remove the scanner top cover assembly, refer to REP 14.2. 3. Check that the CCD module, PL 14.10 Item 2 moves freely from left to right. 4. Check the wiring between the scanner drive motor, PL 14.10 Item 4 and CN2 on the Scanner PWB. 5. If necessary, install new components: • Scanner drive motor assembly, PL 14.10 Item 4. • Scanner PWB, PL 14.10 Item 15. • CCD module, PL 14.10 Item 2. • Scanner assembly, PL 14.10 Item 1. |
Error code: | 15-100 ... 15-500 |
Description: | Scan to E-mail Faults |
Causes: | These are the faults displayed when the machine encounters scan to e-mail problems. The faults are listed in code order, together with any recommended action. Please note that service actions are limited. |
Remedy: | 15-100 Group Name has no Assigned Email Addresses No email address is assigned to the group name. Remove the group name from the ‘To:’ field or enter a valid email address. 15-110 Email Send Failed Email SMTP server returned an error during transmission. The SMTP server authentication may be supported but not enabled on the device or any 500 code is returned from the mail server. Resend the email. 15-120 Invalid Recipient Email Address The email address has either been restricted or is in the wrong format. Re-enter the email address. 15-130 Mail Too Large The machine is unable to split the mail and send it. This can occur when the machine is configured to send a maximum mail size. For example 1.0MB and the scanned mail page exceeds this size. Increase the mail size via CentreWare Internet Services. If the fault persists, increase the mail size allocation on the mail server. 15-140 Invalid Email Address The user has attempted to enter an invalid email ID. Examples are: • Spaces in the ID • Invalid starting character such as `.`, `+`, `_`, `@` • More than one `@` 15-150 Group Not Available The user has attempted to enter an invalid group number. Confirm that the group is available and has mail addresses associated with it. 15-160 Memory Full The HDD is full during scan to email. 15-170 Memory Full The machine does not have enough memory to prepare the next job. 15-200 Network Controller Error A NIC error (SMTP). One of the following Simple Mail Transfer Protocol errors may have occurred: • SMTP_ENCODER_FAILURE. Error returned by NIC during SMTP encoding activity. • SMTP_MEMORY_FAILURE. Error returned by NIC for memory failure during SMTP operation. • SMTP_MISC_ERROR. Miscellaneous error returned by NIC during SMTP operation. Switch off the machine, then switch on the machine. Resend the email. 15-300 Network Connection Failure Any communication or network failure during SMTP or LDAP operations. Check the network connection. Switch off the machine, then switch on the machine. 15-310 Authentication Failure The user has attempted to enter an invalid user name or corresponding password. Enter a valid user name and password. 15-320 Mail Server Connection Failure The machine can not contact the SMTP server. Check the SMTP IP address or host name. Check that the SMTP port is open and working correctly. 15-330 DNS Connection Failure The machine cannot contact the Domain Name System to resolve the SMTP host name. Check that the DNS server is online. 15-340 Mail Exceed Server Support The maximum configured mail size exceeds the server limit. Reduce the mail size option. 15-400 LDAP Communication Failure The machine can not contact the LDAP server. Check the LDAP IP address or host name. Check that the LDAP port is correct and open. 15-410 LDAP Search Failed The LDAP server has returned an error during transmission. The LDAP server authentication may be supported but not enabled on the device or the maximum search results have been exceeded. Resend the email. 15-420 LDAP Search Timeout Exceeded The LDAP search timeout has been exceeded. Resend the email. 15-430 No Matching Entries in LDAP Directory The LDAP server cannot match the entry by user. Check the spelling of the LDAP entry, then resend the email. 15-500 Session Timeout The user has not touched a key within in the designated time frame. Resend the email. 15-510 Scan Error The machine has detected an error with the scanner. Check the scanner, refer to the 14-100 CCD Lock RAP. 15-520 Stop Pressed from MFP The user has cancelled the email job. 15-600 Authentication Required The mail server requires user authentication to be enabled. Enable user authentication. Refer to the System Administration Guide. 15-700 DNS Error The machine can not contact the DNS server or a DNS resolution failure has been detected. Check the DNS server setup or enter a valid email address. 15-800 Pop3 Error The machine has detected a POP3 protocol error or an error during a POP3 session. Enter a valid email address. 15-810 Pop3 Connection Failure The machine could not connect to the configured POP3 server. Check the POP3 server setup. 15-820 Pop3 Authentication Failure The machine could not login into the POP3 server. Re-enter the user name and password. 15-830 Pop3 Authentication Required The POP3 server requires authentication to be enabled. Enable authentication. Refer to the System Administration Guide. Final Actions Perform the OF7 Main PWB Check RAP. |
Error code: | 17-100 ... 17-610 |
Description: | Network Controller Faults |
Causes: | These are the faults displayed when the machine encounters network controller problems. The faults are listed in code order, together with any recommended actions. Please note that the service actions are limited. |
Remedy: | NOTE: The network connection has two LEDs positioned next to the network port. The upper LED on indicates that the PWB is ready. The lower LED flashing indicates that the network is good. 17-100 IP Address is Conflicted The IP address of the machine is being used by another device. Go to GP 4 System Administration Tools. Check with the customer that the connectivity and network setup settings are correct. 17-110 Connection Error The machine encountered an error when establishing a connection to the designated server. Check with the customer that the connectivity and network setup settings are correct. Refer to GP 4 System Administration Tools. 17-120 Server Not Found The machine can not find the designated server. Check with the customer that the connectivity and network setup settings are correct. Refer to GP 4 System Administration Tools. 17-130 Login Error The machine can not login to the designated server. Check with the customer that the connectivity and network setup settings are correct. Refer to GP 4 System Administration Tools. 17-140 Access Denied A permissions error occurred. Check with the customer that the connectivity and network setup settings are correct. Refer to GP 4 System Administration Tools. 17-150 Lock Exists The *.lck directory already exists. 17-200 Network Cable is Disconnected The network cable is not connected. Check the network cable. 17-400 User Cancelled The user cancelled the network scan job. 17-500 Document Jam Occurred A document jam occurred during the scan operation. 17-510 Operation Error An error occurred when sending the image file. 17-600 Filename is Too Long The name of the file to be sent is longer than the destination systems limits. Shorten the file name. 17-610 Scan File Exists The file name already exists on the destination server. Change the file name. |
Error code: | 17-700 ... 17-810 |
Description: | Server Error |
Causes: | 17-700 A BOOTP server error has occurred but the automatic assigning of an IP address is working. 17-710 A BOOTP server error has occurred and the automatic assigning of an IP address is not working. 17-800 A DHCP server error has occurred but the automatic assigning of an IP address is working. 17-810 A DHCP server error has occurred and the automatic assigning of an IP address is not working. |
Remedy: | 1. Go to GP 4 System Administration Tools. Select Connectivity and Network Setup. Scroll to TCP / IP Settings. Disable dynamic addressing. 2. Switch off, then switch on the machine. Re-enable dynamic addressing. 3. If the fault persists, again disable dynamic addressing. Assign a new static IP address. |
Error code: | 17-900 |
Display: | 802.1x Network Error |
Description: | 802.1X Authentication Error |
Causes: | The 802.1X authentication failed. |
Remedy: | 1. Ensure that the 802.1X EAP type, username and password for the machine authentication switch and authentication server match. |
Error code: | 20-100 ... 20-900 |
Description: | Fax Faults |
Causes: | These are the faults displayed when the machine encounters fax problems. The faults are listed in code order, together with any recommended actions. Please note that the service actions are limited. If the machine has a fax fault without displaying a fault code, go to the 20A Fax Faults Without a Code RAP. |
Remedy: | 20-100 Communication Error A communication failure has occurred with either the fax transmission or reception. Resend the fax. 20-110 Mailbox Error The machine is not available for mailbox communication. Go to GP 4 System Administration Tools. Check that the mailbox ID and password are correct. 20-120 Scanning Error While sending a fax using manual dial, a scanning error has occurred. Clear any jams. Switch off the machine, then switch on the machine. Resend the fax. If the fault persists, check the scanner, refer to the 14-100 CCD Lock RAP. 20-200 Group Not Available The user has selected a group location where only a single location can be used, or when the group location is unavailable. Try again, checking for the correct group location. 20-300 Incompatible The remote party does not have the feature the user has requested, for example, polling. Change the settings, then resend the fax. 20-400 Line Busy The remote party did not answer. Wait, then resend the fax. 20-410 Line Error There is a problem with the phone line, affecting transmission or reception. Try again and if necessary, wait for the line to clear. 20-500 Memory Full The fax data memory is full. Delete any unnecessary documents awaiting transmission, or wait until more memory becomes available, or split the current Fax in to smaller units. 20-550 Low Memory The available fax memory is getting low. 20-600 No Answer It has not been possible to connect to the remote fax, even after re-dial attempts. Check that the remote fax is on line and try again. 20-700 Number Not Assigned No number has been assigned for the speed dial location selected. Assign a number to this location or dial the number manually. 20-800 Power Failure During a power-off period, the machine has lost its user memory. Check that the backup battery is holding its charge of about +3V. If necessary, install a new battery. Wait, then resend the fax. 20-900 Retry Redial This indicates that the machine is waiting to re-dial. Press Start to re-dial immediately, or press Stop to cancel the re-dial procedure. Final Actions Perform the following: 1. Install a new fax PWB : 2. Perform the OF7 Main PWB Check RAP. |
Error code: | 20A |
Description: | Fax Faults Without a Code |
Causes: | Use this RAP when the machine has a fax fault but does not display a code. If a fax fault code is displayed, go to the 20-100 to 20-900 Fax Faults RAP. |
Remedy: | 1. Ensure the telephone line cable is properly connected into the line connector on the Fax PWB module . 2. Ensure the correct dialing mode is selected. Refer to GP 4 System Administration Tools. 3. Use a known good telephone handset or a line test tool to check the telephone line. 4. If sent faxes are blank or light, make sure that the scanner lock is completely unlocked. 5. If necessary install a new fax PWB . 6. Perform OF7 Main PWB Check RAP. |
Error code: | OF1 |
Description: | Audible Noise |
Causes: | Use this RAP to isolate and identify the source of unusual noises. |
Remedy: | 1. Ask the customer if there are any specific machine functions that are noisy. 2. Identify the source of the noise by exercising the machine in all modes. 3. Use diagnostics to run individual components. 4. Go to the relevant subsection: • Main Drives and Paper Transport • LSU • DADF • Tray 2 5. Refer to Possible Causes and Potential Solutions. Main Drives and Paper Transport • Enter dC330 code 04-100 to run the main BLDC motor. The following components will be run. – The print cartridge . – The registration roll . – The registration roll idler . • While the main BLDC motor runs, stack the code 08-810 to energize the tray 1 pickup solenoid and run the tray 1 pickup roll and feed roll . • While the main BLDC motor runs, stack the code 08-850 to energize the registration solenoid and run the registration roll and registration roll idler . • While the main BLDC motor runs, stack the code 08-800 to energize the bypass feed solenoid and run the bypass pickup roll . • Enter dC330 code 04-300 to run the duplex motor. The duplex rolls and , will rotate. • Enter dC330 code 04-200 to run the exit motor. The following fuser components will be run: – The heat roll in the fuser . – The pressure rolls in the fuser and . – Exit roll . • Enter dC330 code 04-120 to run the main fan . • Enter dC330 code 10-500 to run the fuser fan . • Enter dC330 code 09-500 to run the SMPS fan . LSU • Enter dC330 code 06-100 to run the LSU motor. DADF • Enter dC330 code 05-200 to run the scan motor , in the DADF. The following components will be run: – Scan roll . – Exit roll . • While the scan motor runs, stack the code 05-300 to energize the pickup solenoid and run the DADF pickup roll assembly . • While the DADF scan motor runs, stack the code 05-310 to energize the registration solenoid and run the registration roll . Tray 2 • Enter dC330 code 07-210 to run the tray 2 feed motor . The tray 2 feed roll , will rotate. • While the tray 2 feed motor runs, stack the code 08-820 to energise the tray 2 pickup solenoid and run the tray 2 pickup roll assembly . Possible Causes and Potential Solutions Go to the relevant procedure: • Squeaks • Unusual Noise from the Scanner Assembly Squeaks Possible causes are: • Contamination of the bushes and drive shafts. Solution: – Clean the components. – Plastic bushes should be cleaned and lubricated. – Install new components as necessary. • Bearings in cooling fans Solution: – Install new components as necessary. • Mis-adjusted or worn drive belts. Solution: – Install new components as necessary. • Mis-aligned or damaged parts. Solution: – Check for parts that are damaged or out of position. – Adjust the components if appropriate. – Install new components as necessary. • Noise from the DADH input tray document guides. Solution: – Clean the DADH input tray in the area beneath the input guides. Unusual Noise from the Scanner Assembly Possible causes are: • Mis-aligned or damaged parts. • Defective motor driver. Solution: • Check the position of the scan motor and associated gears . • Ensure the CCD module , moves freely. • Install new components as necessary . |
Error code: | OF2 |
Description: | UI Touch Screen Error |
Causes: | Use this RAP to solve UI touch screen problems when the machine has power but either the display is missing, is too dark or the UI screen responds incorrectly or does not refresh. |
Remedy: | 1. If possible, enter dC305 UI test. Perform the relevant tests to check the operation of the UI. 2. Remove the UI, refer to REP 2.1. Check the ribbon cables between the UI PWB and the touch screen . 3. Check the following wiring: • Between CN2 on the UI PWB and CN6 on Main PWB. • Between CN1 on the UI PWB and CN11 on Main PWB. • Between CN11 on the UI PWB and CN10 on Main PWB. 4. If necessary: a. Install new components: • Touch screen . • UI assembly . b. Perform OF7 Main PWB Check RAP. |
Error code: | OF3 |
Description: | Air Systems |
Causes: | Use this RAP to diagnose faulty machine fans. Faulty fans can cause image quality defects, odours or overheating. |
Remedy: | Check the following fans: • SMPS Fan • Main Fan • Fuser Fan SMPS Fan Refer to Wiring Diagram 9. Perform the following: 1. Switch off the machine, then switch on the machine. 2. Enter dC330 code 09-500. Check that the SMPS fan runs at normal speed. 3. Check the wiring between the SMPS fan and CN8 on the Connection PWB. 4. Install new components as necessary: • SMPS fan . • Connection PWB . Main Fan Refer to Wiring Diagram 9. Perform the following: 1. Switch off the machine, then switch on the machine. 2. Enter dC330 code 04-120. Check that the main fan runs at normal speed. 3. Check the wiring between the main fan and CN1 on the Connection PWB. 4. Install new components as necessary: • Main fan . • Connection PWB . Fuser Fan Refer to Wiring Diagram 9. Perform the following: 1. Switch off the machine, then switch on the machine. 2. Enter dC330 code 10-500. Check that the fuser fan runs at normal speed. 3. Check the wiring between the fuser fan and CN2 on the Connection PWB. 4. Install new components as necessary: • Fuser fan . • Connection PWB . |
Error code: | OF4 |
Description: | Copying Error |
Causes: | Use this RAP if the machine does not copy correctly when the customer uses features such as auto size detect, edge erase, book copying and image shift. |
Remedy: | 1. Perform the Scan Edge Print test, GP 18. 2. If the test fails, clean the document glass. 3. If necessary, install a new scanner cover . |
Error code: | OF5 |
Description: | Stapler Fault |
Causes: | Use this RAP if the stapler fails to operate. |
Remedy: | 1. Check the stapler door interlock switch, go to 01-700 Stapler Door Open RAP. 2. Check the wiring between CON1 on the stapler and CN4 on the Connection PWB. 3. Open the stapler door . Check that the paper present switch actuator moves freely and actuates the paper present switch. 4. Install new components as necessary: • Stapler . • Connection PWB . |
Error code: | OF6 |
Description: | Unable to Boot |
Causes: | Use this RAP if the machine powers up but fails to boot. |
Remedy: | 1. Switch off the machine, then switch on the machine. 2. Check the memory DIMM is correctly installed. 3. If necessary: a. Install new components: • Memory DIMM . • Hard disk drive . b. Perform OF7 Main PWB Check RAP |
Error code: | OF7 |
Description: | Main PWB Check |
Causes: | Use this RAP to check the main PWB. This RAP must be performed before a new main PWB is installed |
Remedy: | PWB Checks The following steps are used to diagnose a fault with the input voltage to the main PWB or output voltage from the main PWB. Perform the following: 1. Ensure the supply voltage is within specification, refer to GP 7 Machine Specifications. If possible, connect the machine directly to a known good power supply. If possible, do not connect the machine to a multiway connector or power strip that is being used to supply power to other electro-mechanical devices. Card readers, printers and PC’s are known to cause problems for Xerox equipment if they share a power supply. If the customer’s power supply is faulty, inform the customer. 2. Refer to Wiring Diagram 6. Disconnect CN26 from the Main PWB. Check the output voltage from the connection PWB . If necessary, install a new connection PWB. If the output voltage from the connection PWB is good, reconnect CN26. Check the voltage on the main PWB. Repair the wiring as necessary. 3. Refer to Wiring Diagram 2, Wiring Diagram 3, Wiring Diagram 5 and Wiring Diagram 7. Actuate each component connected to the main PWB. Check that the signal voltage from each component changes state. Check the wiring or install new components as necessary. 4. Check all connectors on the main PWB. If necessary, remove any oxidisation from the pins and connectors. 5. If the fault is still present, perform the Software Checks. Software Checks The following steps are used to clear any memory or software faults. The customers settings will be reset to default. Ensure all customer data is recorded before clearing the memory. Perform the following: 1. Print the System Configuration and Fax Phone Book (TBD) reports, refer to GP 5. Enter dC132. Initialize the Copier NVM, Network NVM and Fax Card NVM. 2. Reinstall the machine firmware, refer to GP 6 Firmware Upgrade. 3. If the fault is still present, perform the Final Actions. Final Actions Perform the following: 1. Install a new main PWB . 2. Perform GP 15 Shading Test. |